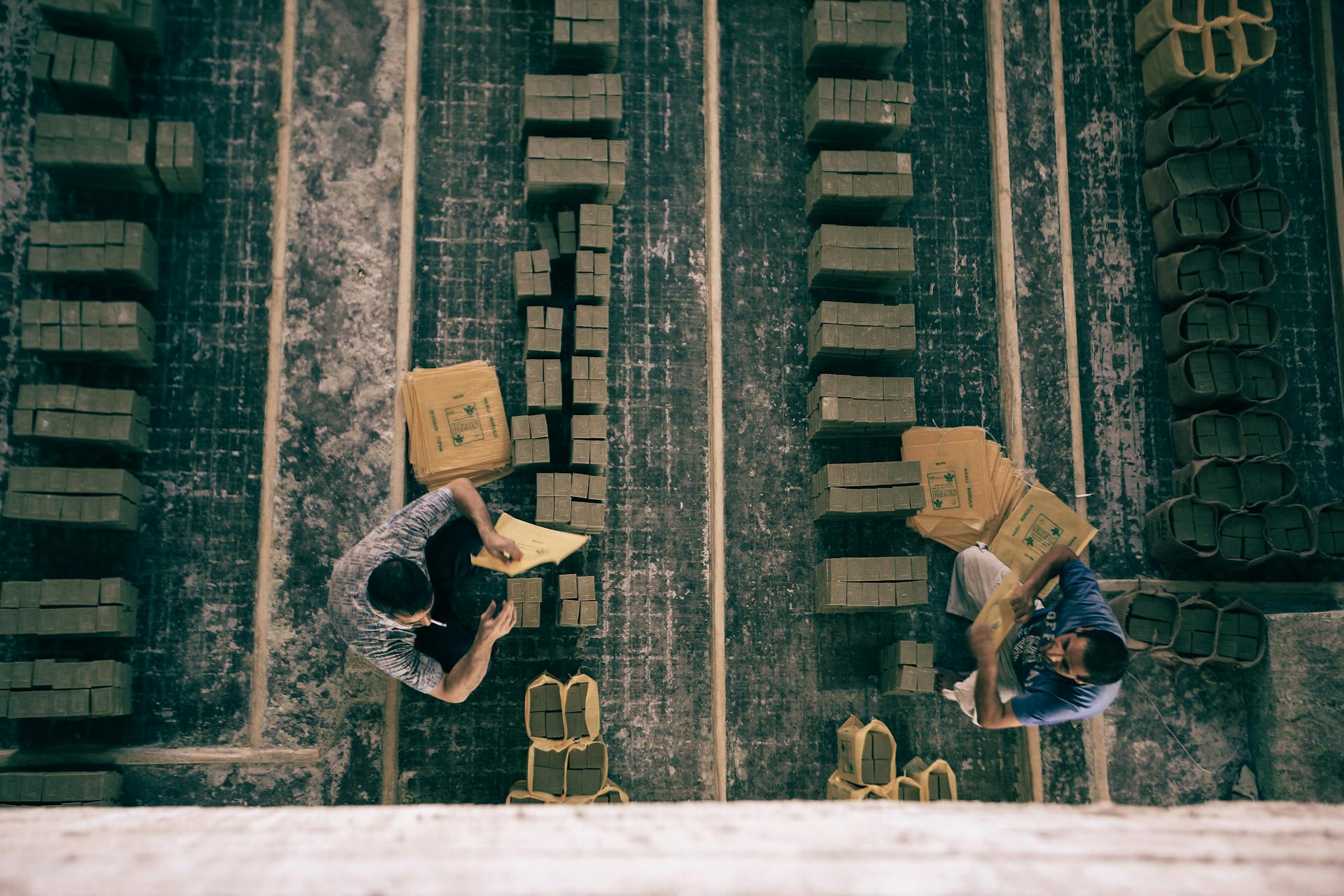
Optimizing the manufacturing process is crucial for a company's success. This involves streamlining production to increase efficiency and reduce costs.
Companies can achieve this by implementing lean manufacturing techniques, which eliminate waste and focus on producing high-quality products. This approach has been successfully adopted by many businesses, leading to significant improvements in productivity and profitability.
Streamlining production involves analyzing and optimizing each stage of the manufacturing process. For instance, automating tasks and implementing just-in-time inventory management can help reduce lead times and improve delivery schedules.
