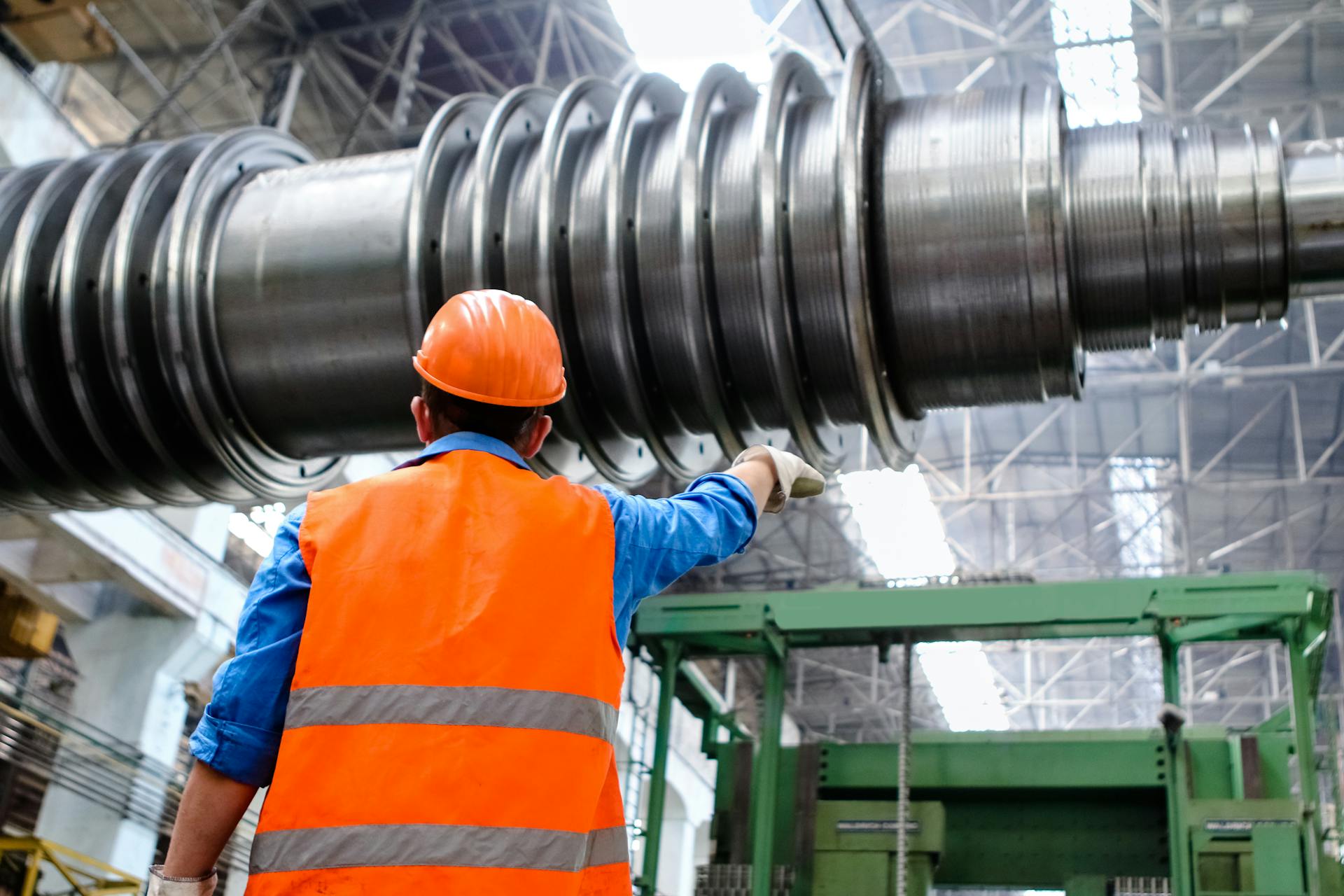
PPE manufacturing is something we have long heard of but may not fully understand. In our daily lives, we encounter potentially dangerous situations that can cause harm if proper precautions are not taken. This is where PPE equipment comes into play.
