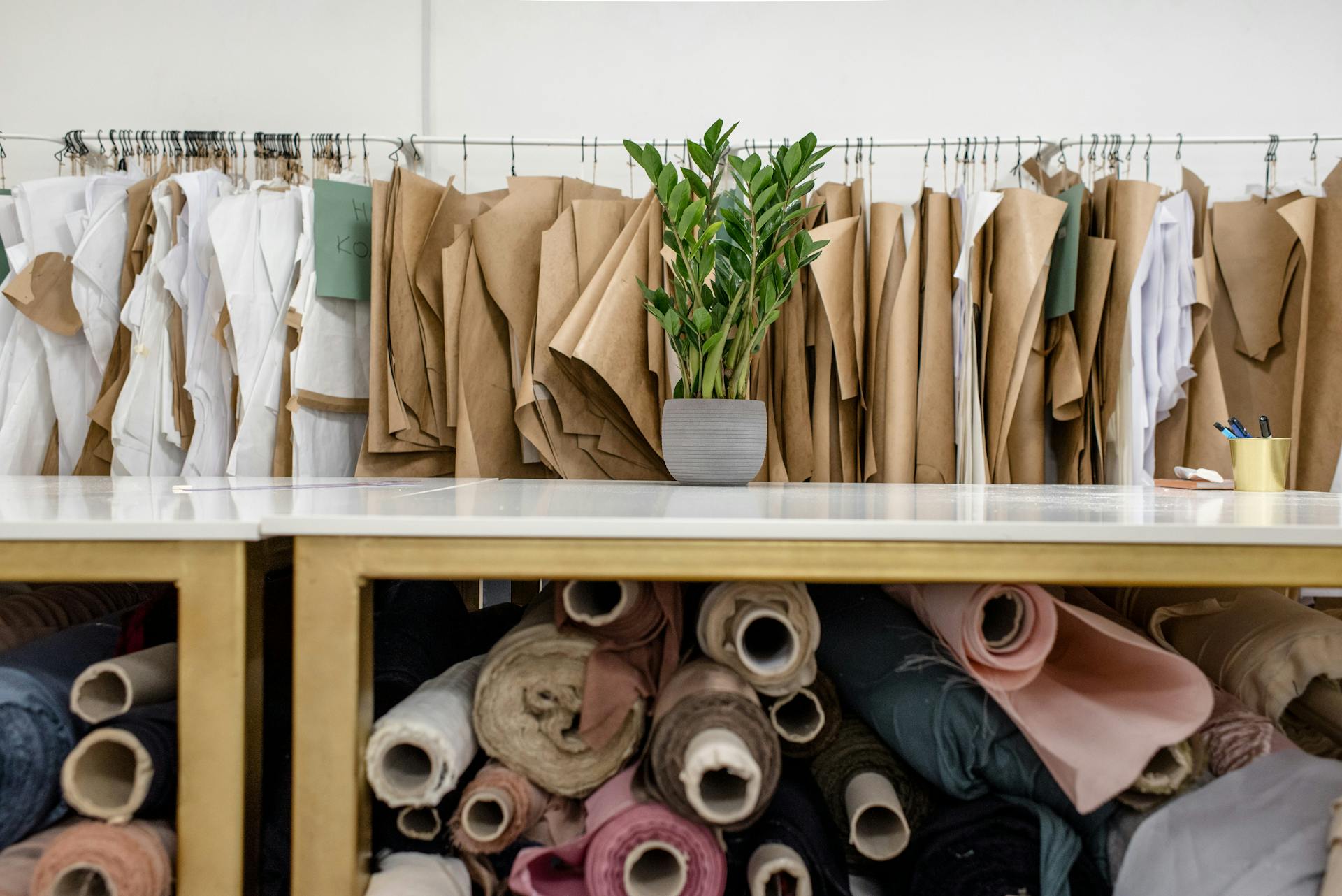
Textile manufacturing is a diverse industry that has been around for centuries. We've looked back in time and discovered textile making weaving dating back to prehistoric times. Things stem from the importance of providing comfort, and textiles have remained an important staple ever since. The textile manufacturing industry is an important industry that represents millions of jobs worldwide.
