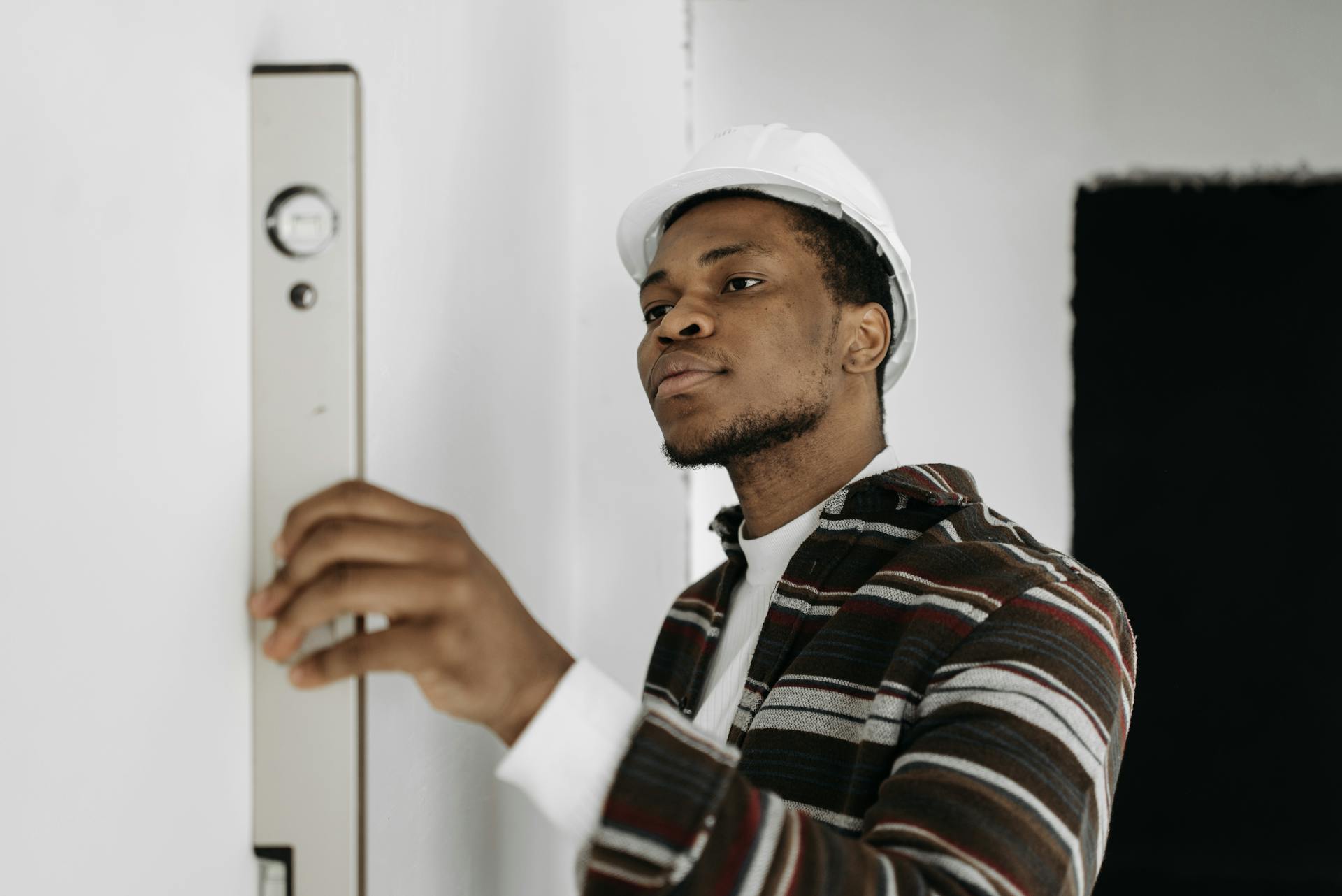
If you run a product-making business, you've probably heard of multi-level BOMs. Also known as indented bills of materials or hierarchical BOM structures, they are vital ingredients in creating finished goods. Simply put, a multi-level BOM is a list of all the sub-assembly components and materials required to make a product. These BOM structures have multiple levels, with each level representing an assembly or sub-assembly that makes up the final product.