PPE stands for Personal Protective Equipment, and this gear protects workers from the potential hazards of their job. Common items considered PPE include gloves, safety glasses, earplugs, and more. Employers must administer manufacturing PPE to ensure their employees are protected from workplace hazards such as forms falling debris, sharp materials, chemicals, and other harmful substances.
Having a comprehensive understanding of PPE manufacturing lets us begin to appreciate its importance in our lives. Health organizations encourage us to make wearing the proper PPE a good habit when dealing with potentially hazardous situations. The failure to wear specific task-fitting PPE can result in severe consequences during manufacturing processes. Proper PPE usage helps reduce the risk of injury or illness resulting from exposure to these hazards.
Broaden your view: Farming Equipment Brands
Essential Guidelines for Ensuring PPE Safety Requirements
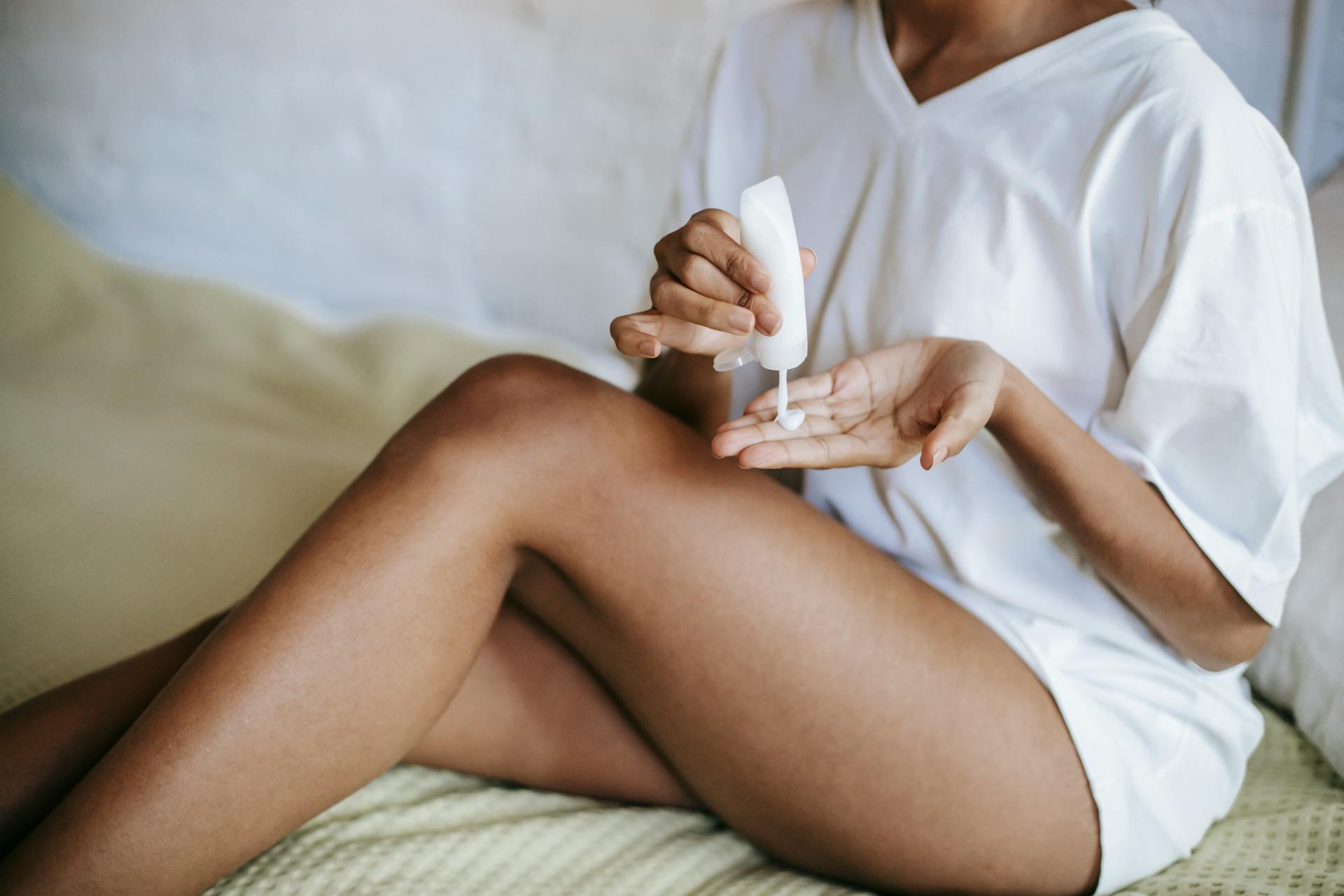
Promoting PPE safety is crucial to protecting employees from workplace hazards. Workplace safety officers should check work sites regularly to ensure that the needed properly-fitted PPE is available and provided to employees. It is important to train employees on the OSHA PPE standards and provide protective goggles, face shields, and safety glasses when working with flying particles or corrosive materials that pose a risk of eye punctures, abrasions, or contusions. Protective gloves are also required when employees are possibly exposed to corrosive liquids, chemicals, blood, or potentially infectious materials.
