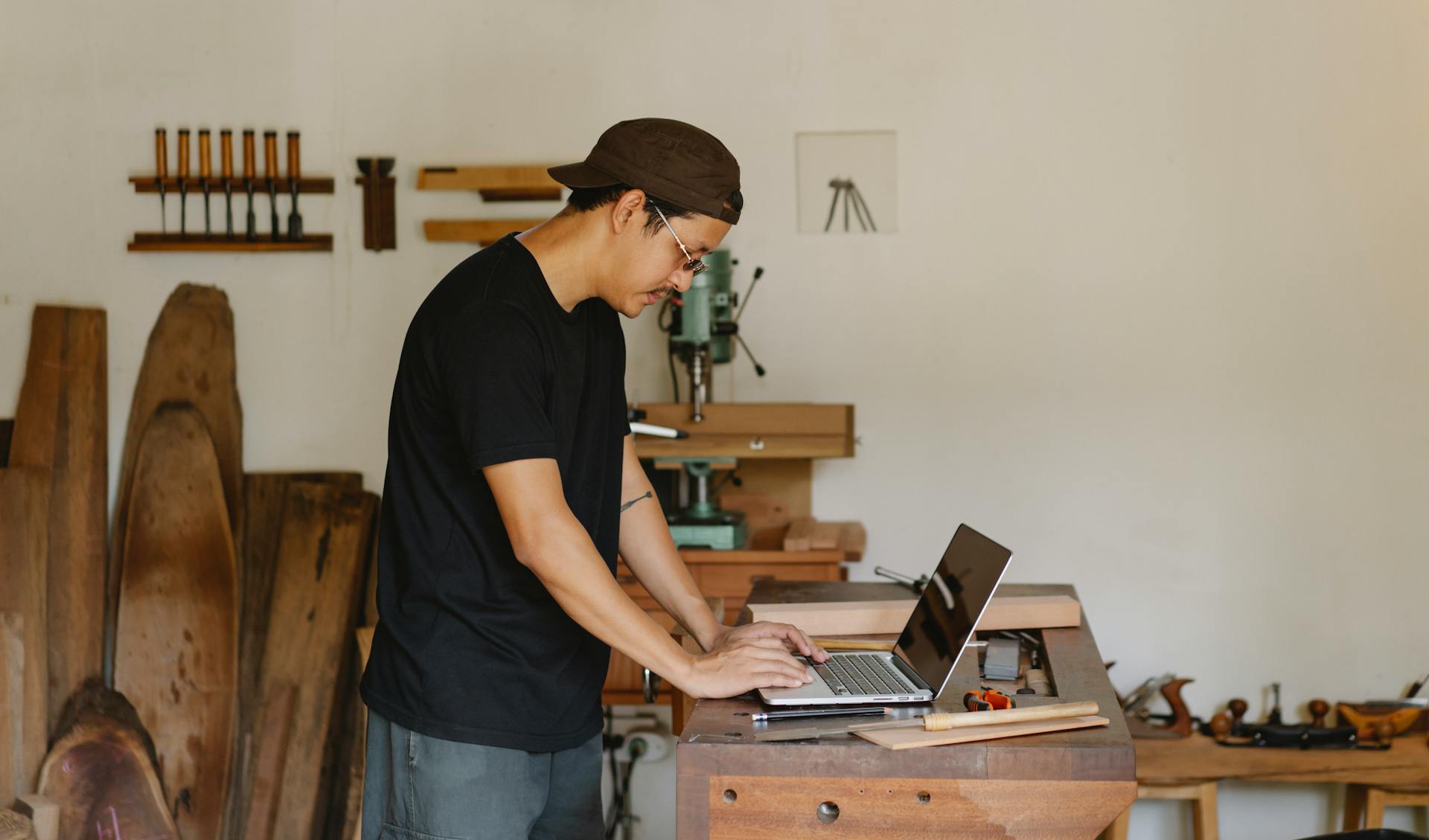
Decades ago, creating a working prototype was generally needed to see how a single item would perform in the manufacturing process. This was often a time-consuming undertaking that required an assembly line and physical prototype to be created by engineers. However, with the digital transformation of manufacturing companies, complete virtual models can now be used to simulate the entire assembly process without ever leaving a computer screen.
This new approach to production is known as digital manufacturing, and it's revolutionizing the way we work. By reducing development timelines and allowing errors to be corrected early on, digital manufacturing reduces costs while delivering actionable results. With this technology, manufacturers can create a complete virtual model of their product before even starting production.
