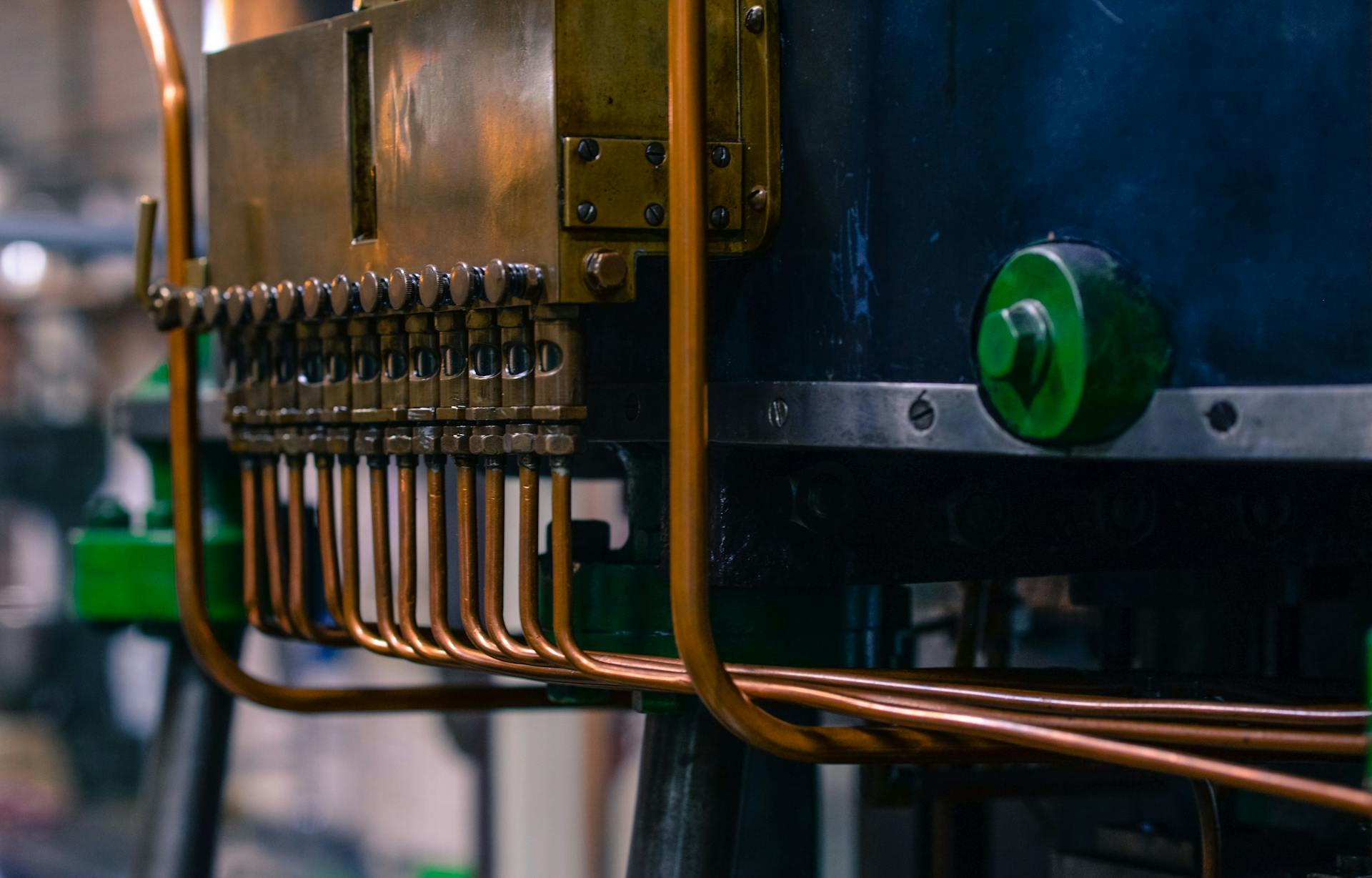
Turbo expander design and engineering services are crucial for optimizing the performance of turbo expanders in various industrial applications. Turbo expanders can be designed to handle different types of fluids, including natural gas and refrigerants.
The design process involves selecting the right materials and components to ensure the turbo expander can withstand the operating conditions. This includes choosing the right impeller and diffuser designs to achieve the desired expansion ratio.
