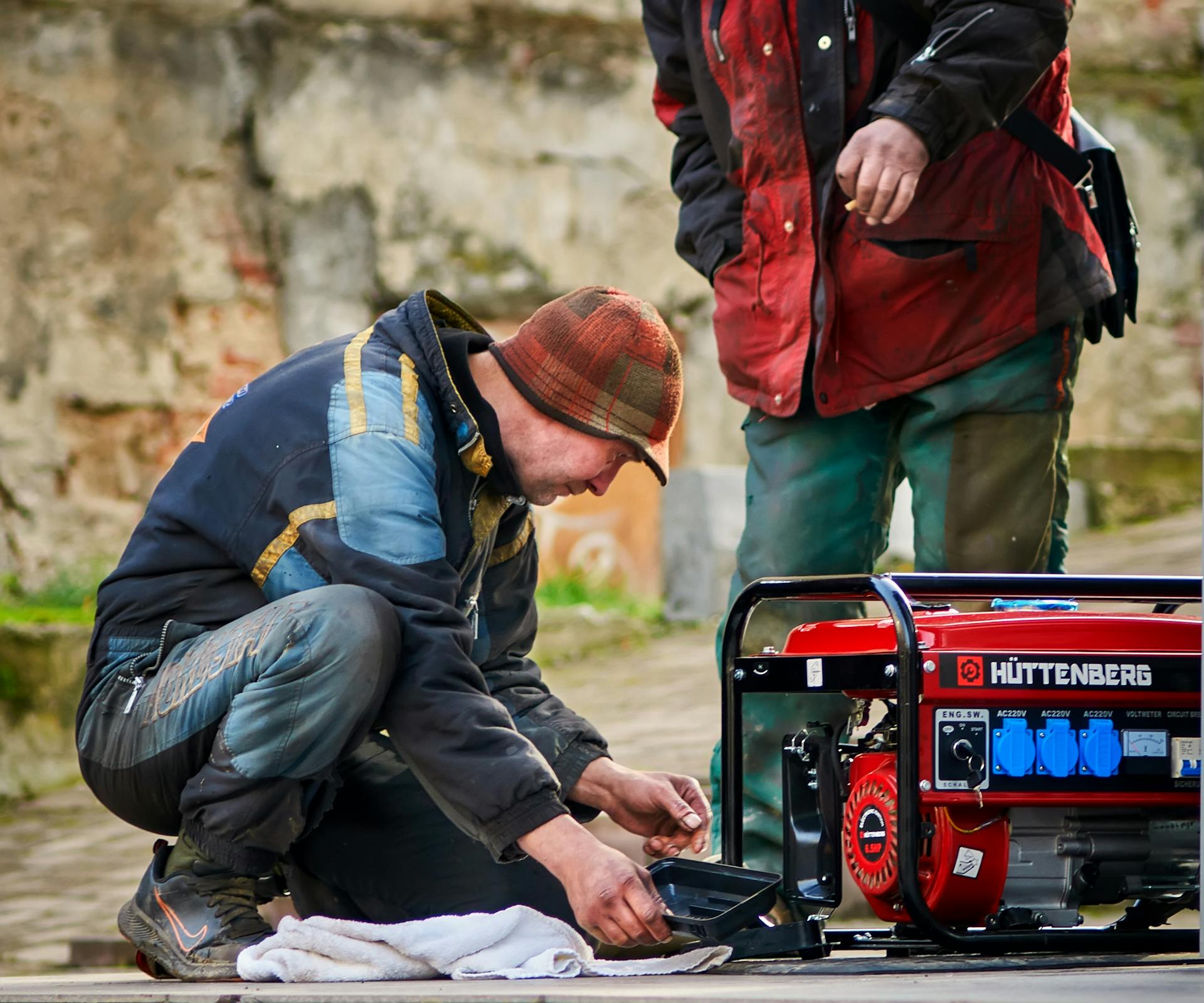
Researchers have made significant breakthroughs in developing efficient thermoelectric generator systems. These systems have the potential to harness waste heat from various sources and convert it into usable electricity.
A thermoelectric generator study has shown that the use of advanced materials can significantly improve the efficiency of these systems. By leveraging the unique properties of these materials, scientists have been able to create more effective thermoelectric devices.