Effective communication and collaboration among team members are also essential for process optimization. By working together, teams can identify areas for improvement and implement changes that benefit the entire production line.
For another approach, see: Manufacturing Process Automation
Types of Manufacturing
There are several types of manufacturing processes that businesses can adopt. Repetitive manufacturing is used for high-demand products like automobiles or electronics, and involves a 24/7 production line producing identical items at a high output rate.
Discrete manufacturing, on the other hand, uses an assembly or production line, but the products vary, requiring operations to change to compensate. This type of manufacturing is often used for products that require customization or have unique features.
Batch manufacturing produces items in batches to meet customer demand, which can be a single batch or continuous in nature. Job shop manufacturing involves production in a small workshop area with no assembly line, and is commonly used for low-volume custom orders.
Here are the main types of manufacturing processes:
Assemble to Order (ATO)
Assemble to Order (ATO) is a manufacturing approach where components are stocked and ready for assembly when a sales order is received. This method allows for some customizability, but not to the same extent as make-to-order.
In an ATO system, products might have some customizability, but it's not as flexible as make-to-order. The key benefit of ATO is that it allows businesses to offer products with some level of customization while still maintaining a relatively short lead time.
Broaden your view: Purchase Order Process
Businesses that use ATO often have a production workflow that involves stocking components and then assembling them into finished products when a sales order is received. This approach can be beneficial for businesses that need to offer products with some level of customization.
Here's a comparison of ATO with other manufacturing approaches:
Discrete manufacturing is often used in ATO systems, where each product manufactured can be specifically identified and tracked using a bill of materials. This approach is beneficial for businesses that need to offer products with a high level of customization.
Batch
Batch production manufacturing is a type of manufacturing process that involves producing a limited number of products at a time. This process is halted after the production numbers are met, and production is resumed again after a period of pause. The amount of products produced usually depends on the customer's order.
The products in a batch are highly consistent, but there can be variations between two different batches. This allows for quality control and machinery testing during the waiting time between batches. It also makes inventory management and utilization easier.
Worth a look: Production Planning
Batch manufacturing involves producing items in batches to meet customer demand. This can be met with one batch, several, or the batch process can be continuous in nature.
Here are some key characteristics of batch production manufacturing:
Batch production manufacturing is commonly used in industries where products are made to order, such as custom machinery or specialized aircraft parts.
Custom
Custom manufacturing is a mode of production that's centered around unique customer specifications. It's often used for one-off or limited runs of a particular product.
The customers dictate the exact parameters for the product, ranging from design to functionality. This can result in significant delays in delivery time.
Custom manufacturing is intrinsically linked to specificity, making it a great option for products that require unique features or customization. The initial investment is typically moderate, given that production kicks off only after an order is confirmed.
Pre-payment is usually part of the transaction process, which can help manage cash flow and production costs. However, custom manufacturing can be challenging due to its reliance on individual orders.
You might like: Production Management
Here are some common characteristics of custom manufacturing:
- Production only commences once an order is placed and detailed specifications are provided.
- Lead time for each product can be extensive.
- Customers dictate the exact parameters for the product, from design to functionality.
This type of manufacturing is often used in industries such as aerospace, construction, or technology, where specialized products are being made for a very specific purpose. Custom manufacturing can also result in a premium for the products, as they may not be easily acquired in a marketplace.
Manufacturing Methods
There are several manufacturing methods available, each with its own strengths and weaknesses. Some of these methods include assembly line manufacturing, which was a driving force behind the industrial revolution.
Assembly lines are commonly used in mass production industries, where products are created in an assembly plant and then shipped to customers. This method is often used for products that have a long shelf life, such as automobiles and electronics.
Manufacturers can also adopt different types of manufacturing processes, including repetitive, discrete, job shop, continuous, and batch manufacturing. These processes can be used in various industries, such as mining, where materials are extracted and processed in a continuous manner.
Here are some common types of manufacturing processes:
- Repetitive manufacturing: Uses an assembly or production line to produce identical items at a high output rate.
- Discrete manufacturing: Utilizes an assembly or production line, but products vary, requiring operations to change.
- Job shop manufacturing: Creates smaller batches of products at different rates.
