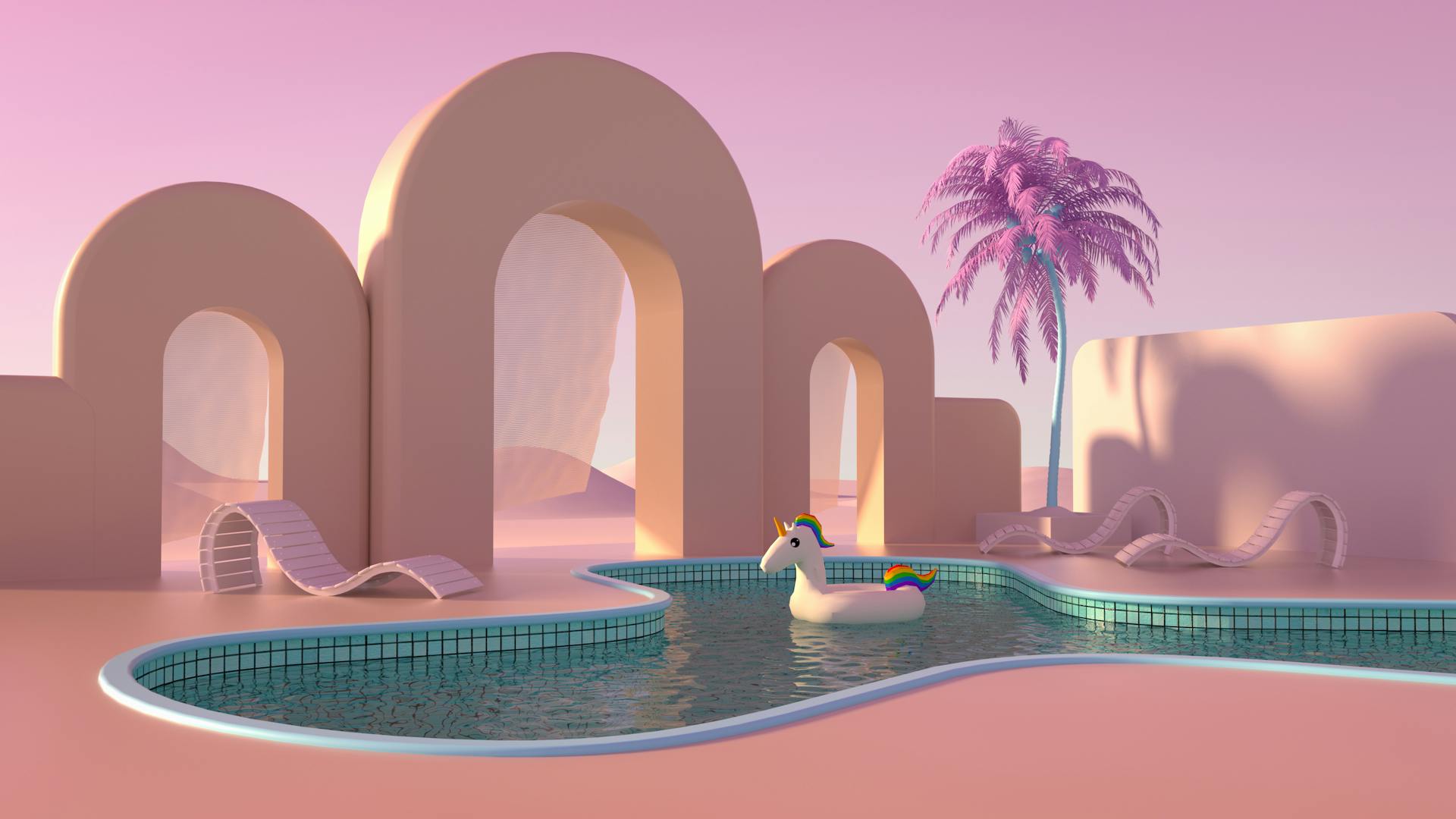
In the military aircraft industry, future programs are gaining interest in digital technologies such as the digital thread and digital twin concepts. These concepts apply lessons learned from the defense industry to upcoming programs, with a focus on digital manufacturing and cyber-physical system goals. Known as Industrie 4.0 or smart manufacturing, this concept is part of the Industrie 4.0 roadmap where cyber-physical system refers to a digital representation of a physical system that communicates properties and live status.
The future smart factories smart manufacturing strives to optimize business by digitizing physical processes through cyber-physical systems. To achieve this, system architects evaluate how similar digital connectivity goals start converging into a single framework strategy for manufacturing systems. The digital twin refers to a digital model that includes design specifications, engineering models describing geometry, materials, components, operational data unique to a specific physical asset, and more specifically identifies an entire product or system based on its unit identifier (tail number).
A fresh viewpoint: Barcode Systems for Manufacturing
How do digital threads enable digital twins?
Digital threads are the interrelated processes that connect the various related data sets in products, processes, and workflows. They use IIOT capabilities to establish a holistic view of engineering, manufacturing, and operation. Advanced versions incorporate physical world sensor data to create physics-based virtual sensors utilizing physical world proxies.
Digital twins are virtual representations of real-world data from a product or system. They allow users to test potential scenarios and find optimization opportunities before deploying them in an industrial environment. Digital threads enable product manufacturers to establish a holistic data set for their products by providing up-to-date information on the original design, engineering, and manufacturing operation.