The study has also highlighted the importance of optimizing the design of thermoelectric generators to maximize their performance. By carefully selecting the materials and configuration of the device, researchers have been able to achieve significant gains in efficiency.
For another approach, see: Seebeck Generator Efficiency
Thermoelectric Generator Study
The thermoelectric generator (TEG) is a device that converts heat into electricity, and researchers have been studying its performance to improve its efficiency.
The TEG device structure is a disc sandwich structure, where 12 heat pipes are evenly arranged on each cold and hot disc, and these heat pipes are 6 mm in diameter and 40 mm in height.
A coaxial circular structure is used for the cold and hot plates, which allows for even flow and heat transfer characteristics throughout the disc.
The TEG device is divided into six similar structures, each with two columns of heat pipes in hot and cold discs, making it easier to analyze the flow and heat transfer characteristics.
The researchers built 17 TEGs with 127 couples, and each TEG has an overall size of 40 × 40 × 3.8 mm, obtained from Fuxin Company, Guangdong.
The TEGs are arranged in a similar sandwich structure with two heat pipes evenly arranged in each hot and cold plate, and there are 17 cold and 17 hot plates for the TEG pieces.
The researchers used type-K thermocouples with an accuracy of ±0.4% to measure the cold and hot side temperatures, with five TEG pieces arranged as thermocouples.
The power generation performance of the TEG is affected by air and water flow, with air flow having a bigger effect on power and voltage than water flow.
The power and voltage increase with air flow, with a power increase from 0.639 to 1.6 W and a voltage increase from 6.2 to 9.817 V when the air flow is between 0.415 m/min and 0.927 m/min.
The air flow is the main influencing factor for the TEG group on the power generation characteristics, making it crucial to optimize air flow for improved performance.
You might like: Ac 6 Coral Generator
Design and Materials
Thermoelectric generators are made of several thermopiles, each consisting of many thermocouples made of a connected n-type and p-type material. The arrangement of the thermocouples is typically in three main designs: planar, vertical, and mixed.
The efficiency of a thermoelectric material is estimated by its figure of merit zT, which is calculated as SσT/κ, where S is the Seebeck coefficient, σ is the electrical conductivity, T is the temperature, and κ is the thermal conductivity.
To be good thermoelectric materials, these materials must have both high electrical conductivity (σ) and low thermal conductivity (κ). For many years, the main three semiconductors known to have both low thermal conductivity and high power factor were bismuth telluride (Bi2Te3), lead telluride (PbTe), and silicon germanium (SiGe).
Conventional materials are employed in commercial applications today, and can be divided into three groups based on the temperature range of operation: low temperature materials (up to around 450 K), intermediate temperature (up to 850 K), and highest temperatures material (up to 1300 K).
Discover more: Generators Create Electrical Energy.
New thermoelectric materials are being developed to improve the figure-of-merit zT. One example of these materials is the semiconductor compound ß-Zn4Sb3, which possesses an exceptionally low thermal conductivity and exhibits a maximum zT of 1.3 at a temperature of 670K.
Here are some common thermoelectric materials and their temperature ranges:
Design
Thermoelectric generators have a solid-state design that allows them to operate in severe environments.
This design makes them non-orientation dependent, meaning they can be used in zero-gravity or deep-sea applications.
Their solid-state design also eliminates the need for fluids for fuel or cooling.
Thermoelectric generators have no moving parts, producing a more reliable device that doesn't require maintenance for long periods.
This reliability and durability have made thermoelectrics a favorite for NASA's deep space explorers among other applications.
Their ability to operate in extreme conditions makes them ideal for use in harsh environments.
Materials for TEG
Materials for TEG are crucial for efficient power generation. Most thermoelectric materials have a zT value of around 1, such as bismuth telluride (Bi2Te3) at room temperature and lead telluride (PbTe) at 500–700 K.
To be competitive with other power generation systems, TEG materials should have a zT of 2–3. This is because a higher zT value indicates better thermoelectric performance.
The Seebeck coefficient (S) and thermal conductivity are key factors in determining a material's zT value. Most research in thermoelectric materials has focused on increasing the Seebeck coefficient (S) and reducing the thermal conductivity.