- Continuous manufacturing: Uses a 24/7 production line to produce materials like gases, liquids, and chemicals.
- Batch manufacturing: Produces items in batches to meet customer demand.
Manufacturing, Transport, and Assembly Options
Make-to-stock (MTS) is a traditional manufacturing technique where products are manufactured anticipating potential demand and stored in inventory. This allows customers to get the product instantly when desired.
In MTS, manufacturers can use prior sales to estimate production volume, and estimates can also be based on market research. This approach provides the advantage of the shortest lead time, as products are ready before customer demand.
However, MTS has a main disadvantage: high upfront costs. Large-volume production beforehand requires a significant investment, and there's a risk of products going unsold, resulting in losses.
For smaller industries, like furniture-making, on-demand manufacturing models can be employed to adjust production volume according to market demand. This helps with inventory management and allows for more flexibility.
On a larger scale, manufacturers may use batch production to have readymade orders before the market requires them. However, production volume is limited due to shifting market trends and required capital.
Here are some common manufacturing, transport, and assembly options:
Assembly lines, as seen in mass production industries, are another option. After products are created in the assembly plant, they are shipped to customers, usually with no post-processing required after the assembly stage.
Manufacturers and Workflows
Repetitive manufacturing is a type of manufacturing process that uses an assembly or production line running 24/7 to produce identical items at a high output rate.
This type of manufacturing is typically used for products that are in high demand or have a long shelf life, like automobiles or electronics.
Discrete manufacturing utilizes an assembly or production line, but the products will vary, requiring operations to change to compensate.
Continuous manufacturing, on the other hand, is the same as repetitive manufacturing, using a 24/7 production line, but its production materials are not countable, like gases, liquids, and chemicals.
Batch manufacturing produces items in batches to meet customer demand, which can be met with one batch, several, or the batch process can be continuous in nature.
A fresh viewpoint: Batch Manufacturing
Here are some common types of manufacturing workflows:
Job shop manufacturing makes use of production areas, creating smaller batches that can be manufactured at different and more desirable rates.
Manufacturers may also adopt a Make-to-Order (MTO) workflow, where production starts only after a customer places an order, eliminating upfront production costs and reducing the risk of unsold products.
However, MTO workflows often come with uneven product demand, resulting in slower periods of business.
Make to Assemble (MTA)
Make to Assemble (MTA) is a manufacturing technique that's often used in industries where customization is key. This method involves manufacturing subparts of a product beforehand, but product assembly takes place after the customer orders the product.
The MTA model combines some benefits of Make-to-Supply and Make to Order, allowing for short waiting times after customer orders and product customization. This is because the component parts are manufactured beforehand, enabling quick assembly and delivery.
Companies that use MTA often get a head start by starting production on component parts, which can lead to faster delivery times for customers. However, there's still a risk of being stuck with inventory that doesn't materialize, and the company may lose the benefits of Make-to-Order and Make-to-Stock processes.
To understand the MTA process better, let's break it down into its key components:
By understanding the MTA process, businesses can make informed decisions about their manufacturing strategies and meet the evolving needs of their customers.
Metal Fabrication
Metal fabrication is a crucial part of the manufacturing process, working with metal raw materials to create products for various industries.
It meets the requirements of industries such as automotive, agricultural, and industrial machinery, among others.
Metal fabrication can operate in job shop manufacturing models or larger-scale production lines.
This versatility allows metal fabrication to cater to a wide range of products and industries.
Some common examples of metal fabrication include pipes, turbine rings, metal plates, sheets, and automobile frames.
Metal fabrication is essential for producing complex products that require precision and accuracy.
It's a vital part of the manufacturing process, and its applications are vast and varied.
A unique perspective: Discrete vs Process Manufacturing
Product Design
Product Design is a crucial stage in the manufacturing process. It's where the product is materialized into engineering graphical designs, taking into account the dimensions of each product feature.
A business plan helps manufacturers outline the manufacturing number and scaling strategy, which is essential for product design. Various product materials are shortlisted at this stage, ensuring the final product meets customer needs.
Research considerations play a significant role in product design, as it incorporates any manufacturing limitations discovered during the research stage. This helps manufacturers create a product that is not only profitable but also meets customer demands.
During this stage, the manufacturing process is deeply rooted in research and development, which enables manufacturers to forecast their product profitability.