At the top level, a multi-level BOM will include the finished product and all its SKUs, part descriptions, quantities, costs, and any additional specifications needed for manufacturing. Below that are the various sub-assemblies and their own bill of materials required to create them. This modular BOM structure allows for configurable BOMs that can adapt to different products or variations within a product line.
If all this sounds overwhelming don't worry! By the end of this article, you'll have a pretty good grasp on multi-level BOMs. We'll cover what they are, how they work in smart manufacturing software, and why automated scheduling and BOM software lets businesses streamline their operations. Stick around until the end for information on Katana's 14-day free trial so you can see firsthand how multi-level BOMs can help your business thrive. If you're already familiar with these concepts we'd recommend skipping ahead to our smart manufacturing software chapter where we'll dive into more advanced topics.
You might like: Multi Location Inventory Management
Structure of a Multi Level BOM
Multi level BOM resembles a family tree, with a parent item at the top and purchased parts and raw materials branching out from it. Each branch represents a different BOM level and can be broken down even further into sub-assemblies or components. This hierarchical structure allows for easy organization and understanding of complex manufacturing processes.
The BOM tree is an essential tool for managing multi-level BOMs. It provides a visual representation of the entire product structure and helps manufacturers keep track of all the components needed to build the final product. By breaking down each level into smaller parts, it becomes a lot easier to manage the huge amount of SKUs that are involved in manufacturing.
Pro tip: When defining multi-level BOMs, it's important to use consistent naming conventions for parts and assemblies. This makes it easier to search for specific items when generating SKUs. Luckily, there are software solutions available that can automate this process with SKU generators, allowing manufacturers to focus on other critical aspects of their business.
On a similar theme: Shopify Multi Stores
Discover When Multi-Level BOMs May Not be the Best Choice
Multi-level BOMs can be an effective tool for materials planning, providing a detailed structure of component quantities and assembly operations. However, when it comes to the big picture of the production process, multi-level BOMs can lose sight of the forest for the trees. In situations where short throughput times and just-in-time models are crucial, using a flattened BOM or a single-level BOM may make more sense from a production scheduling point of view.