Despite its long-standing history, the textile manufacturing industry has had a sullied reputation due to exploitation and ill-treatment toward factory workers. The tragic Rana Plaza collapse in 2013 shed light on the dangerous working conditions and low wages many textile workers face. However, we've delved deeper into how this important industry works today, and there's so much more to uncover in the fascinating world of textile manufacturing.
In this article, we'll unravel the key to success in the textile manufacturing business by exploring how modern-day textile manufacturers operate today. We'll share pro tips on everything from textile production to manufacturing inventory management, giving you insights into what it takes to succeed in this exciting field. So come along as we take a deep dive into the fascinating world of textile manufacturing!
Consider reading: Digital Marketing Strategy for Manufacturing Company
Discover the Fascinating World of Textile Manufacturing!
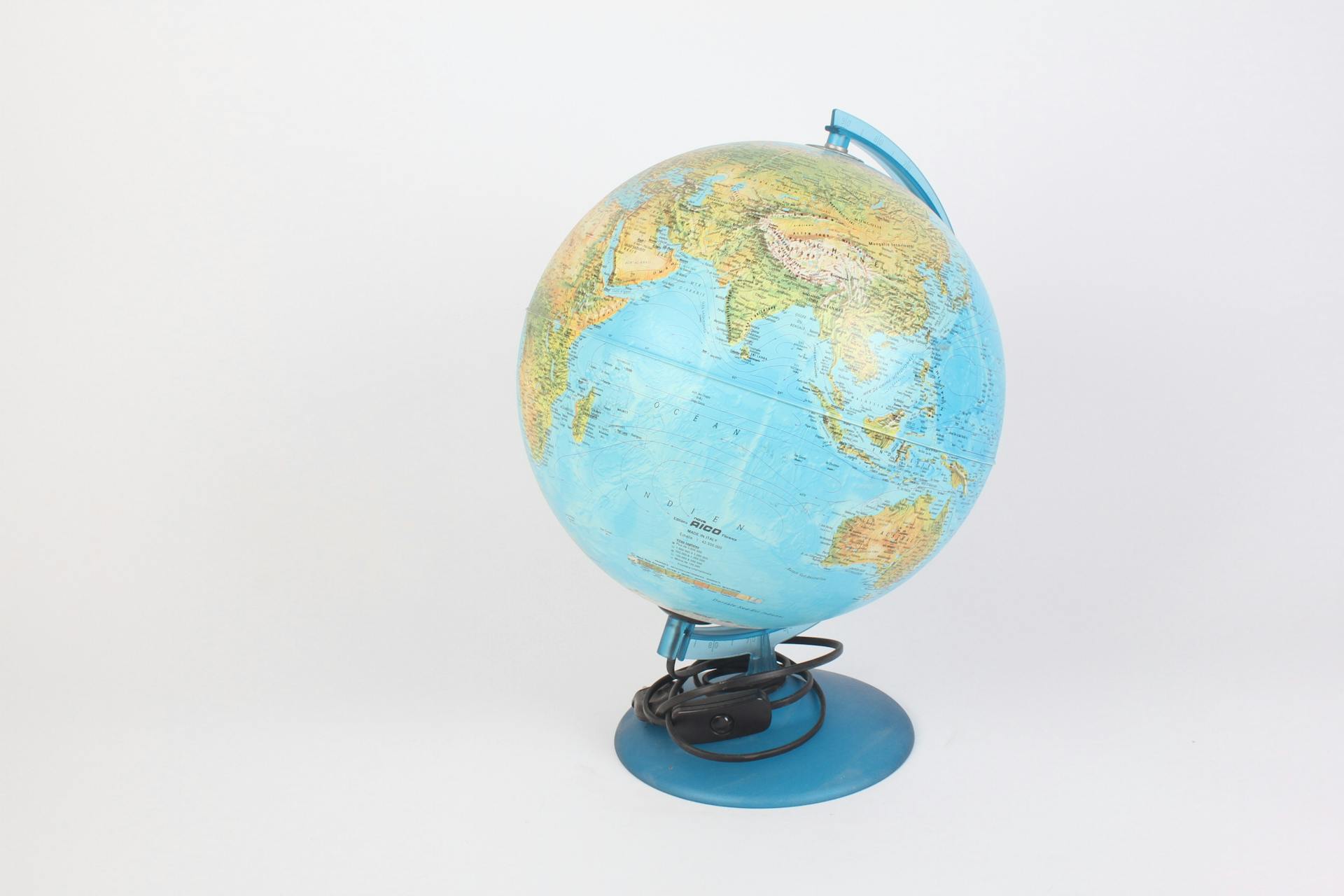
Textile manufacturing is a huge industry that has been around for centuries. It involves the production of fabrics, including dyed printed and woven fabrics, from various materials such as cotton remaining the most important natural fiber in use today. In fact, in 2007 alone, over 25 million tons of cotton were produced on an area of 35 million hectares worldwide.