Raw Materials
Raw materials play a crucial role in manufacturing. Their prices can fluctuate, affecting product costs.
The price of a product is based on the prices of raw materials during product design. This means that even if manufacturers want to adjust product prices, they may not have the freedom to do so if raw material prices increase unexpectedly.
Manufacturers have to be prepared for unexpected price hikes. This is why it's essential to keep an eye on raw material prices and adjust production plans accordingly.
Here are some types of raw materials commonly used in manufacturing:
- Metals, such as those used in the metal fabrication sector
- Concrete, lumber, bricks, and other materials used in construction materials manufacturing
These raw materials are used in various sectors, including automotive, agricultural, industrial machinery, aviation, and construction materials manufacturing.
For another approach, see: Bill of Materials
Manufacturing Strategies
Manufacturing Strategies involve different approaches to producing parts. The assembly line manufacturing process uses finished products from repetitive manufacturing, making it a quicker process as only the joining of various components is required.
Manufacturing process requirements vary depending on the approach used. The assembly line process has a quicker production time compared to other methods.
In manufacturing, the choice of strategy depends on the specific application and desired outcome.
On-Demand
On-Demand manufacturing is a process that's all about customization. It involves producing small batches of products after receiving customer orders, with customers often specifying their product requirements.
This approach requires a low initial investment, but it does have a drawback - long lead times. An order goes into production only after customers place their order, which can result in a very long production time.
On-Demand manufacturing is often used for products that have a long shelf life, such as electronics or automobiles. It's also a great way to meet customer demand, as you can produce items in batches to meet specific needs.
Here are the different types of manufacturing processes, including On-Demand:
- Repetitive manufacturing
- Discrete manufacturing
- Job shop manufacturing
- Continuous manufacturing
- Batch manufacturing
Note that On-Demand manufacturing is not the same as Continuous manufacturing, which produces materials like gases, liquids, and chemicals 24/7. On-Demand manufacturing, on the other hand, produces small batches of products after receiving customer orders.
In the case of On-Demand manufacturing, customers often provide part of the payment in advance. This approach requires a flexible production system that can adapt to changing customer needs.
PA Innovation Program
Pennsylvania is a hub for innovation in manufacturing, thanks to the Manufacturing PA Innovation Program. This program brings together businesses and top research institutions to advance new products or process innovations.
Undergraduate and graduate student fellows at PA universities work closely with manufacturers to drive innovation. They're not just theoretical experts, but hands-on problem solvers with real-world experience.
The Manufacturing PA Innovation Program is just one example of how Pennsylvania is investing in its talent pipeline. With an emphasis on job training for in-demand career pathways, the state is ensuring its companies and communities stay globally competitive.
Manufacturing has a significant economic impact in Pennsylvania, exceeding $116 billion and accounting for over 10% of all jobs in the state. With over 566,800 residents employed in the industry, it's clear that manufacturing is the backbone of the economy.
The National Additive Manufacturing Innovation Institute (NAMI) is another important initiative that's increasing the country's global manufacturing competitiveness. As a public-private partnership, NAMI brings together industry, government, academia, and workforce leaders to drive innovation and growth.
By supporting programs like the Manufacturing PA Innovation Program and NAMI, Pennsylvania is setting itself up for success in the manufacturing industry. With a strong focus on innovation, education, and job training, the state is poised to remain a leader in global manufacturing for years to come.
Take a look at this: Digital Marketing Strategy for Manufacturing Industry
Do Small Manufacturers Earn Big Profits?
Manufacturing can be a lucrative field, but it's not a guarantee of megabucks. In 2017, the average manufacturing worker in the United States earned $84,832 annually.
The industry's size makes it hard to quantify individual profits, but we can look at some examples. In 2008, the average revenue of a sole proprietorship ranged from $11.9 thousand for unclassified establishments to $1.1 million for coal mines.
Some sub-sectors, like the fashion industry, are more profitable than others. In 2015, the global fashion industry was a 1.2 trillion dollar industry, with $250 billion spent annually on fashion in the United States.
Fashion designers, for instance, can earn a decent income. In 2015, 17,000 fashion designers were operating in the industry, each earning an average of $73,600.
Manufacturing Industries
The manufacturing industry is a vast and diverse sector, with numerous sub-sectors that cater to different needs and products. The automotive manufacturing sector, for instance, is one of the largest in the world, with companies like Toyota Motor Corporation generating high revenue.