While multi-level BOMs are useful for dividing up production into individual operations, they can needlessly complicate matters when it comes to purchasing activities. Time spent ordering components one by one can add up quickly and increase the likelihood of ordering errors. Instead, using a single-level BOM allows purchasing to synchronize deliveries and reduce time spent on ordering. This approach also helps assembly workers keep track of finish times for each individual operation.
Another potential downside of multi-level BOMs is that they overcomplicate simple things and miss important nuances. For example, in situations where multiple blocks need scheduling simultaneously or where product structures become too complex, it may be better to use flattened BOMs or single operation routings instead. Ultimately, whether you choose to use multi-level BOMs or not depends on your specific production environment and requirements.
If this caught your attention, see: Multi Channel Selling
The Two BOM Structures
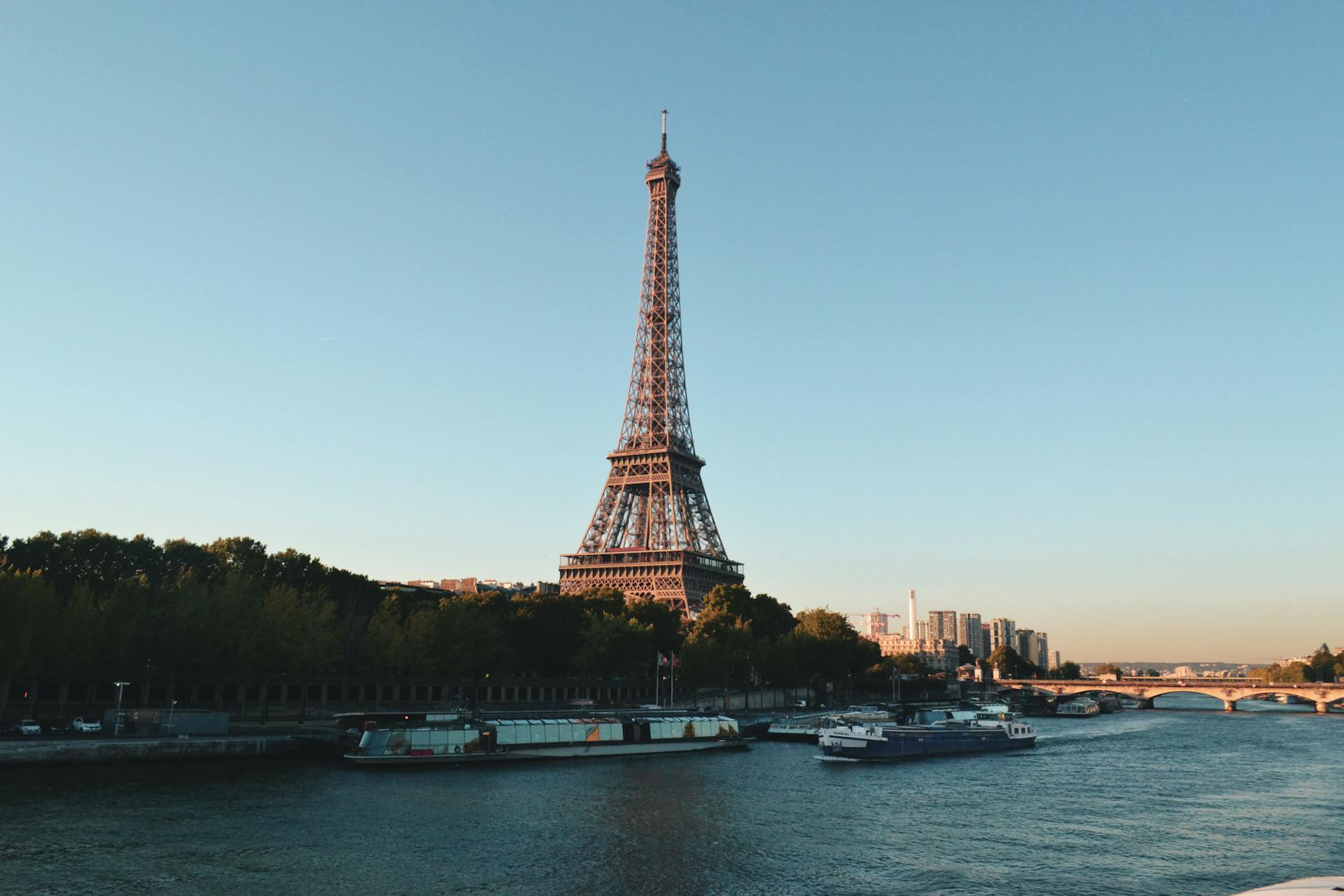
In the world of manufacturing, there are two types of Bill of Materials (BOM) structures: Single-Level BOM and Multi-Level BOM. A Single-Level BOM is a simple list of all the parts and components needed to create a finished product. On the other hand, a Multi-Level BOM breaks down the creation process into multiple levels or subassemblies. This type of BOM is particularly useful for complex products that require multiple stages of assembly. As such, understanding the difference between these two structures and how they work can have a significant impact on your manufacturing process's efficiency and overall success.
A fresh viewpoint: Discrete vs Process Manufacturing
Revolutionize Your BOM Management: Is Excel Your Top Pick?
When it comes to managing multi level boms, the obvious choice for many businesses is an excel spreadsheet. However, relying on inefficient excel spreadsheets can be a waste of time as these spreadsheets need to be constantly updated manually with potential product variants and resolved boms that grow exponentially over time. Calculating costs and quantities calculating totals for multi level boms requires extensive setup and complex formulas, taking valuable time away from other important tasks.
One major problem with using excel spreadsheets for managing multi level boms is the increased complexity of creating a multi level indented bom. Existing multi level boms easily make human errors, like accidentally deleting key columns or parts managing multiple instances. These small mistakes can lead to huge errors in the production process, ultimately affecting key business decisions made based on incorrect data. Additionally, sorting functions in excel can cause major problems when sorting columns in large spreadsheets where one mistake could have disastrous consequences.
