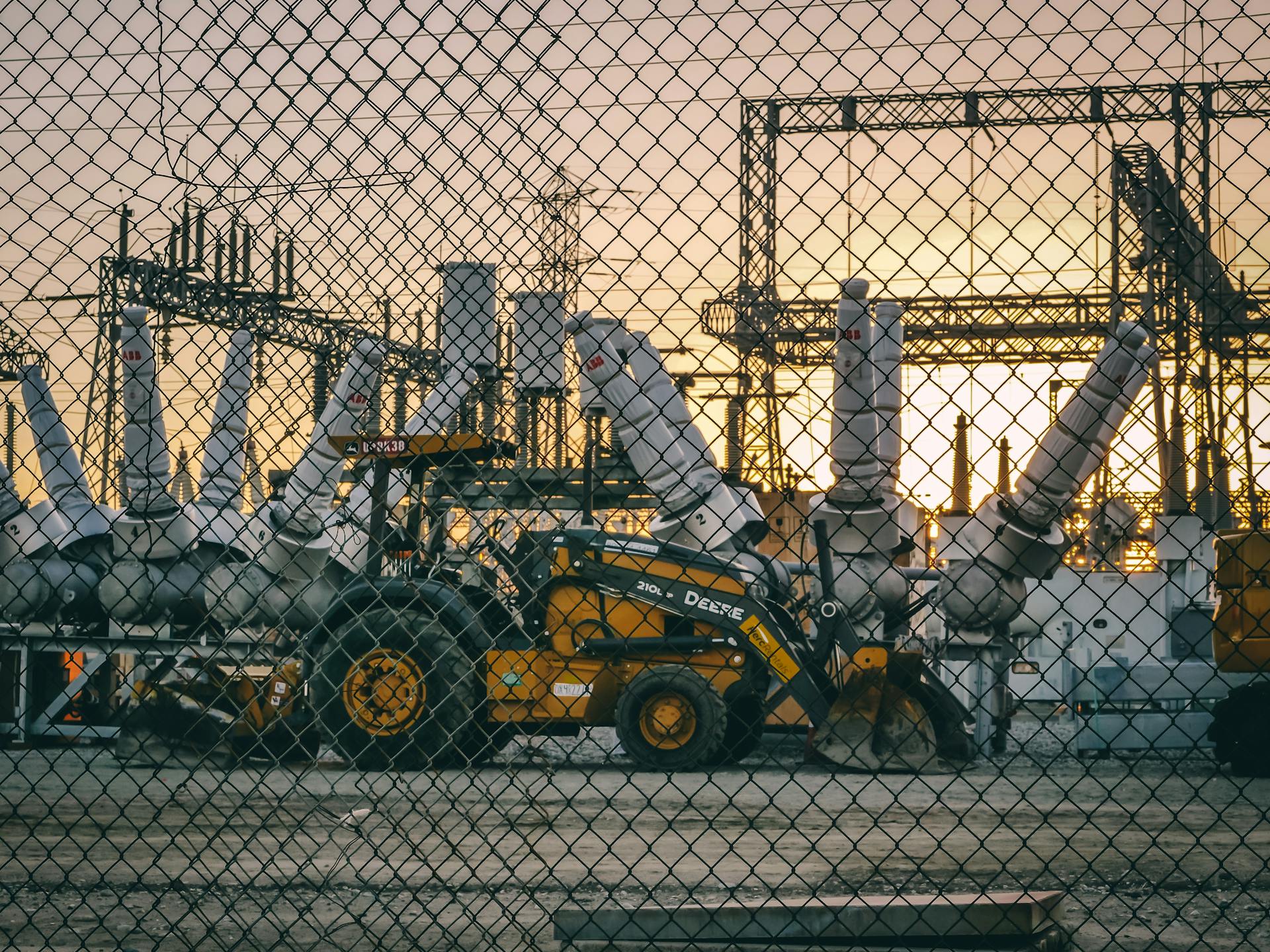
Turbogenerator systems have been a crucial component in thermal power plants for decades, providing efficient and reliable electricity generation.
In a typical thermal power plant, a turbogenerator system can achieve an efficiency of up to 40% in converting thermal energy into electrical energy.
These systems are designed to withstand high temperatures and pressures, often operating at temperatures above 1,000°C and pressures over 100 bar.
The high efficiency of turbogenerator systems makes them an attractive option for power plants, allowing them to generate more electricity while minimizing fuel consumption.
What Is a Turbogenerator?
A turbogenerator is a large electric generator driven by a steam turbine, water turbine or gas turbine to generate electrical power. This process is fundamental to the functioning of contemporary society.
The production of electricity is essential, and turbogenerators convert a variety of energy forms into usable electricity. This ensures a constant and efficient supply for various industrial, commercial and residential sectors.
A turbogenerator is connected to a steam turbine, which is particularly used in power plant infrastructure. This is where the large-scale generation of electricity takes place.
Mechanical energy is harnessed to transform it into electrical energy through the operation of a turbogenerator. This is the basic concept behind how turbogenerators work.
Construction Features
A turbo generator's construction features are quite fascinating. The rotor is typically a non-salient pole type, usually with two poles.
