
The manufacturing industry has come a long way in recent years, thanks to manufacturing process automation. But, unfortunately, many people still have assumptions about automation that are simply not true. Some people envision conveyor belts and mass layoffs, with soulless robotic arms picking up the slack. However, this is not an accurate portrayal of the modern manufacturing business process.
In fact, the industrial robotics boom has made automated manufacturing systems an important tool for large-scale manufacturers looking to improve their daily operations. These tools perform repetitive manufacturing processes with ease and precision that humans simply cannot match. The use of robotic arms and other automated machines also frees employees from mundane tasks, allowing them to focus on more creative and value-adding tasks like inventory management tools or marketing strategies.
But it's important to note that manufacturing automation isn't limited to production lines or inventory orders purchasing – there are so many areas where automation can help streamline the entire manufacturing business process. So ado let's delve straight into how embracing a fully automated manufacturing system can help your business thrive in the future.
Additional reading: Automated Farming Equipment
Unveiling the Concept of Manufacturing Automation

Manufacturing process automation has become a key strategy for increasing growth in today's business world. It refers to the use of technological advancements to perform operations that were previously done by humans. This includes the use of robotic tools and production management software to streamline the manufacturing process and improve factory floor productivity.
Physical products are created through a series of steps that are collectively known as the manufacturing process. This process involves several specialized tasks, such as production planning, inventory management, and quality control. By automating these tasks, manufacturers can reduce costs and increase efficiency while producing high-quality products.
Process automation is an essential element of modern manufacturing. It offers a range of benefits for businesses looking to improve their bottom line. By implementing automated systems on factory floors, manufacturers can enhance productivity and reduce downtime while improving product quality and reducing waste. As technology continues to advance, we can expect to see even more innovative solutions that will help manufacturers stay competitive in today's fast-paced marketplace.
Readers also liked: Automated Inventory Management
1. Reduce costs and production waste
Reducing costs and production waste is one of the biggest challenges that businesses face in today's competitive market. To properly adopt lean inventory techniques, you need to track inventory movements and WIP manufacturing costs. Automated manufacturing can help you with this by providing real-time data on your operation progress, allowing you to make informed decisions about production.
By implementing automated manufacturing, you can handle multiple projects at the same time while reducing labor costs and improving quality control. This turn generating higher profits for your business. Moreover, it improves customer satisfaction by delivering products on time without any delay or defects. Overall, automation can help your business to streamline its operations and reduce waste while increasing profitability.
2. Improve response time
One of the main reasons for slow response times in manufacturing is the lack of real-time data. Without this information, it's difficult to make informed decisions about when to start production or adjust stock levels. However, manufacturing process software can help compensate for these issues by providing a wide range of data points that can be used to streamline and optimize manufacturing tasks.
Another challenge facing manufacturers is skilled labor shortages, especially in industries like automotive. This is where manufacturing process software really shines, as it's designed to automate many of the most time-consuming and repetitive tasks that would otherwise require highly skilled workers. By using software built specifically for these purposes, businesses can drastically increase their fulfillment rates while reducing the material required to do so. Overall, investing in modern manufacturing technology is key to improving response times and staying competitive in today's fast-paced market.
Recommended read: Manufacturing Lead Time
Automated manufacturing with cloud manufacturing software

Automated manufacturing has made life easier for scaling manufacturers by reducing manual labor and improving efficiency in the manufacturing industry. Katanas cloud manufacturing software is an all-in-one solution that has become one of our favorite business tools. With order fulfillment, supply chain, and customer service all integrated into one system, we can easily automate our entire process.
At first glance, terms like "process automation" might seem intimidating. However, the process automation definition is quite simple: it's a way to describe software that can automatically monitor inventory movement, manufacturing orders, and finished goods. With full power over automated manufacturing processes like raw materials inventory management and inventory tracking across multiple warehouses, Katanas intuitive visual platform makes it easy for even the most impromptu approach to production planning to achieve satisfactory results.
Before we introduced cloud manufacturing software like Katana into our workflow, we approached work ad-hoc and experienced delays in production planning and fulfillment rates. But since we've started using Katana's natural native interface and task list feature, team members with any level of experience can understand how our entire business operates with ease. Katanas efficient material purchasing plans have also helped us save on manufacturing costs without compromising on quality or quantity. Overall, Katanas intuitive process automation has significantly improved our business operations and allowed us to focus on growing our business in the most efficient way possible.
