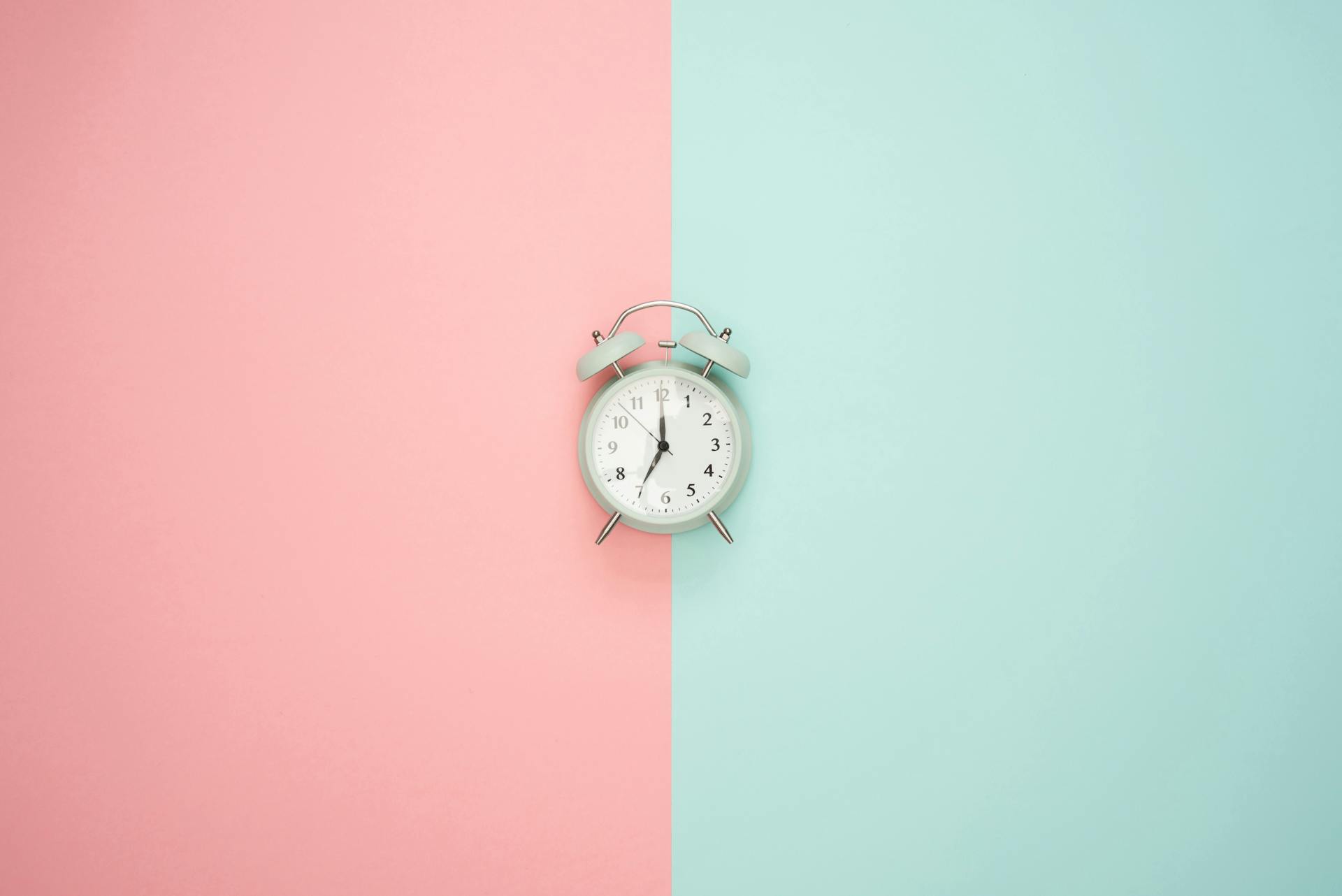
Manufacturing lead time is the duration between the initiation of a manufacturing process and its completion. No-one likes to wait for long periods for their products to be manufactured, which is why reducing manufacturing lead times is crucial for small scale manufacturers. The difference between a 20 minutes wait time and a 10 minutes one can make all the difference in whether customers feel worth it or not.
Understanding lead times and how to reduce them is essential for any manufacturer looking to stay competitive in today's market. There are several tools needed for scheduling efficiently and reducing lead times, but there are no short cuts when it comes to implementing production scheduling software that can help manufacturers lower their lead times. With many businesses offering a 14-day free trial of their software, there is no excuse not to try out this solution.
