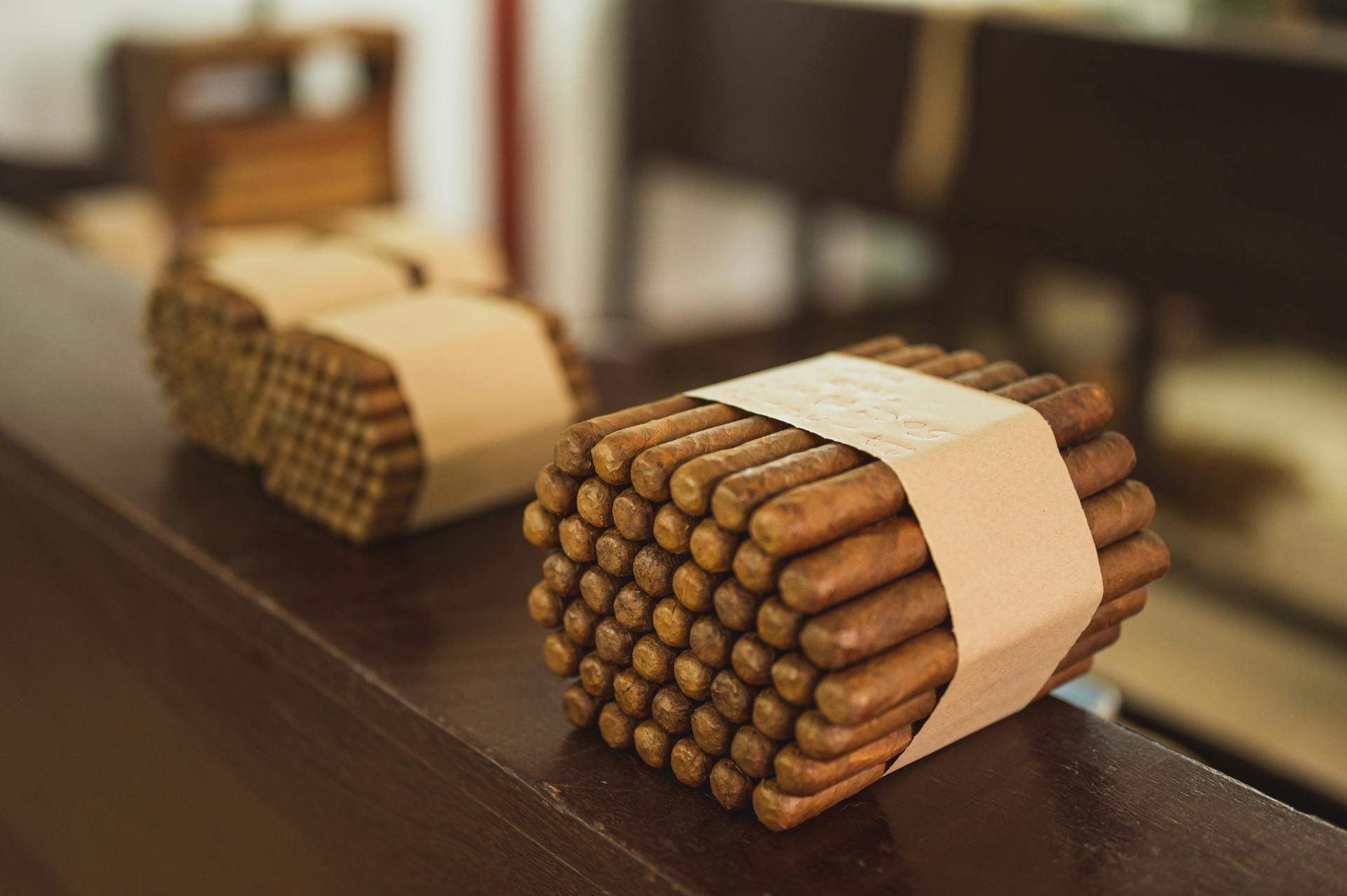
Are you a growing manufacturer struggling with managing your quickbooks raw material inventory? You're not alone. Inventory management can be a tough nut to crack, especially for scaling manufacturers who are dealing with multiple shopify stores and drop shippers. The problem lies in the fact that QuickBooks Online doesn't have a dedicated manufacturing module, leaving many manufacturers manually updating their inventory levels.