Recommended read: Process Automation
The different types of process automation systems
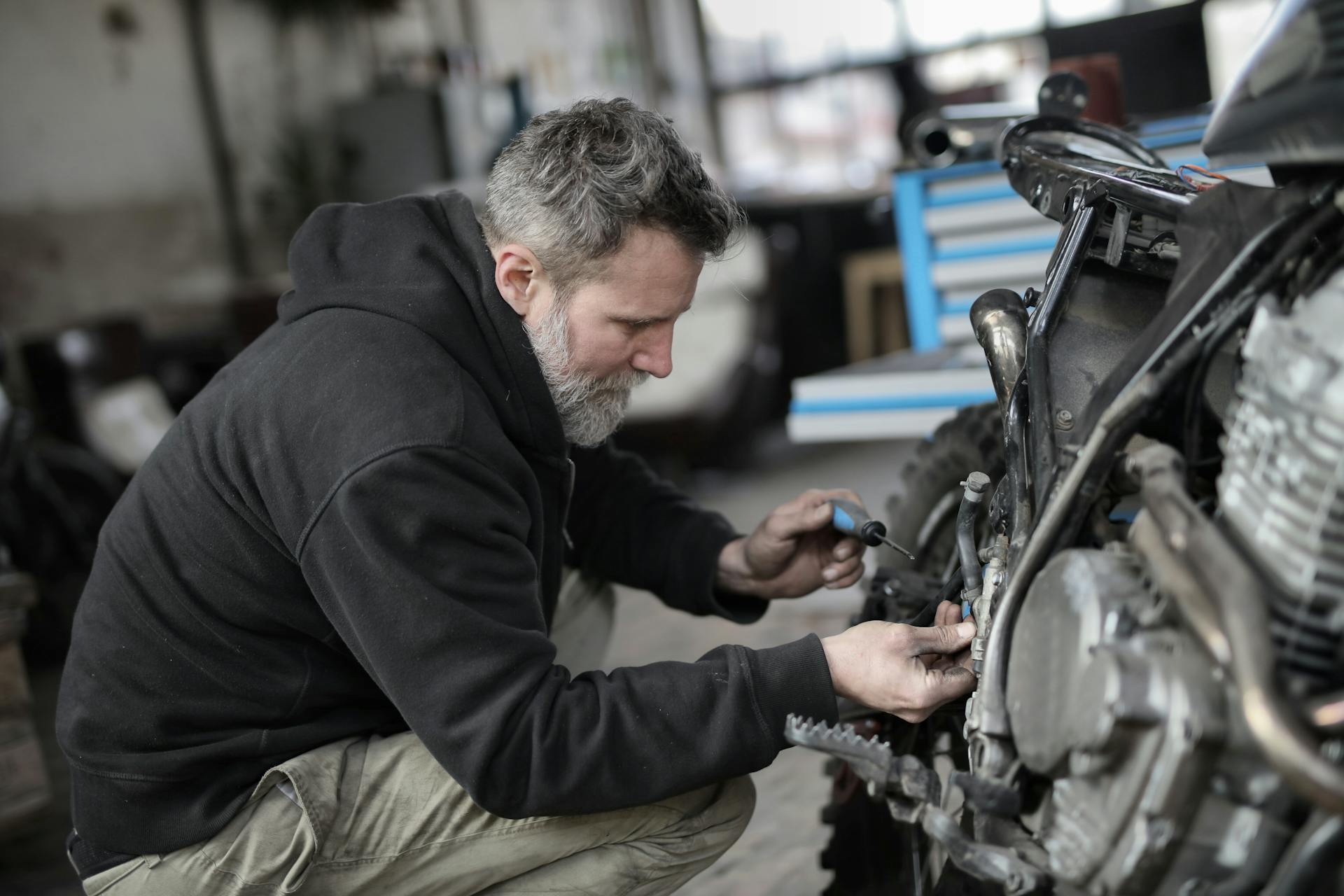
The manufacturing automation solutions can be categorized into three types of process automation systems, which are fixed automation, programmable automation, and flexible automation. Fixed automation is suitable for large manufacturers with high production volumes and little product variation. Programmable automation is designed for batch production with moderate levels of product variety. Flexible automation is ideal for small to medium-sized manufacturers that produce a wide range of products in low to medium volumes.