A good turbo expander design can significantly improve the efficiency of the expansion process, reducing energy losses and increasing overall system performance. By optimizing the design, engineers can also minimize the risk of damage to the turbo expander and other connected equipment.
Turbo expander design and engineering services can be tailored to meet the specific needs of various industries, including oil and gas, chemical processing, and cryogenic applications.
Applications
Turboexpanders are incredibly versatile, with a wide range of applications across various industries.
One of the primary uses of turboexpanders is in low-temperature processes, such as gas liquefaction and power recovery. These processes require the expansion of gases to extremely low temperatures, which turboexpanders are well-suited to handle.
Turboexpanders are also used in process refrigeration and power recovery as process fluid compression, which is essential in industries like gas processing, chemical, and petrochemical.
In these applications, turboexpanders can be supplied with oil lubricated bearings or active magnetic bearings, offering flexibility and reliability.
Design and Engineering
At L.A. Turbine, they use a rigorous design process to ensure each turboexpander meets performance, flow, and quality requirements. Their engineering design and development processes are ISO 9001:2008 compliant, guaranteeing a high level of quality.
They employ multiple engineering approaches, including 3D CAD Based Design, which allows for faster design cycles and automated drawings, reducing errors and speeding up deliveries. 1D Meanline Analysis is also used to perform initial sizing and predict performance without the need for time-consuming CFD analysis.
The company uses advanced commercial turbomachinery design and CFD codes for 3D Design & Analysis, as well as Finite Element Analysis (FEA) for structural analysis of critical parts. This ensures a robust design that can withstand the operating range.
Here are some of the key design and engineering approaches used by L.A. Turbine:
- 3D CAD Based Design
- 1D Meanline Analysis
- 3D Design & Analysis
- Structural Analysis
- Resonance Analysis
- Resonance Testing
- Rotor Dynamics
- Machine Verification
Engineering Design
Engineering design is a crucial aspect of creating reliable and efficient machinery. L.A. Turbine's team of experts uses multiple engineering approaches in the design process to ensure each turboexpander meets performance, flow, and quality requirements.
Their design process is ISO 9001:2008 compliant, which means it meets international standards for quality management. This ensures that every step of the design process is thoroughly planned and executed.
The company uses 3D CAD based design to create accurate drawings and generate bills of material quickly. This approach reduces errors and speeds up delivery times.
1D meanline analysis is also used to perform initial sizing and predict performance without the need for time-consuming CFD analysis. This in-house developed code, combined with commercial software, gives L.A. Turbine a competitive edge.
Advanced commercial turbomachinery design and CFD codes are used for 3D design and analysis. This allows the team to predict machine performance with high accuracy.
Finite Element Analysis (FEA) is used to analyze the structural integrity of critical parts. This ensures that the design is robust and can withstand the operating range.
Resonance analysis is a stringent predictive structural analysis that is applied to all wheel designs before fabrication. This step helps identify potential issues before they become major problems.
All wheels undergo rigorous "ring" tests, using lightweight accelerometers paired with an impact hammer, to identify all resonant frequencies. This testing ensures that the wheels are designed and built to withstand the demands of the turboexpander.
Here are some of the key engineering approaches used by L.A. Turbine:
- 3D CAD based design
- 1D meanline analysis
- 3D design and analysis
- Structural analysis (FEA)
- Resonance analysis
- Resonance testing
- Rotor dynamics analysis
- Machine verification
With over 45 years of design and manufacturing expertise, L.A. Turbine's team has developed a reputation for creating reliable and efficient machinery. Their commitment to using cutting-edge design technologies ensures that their machinery remains at the forefront of the industry.
Engineering Support Services
Engineering Support Services is crucial for the successful operation of complex systems like the FreeSpin® In-line Turboexpander.
Sapphire Technologies provides comprehensive commissioning support after installation, ensuring the system is properly checked and prepared for start-up.
The commissioning process includes training the site user on how the system works.
Maintenance requirements for the FreeSpin® system are minimal, but Sapphire Technologies is available to support any needs that may arise.
The primary maintenance task is periodic cleaning of the air filters, typically performed by the user.
Introduction to Rotor Dynamics
Designing and engineering a turboexpander requires a deep understanding of rotor dynamics. This complex field involves predicting and analyzing the behavior of rotating parts under various operating conditions.
To ensure robust design, L.A. Turbine performs Finite Element Analysis (FEA) of critical parts, which ensures the design can withstand the operating range. This helps prevent costly failures and downtime.
