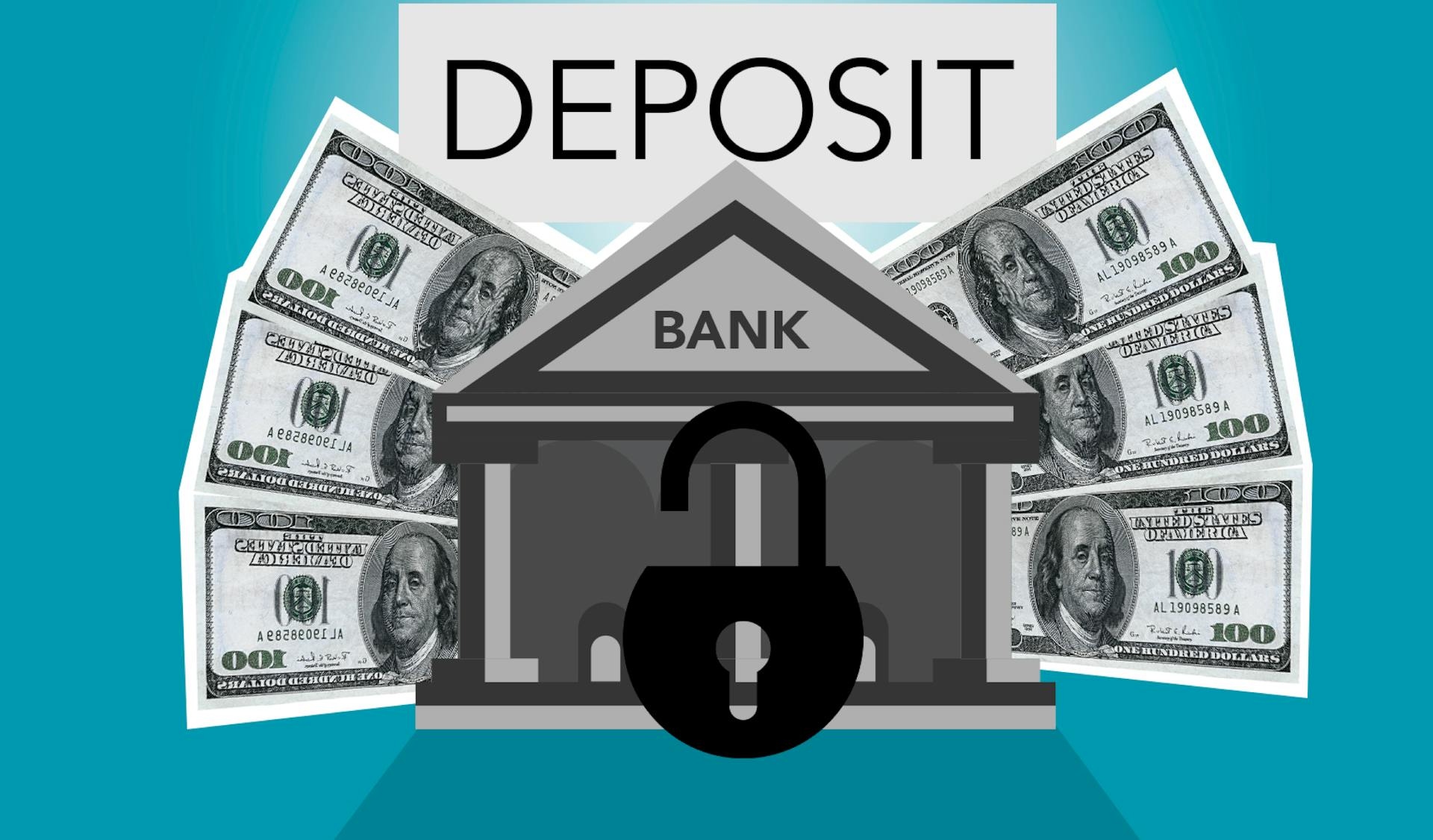
A bill of materials (BOM) is an important document ready for anyone starting production or building products. Imagine you're a first-time baker attempting to make your favorite dessert. You'll quickly find that having a list of ingredients and their quantities is crucial to the success of your dish. Just as a food recipe lets you know what ingredients you need and how much of each, a BOM provides the same information for manufacturers.