The benefits of digital manufacturing are clear: reduced development timelines mean faster time-to-market for new products, while eliminating physical prototypes reduces costs and allows for errors to be corrected early on. This enables manufacturers to make better decisions about their production processes, resulting in higher quality products at lower costs. In short, digital manufacturing is changing everything we know about how things are made.
You might enjoy: Discrete vs Process Manufacturing
Exploring the Advancements of Digital Manufacturing
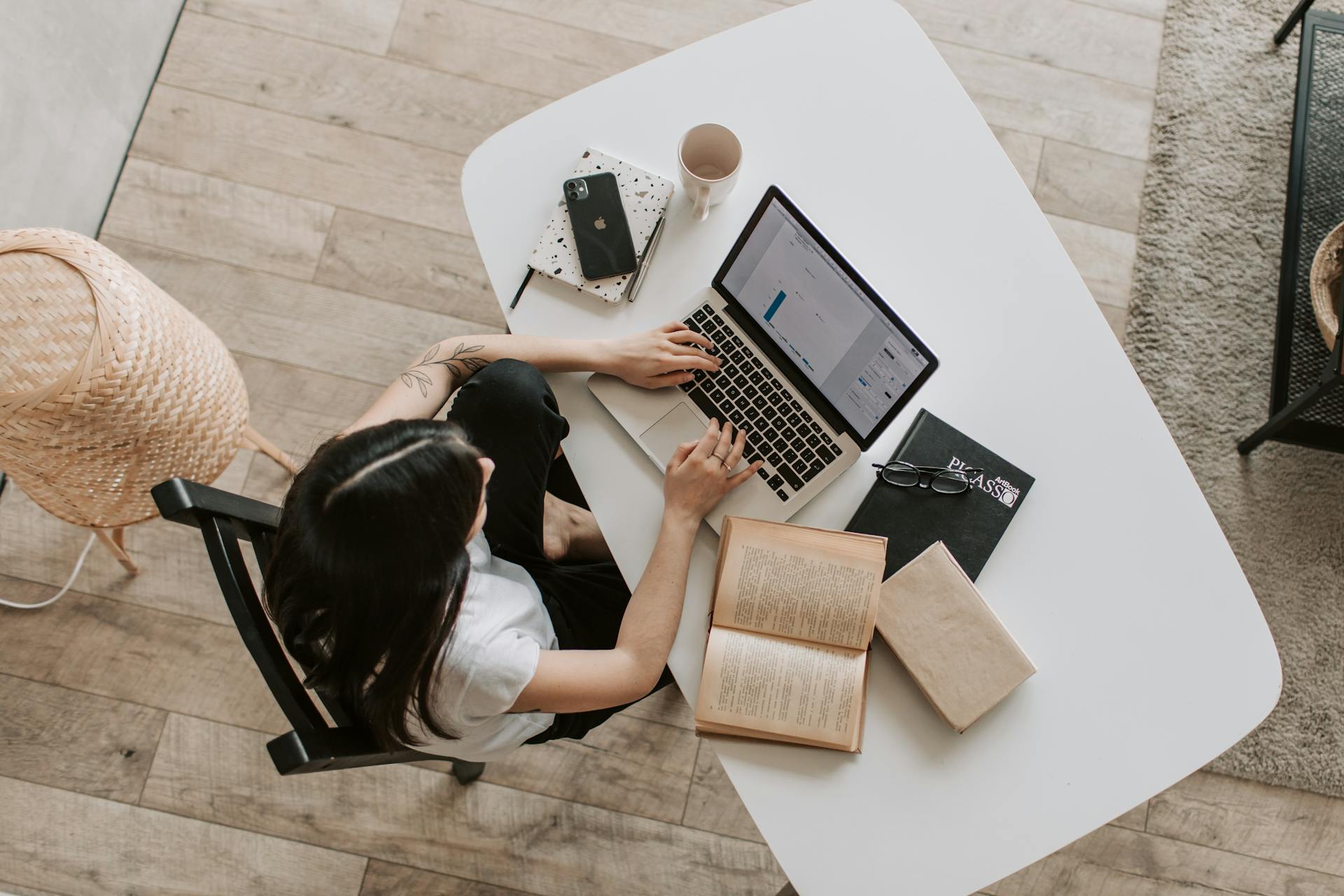
Digital manufacturing is revolutionizing the manufacturing process for companies around the world. Instead of relying on traditional methods, industry 4.0 engineers are using a technology-driven approach to create custom products that were previously impossible due to requiring large minimum order quantities. With digital manufacturing, a virtual model is created using computer-aided design (CAD), which is then physically created based on that model. This allows for greater flexibility and speed in the manufacturing process.