Foot protection is another critical aspect of PPE safety as foot injuries can result from hot corrosive or poisonous substances and falling objects. Inspect hard hats periodically to check the suspension system and maintain all PPE in ready-to-use conditions. Eyewash facilities and quick drench showers should be easily accessible in case an employee is accidentally exposed to corrosive materials.
It is essential to establish safe work procedures for decontaminating PPE after hazardous exposures. Properly cleaning and maintaining PPE will ensure that it remains effective at protecting against future exposures. By following these guidelines for promoting PPE safety, employers can create a safer work environment for their employees while minimizing the risks associated with hazardous exposures.
Take a look at this: Bill of Materials
Steps to administering manufacturing PPE properly in the workplace
Administering manufacturing PPE properly in the workplace is not an easy task. It takes great coordination and attention to detail to ensure that all employees are properly trained on how to use their personal protective equipment correctly. The first step in administering PPE is identifying the hazards present in the workplace and selecting appropriate protective equipment. Then, all employees should be trained on how to properly wear and care for their PPE, as well as how to inspect it for damage before each use. Finally, regular audits should be conducted to ensure that all employees are following proper PPE procedures.
The Vital Significance of PPE in the Manufacturing Industry
PPE manufacturing is critical to prevent injuries caused by hazardous materials, including chemicals, noise, heat, and flying debris. These potential injuries can occur if workers don't wear PPE, making it essential for workers to feel confident and safe in their workplace. By wearing PPE, workers can reduce the risk of injury and maintain a positive attitude towards their job.
In many cases, wearing PPE can even lead to increased productivity. A safe workplace is a happy workplace, and when workers feel secure in their environment, they are more motivated to perform better. For instance, OSHA (Occupational Safety and Health Administration) has set noise exposure limits that require workers to wear hearing protection in loud environments. By preventing injuries with PPE, employers can save money on medical expenses and lost productivity while ensuring that employees are healthy and happy.
Preventing injuries with PPE not only saves money but also protects workers alike from expenses related to workplace injuries. When employees know that they are wearing the necessary equipment to do their job safely, they have peace of mind knowing that they won't suffer any harm as a result of their work. Ultimately, investing in PPE manufacturing means investing in the well-being of both employers and employees while minimizing the risk of potential hazards associated with working on-site.