In simple terms, a BOM is a comprehensive list of all the raw materials, sub-assemblies, parts, and quantities needed to build or manufacture a product. This document helps with materials management by outlining exactly what is required so that manufacturers can order the necessary components and avoid oversights or mistakes during production. In this article, we will explore bill of materials in more detail and provide pro tips for creating an effective one yourself. Plus, we'll share an exclusive offer for those interested in trying out our 14-day free trial for our innovative BOM software tool.
Suggestion: Quickbooks Bill of Materials
The Significance of Bill of Materials in Manufacturing
The materials BOM is a core element to any efficient manufacturing operation. It outlines the varied applications, production recipe, assembly component list, and materials details for a given product. The bill of materials serves as an essential tool for materials management by providing a comprehensive inventory of all raw materials, sub-assemblies, intermediate assemblies, sub-components, and parts needed to manufacture goods.
Purchasing materials is one of the most critical operational steps in the manufacturing industry. The bill of materials provides detailed information on the exact quantities and types of materials needed. This information helps in negotiating better prices with suppliers and ensures that there are no delays or shortages during production. Accurate material planning based on BOM also enables manufacturers to manage their inventory efficiently.
Without a proper understanding of the bill of materials, it can become challenging to run an efficient manufacturing business operates. By implementing accurate BOMs into the manufacturing process, businesses can ensure they keep up with changing market demands while minimizing waste and maximizing profits. In conclusion, manufacturers must understand how vital bill of materials is in ensuring effective production planning and execution.
On a similar theme: Quickbooks Raw Material Inventory
Get Your Hands on a Valuable Materials BOM Template for Free
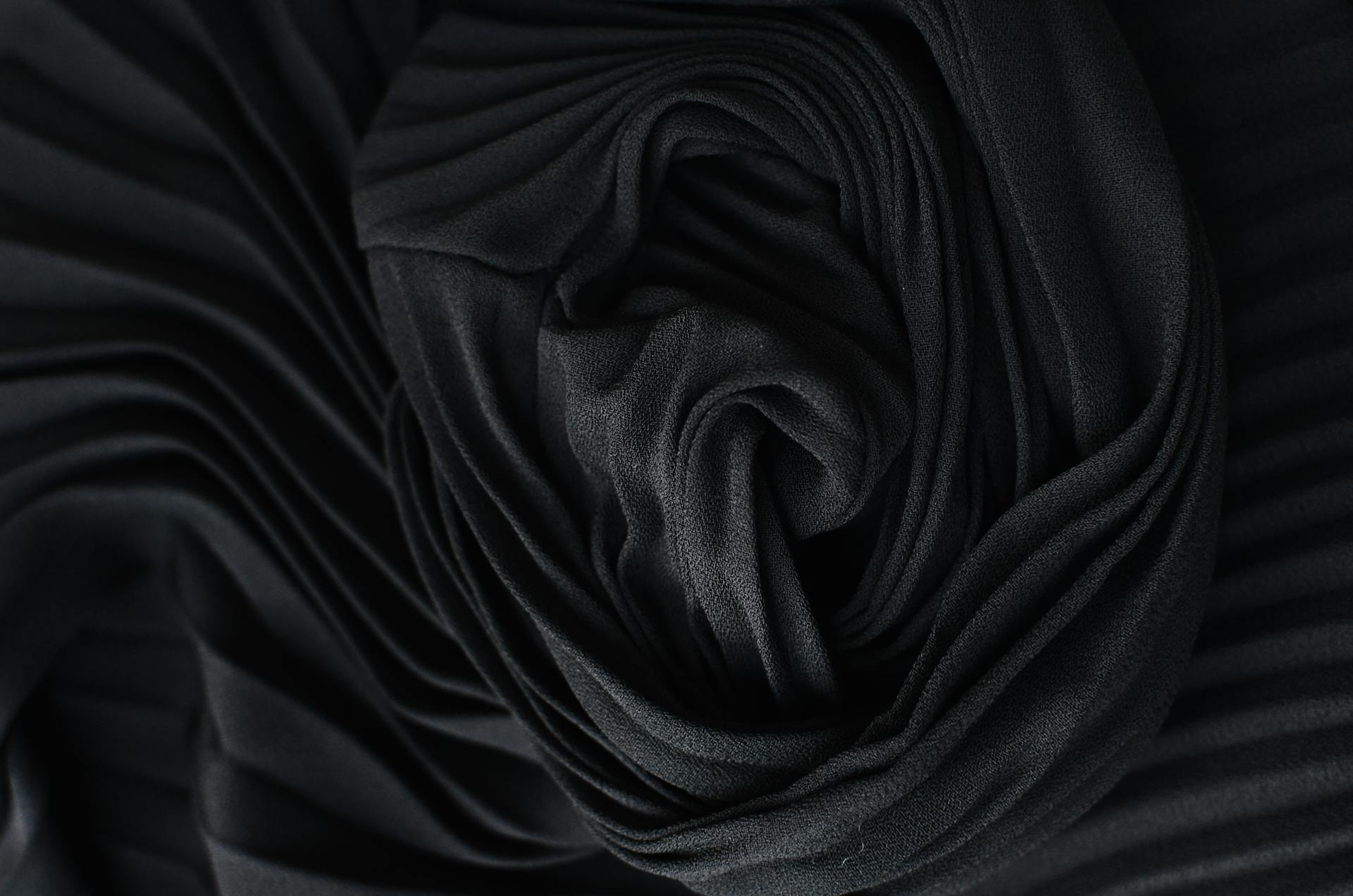
Looking for a way to control inventory and minimize production delays? A free bill of materials template can help! This valuable materials template helps you plan purchases, estimate costs, and keep track of your inventory - all in one place.
With a free BOM template, you can easily create a detailed list of the raw materials needed for each product. Having this information at your fingertips will help you stay on top of inventory levels and make sure that you always have the supplies you need to meet demand. Plus, by using the materials estimate costs plan feature, you can better manage your budget and avoid unexpected expenses. Don't miss out on this opportunity to streamline your production process - get your hands on a free BOM template today!
See what others are reading: Production Management
The Fascinating Story of the Bill of Materials
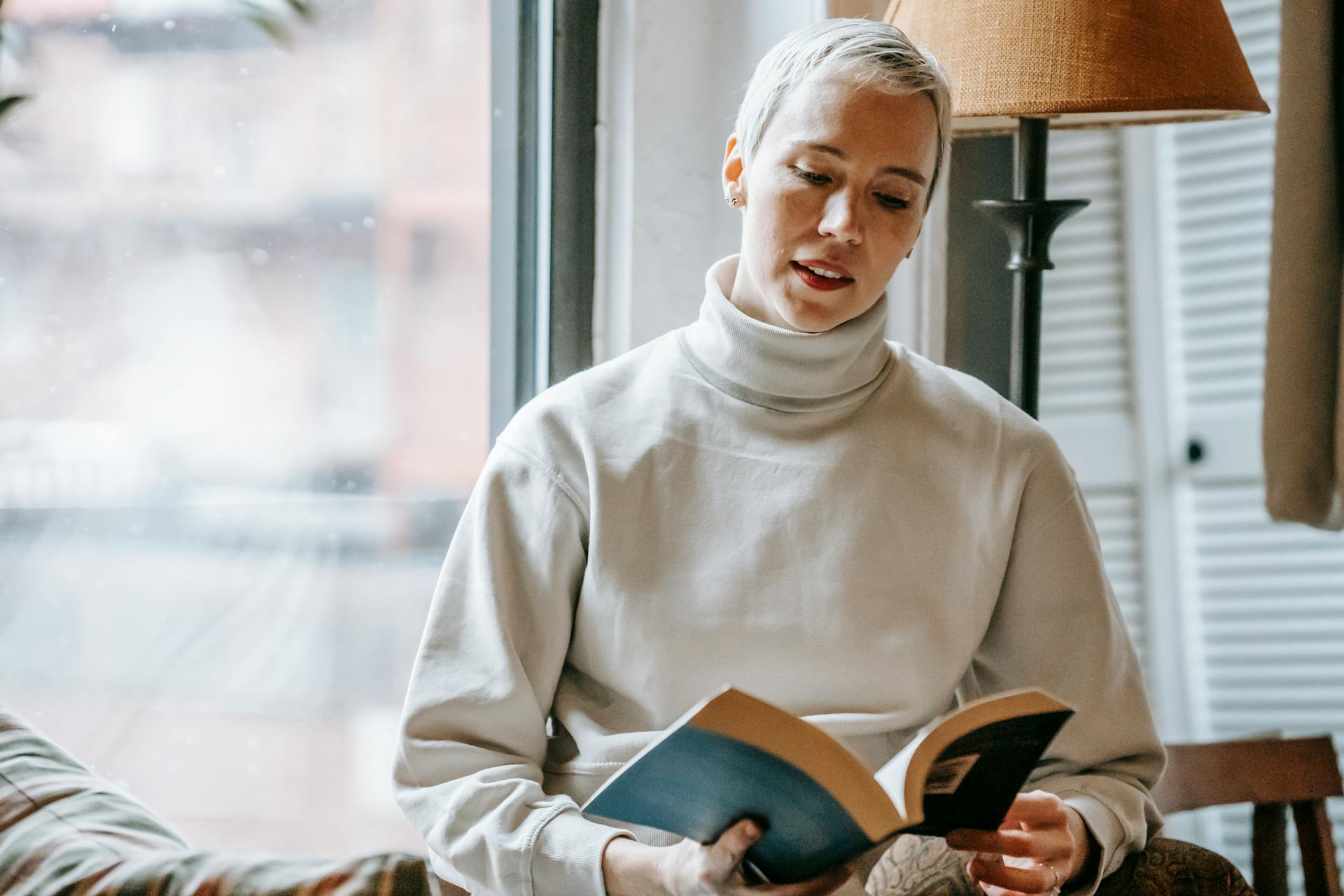
The bill of materials (BOM) is a crucial document that lists all the parts and materials needed to build a product. It has been an important aspect of production planning since the 1960s when advances in inventory management and control software engineers created programs to