But fear not! There is a solution - QuickBooks Online has an awesome tool to help you optimize production and manage your quickbooks raw material inventory effectively. In this article, we've got you covered. Learn how to effortlessly add Shopify tools to your QuickBooks Online account and integrate them with specialized manufacturing software to maximize your productivity. Follow our pro tip to streamline your manufacturer selling process and take your business to the next level.
You might enjoy: Quickbooks Online Lot Tracking
Effortlessly Add Your Inventory on QuickBooks Online
Are you having trouble managing your raw material inventory on QuickBooks Online? Entering inventory may seem like a daunting task, but it's actually a straight forward process. If you're missing features needed for your manufacturing business, don't worry! QuickBooks Online has all the tools necessary to manage your inventory effectively.
To enter inventory on QuickBooks Online, simply select "New" in the services dashboard, and then click on "Inventory Item". From there, fill out the relevant fields with information about the item you're entering. Once you've finished, click save and voila! Your item is now part of your QuickBooks inventory system.
An important part of raw material inventory management is keeping track of all items accurately. If you're entering multiple items at once or have existing data outside of QuickBooks, use the import option to make things easier. With QuickBooks Online, entering and managing your inventory has never been simpler.
Take a look at this: Quickbooks Bill of Materials
QuickBooks manufacturing and wholesale accounting software
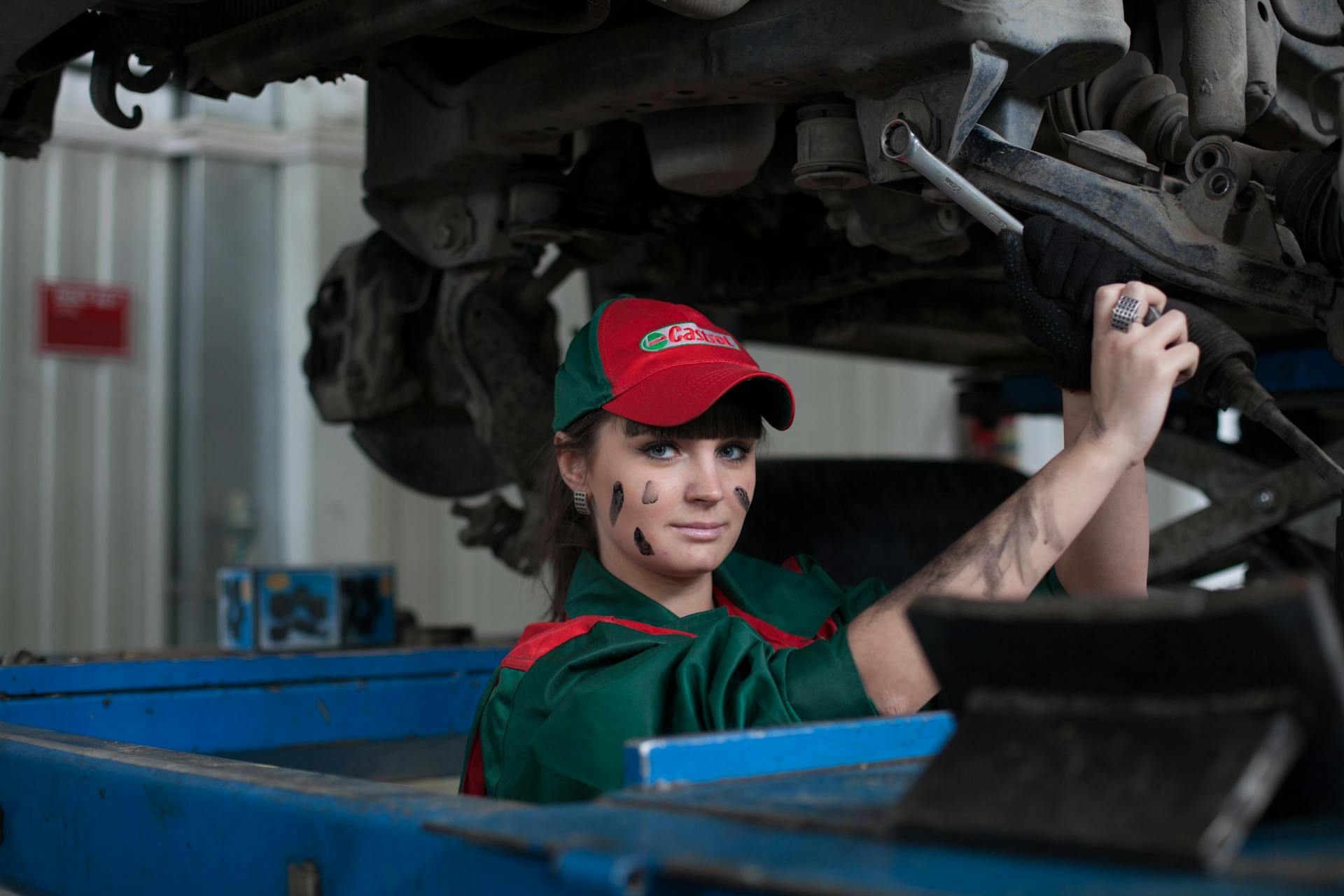
QuickBooks Online advertises a manufacturing and wholesale edition that can help automate manual processes for businesses in these industries. With features such as sales fulfillment and accurate inventory counts, QuickBooks Online tracks inventory items to deliver detailed analytics and financial reports for study. By keeping track of key inventory reports, businesses can make informed decisions and deliver accurate forecasts for their financial aspects.
Handling inventory processes manually takes significant time, but with QuickBooks Online, defining material inventory and labor amounts accurately is made easy. Specific pricing structures can also be set up for customer classifications in QuickBooks to segregate payment details based on customer type. This allows businesses to focus on individual sales without worrying about payment confusion or errors.
Overall, QuickBooks Online's manufacturing and wholesale edition offers many benefits for businesses looking to streamline their operations. From easy assembly processes to detailed tracking of sales processes, this software can help save time and improve accuracy while helping businesses make informed decisions about their future growth strategies.