Discover the different categories: 4 fundamental kinds
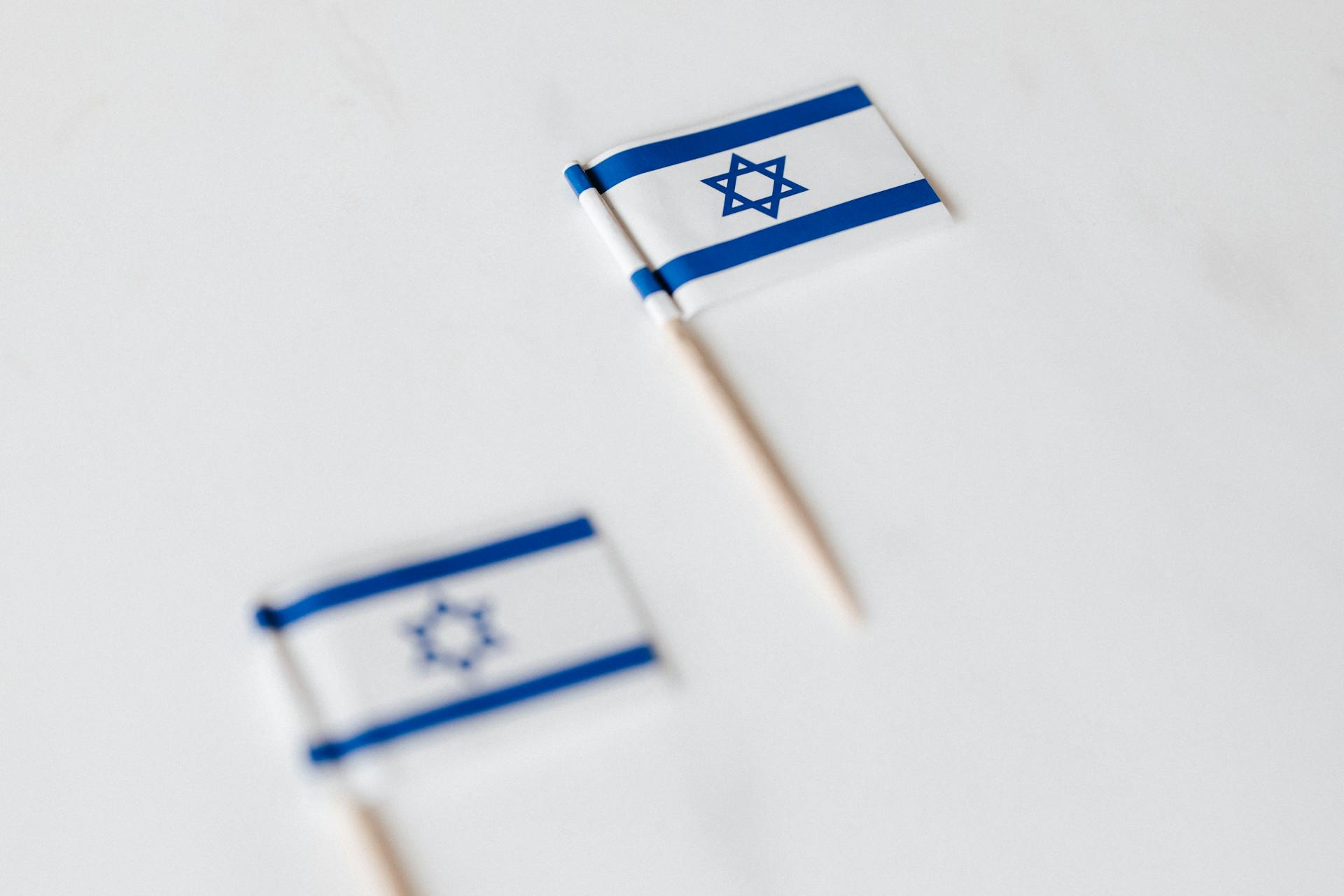
When it comes to workplace safety equipment, there are numerous types of Personal Protective Equipment (PPE) available. The four fundamental kinds of PPE are basic PPE, specialized PPE, hazard assessment-based PPE, and job task-based PPE. Basic PPE includes items such as gloves, hard hats, and safety glasses that protect employees from general hazards. Specialized PPE is necessary in certain work conditions where basic PPE does not necessarily eliminate the hazard exposure. Hazard assessment-based PPE is determined after a thorough evaluation of the risks present in a particular work environment. Job task-based PPE is chosen based on specific job tasks performed by employees and must adhere to strictest controls for maximum protection against potential hazards.
1. Skin and Body Protection
PPE includes hard hats, safety vests, heat-resistant clothing, safety gloves, knee pads, safety boots, and safety harnesses among others. The primary purpose of PPE is to protect employees from physical hazards in the workplace. These hazards include extreme temperatures, flames, sparks, toxic chemicals, insect bites, and object falling among others. Safety tips recommend that hard hats should be tightened inside to ensure good fit and eliminate electrical resistance. Workers should also avoid exposing themselves to direct sunlight as well as using harmful cleaning agents.