monitor inventory and reconcile balances. The BOM was further developed with the introduction of materials requirements planning (MRP) which integrated production planning, scheduling and inventory control. In the 1960s enterprise resource planning (ERP) emerged, incorporating MRP into larger business systems. Today, the BOM remains an integral part of manufacturing, particularly with Toyota's just-in-time approach emphasizing lean production techniques.
Take a look at this: Production Planning
What Is a Bill of Materials (BOM)?
A bill of materials (BOM) is a comprehensive list of all the components, parts, and raw materials required to manufacture a product. It provides organizations with essential information to plan purchases, estimate costs, control inventory, and minimize production delays. The BOM includes details such as part numbers, descriptions, quantities, and unit costs.
Key takeaways from a BOM include its ability to help organizations plan purchases more effectively by ensuring they have the necessary components available when needed. By including materials estimate costs plan in the BOM, organizations can better manage their budgets and prevent overspending or shortages. Additionally, maintaining an accurate BOM can help control inventory levels by ensuring that only necessary items are ordered and kept in stock. This reduces the risk of unnecessary waste or obsolescence. Finally, having a complete and up-to-date BOM minimizes production delays by providing clear instructions for assembling products and ensuring that all necessary components are available before production begins.
Unveiling the Importance of BOM Usage: A Must-Read!