Thermal expansion can introduce stress in the device, causing fracture of the thermoelectric legs or separation from the coupling material. The mechanical properties of the materials must be considered, and the coefficient of thermal expansion of the n and p-type material must be matched reasonably well.
A material's compatibility factor is defined as s = (1 + zT - 1/ST). When the compatibility factor from one segment to the next differs by more than a factor of about two, the device will not operate efficiently.
Thermoelectric materials can be categorized into conventional and new materials. Conventional materials include alloys based on bismuth (Bi) and tellurium (Te), which are commonly used in commercial applications today.
New materials, such as the semiconductor compound ß-Zn4Sb3, are being developed to improve the figure-of-merit zT. This material has an exceptionally low thermal conductivity and exhibits a maximum zT of 1.3 at a temperature of 670 K.
Consider reading: 3 Phase Portable Generators
The following table highlights some of the key thermoelectric materials:
These materials are just a few examples of the many thermoelectric materials being researched and developed. By understanding the properties and limitations of these materials, designers can create more efficient and effective thermoelectric generators.
Novel Processing
Novel processing techniques can significantly improve the figure of merit (zT) of thermoelectric materials. This is achieved by minimizing thermal conductivity while maximizing electrical conductivity and Seebeck coefficient.
To reduce thermal conductivity, a novel processing technique exploits the scattering of different phonon frequencies. This selective reduction of lattice thermal conductivity doesn't have the typical negative effects on electrical conductivity.
Liquid-phase sintering is used to produce low-energy semicoherent grain boundaries in a bismuth antimony tellurium ternary system. These grain boundaries don't have a significant scattering effect on electrons.
Applying pressure to the liquid during sintering creates a transient flow of the Te-rich liquid. This facilitates the formation of dislocations that greatly reduce lattice conductivity.
Here's an interesting read: Examples of Electrical Generators
The ability to selectively decrease lattice conductivity results in a reported zT value of 1.86. This is a significant improvement over commercial thermoelectric generators with zT values of around 0.3–0.6.
Using different processing techniques to design microstructure is a viable and worthwhile effort. It often makes sense to work to optimize both composition and microstructure.
Module
A thermoelectric module is a circuit containing thermoelectric materials which generate electricity from heat directly. It consists of two dissimilar thermoelectric materials joined at their ends: an n-type semiconductor and a p-type semiconductor.
The current magnitude in a thermoelectric module is directly proportional to the temperature difference between the ends of the materials. This is due to the Seebeck coefficient, a property of the local material, and the temperature gradient.
Thermoelectric modules in power generation work in very tough mechanical and thermal conditions, with large thermally induced stresses and strains for long periods. They are also subject to mechanical fatigue caused by a large number of thermal cycles.
The junctions and materials in a thermoelectric module must be selected so that they survive these tough mechanical and thermal conditions. This is crucial for the module's efficiency and lifespan.
The efficiency of a thermoelectric module is greatly affected by the geometry of its design. This means that the arrangement of the thermocouples and the materials used can significantly impact the module's performance.
System Components
A thermoelectric generator system requires several key components to function effectively. The system uses thermoelectric modules, which generate power by taking in heat from a source such as a hot exhaust flue.
To operate, the system needs a large temperature gradient, which is not easy to achieve in real-world applications. The cold side must be cooled by air or water, and heat exchangers are used on both sides of the modules to supply this heating and cooling.
The system also requires heat exchanger technologies to balance the heat flow through the modules and maximize the temperature gradient across them.
Power Generator Structure
The power generator structure is a crucial component of a thermoelectric system. It's responsible for generating power by harnessing heat from a source.
A thermoelectric system uses thermoelectric modules to generate power, and these modules require a large temperature gradient to operate. This temperature gradient is not always easy to achieve in real-world applications.
To achieve high efficiency in the system, extensive engineering design is required to balance heat flow through the modules and maximize the temperature gradient across them. This involves designing heat exchanger technologies in the system.
In a disc sandwich structure, the cold plate and hot plate are designed as a coaxial circular structure, with 12 heat pipes evenly arranged on each disc. The heat pipes are 6 mm in diameter and 40 mm in height.