Worth a look: Wholesale Inventory Management
Enhance Your Shopify POS Inventory Control with Simple Tips
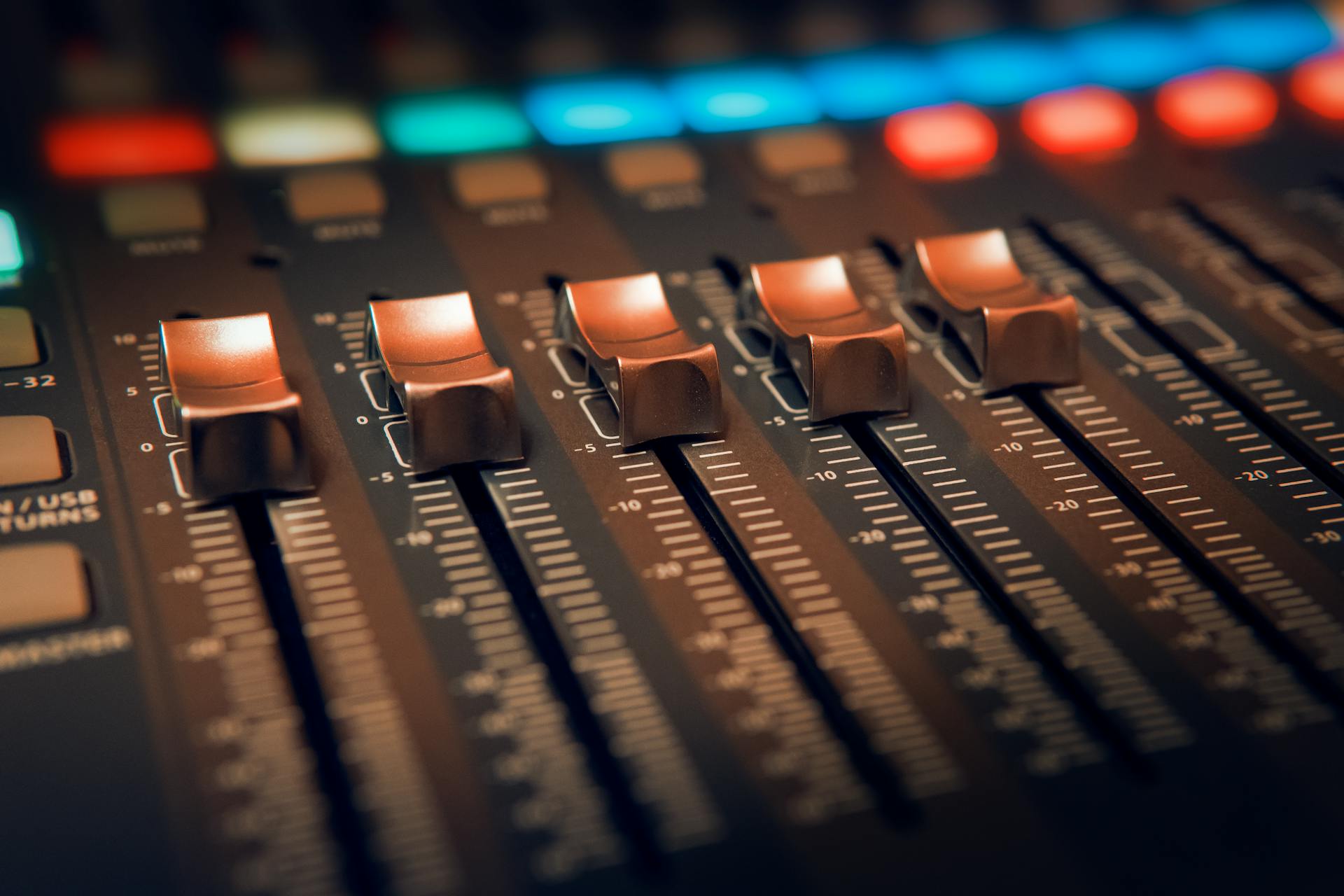
Are you selling Shopify products and looking for ways to boost sales? One of the best ways to do so is by optimizing your inventory management. This is where Shopify POS inventory management comes into play. With the right tools and techniques, you can streamline your inventory control process and make sure that you always have enough stock to meet demand.
The first step in enhancing your Shopify POS inventory control is to take advantage of the built-in features offered by the platform. This includes setting up inventory alerts, managing product variants, and tracking sales data. By doing so, you can identify which products are performing well and which ones need more attention. This will help you make informed decisions when it comes to restocking and pricing strategies.
Another way to improve your inventory management is by exploring new brands to sell on your platform. By diversifying your product offerings, you can attract a wider range of customers and increase sales. Just be sure to do your research beforehand and choose brands that align with your target audience's interests and values. With these simple tips, you can enhance your Shopify POS inventory control and take your business to new heights!