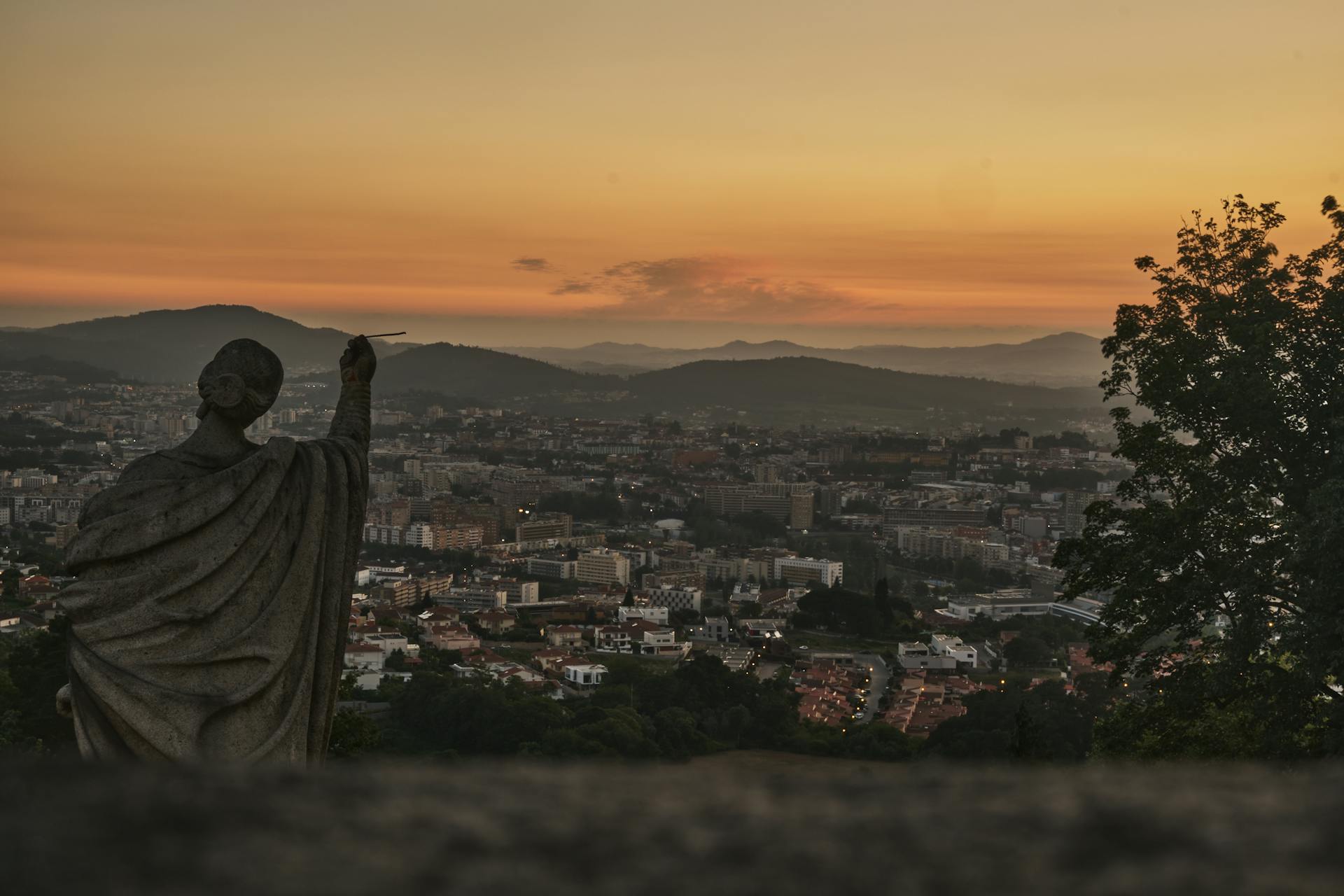
BOM usage is crucial in any manufacturing process as it provides a comprehensive list of materials required for production. Without it, time-consuming mistakes may occur, which include shortages and materials production downtime, resulting in earlier delays and additional expediting charges. Conversely, proceeding with BOM increases efficiency by identifying potential issues beforehand and ensuring that all necessary components are available for the production process.
Additional reading: Discrete vs Process Manufacturing
Discovering the Varied Varieties of Material Lists
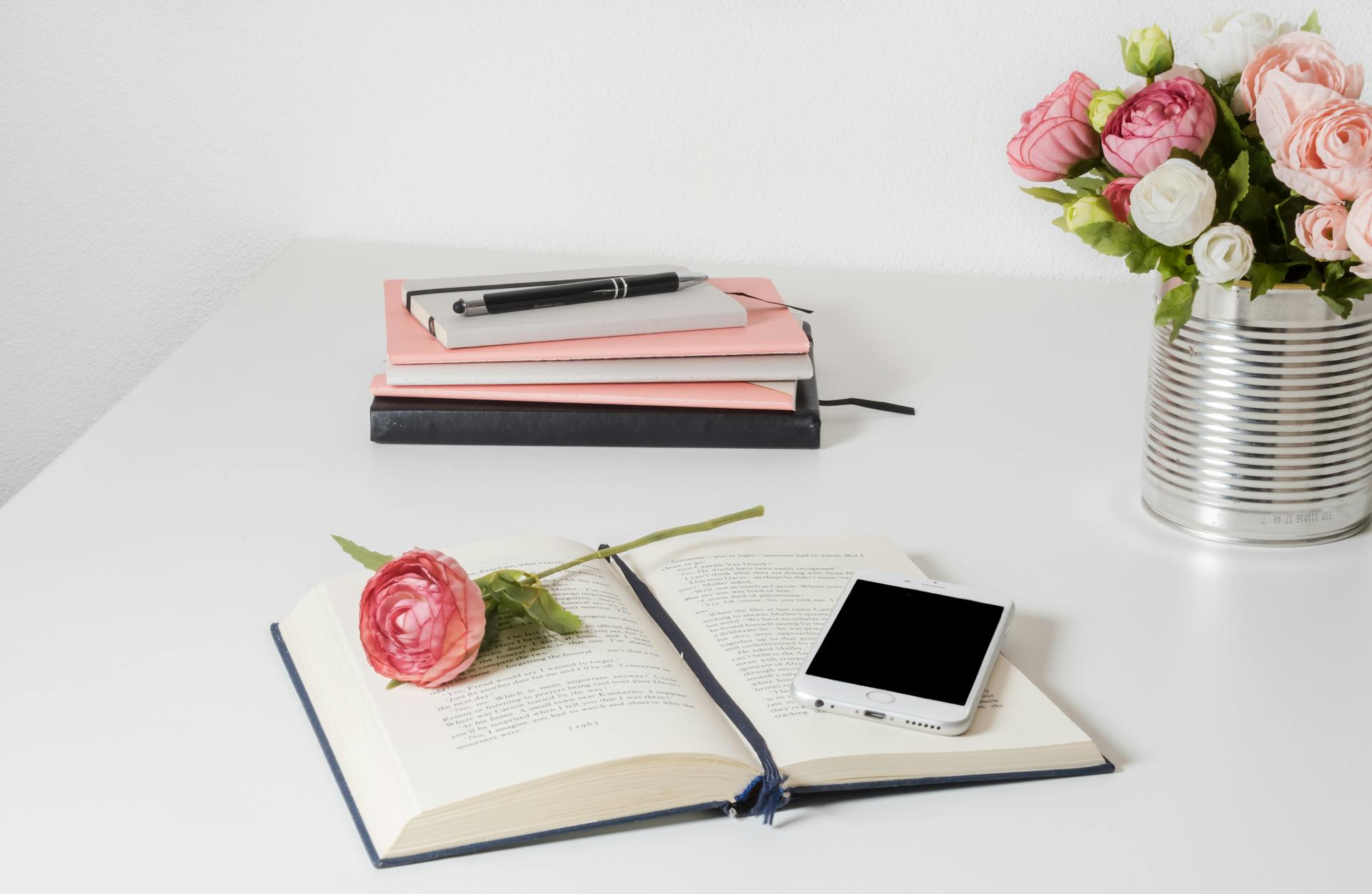
A bill of materials, also known as a BOM, is a crucial document in the product development lifecycle. It outlines all the components and raw materials needed to create a finished product. There are several types of BOMs, including multi-level BOMs and manufacturing BOMs.
The primary types include engineering, sales, and manufacturing BOMs. Engineering BOMs are created during the design phase and list all the components needed to create a product. Sales BOMs are used for pricing and quoting purposes and may not include every single component. Manufacturing BOMs are used in production and provide detailed instructions on how to assemble the final product. Understanding these different types of material lists is essential for effective product development and production management.
Experience the Advantages of BOM Manufacturing Today
BOMs, aka product recipes, offer a number of advantages in manufacturing. By specifying all the necessary components and their quantities, BOMs help ensure that products are consistently produced to meet quality standards. They also enable better control over inventory levels and facilitate accurate cost accounting. With the use of BOMs, manufacturers can streamline their production process and ultimately improve their bottom line.
1. Less waste
A bill of materials (BOM) is a crucial tool for manufacturers who want to decrease waste. Keeping unusable products, excess inventory or incorrectly assembled products can make any manufacturer cringe. By organizing parts efficiently with a BOM, excess inventory and incorrect assembly issues aren't left to chance.
Product recipes provided by the BOM can help manufacturers constantly self-improve and ensure that their bom inventory helps them keep optimal levels of parts on hand for production. An organized BOM system will save money in the long run by decreasing waste and allowing for efficient production processes.