One of the biggest advantages of digital manufacturing is its impact on inventory management. Companies no longer need to stockpile finished goods, as they can be produced on demand using digital manufacturing processes. This means that companies can reduce their inventory carrying costs while still meeting customer demand in a timely manner. Additionally, with the use of Manufacturing Execution Systems (MES) and digital twins, companies can closely monitor every step of the production process and make adjustments as needed.
3D printing has been one of the most significant advancements in digital manufacturing. It allows manufacturers to produce complex parts quickly and efficiently without needing expensive tooling or molds. This has opened up new possibilities for product design and engineering. Not only does it reduce lead times, but it also allows for more precise customization options for each physical product. Overall, digital manufacturing is changing the way manufacturers approach production by streamlining processes and increasing efficiency while reducing costs and improving quality control standards.
See what others are reading: Digital Marketing Strategy for Manufacturing Industry
Three company archetypes join the race
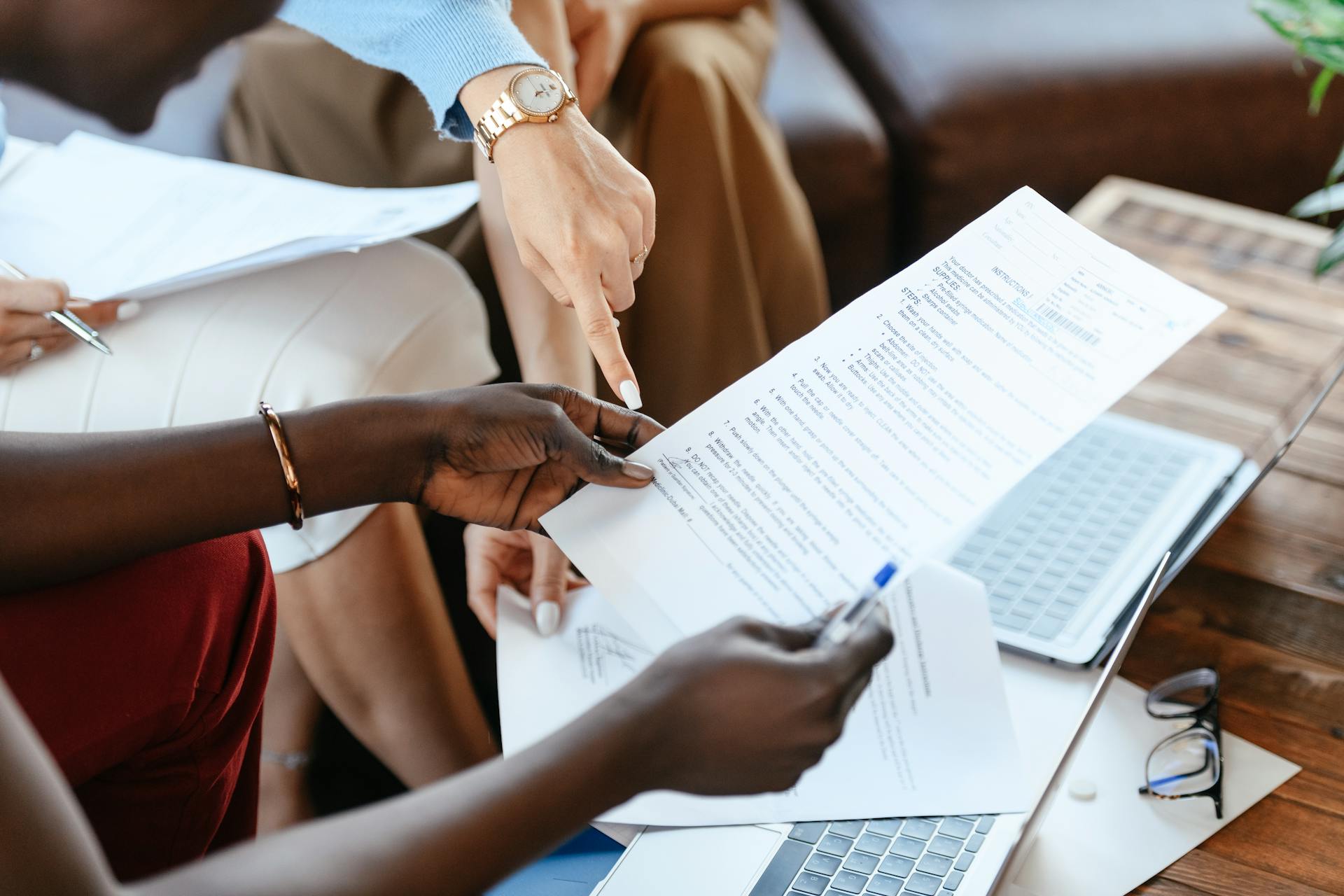
Three company archetypes have joined the race towards digital manufacturing. The cautious starters, frustrated experimenters and leading companies generally fall under these archetypes. Manufacturers playing catch-up have started experimenting with pilot programs but remain unable to achieve the full benefits of Industry 4.0 due to the lack of a clear understanding of how to deploy solutions that can achieve financial ROI.