Related reading: Barcode Inventory Control
QuickBooks Manufacturing: Understanding Negative Inventory
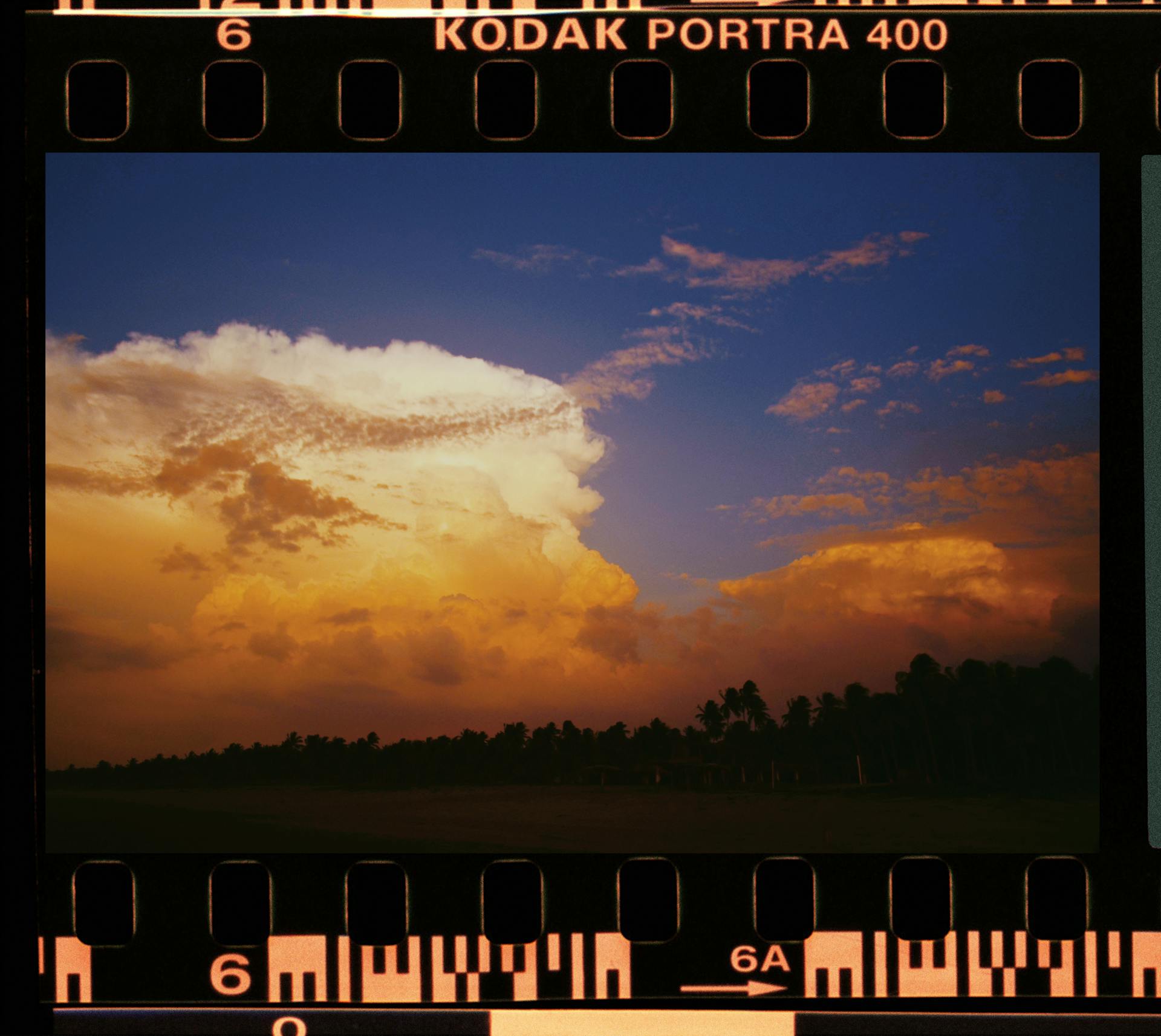
Understanding negative inventory is crucial for any business that deals with inventory management, especially in QuickBooks Manufacturing. Negative inventory occurs when there is an imbalance between the current inventory holdings and the amount of product sold. QuickBooks Manufacturing occurs at a product level, where each product can have its own unique inventory stock status.
Negative inventory can occur due to various reasons such as incomplete sales order fulfillment or incorrect data entry. However, this does not mean that your business has lost money. QuickBooks Manufacturing provides an easy fix for negative inventory by allowing you to adjust your average cost and reconcile your accounts accordingly.
The key takeaway when it comes to QuickBooks Raw Material Inventory is to understand how negative inventory can impact your business and how to fix it quickly. By keeping track of your current inventory holdings and reconciling them regularly, you can avoid negative inventory altogether. With the help of this wholesale tutorial, you will be able to manage your raw material inventory efficiently and effectively using QuickBooks manufacturing tools.