Textile production is a complex process that produces tons of finished products every day. Textile production processes have changed over time. From the Latin word textilis meaning "woven," to the French exere meaning "to weave," textiles have come a long way since their inception.
Today, textile manufacturers operate with modern machinery and advanced technology to produce high-quality fabrics efficiently. This important industry continues to grow, with a huge increase in textile production seen in recent years. So why not dive deeper into this fascinating world and discover how textiles are made?
Historical and Modern Textile Manufacturing
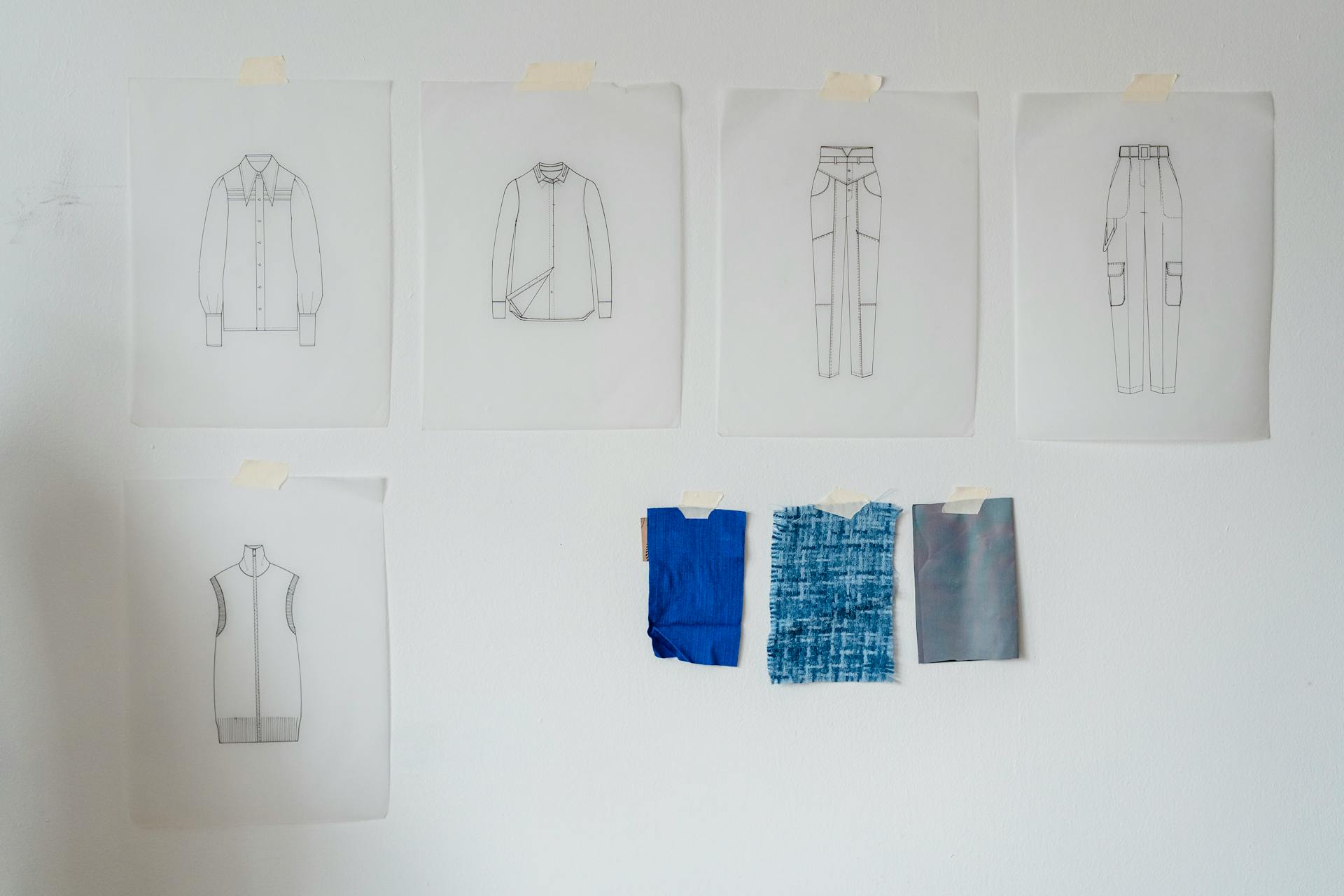
The earliest textile manufacturing process dates back to the Neolithic period, where people employed repeated movement to create loops and design nets. As mentioned earlier, the ancient trade network known as the Silk Road played a significant role in the development of textile manufacturing. Iron, ivory, horses, pottery, and silk pass through this route making them influential commodities in various civilizations.
Fast forward to the industrial revolution; large-scale textile manufacturing employs process automation to produce fabrics in an incredibly short amount of time. However, this has resulted in a decline in jobs for the manufacturing workforce. Despite this setback, textile manufacturing remains an important industry today.
In 2018, textile manufacturing accounted for approximately $250 billion worth of apparel shipments globally. With free trade agreement partners making up a significant portion of its trade, textile manufacturing companies find success by adapting to modern technology while staying true to their roots in traditional craftsmanship. The silk road may have evolved into something different now, but the strength of its legacy continues through advancements in modern-day textile manufacturing.
Expand your knowledge: Discrete vs Process Manufacturing
Cotton Goes Through an Intriguing Transformation