Another disadvantage of using excel spreadsheets for managing multi level boms is that the spreadsheet documentation isn't reliable or up-to-date. This makes it difficult for manufacturing businesses to keep up with changes in their bom hierarchy and part numbers, leading to confusion and missed opportunities for improvement. A better alternative would be investing in a software tool specifically designed for managing multi level boms that eliminates the need for manual updates while providing accurate data at all times.
Consider reading: Service Level Management
Create Accurate Material Lists with Our Free BOM Template
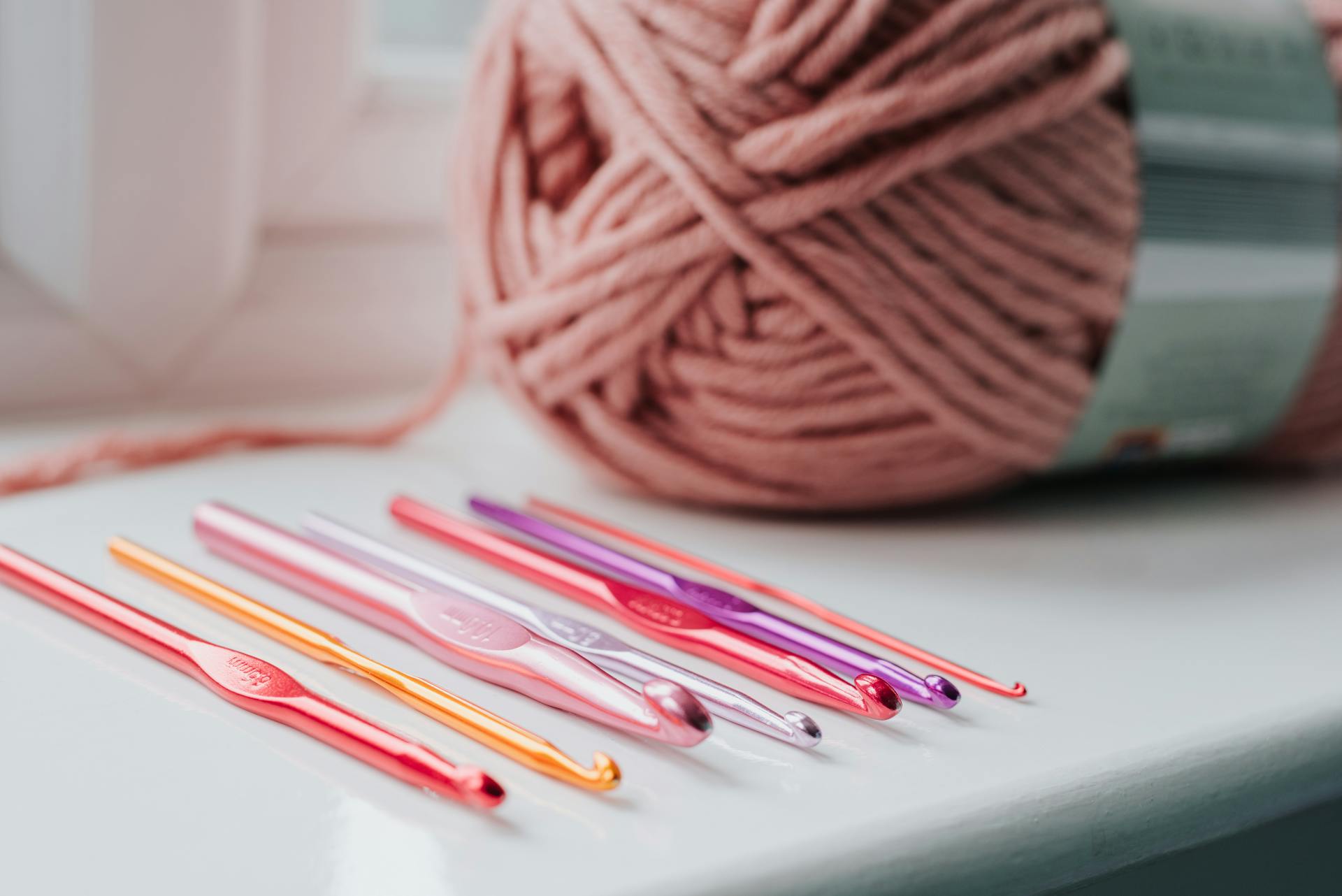
Are you struggling to create accurate material lists for your projects? Look no further than our free BOM template! This multi-level bill of materials template allows you to plan purchases and estimate costs, helping you control inventory and minimize production delays.