Master the Art of Crafting BOMs with These 7 Simple Steps
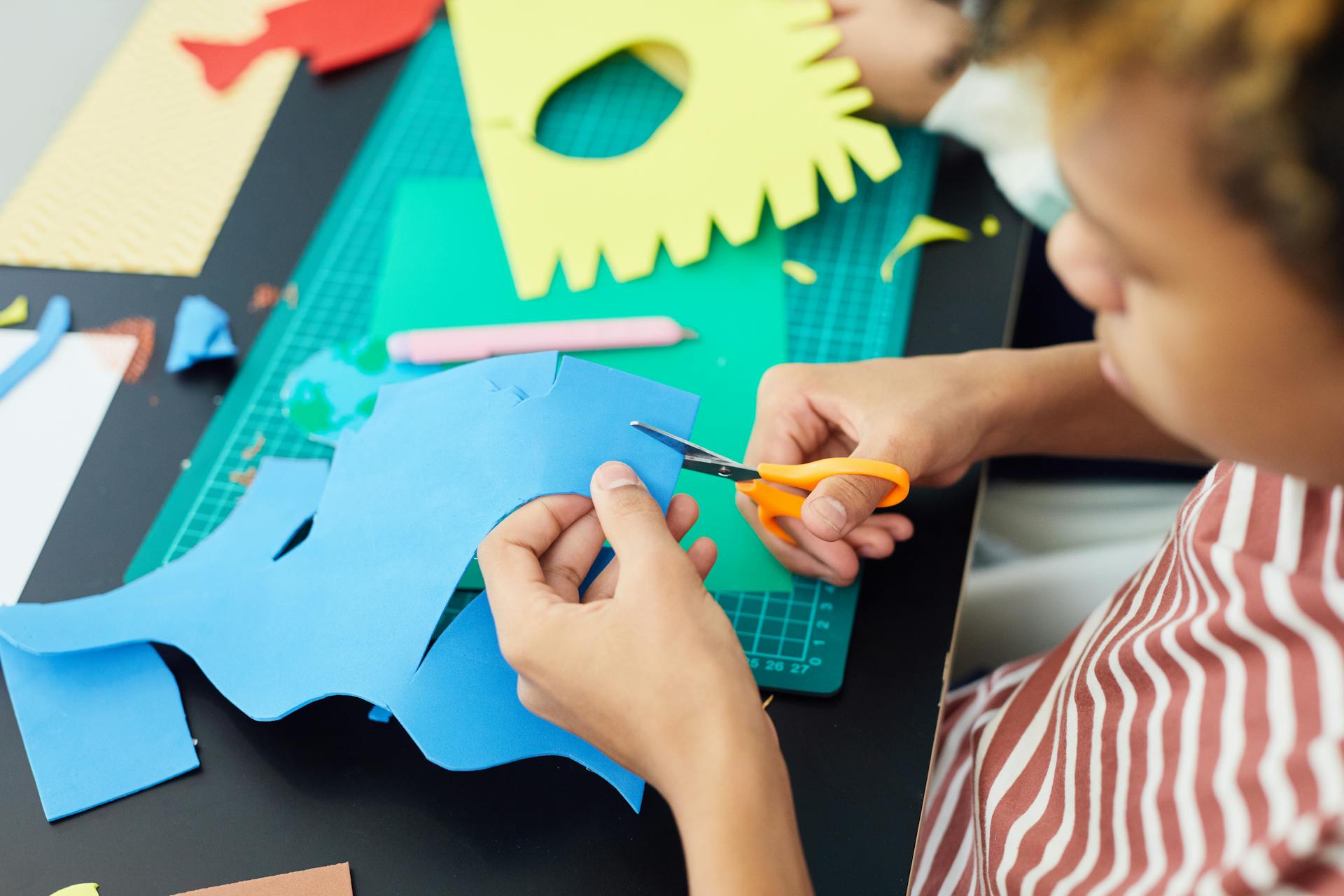
Mastering the art of crafting BOMs (bill of materials) is crucial for industry designers, purchasing scheduling, and planning workers. An accurate BOM serves as the foundation for producing finished goods, enabling actual production process to run smoothly. Follow these 7 simple steps to create a well-structured and comprehensive BOM that will save time and reduce errors in your manufacturing process.