The frustrated experimenters are those who have started experimenting with deploying technologies but are facing roadblocks in achieving network-wide strategy. Without a deployment roadmap, they remain lost in their digital-transformation journeys. The cautious starters, on the other hand, are taking things slow by testing out small-scale pilot programs before accelerating rollout.
Leading companies that have already embarked on their Industry 4.0 journey have deployed solutions but still need to realize their full benefits. They need to focus on developing a network-wide strategy and deployment roadmap that aligns with their business goals, ensuring they achieve financial ROI. By doing so, they will stand out among their peers and take advantage of the opportunities presented by Industry 4.0.
Consider reading: Digital Thread
Discover the Power of Three-dimensional Modeling
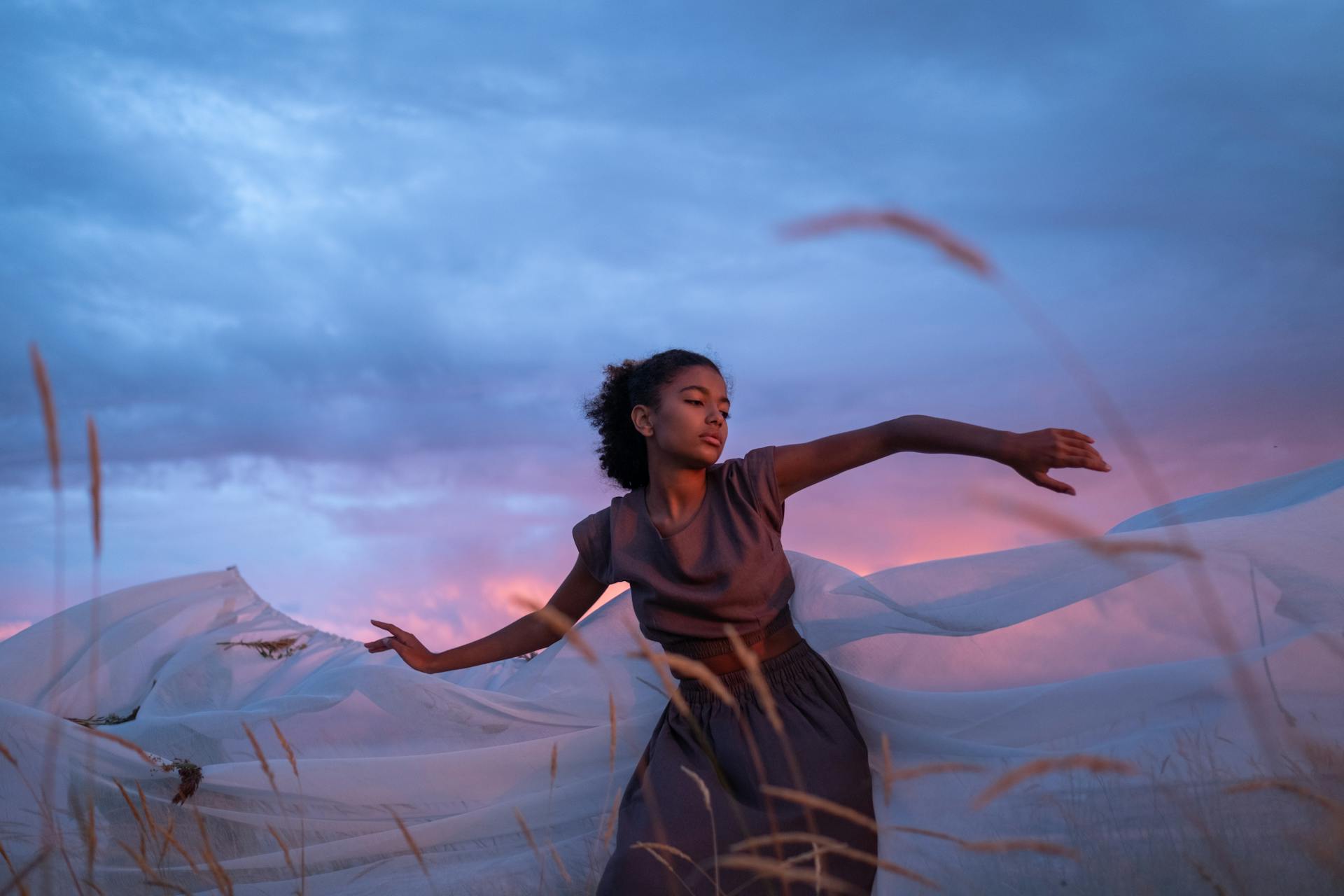
Manufacturing engineers can benefit greatly from using 3D modeling software to improve their intended applications. This technique lets engineers analyze the factory floor layout and production flow to increase efficiency in current manufacturing processes. With three-dimensional modeling, manufacturers can simulate the production process and identify any potential issues before they arise. This technology is a powerful tool for improving manufacturing processes and reducing costs.