Curious to learn more? Check out: Lead Tips
Understanding Lead Time: Everything You Need to Know
Lead time is the amount of time it takes from when a manufacturing order is placed until the product is completed. It includes scheduling production, processing time, and time spent making purchases. Let's imagine you're managing a company that produces wooden model bicycles. To make these bicycles, you need to source wood, wheels, pedals, and other materials. The lead time for each of these components will vary depending on suppliers and shipping times.
Manufacturing lead time takes place once all the necessary materials have been gathered. This includes the time it takes to actually produce the bicycle itself. Completing production can take several days or even weeks depending on the complexity of the product. Keep in mind that lead times can also be affected by unexpected delays like machine breakdowns or inclement weather.
The term people often confuse with lead time is processing time. Processing time refers only to the actual amount of productive work being done on a product. Understanding manufacturing lead times lets quickly explore how long it takes for your business to produce a finished good and deliver it to your customer base. By effectively managing your lead times, you'll be able to provide accurate delivery dates and avoid frustrating your customers with delays.
1. Lead Time vs Cycle Time
Lead time and cycle time are two terms that often get used interchangeably, but they actually have varying definitions. Lead time refers to the amount of time it takes from when a customer places an order until the product is delivered to them, while cycle time refers to the amount of time it takes to complete a specific process within the manufacturing lead time.
When talking about manufacturing lead time, it's important to understand that the clock starts ticking as soon as an order is placed. This means that lead time starts at the moment actual work starts on fulfilling the order, while cycle time starts at a specific point within that process. The order fulfillment cycle doesn't end with manufacturing - it can also include processes like purchasing and shipping - which is why understanding both lead time and cycle time is crucial for delivering products in a timely manner.
Ultimately, what matters most is how long the customer perceives they're waiting for their product - whether it's during lead or cycle times doesn't matter much to them. From a manufacturer's perspective though, understanding these concepts helps ensure efficient production processes and avoids delays that could result in unhappy customers waiting for their magnificent model bicycle.
Readers also liked: Manufacturing Process Automation
Speak Up: Share Your Thoughts and Ideas
Manufacturing lead time is a crucial part of any supply chain. Whether you're in the food and beverage industry, health and beauty, or home goods, reducing lead time can help improve customer satisfaction and increase sales. With the right tools and training support, smart inventory management can help reduce lead times and optimize your warehouse management system.
If you're looking for an ecommerce inventory management software with pick pack ship and catalog features, look no further than our product line! Our software provides press awards-winning solutions for Amazon FBA inventory management, toys & games, tools & calculators, and many more industries. Plus, our customer support team is always available to answer your ecommerce inventory management questions.
To comment on this article about manufacturing lead time or any other topic related to inventory management software, simply leave a comment below. We value your feedback! Please note that your email address will not be published; required fields are marked *. This helps us reduce spam learn more about our readership demographics. Additionally, we use cookies to collect comment data in order to better understand how our content is being received by our audience.
Explore further: Project Management for Manufacturing
Discover the True Meaning of Manufacturing Lead-Time
If you're new to manufacturing, you may have some common questions about lead-time. To define lead-time simply, it's the time it takes for a customer to receive stock after they place an order. Lead-times affect every aspect of the manufacturing process, from when you're relying on outsourced products to how fast your supply chain works.
As mentioned earlier in this article about manufacturing lead-time, understanding lead-times is essential to running a successful manufacturing business. It's important to note that lead-times aren't just determined by your own manufacturing process; they can also be influenced by external factors like shipping delays or supplier errors.
To make your supply chain work faster and more efficiently, it's crucial to understand how lead-times affect your business. By analyzing and optimizing your lead-time data, you can improve customer satisfaction and increase profits. So next time you hear someone talking about manufacturing lead-time, remember that it's not just a buzzword – it's a critical part of your business strategy.