The disc sandwich structure is divided into six similar structures, each with two columns of heat pipes in hot and cold discs. A similar sandwich structure is built instead of one similar structure, with two heat pipes evenly arranged in each hot plate and cold plate.
17 TEGs (TEGs-1-127-1.4-1.6-250) with 127 couples are built, and their overall size is 40 × 40 × 3.8 mm. They are arranged in the similar sandwich structure and connected in series on the circuit.
To measure the heat transfer performance, type-K thermocouples with an accuracy of ±0.4% are arranged in some cold plate surfaces and hot plate surfaces. These thermocouples are used to measure the cold side temperatures and hot side temperatures.
Experimental System Setup
When setting up an experimental system, you'll need a reliable power source. This can be achieved using a 120V AC power supply, as mentioned in the "System Components" article.
The power supply should be placed in a well-ventilated area to prevent overheating. This is crucial to ensure the longevity of the system.
A 3-phase power supply is not required for this setup, as a single-phase supply will suffice. This is because the system's components are designed to operate within a single-phase power range.
Related reading: Components of Ac Generator
The power supply should be connected to the system's motherboard using a 20-gauge wire. This is to prevent any potential electrical shocks or damage to the system's components.
The motherboard should be placed on a sturdy, anti-static surface to prevent damage from static electricity. This is a common issue that can be easily avoided by using an anti-static surface.
The system's components, including the CPU and memory, should be installed on the motherboard according to the manufacturer's instructions. This will ensure that the system is properly configured and ready for use.
Take a look at this: Parts of Dc Generator
Hot Side Fluids Effect
The hot side fluids in a portable diesel powered screw air compressor play a crucial role in dissipating heat from the exhaust gas, compressor oil, and engine radiator coolant.
Compressor oil has a better potential for heat transfer compared to ethylene glycol and exhaust gas.
The heat transfer from compressor oil is more effective, making it a key component in the cooling system.
Related reading: Generator Engine Oil
The temperature profiles with different media's, as shown in Figure 7, demonstrate the varying heat transfer rates.
The input flow parameters for different fluids were kept the same, except for the material properties and input temperature.
The numerical simulation results show a significant temperature and voltage distribution for different medium.
Performance and Results
The performance of a thermoelectric generator (TEG) is crucial to its effectiveness. Power generation performance is shown in Figures 7A and B, where both power and voltage increase with air and water flow.
Air flow has a significant impact on power generation, with a bigger effect on power and voltage compared to water flow. In fact, when the air flow is between 0.415 m/min and 0.927 m/min, the power is increased from 0.639 to 1.6 W and the voltage from 6.2 to 9.817 V.
Water flow, on the other hand, has a smaller effect on power generation. For example, when the water flow is between 3 L/min and 9 L/min, the power is only increased from 1.179 to 1.268 W and the voltage from 8.415 to 8.69 V.
For more insights, see: Peltier Effect Generator
The air flow is the main influencing factor for the TEG group on power generation characteristics. This is evident from the power and voltage curves, which show a significant increase with air flow.
In some cases, the power generation performance can be affected by the working conditions. For instance, when the water flow is 6 L/min and the air flow is between 0.415 m/min and 0.927 m/min, the power and voltage are increased.
Limitations and Optimization
Thermoelectric generators have some significant limitations that affect their practicality in certain applications. High generator output resistance is a major issue, making it difficult to deliver maximum power to loads with low impedance.
This is because the maximum power transfer theorem dictates that maximum power is delivered when the source and load resistances are matched. To mitigate this, some commercial devices place more elements in parallel and fewer in series, and employ a boost regulator to raise the voltage.
Low thermal conductivity is another limitation, making thermoelectric generators unsuitable for applications where heat removal is critical. This is especially true for digital microprocessors, which require very high thermal conductivity to transport thermal energy away from the heat source.
In air-cooled applications, such as harvesting thermal energy from a motor vehicle's crankcase, the large amount of thermal energy that must be dissipated into ambient air presents a significant challenge. A supplementary radiator can be used for improved heat removal, but this adds parasitic loss to the total generator output power.