The Significance of PPE Manufacturing: Why It Matters
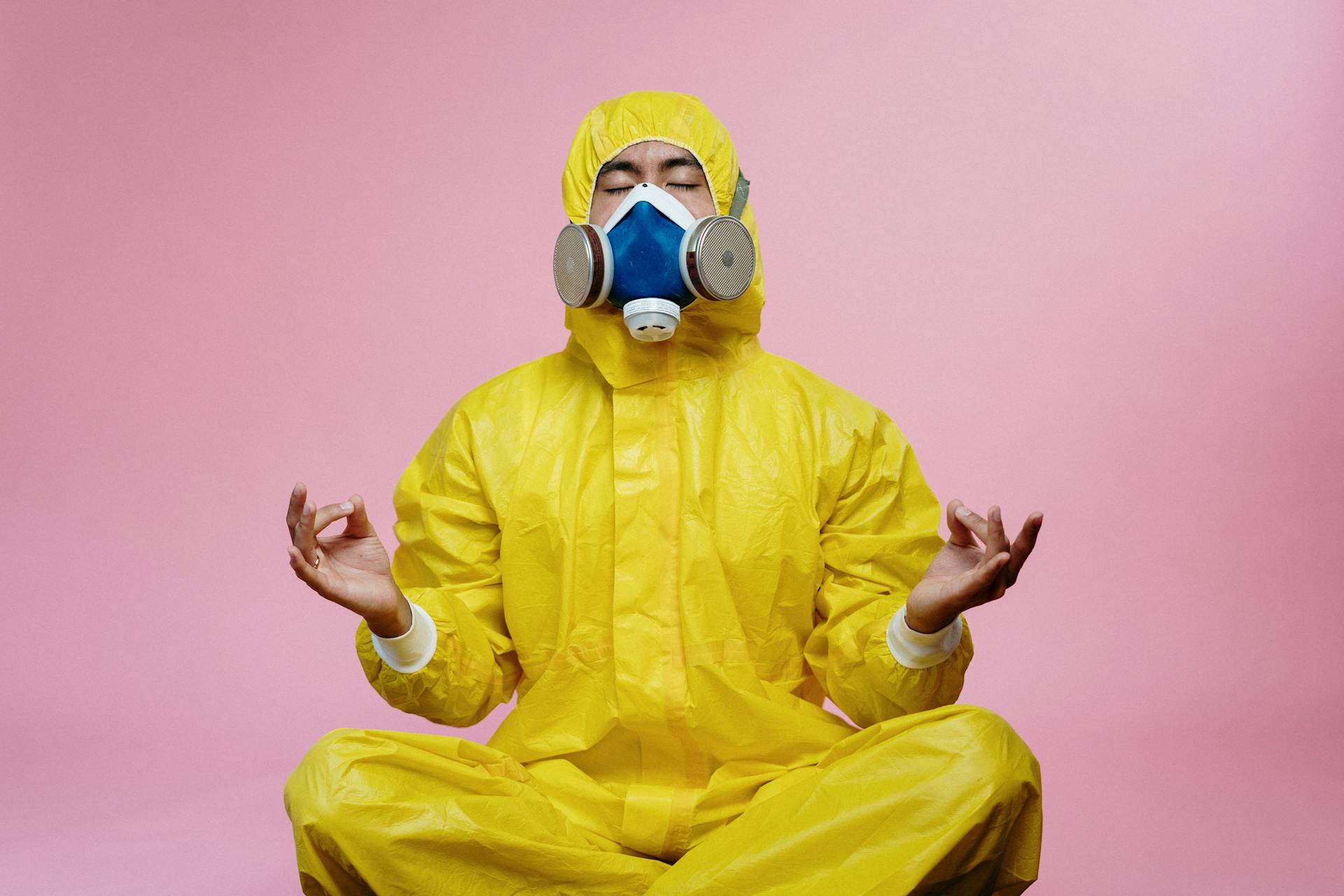
Personal Protective Equipment (PPE) manufacturing is essential for the safety of workers in various industries. The production of PPE involves using specialized equipment to create protective gear such as gloves, masks, and gowns. PPE manufacturing equipment includes cutting machines, sewing machines, and heat sealers. These tools help to streamline the production process and ensure that the final products meet industry standards.