Curious to learn more? Check out: Automation in Construction
Discover the Fascinating Mechanisms behind Automation Works
Automation systems operate similarly to the human body. Just like how humans nerves relay messages to the brain, electrical signal sensors collect signals and transmit them to the input controller such as a CNC controller. The input device detects physical presence, pressure, smell molecules, ultrasonic pressure, RFID sensors or wireless waves and relays signals to the controller. This controller makes decisions based on these inputs and outputs signals to actuators devices that make a part move or display information such as opening a kiln door.
The simplest modern automation concept dates back to the 18th century when closed loop control was used in steam engine governors. A sensor detects a process variable (such as temperature) and compares it to its desired state. Open loop controllers do not compare states but instead use external inputs such as discrete controllers that respond when they detect moisture levels. Sequential controllers compare states of different sensors and trigger functions accordingly.
With the rudimentary development of proportional integral derivative (PID) controller originally used for analog control systems, Programmable Logic Controllers (PLC) evolved from specialized microprocessors used to replace hardware devices such as timers eventually becoming computers that are now used widely in production environments for centralized control of all aspects of manufacturing processes.
Intriguing read: Manufacturing Quality Control
Industries Utilizing Manufacturing Automation
The use of manufacturing process automation is a rapidly growing trend in many industries. The automotive industry is one of the leading sectors that have been utilizing automated manufacturing efforts. They are working alongside humans to ensure high-quality control and reduce human error. Some tasks require precise manufacturing automated reporting, which can be achieved with built-in safety features that can stop machinery in case of an emergency.
The medical industry is another sector that has been using automation to perform tasks at reduced rates while ensuring consistent product quality. To limit human interaction, many aspects of the medical industry rely heavily on improved food safety and reduced recall risks through automated tracking and reporting. This has also helped improve decision making by adjusting scheduling to reduce food waste and product loss.
The consumer goods industry depends on automated processes to meet demand while bleeding costs due to the labor shortage in manufacturing automation. This includes assembly, packaging, material handling, shipping, inspection, testing, scheduling, and more. With the use of tech products increasing the need for automated manufacturing robotics, they can drastically enhance production speed tests and remove defective products while maintaining optimal manufacturing conditions to create higher quality products at a lower production cost. The packaging industry also helps manufacturers stay competitive by keeping employees safer while improving packaging flexibility to accommodate larger and more diverse product varieties.
Consider reading: Purchase Order Automation
Discovering the Path of Automation in Manufacturing
The manufacturing industry based on current technological advances is undergoing a steep rise in manufacturing automation. Automation technology has allowed machines to efficiently perform complex tasks that were once only possible with human workforce. However, this doesn't mean robots can replace humans performing tasks altogether. The human touch is still needed to tackle present ergonomic and safety challenges and for problem-solving creativity people management.
Manufacturing automation tools can help manufacturers improve their business automation by streamlining manufacturing processes, achieving efficient production, and making smart data-driven decisions. Starting with data-collection and automated scheduling, manufacturers can include automating processes along the entire product cycle using related digital manufacturing systems such as enterprise resource planning (ERP) solutions, enterprise quality management systems (QMS), and coordinated material management systems.
While automation isn't necessarily designed to replace humans performing tasks, it's meant to help them retrained quicker and provide relief from physically laborious work. By embracing digital transformation strategies that incorporate automation technologies, manufacturers can create a more productive environment for both employees and businesses alike.
Consider reading: Digital Manufacturing
Discover the Magic of Automation in Industry!
In manufacturing, production environments automation has gained increasing acceptance as the industry leverages control systems to manage equipment and boost output. Keeping complex parts within ideal dimensions is crucial to achieving desired results, and automated production lines offer a solution to this challenge. Fixed production lines consisting of a transfer system, evolving part tools, and parts are controlled by a programmable logic controller (PLC) that manages work by controlling equipment timing.
Machining, creating and shaping parts, and assembling products are all related range of tasks that can utilize automation. The factory automation infrastructure describes the total collection of buildings, tools, utilities, and processes required for producing products effectively at scale. Robotics applications are an essential part of any modern manufacturing process automation system.