Cotton is an important natural fibre used in textile manufacturing. This versatile crop has been cultivated for thousands of years and continues to be a major player in the industry today. In the year 2007, global yield was around 25 million tons, with approximately 35 million hectares cultivated across 50 countries.
The transformation of cotton from a plant into cotton textiles involves several preparatory processes. The first step is harvesting the raw material, which involves picking the cotton bolls by hand or machine. After being harvested, the fibres must then be separated from the seeds using a process called ginning. Once separated, the cotton fibres are processed further through spinning, weaving or knitting to create various types of fabrics.
Overall, the transformation of cotton from a humble crop into fashionable and functional textiles is truly fascinating. From its cultivation in fields spanning millions of hectares worldwide to its processing through various preparatory processes, cotton remains one of the most important natural fibres used in textile manufacturing today.
1. Cultivating and harvesting[edit]
Cultivating and harvesting cotton is an important part of textile manufacturing. The planting season starts in the early spring, with the cotton bolls appearing during long hot dry summers. Low humidity Indian cotton gossypium arboreum produces shorter staples, while hand processing American cotton gossypium hirsutum produces longer staple needed for mechanized textile production.
To harvest the cotton boll, there are two main methods: stripper harvesters and spindle pickers. Stripper harvesters remove the entire boll from the plant, while spindle pickers pull just the seed pod from the cotton plant attached to a small amount of fiber. Using these machines can result in a higher rate of produced compared to actual workers needed on a farm. Mississippi bower flowers produced almost 13,000 bales which could create around 94 million t-shirts!