Safety tips recommend that employees should ensure full body protection by wearing bodysuits or heat-resistant clothing when handling high-temperature hazards. Safety gloves are also recommended to prevent skin burns and absorption of harmful substances that could cause cuts or fractures. Workers should ensure hand protection fits perfectly to avoid cuts or burns caused by chemical residue on rubber gloves. Additionally, workers should use knee pads and safety boots to prevent leg injuries caused by rolling objects or hot substances as well as electrical hazards on slippery surfaces.
Finally, it is important for employees to use safety harnesses when working at heights to prevent falling incidents that could lead to tears, deformities or burn marks in case of a fall. Safety tips suggest that harnesses should be connected securely to the worker's body during a falling incident. Additionally, workers should ensure their safety boots have slip-resistant soles and sole plate in good condition to prevent punctures while walking on slippery surfaces.
Here's an interesting read: Manufacturing Company Tips
Experience efficient production with cellular manufacturing
If you're in the business of PPE manufacturing, you know how important it is to keep up with demand. One important component of that is implementing a lean manufacturing mindset, which includes using cellular manufacturing. This great technique involves grouping similar processes together in a cell, allowing for faster production times and less waste.
By utilizing cellular manufacturing, you can process improvement discover opportunities that will help your business thrive. Not only does this method reduce lead times and improve quality control, but it also helps ensure that your team is working efficiently and effectively. With this approach, you'll be able to meet demand while keeping costs low – which is crucial for success in any industry.
In conclusion, if you're looking for effective business tips for PPE manufacturing or any other industry where efficiency is key, consider implementing cellular manufacturing. It's a proven method that has been successful in many different settings and can help streamline your production process. With just 4 mins read on this article, you've already taken the first step towards improving your bottom line – so why not give it a try?
Take a look at this: Purchase Order Process
Discover What PPE is and What it Means in Your Workplace
Personal protective equipment (PPE) refers to a range of equipment designed to reduce employee exposure to chemical, biological, and physical hazards in the workplace. The purpose of PPE is to protect employees from harm by creating a barrier between them and the hazard. PPE is just one part of an overall safety program that includes engineering and administrative controls to keep exposure levels below acceptable levels. Understanding what PPE is and how it works is essential for employers who want to protect their workers from harm.
PPE Safety Examples