The continued work on automation provides manufacturers with an opportunity to streamline their operations and increase their productivity while reducing costs associated with labor-intensive tasks. In other words, maintaining automated production lines allows manufacturers to focus on higher-level tasks while ensuring consistency in product quality. The benefits of implementing automation go beyond just improving efficiency; it also enhances worker safety and reduces errors caused by human intervention.
See what others are reading: Manufacturing Agricultural Equipment
1. Four Types of Factory Automation Systems
There are four main types of automation systems used in manufacturing process automation. The first type is complete automation, which is designed for a specific purpose and is used to carry out production processes in a factory-related business without human intervention. This type of system uses computer-integrated manufacturing (CIM) integrated manufacturing automation and computerization CIM systems to control the production processes. The second type is flexible machine systems or flexible manufacturing systems (FMS) that extend the capabilities of programmable systems and enable changeovers to be made quickly, reducing production time for flexible systems that produce medium-sized lots.
Programmable automation systems make up the third type, which accommodates variation in objects batches, including numerical control machine tools, where a computer program runs to produce batches of similar products. These programmable automation lines include nonproductive periods when the system reprograms controls for new tasks. The fourth type is fixed automation systems, which are rigid and hard-wired into equipment dictates and generally limited to one product manufactured in high volumes. These four types of factory automation have revolutionized the way we manufacture goods, providing greater efficiency and productivity than ever before.
Curious to learn more? Check out: Manufacturing Control
2. Tools in Factory Automation
Industrial automation has come a long way since skilled machinists originally punched card instructions to run numerically controlled machine processes. Today, automated expressions rely on electrical signals for tool selection and tool movement as well as spindle speeds, making the manufacturing process more efficient than ever before. The part program consists of coded sequential machine instructions that the computer runs, combining uniformity, consistent quality, and a high rate of production.
Computer numerical control (CNC) relies on a computer processor to store, edit, and review coded part programs. When errors arise, operators can use command lines to perform steps or revise objects until they achieve the final design. Computer-aided manufacturing systems (CAM systems) streamline process planning, production scheduling, machining, and quality control while programmable logic controllers (PLCs) with hardened microprocessors harmonize signals between instruction actuators and human-machine interfaces. These serve as user-accessible means to monitor processes while advanced communication protocols like Ethernet systems enable work cells to easily communicate today.
Automation refers to two types of factory automation: caged automated systems where manual factory isolated work cells rely on efficient scheduling of mechanical steps islands; and inline assembly systems that work to produce large lots while minimizing product line changeover for related products with smaller lots. Inline assembly production is often the slowest task in the manufacturing process requiring accurate planning and specialized engineering required for purpose-built lines that ensure constant throughput of inline assembly using minimal human labor.
A different take: Barcode Systems for Manufacturing
3. Equipment in Factory Automation
In automated production, equipment plays a key role in the manufacturing process. Image-capture equipment and image sensors are essential for capturing visual data to inform decisions made by automation systems. Storage devices are also necessary for storing data that is recorded by image-capture equipment and other measurement equipment used in the manufacturing process.
Illumination systems and optical subsystems are critical components of image-capture equipment, providing lighting that enables vision systems to capture images of products moving down the production line. System boards are another essential component, serving as the backbone of automation systems that control machinery and collect data on various aspects of the manufacturing process. Overall, these pieces of equipment work together to enable manufacturers to streamline their operations and increase productivity.
Frequently Asked Questions
Do all factories approach industrial automation the same way?
No, factories approach industrial automation differently depending on their needs and resources. Factors such as industry type, production volume, and budget all play a role in determining the automation strategy.
Is automation the future of manufacturing?
Yes, automation is the future of manufacturing as it allows for increased efficiency, productivity, and cost savings. With advancements in technology such as AI and robotics, the role of automation in manufacturing will only continue to grow.
What are the advantages of automation systems on the factory floor?
Automation systems on the factory floor bring many advantages such as increased production efficiency, improved product quality, reduced labor costs, and enhanced worker safety.
What can automation do for the manufacturing industry?
Automation can improve efficiency, increase productivity, reduce costs, and enhance safety in the manufacturing industry by using machines and technology to perform tasks that were previously done manually or with human intervention.
What will the future of manufacturing look like with AI?
The future of manufacturing with AI will be characterized by increased efficiency, reduced costs, and improved quality control. AI-powered machines will automate repetitive tasks while providing real-time insights to enhance decision-making processes.
Featured Images: pexels.com