Rotor dynamics analysis is crucial in predicting critical speeds and ensuring the turboexpander operates safely and efficiently. Advanced commercial software is used for API-compliant rotor dynamics analysis throughout the required operating range.
Resonance analysis is also applied to all wheel designs prior to fabrication, identifying potential issues before they become problems. This proactive approach helps prevent costly repairs and ensures the turboexpander meets performance and quality requirements.
Here's a breakdown of the rotor dynamics analysis process:
- API-compliant rotor dynamics analysis
- Advanced commercial software
- Required operating range
Critical speeds can be verified using the Bently-Nevada ADRE system, which measures and analyzes machine vibration. This helps ensure the turboexpander operates within safe limits, reducing the risk of failure and downtime.
Product Selector
The Product Selector is a valuable tool for finding the right turboexpander for your application. It matches horsepower and mass flow to select the correct size.
You can use this tool to find a turboexpander for hydrocarbon processing, industrial gas liquefaction, or power recovery and generation. These are the main areas where LAT designs and builds turboexpanders.
Their designs include expander-compressors with active magnetic bearings or oil bearings, expander-dynos with oil brakes, expander-generators, high-speed direct-drive expander generators, and specialized machines.
Amb Off Skid Controller
The AMB off skid controller is a great option for those who want a safe and controlled experience. It's designed for use in unclassified/safe areas.
This type of controller is perfect for operators who desire an unpurged AMB control panel.
Dynamometer
A dynamometer is a high-speed machine used in various applications, including the Expander-Dynamometer, which is composed of an expander stage loaded by an oil brake.
The Expander-Dynamometer is a type of turboexpander-dynamometer that uses an oil brake instead of a compressor or generator. This design allows for efficient energy recovery.
In the context of the Expander-Dynamometer, the oil brake plays a crucial role in loading the expander stage.
Configurations & Specifications
The ARES AMB Turboexpander is a reliable choice for many applications, with its compact design making it a great option for space-constrained projects.
The ARES AMB Turboexpander comes in various frame sizes, allowing for flexibility in installation and design.
With a wide range of flows, from 10 to 200 kg/s, the ARES AMB Turboexpander can handle various process conditions.
You can expect high-pressure ratios of up to 10:1, making it suitable for high-pressure applications.
The turboexpander's wheel power output can reach up to 5 MW, providing a significant amount of power for various industrial processes.
Its operating temperature range is from -20°C to 200°C, making it a versatile option for various operating conditions.
The turboexpander's pressure ratio and wheel power output are directly related, so understanding these specifications is crucial for proper design and engineering.
Gearbox Redesign
Gearbox Redesign is a crucial aspect of improving the performance of industrial equipment. Eight non-LAT built turboexpanders were underperforming in the field.
A redesign of the gearbox can make a significant difference in efficiency. We solved the problem of underperforming turboexpanders by redesigning the gearbox.
The key to a successful gearbox redesign is identifying areas for improvement. In this case, we found that the existing design was not meeting the required performance standards.
A well-designed gearbox can reduce energy consumption and increase overall system efficiency. By redesigning the gearbox, we were able to improve the performance of the turboexpanders.
The redesign process involved careful analysis and testing to ensure that the new design met the required specifications.
Frequently Asked Questions
What does a turbo expander do?
A turbo expander converts high-pressure gas into work, often powering a compressor or generator. It does this by expanding the gas through a turbine, producing energy that can be harnessed for various applications.
What is the difference between a gas turbine and a turbo expander?
The main difference between a gas turbine and a turbo expander is their primary function: turbines generate power, while turbo expanders reduce pressure and generate power. This distinction lies in their design and application, with turbines often used for power generation and turbo expanders used for pressure reduction.
What is the difference between a turbo expander and a JT valve?
A turbo expander extracts work from gas expansion via a turbine, whereas a JT valve achieves a constant enthalpy expansion adiabatically without work output. In essence, a turbo expander is a more efficient version of a JT valve.
What is the cryogenic turbo expander process?
The cryogenic turbo expander process is a method that uses a turboexpander to produce refrigeration and achieve very low temperatures. This process enables the recovery of valuable light components, such as ethane and propane.
What is the pressure ratio of a turboexpander?
A typical single-stage turboexpander has a pressure ratio of 4:1, but it can range up to 14:1 depending on the process. This significant pressure drop enables energy removal and cryogenic temperature reduction.
Featured Images: pexels.com