The aerospace manufacturing industry requires innovative technologies and processes to meet the highest standards of quality control. Aerospace equipment needs to handle extreme conditions, making every part custom-made to meet specific specifications.
Some of the most popular manufacturing sectors today include food manufacturing, beverage and tobacco products, chemical manufacturing, and electronic equipment, among others. These sectors can be broken down further into sub-sectors, such as food manufacturing, which encompasses animal food manufacturing, grain and oilseed milling, and dairy product manufacturing.
Here are some of the 20 most popular manufacturing sectors today:
- Food manufacturing
- Beverage and tobacco products
- Chemical manufacturing
- Electronic equipment
- Textile mills
- Textile product mills
- Apparel manufacturing
- Leather and allied product manufacturing
- Wood products
- Paper manufacturing
- Printing and related support activities
- Petroleum and coal products
- Plastics and rubber products
- Nonmetallic mineral products
- Primary metal manufacturing
- Fabricated metal products
- Appliance and component manufacturing
- Transportation equipment
- Furniture and related products
- Miscellaneous manufacturing
These sub-sectors can be further broken down into specific categories, such as food manufacturing, which includes animal food manufacturing, grain and oilseed milling, and dairy product manufacturing, among others.
Automotive
The automotive manufacturing sector is one of the largest in the world in terms of revenue. Toyota Motor Corporation, for instance, is the world’s second highest revenue manufacturing industry.
Automobile makers can invest in innovative technologies and processes due to the sector's high demand and revenue. This enables them to produce exceptional quality vehicles.
Modern manufacturing of automobiles utilizes hybrid manufacturing models for exceptional quality control.
Recommended read: Manufacturing Quality Control
Aerospace
Aerospace manufacturing industries require one of the most innovative manufacturing technologies.
The aerospace industry creates equipment that needs to handle the toughest conditions. This means every part is based on custom specifications to meet the highest standards of the aerospace sector.
These custom specifications are crucial for ensuring the equipment can withstand extreme temperatures, intense pressure, and other harsh conditions.
Check this out: Agricultural Equipment Manufacturers
Defense
Defense manufacturing industries are similar to the aerospace sector, requiring tough metal alloys and innovative materials to withstand field conditions. They utilize the on-demand manufacturing model with high customization.
Defense manufacturing industries face significant challenges, including competition, environmental concerns, cyberattacks, workforce development, and regulatory compliances. These challenges can lead to tremendous losses and business closures.
The defense industry needs to invest in workforce training to hire a skilled workforce and meet regulatory compliances. This includes quality control of the final product and workplace conditions.
Here are some key challenges that defense manufacturing industries face:
- Competition: Defense manufacturers must spend extra to improve product features and market that product.
- Environmental Concerns: Manufacturing involves a certain level of carbon footprint, which is a concern in the defense sector.
- Cyberattacks: Defense businesses rely on IT systems to store data, making them vulnerable to cyberattacks.
- Workforce Development: Defense manufacturers must invest in workforce training to hire a skilled workforce.
- Regulatory Compliances: Defense manufacturing industries must comply with various regulatory requirements, including quality control and workplace conditions.
Electronics
Electronics manufacturers use mass production methods combined with an assembly line setup.
This efficient approach allows them to produce smaller parts, like PCBs and semiconductor setups, in their own production line.
Smaller parts are then assembled in a later phase at the manufacturer's facility.
This process enables electronics manufacturers to produce a high volume of products in a relatively short period of time.
Electronics manufacturers keep inventories of raw materials on hand, just like food manufacturers.
Assembling the finished products with packaging materials is a key part of the process.
The electronics industry relies on a combination of mass production and assembly line setup to get products to market quickly.
Chemical
The chemical processing industry is a fascinating sector that converts raw materials into products like bleach, oil, cosmetics, and floor cleaners. These products are then packed in dedicated containers for later assembly.
Chemical manufacturing is one of the most popular sectors in the manufacturing industry, ranking third on the list of 20 most popular sectors. This industry operates in process manufacturing industries, where raw materials are transformed into finished chemicals.
The chemical processing industry uses the batch production method, which involves producing small batches of products to meet specific customer needs. This method allows for greater flexibility and customization in the production process.