With our free BOM template, you can easily organize your project's materials into a detailed list. This includes everything from raw materials to finished products, broken down by level and quantity. By using this template, you can ensure that all necessary items are accounted for in advance, allowing you to plan purchases and estimate costs with precision. Plus, by keeping track of your inventory levels through the template, you can minimize the risk of production delays caused by shortages or overstocking. Don't wait any longer - try our free BOM template today and take control of your material planning process!
You might like: Production Planning
The Advantages of Using a BOM
Using a multi-level BOM increases efficiency and reduces the risk of time-consuming mistakes. By listing all the necessary materials and their quantities, production managers can avoid delays caused by shortages or materials production downtime. Conversely, proceeding without a BOM can result in additional expediting charges and earlier delays, making it an essential tool for any manufacturing process.
Curious to learn more? Check out: Production Management
1. BOM notes
The notes section of a multi level BOM is an essential part of the document. This section offers additional information that is not included in the main body of the BOM. It can include details about alternate suppliers, special instructions or warnings about certain parts, and any other relevant notes.
Having an alternate supplier listed in the notes section is important as it allows for flexibility in the manufacturing process. If a specific part is not available from one supplier, having another option listed can save time and prevent delays. In addition, any special instructions or warnings can help prevent mistakes or accidents during production. The notes section may seem like a small component of a multi level BOM, but it can make all the difference in ensuring a smooth manufacturing process.
A fresh viewpoint: Purchase Order Process
What is a Multi-Level BOM (Indented BOM)?
A Multi-Level BOM, also known as an Indented BOM, is a type of Bill of Materials that shows the hierarchical relationship between different components and subassemblies of a product. Unlike a Single-Level BOM that only lists the individual parts needed to make the final product, a Multi-Level Bill breaks down each assembly into its component subassemblies, showing how they relate to one another. This can be especially helpful for manufacturers who need to understand how their products are assembled and what parts are necessary for each step.
For example, let's say you're a furniture manufacturer who makes wooden dressers. Your Indented BOM might start with the highest-level components (the dresser itself), then break down into first-level boms (like drawers and cabinet doors), which themselves might have second-level boms (such as hinges and drawer slides). By breaking everything down this way, you can see not just what parts go into your products but also how they all fit together.
While not all products manufacturers require Multi-Level BOMs or Indented BOMs, they can be incredibly useful when working with complex assemblies. By breaking everything down into discrete levels, you can more easily manage inventory and manufacturing processes, while also ensuring that every part is accounted for. Whether you're making furniture or electronics or anything in between, having clear and detailed Multi-Level Bills can make all the difference in streamlining your operations.
Worth a look: Bill of Materials
Frequently Asked Questions
What is a multi level Bom?
A multi level BOM, or Bill of Materials, is a hierarchical structure that shows the relationship between different components within a product. It helps manufacturers understand the parts needed for production and how they fit together.
What is a BOM level or hierarchy?
A BOM level or hierarchy is a way of organizing the different parts and components needed to make a product. It helps manufacturers understand the relationships between each part and how they fit together in the final product.
What is a multi level BOM in construction?
A multi level BOM in construction is a Bill of Materials that includes all components and sub-components required to complete a project, organized in a hierarchy. This helps ensure that all necessary materials are accounted for and simplifies the ordering process.
What is a manufacturing BOM?
A manufacturing BOM, or Bill of Materials, is a list of all the components and materials needed to produce a finished product. It serves as a blueprint for the production process and helps ensure that all necessary parts are accounted for.
What is a BOM in manufacturing?
A BOM (Bill of Materials) is a comprehensive list of all the components or parts required to manufacture a product. It includes raw materials, sub-assemblies, and finished products with their respective quantities and costs.
Featured Images: pexels.com