When it comes to PPE manufacturing, safety should always come first. The idea we've created is to provide high-quality personal protective equipment that meets the necessary safety standards. This means designing and producing products that can effectively protect workers from harm in various hazardous work environments.
To ensure the safety of our PPE, we conduct regular testing and quality control checks. We also provide sample PDF reports and preview sample PPE reports so that our clients can see the results for themselves. By following these practices, we can confidently say that our PPE will provide reliable protection for those who need it most.
Consider reading: Manufacturing Quality Control
ensuring safety and joy for all
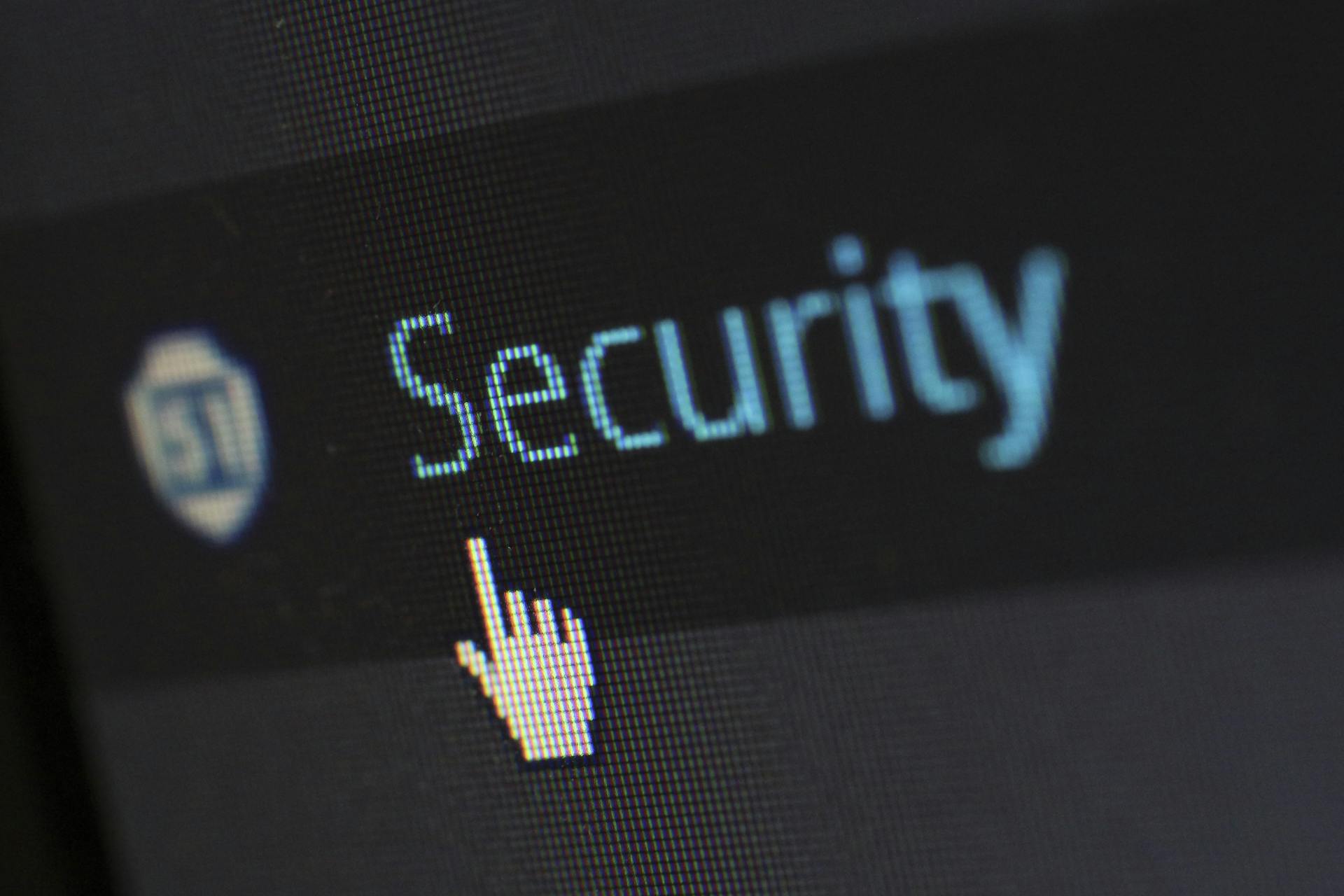
As a manufacturing employer, it's crucial to administer manufacturing PPE properly. Protecting workers is a top priority, and providing them with the necessary protective equipment is essential. Keeping track of your PPE inventory can be challenging, but with Katanas end-to-end ERP software, inventory movements become much more manageable.
With Katanas, you can easily set reorder points for each item in your PPE inventory, ensuring that you never run out of critical supplies. This feature helps avoid PPE-related shutdowns that could harm production and cause delays in delivering finished goods to customers. The software also streamlines the manufacturing process and ensures that the final product meets quality standards.
Katanas offers a 14-day free trial that allows manufacturing employers to test out its features without any commitment. By investing in this solution, you're not only protecting your workers but also safeguarding your business from potential shutdowns due to PPE shortages. With Katanas end-to-end ERP software, you can ensure safety and joy for all by producing high-quality products while keeping workers safe.
Frequently Asked Questions
What is PPE in nursing?
PPE in nursing stands for Personal Protective Equipment, which includes masks, gloves, gowns, and eye protection. It is used to protect both the patient and the healthcare worker from infectious diseases.
Should employers conduct PPE training to comply with OSHA standards?
Yes, employers are required by OSHA standards to provide PPE training to their employees in order to ensure workplace safety and prevent accidents.
How did the PPE shortage happen?
The PPE shortage happened due to a combination of factors, including increased demand from healthcare workers, disruptions in global supply chains, and inadequate preparedness for a pandemic.
How much did the PPE industry receive in grants?
As of August 2021, the PPE industry has received over $4 billion in grants from various government agencies and private organizations to support their efforts during the COVID-19 pandemic.
What happened to PPE manufacturers during the pandemic?
PPE manufacturers experienced a surge in demand during the pandemic as healthcare workers and the general public needed more protective equipment. Supply chain disruptions and shortages of raw materials also impacted their ability to meet demand.
Featured Images: pexels.com