The use of digital manufacturing software has greatly improved PPE production lines. With this software, manufacturers can easily track and monitor their production processes, which helps to identify areas where improvements can be made. Business tips such as improving inventory management and reducing waste can also be implemented with the help of manufacturing software.
In light of recent global events, the importance of PPE manufacturing cannot be overstated. The COVID-19 pandemic has highlighted the need for adequate supplies of protective gear for frontline workers in healthcare facilities around the world. By investing in PPE manufacturing equipment and utilizing digital manufacturing solutions, businesses can play a crucial role in ensuring that our essential workers have access to high-quality protective gear when they need it most.
Related reading: Ppe Manufacturing
Manufacturing control: creating a plan to optimize output
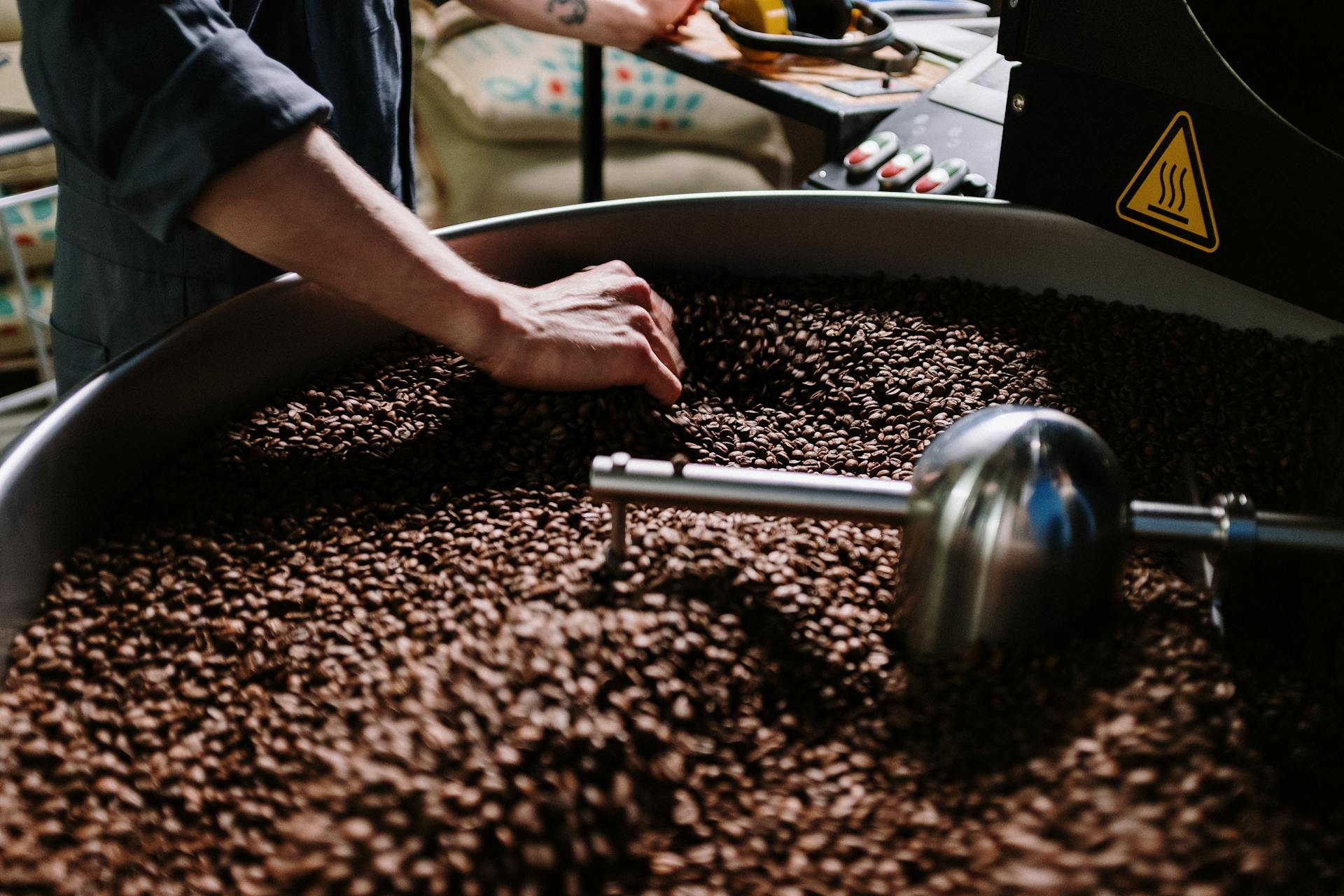
Manufacturing control is essential in creating an optimized output for your business. By implementing a well-structured plan, you can ensure that your products follow a consistent quality standard. With digital manufacturing tools, you can more easily monitor and adjust your production process to achieve the best results.