Here are some examples of products that fall under the chemical manufacturing sector:
- Bleach
- Oil
- Cosmetics
- Floor cleaners
These products are essential in our daily lives, from cleaning our homes to personal care.
Pharmaceuticals
The pharmaceuticals industry is one of the biggest manufacturing industries, creating medicine, vaccines, and other medical products.
These products are manufactured well before consumers demand them, similar to how chemical processing plants operate.
The risk of product expiry is a major concern in this sector, as products are made in advance of demand.
Pharmaceuticals are manufactured on a large scale, with the sector working similarly to chemical processing plants.
Worth a look: Items Manufactured in China
Construction Materials
The construction materials manufacturing business is a complex and varied sector. It involves the production and processing of raw materials such as concrete, lumber, and bricks.
Concrete is a fundamental material in this sector, and its manufacturing model can differ greatly depending on the project requirements. The construction materials manufacturing business works closely with its consumers to meet specific order quantities.
Lumber is another crucial material in construction, and its processing involves various stages, from harvesting to treatment. The manufacturing model for lumber depends on the consumer's needs and the project specifications.
The construction materials manufacturing business is a vital part of the manufacturing industries, supporting various sectors such as construction, infrastructure, and housing.
If this caught your attention, see: Project Management for Manufacturing
Plastics
Plastics are often formed into their final shape through a process called molding, which is commonly used in plastics manufacturing businesses.
This process allows for the creation of complex shapes and designs, making it a popular choice for many industries.
In some cases, plastics can change shape with heat, making them well-suited for additive manufacturing technologies like 3D printing.
These advanced technologies have opened up new possibilities for plastics manufacturing, enabling the creation of complex geometries and customized products.
Paper
Paper manufacturing facilities can produce a wide range of products, from newspapers to notebooks and even cardboard.
The types of products they make are diverse, including books, decorations, and many other paper-based items.
These facilities often use batch production or process manufacturing facilities to meet demand.
The technology used in paper manufacturing is usually simple, due to the limited variation in component parts.
This simplicity can make it easier to set up and run a paper manufacturing facility.
National Innovation Institute (NII)
The National Innovation Institute (NII) is a public-private partnership that brings together industry, government, academia, and workforce leaders to increase the country's global manufacturing competitiveness.
Carnegie Mellon University, Lehigh University, University of Pittsburgh, and Pennsylvania State University are all members of this important initiative, known as the National Additive Manufacturing Innovation Institute (NAMI).
By working together, NAMI aims to advance the field of additive manufacturing and make the United States a leader in this field.
The Manufacturing PA Innovation Program also brings together businesses and internationally acclaimed science and engineering talent to advance new products or process innovations.
Undergraduate and graduate student fellows at PA universities work with PA manufacturers to achieve this goal, making it a great opportunity for students to gain hands-on experience and contribute to the growth of the manufacturing industry.
Local Tax Credit Program
The PA EDGE program offers tax credits to businesses expanding in critical manufacturing sectors. This includes companies that purchase dry natural gas for manufacturing petrochemicals or fertilizers, which may qualify for the Local Resource Manufacturing tax credit.
If you're a manufacturer purchasing clean hydrogen and natural gas from a Regional Clean Hydrogen Hub, you may be eligible for tax credits through the PA Department of Revenue.
Businesses
There are various types of manufacturing businesses, ranging from small sole proprietorships to large corporations. The average revenue of a sole proprietorship in 2008 was around $11.9 thousand for unclassified establishments.
The manufacturing industry is diverse, with various sectors contributing to its growth. In 2017, the average manufacturing worker in the United States earned $84,832 annually.
Some of the most popular sectors in the manufacturing industry today include food manufacturing, beverage and tobacco products, and chemical manufacturing. These sectors are among the 20 most popular sectors listed in the article.
Here are the 20 most popular sectors in the manufacturing industry:
- Food manufacturing
- Beverage and tobacco products
- Chemical manufacturing
- Electronic equipment
- Textile mills
- Textile product mills
- Apparel manufacturing
- Leather and allied product manufacturing
- Wood products
- Paper manufacturing
- Printing and related support activities
- Petroleum and coal products
- Plastics and rubber products
- Nonmetallic mineral products
- Primary metal manufacturing
- Fabricated metal products
- Appliance and component manufacturing
- Transportation equipment
- Furniture and related products
- Miscellaneous manufacturing
These sectors can be broken down further, with sub-sectors such as food manufacturing covering areas like animal food manufacturing, grain and oilseed milling, and dairy product manufacturing.