Worth a look: Discrete vs Process Manufacturing
Effortlessly Cut Manufacturing Lead-Times with These Tactics
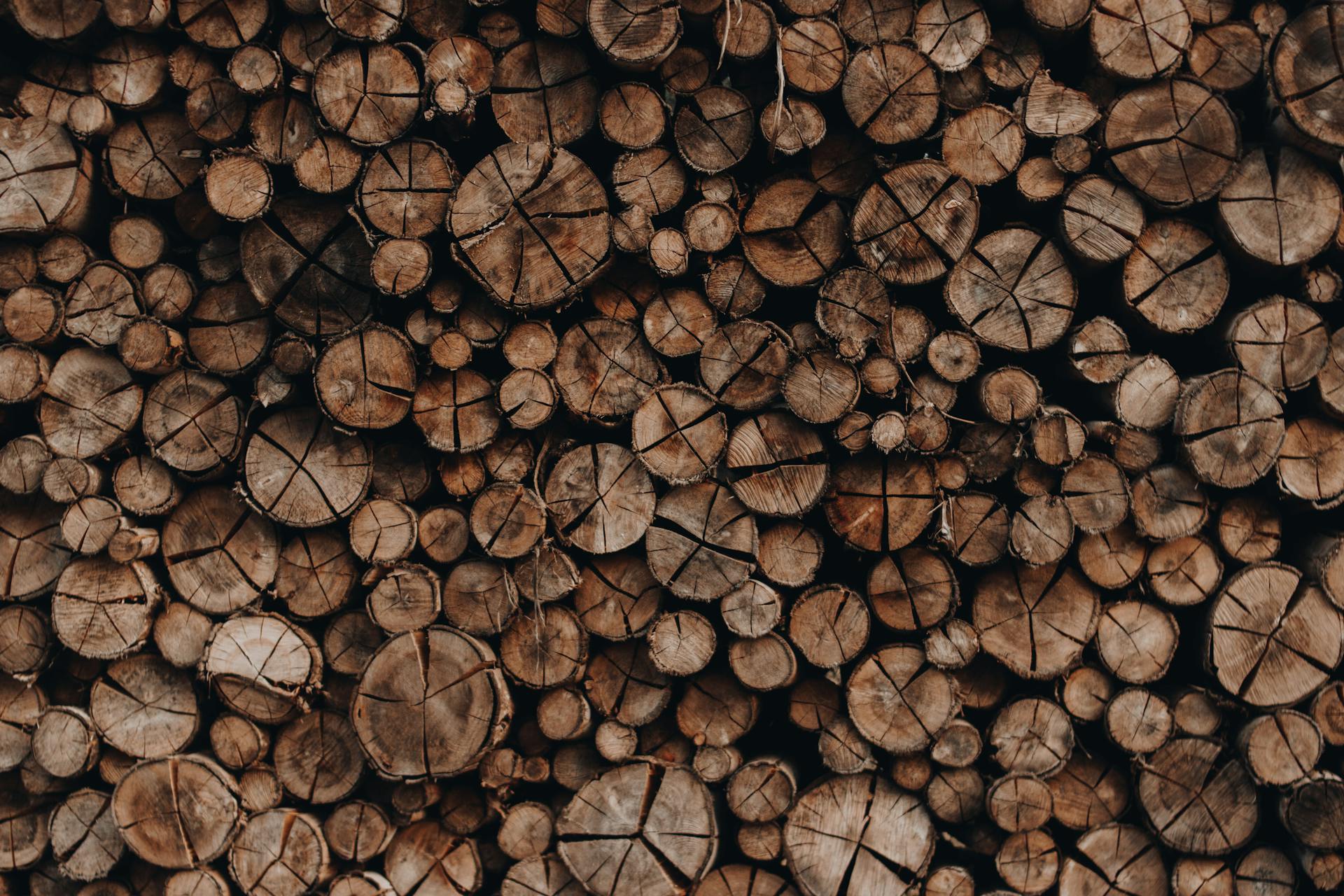
Lead times, let's talk about how to cut them down. There are a few tactics that can help you streamline your manufacturing process and reduce the time it takes to get products out the door. From optimizing your supply chain to implementing lean manufacturing practices, there are several ways to make your operations more efficient and effective. By taking advantage of these strategies, you can reduce lead times and improve your bottom line – all without sacrificing quality or customer satisfaction.
1. Order smaller amounts
Ordering smaller amounts can be a wise strategy when it comes to manufacturing lead time. Placing gigantic orders may seem like a cost-effective way to replenish products, but it can inadvertently increase lead time and cause delays in getting orders fulfilled.
An agile approach that involves ordering smaller amounts more frequently can cut manufacturing lead time and potentially save a business a significant margin. While bulk order discounts may seem appealing, the benefits of frequent orders and quicker supplier fulfilment should not be overlooked. By being mindful of the size of their orders, businesses can take control of their manufacturing processes and ensure timely delivery of their products.