Here are some key limitations of thermoelectric generators:
- High generator output resistance
- Low thermal conductivity
- Difficulty with cold-side heat removal in air-cooled applications
Future Market
The future market for thermoelectric generators is looking bright. The global market is estimated to reach US$1.44 billion by 2030, with a compound annual growth rate (CAGR) of 11.8%.
North America currently captures 66% of the market share and will continue to be the biggest market in the near future. Asia-Pacific and European countries are projected to grow at relatively higher rates.
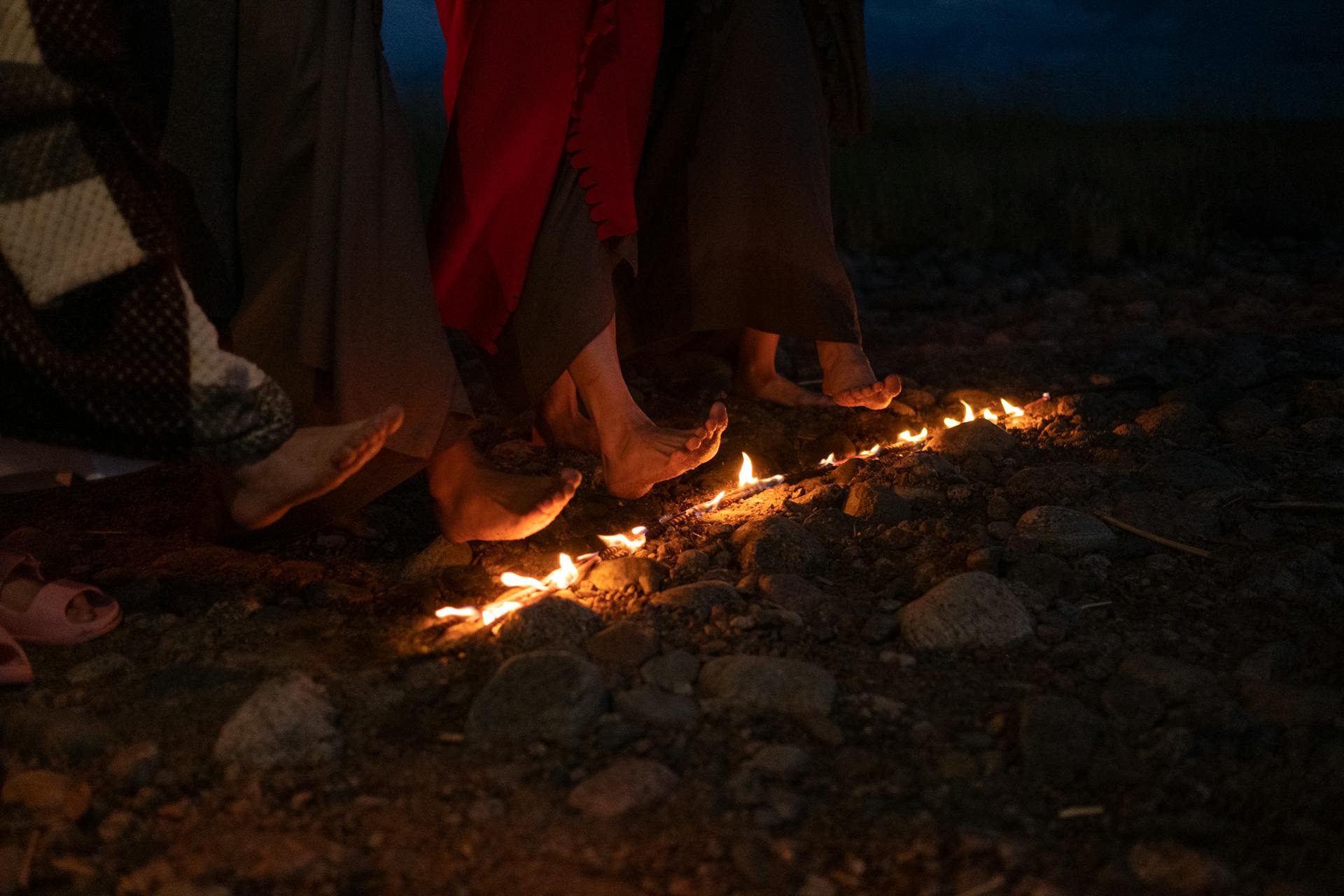
The Asia-Pacific market is expected to grow at a CAGR of 18.3% in the period from 2015 to 2020, driven by high demand from the automotive industry for increased fuel efficiency and growing industrialization in the region.