Why inventory excel sheets are inefficient for manufacturers
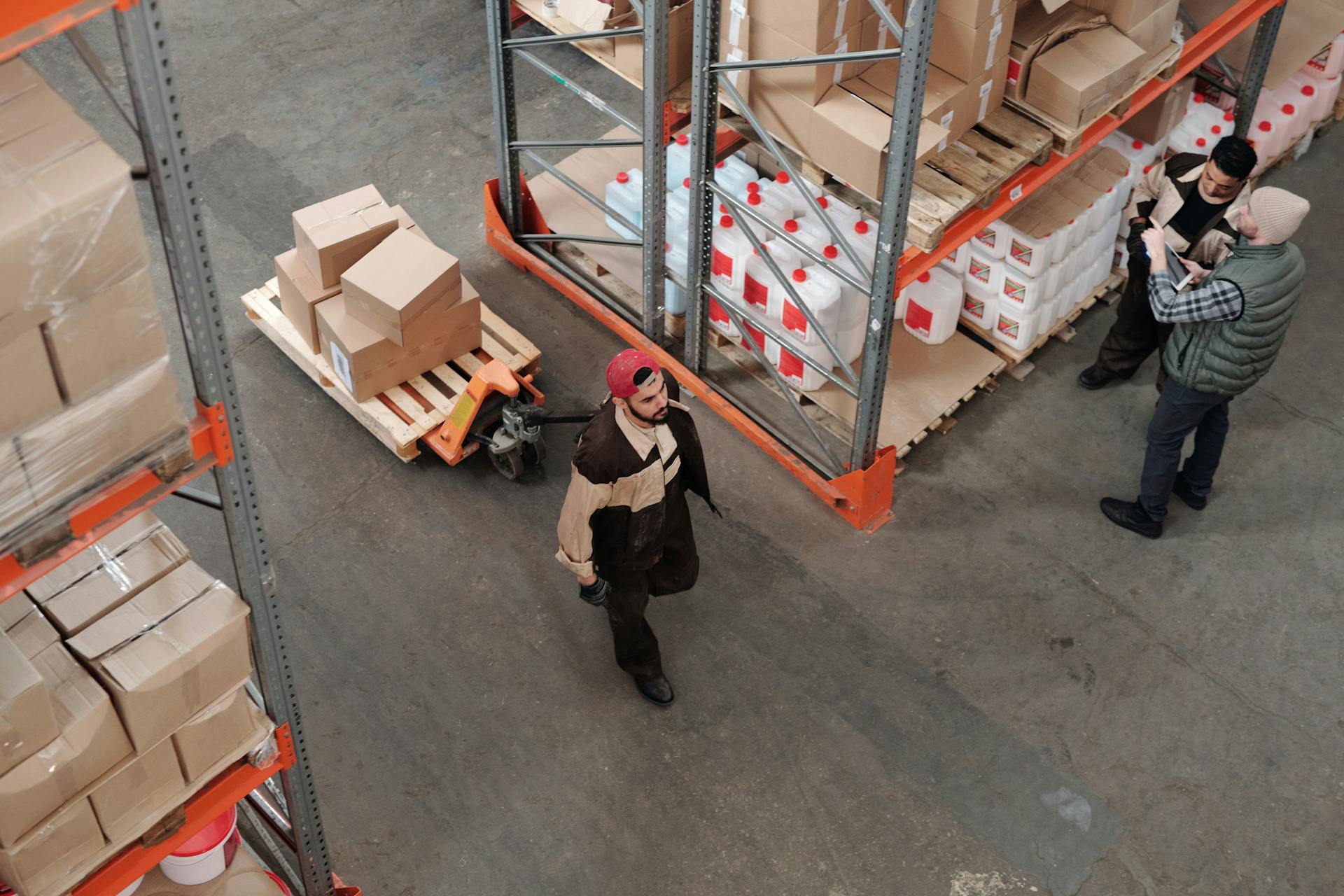
Using an inventory excel sheet may seem like a good idea when monitoring stock levels, but it is not the most efficient method for managing your raw material inventory. These sheets require manual updating, which can lead to errors and discrepancies, making it difficult to keep track of your stock levels accurately. Additionally, inventory excel sheets do not provide real-time data, which can be critical in keeping up with demand.
By using cloud-based alternatives for monitoring material levels, you can ensure that your inventory management is always up-to-date. These cloud-based platforms offer accurate and real-time data that can be accessed from anywhere at any time. This makes it easier for manufacturers to make informed decisions on restocking levels and adjust production schedules accordingly.