2. Preparatory processes – preparation of yarn[edit]
One of the preparatory processes in textile manufacturing is the preparation of yarn. This involves several steps, including ginning, bale-making, blending mixing, and scutching. Scutching refers to the process of cleaning cotton before it is spun into yarn.
The scutching machine was first developed in Manchester, England and was generally adopted throughout the textile industry. The scutching machine worked by using steel bars called beater bars to quickly strike the cotton hard against parallel bars. This process helped to remove any impurities and allowed for air to flow through the cotton chamber more easily. Overall, proper preparation of yarn is essential for high-quality textile production.
Curious to learn more? Check out: Manufacturing Process Automation
3. Spinning – yarn manufacture[edit]
Spinning is the process of creating yarns from fibers. It is an intermittent process that was frame advanced by Samuel Crompton's invention, the spinning mule, in 1779. The mule spinning method produces high-quality twisted thread that is perfect for making fine fabrics. Another popular spinning method is the ring spinning, which was developed later on with the invention of Richard Arkwright's water frame. Ring spinning is a continuous process that results in yarns with greater twist and strength.
Cotton counts refer to the number of yards of cotton yarn that weighs 1 pound (0.45 kg). For example, a 10-count cotton means that 840 yards (770 meters) of yarn weighs 1 pound (0.45 kg). In the United Kingdom counts, a coarse Oldham counts 40 while in the United States, it refers to medium counts. Fine count yarns are often used for warp threads in ring spinning and require more time to produce since they only have seven leas per pound (840 yards). The worsted hank is also another significant measurement used in spinning; it measures 560 yards per hank and can be wound onto a warp beam weighing up to 10 pounds and holding around 80 threads at about 120 yards each. An alternative method used for creating single yarn involves taking a set amount of fiber such as silk or nylon and measuring it out to create either a single yarn of 15 denier or double yarns totaling 30 denier per kilometer.
4. Weaving[edit]
Weaving is an essential process in textile manufacturing. It involves the interlacing of lengthwise threads (warp threads) with crosswise threads (weft passes) to create fabric. The weaving process starts by winding warp threads onto a warp beam, which is then placed on a loom. The sheds open and close to create an open shed for the weft passes to be inserted, and a closed shed for the warp threads to be tightened. The pattern requires that the warp threads are automatically changed to create different designs. This can be done on quick-running looms or slow looms with underpick motions.
In making cloth, picks refer to weft ends, while ends refer to the quarter-inch square inch square ends of heavy domestics or coarse yarns. Draw boys were used on hand looms, which home children helped with from an early age piecing together sections of cloth. As weaving moved into mills during the Industrial Revolution, mill children and their older sisters were employed to prevent child labour. Pirning processing was used for shuttles until bobbins were introduced in 1733 by John Kay. Today, modern technology has made it possible for weaving machines to produce textiles in bulk quantities with minimal manual labor required.
5. Knitting – fabric manufacture[edit]
Knitting is one of the ways to produce textiles, and it involves the interlocking of yarn to create fabric. Hand knitting is a popular way to create small projects like scarves and hats, while machine knitting utilizes weft machines or warp machines that can use single spools or multiple spools depending on the desired outcome.
Warp knitting uses vertical chains zigzagged across the machine cylinder to produce fabrics with a more structured look, while weft knitting uses separate spool containers to create fabrics with a looser, more baggy appearance like the average t-shirt. Cotton yarn giving the finished product an incredibly soft texture is often used in both types of knits. Whether warp knits or weft knits are used, both techniques are essential in textile manufacturing as they offer versatility in creating different types of garments and items.