2. Use a lead-time contract
One way to manage manufacturing lead time is by using a lead-time contract. This type of contract is extremely clear and protects both parties from unexpected delays, such as damaged shipments or discontinuation notifications. A clear contract ensures that neither party is caught off-guard when it comes to the business's lead time.
Without a lead-time contract, delays can wreak havoc on a business's lead time, leading to frustrated customers and lost profits. But with a solid agreement in place, delays don't happen delays, and any potential issues such as price changes or product discontinuations are addressed upfront. Overall, using a lead-time contract can save time, money, and headaches for all involved parties in the manufacturing process.
Intriguing read: Contract Manufacturing
3. Use inventory management software
Using inventory management software is like pressing the "easy button" for your manufacturing lead time. With multiple spreadsheets involved in the supply chain, there's plenty of room for human error. However, an inventory management software solution can help you avoid costly mistakes and streamline your processes.
By using inventory management software, you'll have a bird's eye view of every aspect of your supply chain. This means that you can easily track inventory levels, demand, and production schedules without having to manually comb through spreadsheets. Not only does this improve accuracy, but it also saves valuable time that can be spent focusing on other important aspects of your business. So if you're looking for a way to simplify your supply chain and reduce manufacturing lead times, an inventory management software solution is the way to go!
Boost Your Business by Shortening Manufacturing Lead Times
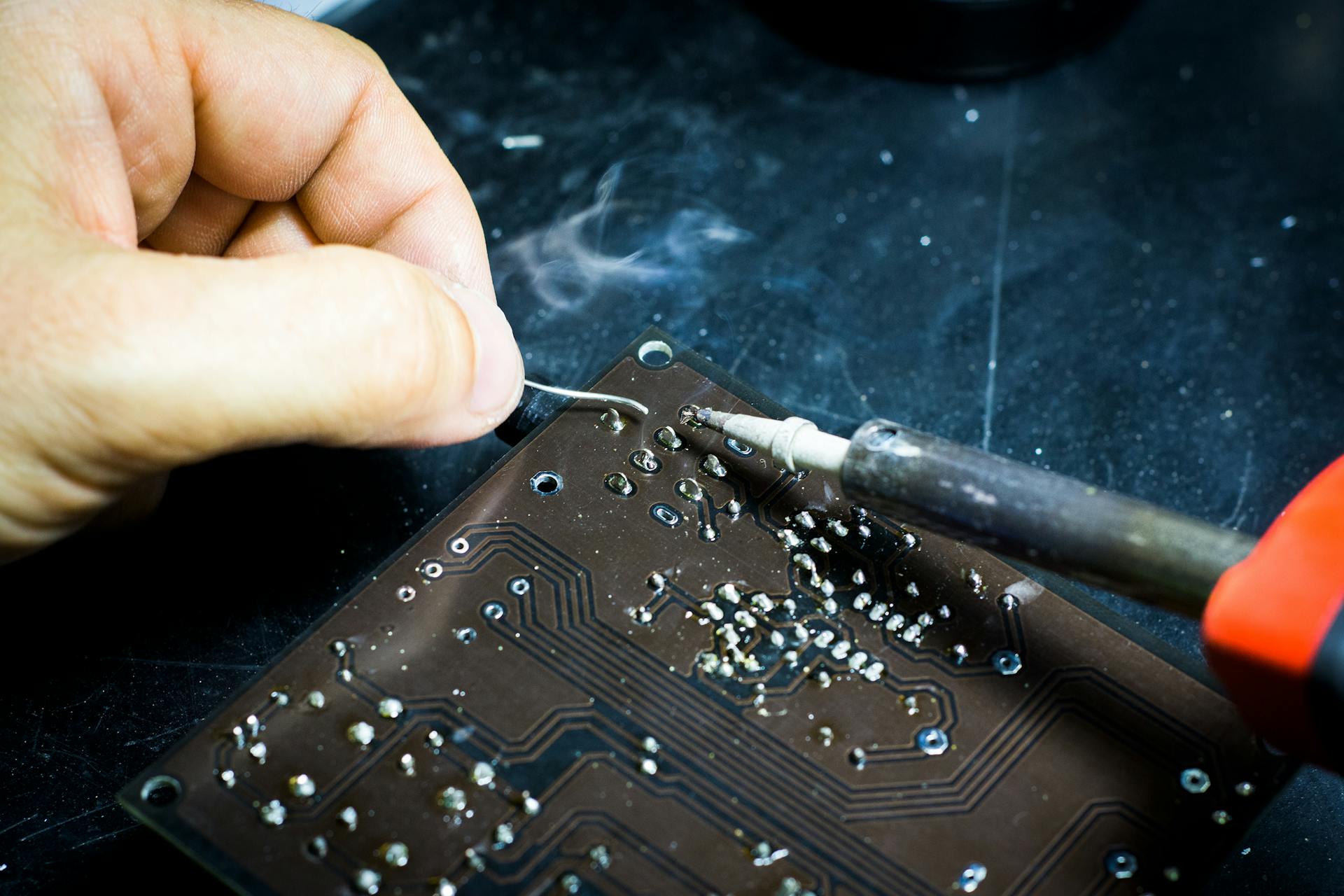
Understanding lead times is crucial to the success of any manufacturing business. The time it takes to manufacture a product from start to finish, including sourcing materials and shipping, is known as lead time. It's the biggest contributing factor to a company's overall efficiency and profitability. Shorter lead times can help businesses save money, increase productivity and ultimately boost their bottom line.