A fresh viewpoint: Purchase Order Process
1. Centralize control of the BOM.
Centralizing control of the BOM (bill of materials) is crucial for any manufacturing company. By having a single record of all parts and components required to build a product, companies can ensure that their information systems remain accurate and up-to-date. This allows for easier tracking of inventory levels, cost management, and efficient production planning.
To assemble information for the bill of materials, it's important to involve all departments within the company that play a role in the production process. This includes engineering, procurement, and manufacturing teams, among others. By centralizing this data into one system or database, each team can easily access and update the same information in real-time. This not only saves time but also reduces errors caused by manual data entry or outdated spreadsheets.
In conclusion, centralizing control of the BOM is critical for any manufacturer looking to streamline their operations and remain competitive in today's market. By creating a centralized system that allows for easy access to accurate information from all departments involved in production, companies can reduce costs, improve efficiency, and ultimately deliver higher quality products to their customers.
2. Determine who will be able to change the BOM.
The bill of materials (BOM) is a crucial document that outlines all the parts and components required to manufacture a product. It's essential to have control over who can make changes to the BOM, as any alterations can have significant implications for the production process.
The decision about who is authorized to change the BOM should be made by the company's management team. Typically, only a select group of individuals or departments will have access to make changes to the BOM, such as engineers or project managers. It's important to ensure that these individuals are qualified and experienced enough to make informed decisions about which parts should be added, removed, or substituted in the BOM. By keeping control over who can change the BOM, companies can better manage their inventory levels, avoid costly production delays and errors, and ultimately ensure that their products meet quality standards.
3. Decide how to track revisions to the BOM.
To make sure that the bill of materials (BOM) remains accurate, it's essential to track revisions. The best way to do this is by using a system that can keep track of changes on a continuous basis. By doing so, you can ensure that each revision is recorded and tracked to ensure that your BOM is always up-to-date.
It's important to note that these revisions should be connected back to the original document. This helps you keep track of the changes made and ensures that all updates are properly documented. By using a reliable tracking system, it's easy to see what changes were made and when they were made, which makes it easier for everyone involved in the project to stay on top of any adjustments or modifications.
Readers also liked: Multi Level Bom
4. Choose the BOM presentation.
Choose the BOM Presentation
When it comes to presenting a bill of materials (BOM), there are a few options to consider. The first is the indented BOM, which shows the hierarchy of components and sub-assemblies. This type of presentation makes it easy to see how each part fits into the overall product design.
Another option is the flat BOM, which lists all components in a single level without any hierarchy. While this type of presentation may be simpler, it does not provide as much context as an indented BOM.
Ultimately, the choice between these two types of presentations depends on your specific needs and preferences. Consider what information you need to convey and what will make sense for your audience. By choosing the right BOM presentation, you can ensure that your product design is clear and easy to understand.
5. Continue to add to and refine the list.
"Bill of materials" is a crucial document that contains all the necessary components required to build a product. However, creating a bill of materials is not a one-time process. It requires constant updates and refinements as new components are added or removed.
As you continue to add to and refine the list, make sure to keep it organized and easy to understand. Use clear descriptions and include any relevant information such as part numbers, quantities, and suppliers. Regularly review the bill of materials with your team to ensure accuracy and identify any potential issues.
Updating your bill of materials regularly will save you time, money, and headaches in the long run. It allows for better communication between teams, reduces the risk of errors or missing parts, and ensures that your production process runs smoothly. So don't hesitate to continue adding to and refining your bill of materials - it's an investment in the success of your product!
Frequently Asked Questions
Why Bill of materials is important?
A Bill of Materials is important because it provides a comprehensive list of all the components needed to manufacture a product. It helps ensure that everything necessary is available and minimizes errors in production.
What is the purpose of the bill of materials?
The bill of materials (BOM) is a document that lists all the components and raw materials needed to manufacture a product. It serves as a reference for production planning, cost estimation, and inventory management.
How to use (BOM) bill of materials in tally?
To use Bill of Materials in Tally, go to Inventory Info and select BOM. Enter the details of the finished product, then select the stock items you want to include in your BOM and their quantity. Save the BOM and use it to track your inventory levels accurately.
What materials to include in your bill of materials?
Your bill of materials should include all the necessary components to manufacture your product, including raw materials, subassemblies, and finished products.
Featured Images: pexels.com