In conclusion, businesses should consider using more advanced methods such as cloud-based alternatives instead of relying solely on inventory excel sheets. By doing so, businesses can streamline their inventory management process and reduce the risk of errors or miscalculations. As part of our business tips series, we highly recommend utilizing these tools to manage your raw material inventory effectively.
Here's an interesting read: Inventory Excel Sheet Inefficient
Is QuickBooks good for manufacturing?
QuickBooks is a popular accounting software among small business owners, but when it comes to manufacturing firms, there are some limitations QuickBooks poses. While QuickBooks can handle inventory management, it lacks the necessary features for tracking raw materials and their costs accurately. Additionally, QuickBooks doesn't integrate with manufacturing and production software which can make the process of tracking materials even more challenging. Therefore, it's essential for manufacturing firms to consider these limitations before using QuickBooks for raw material inventory management.
Readers also liked: Bill of Materials
1. Eliminate bottlenecks
Eliminating bottlenecks in your inventory management is crucial to maintaining a streamlined production process. Slow points in the plan production typically slows down the manufacturing process as a whole, and can lead to delays in delivery schedules. Fortunately, QuickBooks Manufacturing features provide solutions to help eliminate these bottlenecks.
The master production schedule reaches its full potential when routing manufacturing pinpoint is used. This feature allows you to track inventory runs and ensure that every assembly item strictly follows the planned schedule. Moreover, QuickBooks Manufacturing Lead Time features assist with planning for raw material purchases and forecasting more accurately, which helps prevent bottlenecks from developing in the first place. With these tools at your disposal, you can effectively manage your raw material inventory and create a seamless production process that delivers high-quality products on time.
2. Develop your master production schedule
Developing a master production schedule (MPS) plots out the entire production process from start to finish. Using QuickBooks scheduling production tools, businesses can create an MPS that helps them fulfill orders quickly and prevent delays. The MPS lets companies adjust their production plans in real-time, ensuring they have enough raw materials on hand to meet demand. By developing an MPS, businesses can improve inventory cost control and reduce waste.
3. Save your BOMs in one place
Are you tired of keeping track of scattered bills of materials (BOMs) for your raw materials inventory? It can be virtually impossible to keep up with the materials BOM makes and the production progress without having all the information in one place. That's where QuickBooks Manufacturing comes in handy. With QuickBooks Manufacturing, you can define BOMs for each product and automatically list all the necessary raw materials needed for production. Say goodbye to missed orders and errors!
4. Centralize your entire business
Centralizing your entire business is no easy feat, especially when it comes to managing your raw material inventory. Without a centralized system in place, daily operations can become chaotic and data isn't centralized which makes it difficult to make informed decisions. However, the good news is that QuickBooks offers a solution with its inventory management tools.
Gone are the days of developing spreadsheets and manually tracking inventory levels. With QuickBooks' visual dashboard, you can quickly and easily see your current inventory levels, track purchase orders and sales orders as well as manage reordering. By centralizing your inventory management, you'll be able to streamline your operations, reduce errors and improve efficiency. In short - it's a game-changer for any business looking to grow!
Frequently Asked Questions
How to verify and rebuild data in QuickBooks?
To verify and rebuild data in QuickBooks, go to the File menu and select Utilities. Then, choose Verify Data to check for data damage or Rebuild Data to fix any errors found during verification.
What are the three types of inventory?
The three types of inventory are raw materials, work in progress, and finished goods. Raw materials are unfinished products that have not yet been processed or assembled into a final product, while work in progress is partially completed products that are still being worked on. Finished goods are fully completed products that are ready to be sold or used.
What are the issues with raw material inventory in QuickBooks?
Raw material inventory in QuickBooks can present challenges such as inaccurate tracking, difficulty in identifying stock levels, and inability to reconcile physical inventory with system records.
What is an example of raw materials inventory?
Raw materials inventory refers to the stock of unprocessed materials that a company keeps on hand for production. Examples include lumber for furniture makers, cotton for textile mills, and steel for construction companies.
How does QuickBooks calculate the costs of manufacturing?
QuickBooks calculates the costs of manufacturing based on the cost of materials, labor, and overhead expenses associated with producing each item. It uses this information to determine the total cost of goods sold and track profitability.
Featured Images: pexels.com