6. Finishing – processing of textiles[edit]
Finishing is a crucial step in textile manufacturing that adds value to the fabric by enhancing its appearance, feel, and performance. This broad range of finishing processes prepares the textile for the end-user fresh from the loom cotton fabric. The first step involves removing impurities including warp size, non-fibrous impurities, and seed fragments that remain scouring. This chemical washing process is carried out using iron vessels called kiers with an alkali solution or dilute acid to remove natural waxes and free fatty acids. The next step precedes scouring and involves removing size by soaking it in a caustic soda solution under pressure excluding oxygen. Once the fabric cotton has been scoured and bleached using diluted sodium hypochlorite or hydrogen peroxide to improve whiteness, it can be dyed or undergo important non-chemical finishing treatments such as mechanical pre-shrinking, surface fibres smoothing by passing through plates heated by gas flames or sharp teeth imparting downiness softness, embossed effects using heated rollers that generate smooth polished surfaces on the fabric's surface fibres. Additionally, fabrics can produce low flammability crease-resistance through chemical treatments.
Dyeing is a complex chemistry method that offers several dyeing methods depending on the prescribed procedure to achieve improved fastness against washing rubbing. Anionic direct dyes are commonly used for completely immersing cotton fabrics into an aqueous dye bath. Localized dyeing printing designs can also be achieved using previously dyed fabric or predetermine patterns for deep shades, lower levels for white bedding, medical applications or highest levels of dye affinity cotton fibers.
7. Economic, environmental and political consequences of cotton manufacture[edit]
The process of cotton manufacture has significant economic, environmental, and political consequences. Cotton requires arable land to grow and is farmed intensively, requiring large amounts of water to sustain the crop. Modern hybrids are often rainwater fed, which spreads pests and depletes cotton-bearing land. In the textile industry, cotton makes up a major portion of fibre production for spinning, twisting, weaving and knitting for clothing manufacturing. Wet processing including washing, de-sizing, bleaching, rinsing, dyeing printing and coating also uses large quantities of water. The chemical wet processing stage dominates consumption patterns while miscellaneous processes power dominates energy consumption patterns.
Moreover, cotton acts as both a carbon sink and emitter due to fertiliser application and mechanised tools used in its manufacture. Genetically modified cotton crops require expensive pesticides and insecticides aimed at increasing disease resistance. Water required for farming adds an environmental concern especially in organic sectors where water shortages are common in most cotton-growing areas around the world. Mechanisation of cotton harvesting has reduced the need for manual labour that was once done by African slaves or forced labour such as in 2012 Uzbekistan where it remains a major exporter despite concerns raised by human rights groups who have expressed concerns about the use of children to pick cotton. There is currently a 15 million tonne deficit of cotton expected in 2018 due to adverse weather conditions limiting water availability and pest issues affecting crops worldwide.
8. Flax[edit]
Flax is one of the most important bast fibres used in textile manufacturing. It is extracted from the stem of the linum usitatissimum plant, which is commonly found in cooler regions around the world. The process begins when the plant flowers and produces seeds, which are then harvested and dried. Once the seeds are removed, the stalks are left to dry and when they’re ready, they are crushed to extract the fibres.
These fibres are then processed further to create linen, one of the oldest textiles known to man. Linen is widely used for clothing, bed linen and home furnishings due to its durability and strength. Flax has been used for thousands of years and continues to be an important part of textile production today.
9. Jute[edit]
Jute is a natural bast fibre that comes from the Corchorus genus plant. It is very similar to flax and can be found in many parts of the world. Jute has been used for centuries to make a variety of products, including carpets, jute bags, and jutton fabrics.
In textile manufacturing, jute is often used to make composite fabrics. These fabrics are made by blending jute fibres with other materials like cotton or polyester. The resulting fabric is durable, flexible, and has a unique texture that makes it perfect for creating intricate designs. Work continues on improving the quality and quantity of jute fibres in order to make better composite fabrics. In the 1970s, jute-cotton composite fabrics were popular, and today small amounts of jute are still used in textiles all over the world.
10. Hemp[edit]
Hemp is a type of plant that is part of the cannabis sativa species. It has been used for centuries to create a variety of products, including textile materials. The bast fiber, which comes from the stem of the hemp plant, is particularly useful for making cord and other durable materials.