To optimize your manufacturing output, it's important to start with a solid plan. This involves considering factors such as the equipment and materials needed, the production timeline, and quality control measures. By taking these steps, you can ensure that your products consistently meet high-quality standards and that they are produced efficiently.
In conclusion, manufacturing control is crucial for achieving consistent high-quality results in any production process. With the help of digital manufacturing tools and effective planning techniques, you can optimize your output and streamline your operations. So if you're looking for ways to improve your business processes, be sure to keep these tips in mind!
Check this out: Manufacturing Process Automation
Boost Your Company's Efficiency with Digital Manufacturing
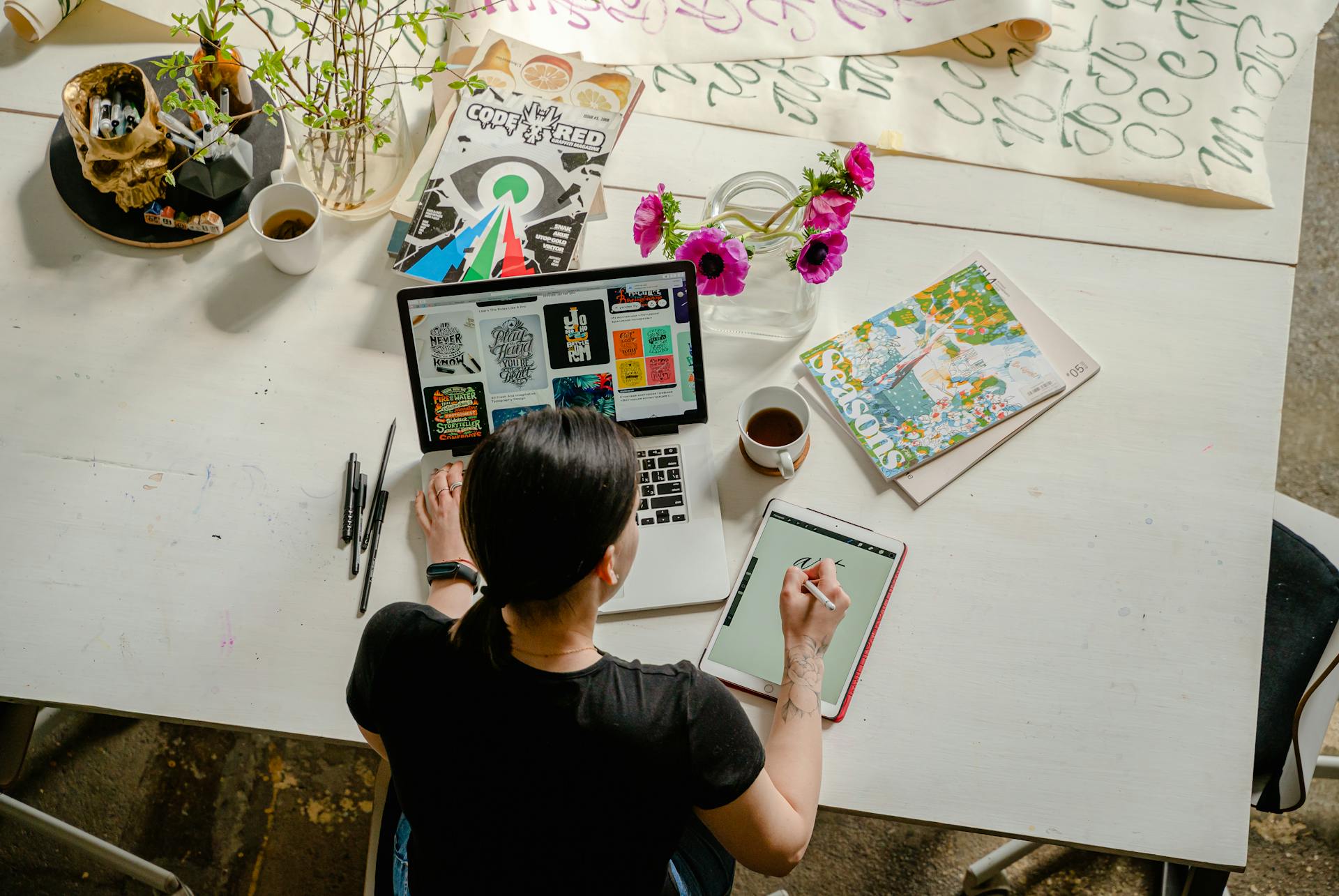
Are you tired of dealing with the limitations of a physical production line? It might be time to leverage digital manufacturing and embrace a digital workflow. Digital manufacturing allows for greater customization and the ability to create unique products, even personalized gifts or bespoke items for specific customers, without committing to a large traditional production run. Project digital manufacturing is a great option for anyone who wants to create a single item or small batch of products.