Reducing lead times requires a deep understanding of your supply chain and optimizing each step in the process. By streamlining communication between suppliers, manufacturers, and distributors, you can minimize delays and get products to market faster. In today's fast-paced marketplace, where customers demand speedy delivery, cutting down on manufacturing lead times can be the key to staying ahead of the competition.
1. An Examole of What Happens if You don’t Understand Lead Time
An Example of What Happens if You don’t Understand Lead Time:
Research shows that understanding lead time is crucial in manufacturing. If you don't understand the concept of lead time, you could end up with dead stock or delayed orders. For instance, let's say you run a small business that sells handmade jewelry. You receive an order for 50 necklaces and assume it's a simple process to make them. However, because you didn't research material and production lead times, it takes longer than expected to receive the necessary supplies. This delay causes a backlog in your production schedule, which means customers' orders are delayed as well.
To avoid creating bottlenecks and resolve customer wait times, it's important to understand manufacturing lead time. Manufacturing lead times can be broken down into material and production lead times, as well as cumulative lead times that take into account all the stages of production. By understanding these factors, you can better estimate how long it will take to complete an order and avoid any delays that may cost you time and money down the road.
Maintain Product Quality When Reducing Manufacturing Lead Time
Decreasing lead time is crucial when it comes to the manufacturing industry. However, reducing lead times doesn't mean sacrificing product quality. Maintaining high-quality standards is a must for customer satisfaction, and that should be the ultimate goal of any manufacturer. One way to do this is by implementing world scheduling, where team members work simultaneously on different tasks without malice intended towards one another.
Floor level operations can also help in reducing lead times while maintaining product quality. By optimizing workstations' layout and ensuring that each workstation decreases waiting time, efficiencies are increased without compromising the quality of the final product. Quality assurance should also be implemented throughout the process to ensure minute details are not overlooked.
Working alternately rather than having workers stuck with tunnel vision on one task can also reduce lead times without affecting final product quality. This allows team members free hands to assist others where necessary and ensures they step out from a single task to look at the bigger picture. The balance struck between reducing lead times and maintaining product quality should always be top of mind as knock-on effects on customers' satisfaction may have severe consequences on inventory valuation methods in the worst-case scenario. Hard work sadly does not always equate to success; it's the right steps needing taking that will result in reduced manufacturing lead time while maintaining absolute perfection for your final product.
Curious to learn more? Check out: Manufacturing Quality Control
Frequently Asked Questions
What is the abbreviation for manufacturing lead time?
The abbreviation for manufacturing lead time is MLT.
What does lead time mean in business?
Lead time in business refers to the amount of time it takes from the start of a process until its completion, including ordering, manufacturing, and shipping. It is an important metric for businesses to consider when planning production and delivery timelines.
What is supply chain lead time?
Supply chain lead time refers to the amount of time it takes for a product to move from the initial stage to final delivery to the customer. It includes all the processes involved in procurement, production, and transportation.
How to manage lead times?
To manage lead times, you should establish clear communication with your suppliers, accurately forecast demand and plan production accordingly, and regularly review and adjust your inventory levels. By doing so, you can ensure timely delivery of products to customers while minimizing stockouts and excess inventory.
What is lead time reduction?
Lead time reduction refers to the process of decreasing the amount of time it takes for a product or service to be delivered to the customer. This can involve streamlining production processes, improving supply chain management, and implementing more efficient logistics strategies.
Featured Images: pexels.com