Hemp textiles have become increasingly popular in recent years due to their eco-friendly properties. Hemp plants require less water and pesticides than other crops used in textile manufacturing, making them a more sustainable option. Additionally, hemp fabrics are known for their strength and durability, ensuring they can withstand wear and tear over time. Overall, hemp textiles are a versatile and sustainable option for those interested in eco-friendly fashion choices.
11. Other bast fibres[edit]
Other bast fibres that are commonly used in textile manufacturing include kenaf, urena, ramie and nettle. Each of these fibres has unique properties that make them suitable for different types of fabrics.
Kenaf is a fast-growing plant that produces strong and durable fibres. It is often blended with other materials to create fabrics that are both lightweight and breathable. Urena is another fast-growing plant that produces soft and silky fibres that are ideal for creating luxurious fabrics.
Ramie is a fibre that comes from the stem of the Chinese nettle plant. It is known for its strength, durability and ability to hold shape well. Nettle fibre is also gaining popularity in the fashion industry due to its sustainable sourcing and versatility in creating various types of fabrics.
12. Other leaf fibres[edit]
Other leaf fibres are also used in textile manufacturing besides the main leaf fibre. These fibres include sisal, abaca, and henequen. Sisal is a strong and durable leaf fibre derived from the agave plant, commonly used for rugs, mats, and cordage. Abaca is another leaf fibre known for its strength and flexibility, often used in paper products and ropes. Henequen is similar to sisal, but with a softer texture and finer quality.
While these other leaf fibres may not be as widely used as the main leaf fibre, they still play an important role in the textile industry. Their unique properties make them suitable for specific applications, such as in heavy-duty products or those requiring flexibility. As the demand for sustainable and eco-friendly materials continues to grow, these alternative leaf fibres may become even more popular in textile manufacturing.
13. Wool[edit]
Wool is a fibre obtained from the fleece of domesticated sheep. The wool fibres are used to make two types of yarn woolens and thread woolens. Wool fibres have unique properties that make it ideal for textile manufacturing. The fibres trap air, creating fluffy yarns or parallel fibres, creating smooth yarns. Modern sheep breeds are bred for uniform fleeces, but landrace sheep have dual coats with soft short undercoats and hardier coarser longer guard layers that have differing characteristics. These layers are processed separately to create durable outerwear or ultrafine wedding ring shawls.
In Europe spinning lopi produces unique yarn by combining both the soft undercoat and long guard hairs of Icelandic sheep. To produce high-quality wool, skilled shearers must handle the soiled wool carefully. After grading based on length, worsteds fibres which form short wool are separated from woollens fibre in carding machines that jumbled arrangement into arranged perpendicular fibers that can be spun into yarn using worsted combs. Grease and vegetable matter are removed with an opening machine before sulphuric acid carbonising washing or sodium carbonate cleaning removes any remaining impurities. Recovered wool can also be felted or chemically extracted to produce pills or materials for other products such as rags or shoddy materials.
Frequently Asked Questions
Why is product development important for textile manufacturers?
Product development is important for textile manufacturers because it allows them to create new and innovative products that meet the changing needs of their customers, stay ahead of competitors, and increase revenue.
What does a textile production manager do?
A textile production manager is responsible for overseeing the production process of textiles, from sourcing materials to ensuring efficient manufacturing and delivery. They work to ensure quality control and timely delivery of products.
What is the history of textile manufacturing in Philadelphia?
Philadelphia has a rich history of textile manufacturing dating back to the late 18th century, with the city becoming a major center for woolen and cotton fabrics in the early 19th century. The industry experienced ups and downs over the years but still plays a significant role in Philadelphia's economy today.
How does the Silk Road affect textile manufacturing?
The Silk Road facilitated the spread of textile manufacturing techniques and materials across different regions, leading to a globalized industry with diverse cultural influences.
How many women were employed in the textile industry in 1950?
It is estimated that around 2.5 million women were employed in the textile industry in the United States in 1950.
Featured Images: pexels.com