Digital manufacturing is a powerful tool that can help companies reduce costs and improve quality through the latest technology advances. A virtual prototype can be created quickly, allowing potential customers to see exactly what they are getting before any physical production takes place. This development process can also help identify potential problems early on, saving time and money in the long run. An ERP solution offering digital manufacturing integration can streamline the entire production line, making it more efficient than ever before.
If you're still unsure about whether digital manufacturing is an attractive option for your company, consider Katanas 14-day free trial. This platform allows you to explore all of the benefits of digital manufacturing without committing to anything long-term. With access to cutting-edge tools and technology, project management becomes easier than ever before. Don't let your company fall behind – embrace the power of digital manufacturing today!
Readers also liked: Manufacturing Company Tips
The common pitfalls of scaling digital transformations
Many companies unwittingly set themselves up for failure when pursuing digital transformations. One of the most common reasons for this is siloed implementation. Often, business leaders site operations manufacturing excellence at a single site experience failing to take into account wider network complexities, leading to a one-size-fits-all approach manufacturers miss the unique circumstances and culture of separate factory sites.
Another issue is analysis paralysis performing deep up-front analysis without gathering robust accurate-enough insights or developing a well-developed extrapolation methodology can lead to technology-first rollout means there is no clear link between opportunities and business challenges or capability requirements, resulting in undermining crucial buy-in from the people charged with making deployment work.
To overcome these issues, manufacturers need to embrace a shorter time-to-impact made possible through pragmatic minimal viable architecture, focusing on technology that can deliver quick results while building towards fully fledged ideal-state data-driven solutions. This approach ensures that industry 4.0 solutions don't become yet another theoretical exercise but result in tangible outcomes that drive growth and competitive advantage.
Tooling and processes[edit]
Tooling and processes are crucial elements in the digital manufacturing process, which utilizes computerized numerical controlled machines (CNC) to enable mass production. The digital manufacturing process involves creating a CAD model and using it to guide the CNC tooling in either subtractive or additive manufacturing. These are the primary categories of digital manufacturing, with subtractive making major strides in recent years due to advances in CNC technology. Overall, digital manufacturing has revolutionized the way products are made, offering unparalleled precision and efficiency.
Frequently Asked Questions
How is Industry 4.0 transforming the manufacturing industry?
Industry 4.0 is transforming the manufacturing industry by integrating advanced technologies such as artificial intelligence, Internet of Things, and big data analytics to optimize production processes, increase efficiency, reduce costs, and improve overall quality.
Should manufacturers wait to roll out Industry 4.0 solutions?
No, manufacturers should not wait to roll out Industry 4.0 solutions. Implementing these solutions can increase efficiency, reduce costs, and improve competitiveness in the long run.
How are digital transformations transforming the manufacturing value chain?
Digital transformations are revolutionizing the manufacturing value chain by automating processes, improving supply chain management and creating innovative products. This is leading to increased efficiency, productivity and profitability for manufacturers.
How are manufacturing workers relying on digital tools?
Manufacturing workers are relying on digital tools such as automation software, 3D printing, and augmented reality for design, production, and quality control processes to increase efficiency and accuracy.
How is digital technology transforming the workplace?
Digital technology is transforming the workplace by automating mundane tasks, increasing productivity, enabling remote work, and facilitating communication and collaboration. It's a game-changer for businesses looking to streamline operations and adapt to the digital age.
Featured Images: pexels.com