The widespread adoption of IIOT technology connected worker technology, augmented reality (AR), and increasingly sophisticated MES systems is quickly expanding the supply chain networks' digital threads. The connective tissue enabling operational insights woven between multiple digital threads creates a digital fabric today's digital mesh needs to orchestrate digital experiences across all channels. This enables end-users to take full advantage of operational intelligence with minimal disruption while still using traditional tools such as spreadsheets or dashboards.
For your interest: Digital Marketing Strategy for Manufacturing Company
Begin and Grow Without Pressure: Finding Your Own Speed.
Digital transformation efforts are supported by the concept of a digital twin and the digital thread. However, manufacturers' initiatives show that there is no one-size-fits-all approach to this process. To achieve improvement success, it's important to start small and pursue achievable goals with appropriately scaled efforts. Digital change isn't an overnight process.
Areas leveraging past work and building upon them can be a great way to begin and grow without pressure. The product development lifecycle digital transformation is a cumulative effort that involves the integration of multiple technologies and systems. Finding your own speed in this journey is critical to avoid feeling overwhelmed while pursuing improvement efforts. By taking things one step at a time and focusing on your unique needs, you can make progress in your approach to digital twin and digital thread implementation.
A different take: Digital Manufacturing
How Digital Twins Aid Digital Transformation

Years ago, the manufacturing community created the term digital twin to describe a virtual representation of physically built organizations. This definition has since evolved to cover tool design, computer numerical control (CNC) equipment, cell lines, and facility planning. A strong foundation for functional departments' digital twin is crucial for optimized design and enhanced digital transformation investments.
A digital twin acts as a virtual single source of truth. Its accurate simulation of smart connected products' mechanical hardware, electronics, electrical distribution systems, and onboard software similarly sends sensor data to an internet-of-things (IoT) platform. Incorporating higher fidelity and detailed definitions from the get-go puts organizations in a position to support improvements throughout the entire development lifecycle.
The benefits of highly detailed and accurate digital twins are tangible. Manufacturing organizations realize tighter collaboration between functional departments, improved troubleshooting capabilities, reduced unnecessary errors, and informed decision-making abilities. The resulting strain on worker executing tasks decreases with robotic assistance. By incorporating detailed digital twins into plants' operations and enhancing their definitions over time, manufacturing organizations can reap significant benefits from their digital transformation investments.
The Power of Digital Thread: Streamlining Your Connections
Digital thread creates a closed loop between the physical and digital worlds, transforming how engineered manufactured products are created. Digital threads seek to create simple universal access to a single set of related data needed for business processes. They enable continuity between physical products, components, parts, and equipment and the digital world.
Layers of manufacturers operate in live cities, labs, worksites, and factories. Physical things are imbued with an incredible amount of product design data, manufacturing process data, asset health information, IoT data, and more. This pertinent information is needed to make decisions about worker tasks and supply chain driven activities that take place across entire operational environments. By utilizing similar threads throughout the enterprise software solutions for IIoT (Industrial Internet of Things), AR (Augmented Reality), MES (Manufacturing Execution System), CAD (Computer-Aided Design), PLM (Product Lifecycle Management), and more; companies create an environment where knowledge gleaned from one function can be shared upstream to inform decision-making in other areas.
The digital thread enables enterprises to effectively communicate bi-directionally across the entire product lifecycle management (PLM) spectrum including manufacturing instructions, supply chain management, service histories, customer events, etc. This thread ensures that all participants utilize current data so they can react quickly when necessary. By analyzing and managing this information through a variety of digital processes such as AR working instructions or IoT asset monitoring; communicate pertinent functions allowing faster decisions to be made using digital tools. All the knowledge gleaned is shared upstream throughout the entire operational environment creating a powerful feedback loop that drives innovation at every stage from design inception all the way through to final delivery.
Readers also liked: Ways Ar Apps
Frequently Asked Questions
Are digital threads the connective tissue of the future?
Yes, digital threads are the connective tissue of the future as they provide a seamless flow of information across different stages of product development and help to improve collaboration and decision-making.
What are digital twins and digital threads?
Digital twins are virtual replicas of physical objects or systems that allow for simulations and analyses to be conducted. Digital threads are the connections between various digital twins, allowing for seamless communication and data sharing among different parts of a system or organization.
What are the three layers of digital twins?
The three layers of digital twins are the physical layer, the digital representation layer, and the analytics layer. These layers work together to create a comprehensive virtual model that can be used for simulation, analysis, and optimization.
How can digital twins drive digital transformation?
Digital twins can drive digital transformation by providing a virtual representation of physical assets or processes, allowing for real-time monitoring and analysis of data. This enables businesses to optimize performance, reduce downtime, and make more informed decisions.
What are the benefits of having a digital twin?
A digital twin provides a virtual replica of physical assets, allowing for real-time monitoring and analysis. This helps improve efficiency, reduce downtime, and enhance decision-making capabilities for businesses.
Sources
- https://www.industryweek.com/technology-and-iiot/systems-integration/article/22007865/demystifying-the-digital-thread-and-digital-twin-concepts
- https://www.ptc.com/en/blogs/corporate/what-is-a-digital-thread
- https://blogs.sw.siemens.com/xcelerator/2021/04/29/the-role-of-the-digital-thread-and-digital-twin-in-digital-transformation/
Featured Images: pexels.com