Manufacturing Process
Once the design stage is complete, it's time to move on to the manufacturing process. This involves acquiring the necessary machinery and equipment to make full-scale processes, as well as investing in labor, storage, insurance, and other capacity costs.
Companies may choose to continually improve their processes, reviewing and implementing smaller changes during the actual manufacturing step. This can help them stay competitive and efficient.
There are several types of manufacturing processes that businesses can adopt, including:
Product Research
Product research is a crucial step in the manufacturing process, where you identify the product features, competing products, and market demand. This stage helps you outline the manufacturing number and scaling strategy.
Manufacturers start by listing the product features, which gives you a clear idea of what you're working with. They also look for competing products to understand the market and identify areas for improvement.
Analyzing the market demand is essential to determine the production volume and pricing strategy. A business plan helps you outline the manufacturing number and scaling strategy, which is vital for the success of your product.
At this stage, you'll also shortlist various product materials, considering factors like cost, durability, and sustainability. This decision will impact the final product's quality and price point.
Prototype Testing
Prototype testing is a crucial step in the manufacturing process. It involves making models of the product that are as identical to the final product as possible.
The prototype gives the manufacturer an idea of what the product will look like, allowing for any major issues to be fixed at this stage. This is a critical time to catch and correct any design flaws.
A prototype is created by drafting a smaller-scale test product that mirrors the true manufacturing product. This is done after the design stage is complete.
Once the prototype is complete, it's time to test it. This includes analyzing the actual resources that went into the product to understand its cost and profit margin.
You might enjoy: Manufacturing Lead Time
Calculating Lead Time
Calculating Lead Time is a crucial step in understanding your manufacturing process. It's the calculation of the time from when the sales order comes in up until its creation.
To calculate manufacturing lead time, you need to add together the different production times for your product, including order preparation time, queue time, setup time, run time, move time, inspection time, and put-away time.
The method by which you forecast your lead time will depend on if you're an MTO (Creating manufacturing orders for production and shipment) or MTS (Creating manufacturing orders for production, receiving sales orders, and inventory stock) business.
Here's a breakdown of the different components that make up manufacturing lead time:
Throughput time, on the other hand, only tracks the time it takes to complete manufacturing, from when the manufacturing order comes in to when the product is ready in the stock room. This metric doesn't include any waiting time before manufacturing or delivery times after it.
Challenges Manufacturers Face Today
Manufacturers face a multitude of challenges in today's business environment. Competition is a significant challenge, with manufacturers needing to invest extra to improve product features and market their products effectively.
Competition is fierce in every manufacturing sector. This means manufacturers must be innovative and proactive in their marketing strategies.
Environmental concerns are another major challenge. Manufacturing has a certain level of carbon footprint, and some sectors are more hazardous in this regard than others.
Cyberattacks are also a growing concern. Modern businesses rely heavily on IT systems to store data, which brings with it the risks of cyberattacks.
Data breaches due to cyberattacks can cause tremendous losses and business closures. This is a risk that manufacturers cannot afford to take lightly.
Manufacturers must invest in workforce development to stay competitive. This includes hiring a skilled workforce and investing in workforce training.
Regulatory compliances are also a challenge. Most manufacturing sectors work under regulatory compliances related to quality control, workplace conditions, and data security.
Here are some of the key challenges manufacturers face today:
- Competition
- Environmental concerns
- Cyberattacks
- Workforce development
- Regulatory compliances
Frequently Asked Questions
What do you mean by manufacturing?
Manufacturing involves the production of goods using labour, machinery, and various processing methods. It's the process of creating physical products from raw materials or components.
Sources
- https://www.3erp.com/blog/manufacturing/
- https://dced.pa.gov/pennsylvanias-top-industries/advanced-manufacturing/
- https://www.investopedia.com/terms/m/manufacturing.asp
- https://katanamrp.com/what-is-manufacturing/
- https://www.nist.gov/el/applied-economics-office/manufacturing/manufacturing-economy/total-us-manufacturing
Featured Images: pexels.com