High shaft rotational speeds are typical of steam and gas turbines, and this is where turbo generators shine. The normal speed of a turbo generator is 1500 or 3000 rpm with four or two poles at 50 Hz.
The rotor is subjected to high mechanical stresses due to its high operation speed. To make it mechanically resistant, the rotor is forged from solid steel and alloys like chromium-nickel-steel or chromium-nickel-molybdenum are used.
The overhang of windings at the periphery is secured by steel retaining rings. Heavy non-magnetic metal wedges on top of the slots hold the field windings against centrifugal forces.
Consider reading: Turboexpander
Hard composition insulating materials, like mica and asbestos, are used in the slots of the rotor. These materials can withstand high temperatures and high crushing forces.
The stator of large turbo generators may be built of two or more parts, while in smaller turbo-generators it is built up in one complete piece.
Here are some common features of turbo generators:
- cylindrical laminated rotor design or salient pole rotor design
- standardized frame sizes
- end shield design
- GVPI (global vacuum pressure impregnation) or VPI (vacuum pressure impregnation) technology
- stator coil-winding or bar-winding design
- brushless or static excitation
- air/water coolers, air/air coolers or open ventilated configuration
- low noise and vibration levels
- packaged design to enable short installation cycles
- excitation and protection system, LS/NS cubicles, bus ducts, synchronization
Cooling Systems
The cooling system plays a crucial role in maintaining the temperature of a turbogenerator within safe limits. This is essential to prolong the life of insulating materials and other critical components, ensuring efficient and reliable operation.
Hydrogen-cooled turbo generators use gaseous hydrogen as the coolant, which offers high thermal conductivity, high specific heat, and low density. This makes it the most common type in its field today, with a 99.0% efficiency.
A hermetically sealed generator prevents the escape of hydrogen gas, reducing damage to the windings' insulation by corona discharges. The cooling system is also designed to dissipate heat generated by internal energy losses during operation, typically using a gas-to-water heat exchanger.
You might enjoy: Hydrogen Turboexpander-generator
A table highlighting the key features of a cooling system in a turbogenerator:
The cooling system is designed to work in conjunction with the excitation system, which supplies the necessary direct current to the rotor winding to create the magnetic field required for electricity generation.
Hydrogen-Cooled
Hydrogen-cooled turbo generators first went into service in October 1937 at the Dayton Power & Light Co. in Dayton, Ohio.
The high thermal conductivity, high specific heat, and low density of hydrogen gas make it an ideal coolant, allowing for a 99.0% efficiency.
Hydrogen is used as the coolant in the rotor and sometimes the stator of the generator, increasing specific utilization. The generator is hermetically sealed to prevent escape of the hydrogen gas.
The absence of oxygen in the atmosphere within the generator significantly reduces the damage of the windings' insulation by eventual corona discharges.
Hydrogen can be manufactured on-site by electrolysis, and it's cooled by a gas-to-water heat exchanger.
Air Cooled
Air Cooled systems are a popular choice for turbo generators, and for good reason. They can handle a wide range of ratings, from 10 MVA to 56 MVA, making them suitable for various applications.
More than 150 four-pole turbo generators have been supplied with air-cooled systems, demonstrating their reliability and effectiveness.
Air-cooled turbo generators are also available in two-pole configurations, which can range from 50 MVA to 220 MVA. This makes them ideal for larger applications.
Over 850 air-cooled turbo generators have been supplied, showcasing their widespread adoption in the industry.
Here are some key features of air-cooled turbo generators:
- up to 220 MVA, capable of synchronous condenser operation
- VPI technology (vacuum pressure impregnation)
- brushless or static excitation
- air/water coolers or open-ventilated configuration
- low noise and vibration levels
- packaged design to enable short installation cycles
- excitation and protection system, LS/NS cubicles, bus ducts, synchronization
Frequently Asked Questions
What is the difference between a generator and a turbo generator?
A turbo generator is essentially a combination of a turbine and an electric generator, whereas a traditional generator is a standalone unit that converts mechanical energy into electricity. The key difference lies in the turbo generator's ability to be powered by a turbine, making it a more efficient and versatile option.
What is the principle of turbo alternator?
The principle of turbo alternators is electromagnetic induction, where kinetic energy from steam drives the rotor to generate electricity. This process harnesses the power of steam to produce electricity efficiently.
What is the efficiency of the turbogenerator?
The efficiency of a hydrogen-cooled turbo generator is 99.0%. This high efficiency is due to the unique properties of hydrogen as a coolant.
Can a turbo be used to generate electricity?
Yes, a turbocharger can be converted into a microturbine for power generation, but it requires a complex and challenging design due to high speeds and temperatures. This conversion is technically possible, but it's a difficult engineering task.
Sources
- https://en.wikipedia.org/wiki/Turbo_generator
- https://www.ansaldoenergia.com/offering/equipment/generators/turbogenerators
- https://aerospace.honeywell.com/us/en/products-and-services/product/hardware-and-systems/electric-power/the-honeywell-turbogenerator
- https://www.andritz.com/products-en/hydro/markets/turbogenerator-thermal-power
- https://inspenet.com/en/articulo/turbo-generator-applications/
Featured Images: pexels.com