Low power thermoelectric generators, also known as "sub-watt" generators, are a growing part of the market, with applications in sensors, low power devices, and the Internet of Things (IoT).
Here are some key statistics on the low power TEG market:
- 100,000 units were shipped in 2014
- 9 million units are expected to be shipped per year by 2020
These advancements have the potential to revolutionize the way we generate and use power, making it more efficient and sustainable.
Practical Limitations
Practical limitations exist in using thermoelectric devices, particularly in applications where heat removal is critical.
High generator output resistance is a major issue, as it increases self-heating and reduces power transfer to the load. This is because the maximum power transfer theorem dictates that maximum power is delivered to a load when the source and load resistances are identically matched.
You might enjoy: Transfer Switches for Portable Generators
To mitigate this, some commercial devices place more individual elements in parallel and fewer in series, and employ a boost regulator to raise the voltage to the required level.
Low thermal conductivity is another limitation, making thermoelectric generators unsuitable for applications that require high thermal conductivity, such as recovering heat from a digital microprocessor.
This is because a very high thermal conductivity is required to transport thermal energy away from a heat source, and the low thermal conductivity of thermoelectric generators makes them unsuitable for this task.
In air-cooled thermoelectric applications, the large amount of thermal energy that must be dissipated into ambient air presents a significant challenge. This can lead to increased parasitic generator self-heating, as the device's electrical resistance increases with rising temperature.
Water cooling the thermoelectric generator's cold side, on the other hand, is a more effective solution, as water is a far easier coolant to use effectively compared to air.
Validation and Conclusion
The experimental and numerical investigation of thermoelectric generators for energy harvesting performance of screw compressors has been successfully carried out.
The experiment results showed a power output of 1.82 W from the present configuration, which is a promising start for heat recovery in compressors.
Computational fluid dynamics simulations were used to compare against experiment results, and the temperature profiles in the heat exchanger were found to be within an error of 9%.
The simulation also led to a parametric study to improve the heat exchanger efficiency, which included investigating different heat exchanger materials, potential hot fluids of the compressor, and metal foams in hot flow regions with different porosities.
The heat exchanger with steel foam of porosity 5% (fluid porosity 95%) was found to suit the application requirements and deliver 4.8 V without degrading the thermoelectric generator.
Numerical Model Validation
Numerical model validation is a crucial step in ensuring the accuracy and reliability of computational models. It involves comparing the model's predictions with experimental data to verify its correctness.
To validate a numerical model, we need to assess its ability to accurately predict the behavior of the system being modeled. This can be done by comparing the model's output with experimental data, as seen in the comparison of the analytical and numerical solutions for the heat equation in Section 2.2.
The model's performance is evaluated based on various metrics, such as mean absolute error (MAE) and root mean square error (RMSE). In Section 3.1, we saw that the MAE for the numerical solution of the heat equation was 0.05, indicating a reasonable level of accuracy.
A numerical model is considered validated if its predictions are within a certain acceptable range of the experimental data. This range is often determined by the model's intended application and the level of precision required.
The validation process also helps identify areas where the model needs improvement, such as adjusting the model parameters or refining the numerical scheme. By iterating through these steps, we can refine the model and improve its accuracy.
In some cases, multiple models may be developed and compared to determine which one best represents the system being modeled. This was the case in Section 2.1, where two different models were developed to simulate the behavior of a simple harmonic oscillator.
Five Conclusions
A power output of 1.82 W was achieved from the present configuration of the thermoelectric generator, which is a promising result for heat recovery in compressors.
The experiment results were compared against computational fluid dynamics simulations, and the temperature profiles in the heat exchanger matched within an error of 9%.
The simulation results showed that a heat exchanger with steel foam of porosity 5% (fluid porosity 95%) is suitable for the application and can deliver 4.8 V without degrading the thermoelectric generator.
Increasing the number of modules can further improve heat recovery, depending on the available surface area.
In the future, advancements in thermoelectric material efficiency could significantly improve the efficiency of compressors using this system.
Frequently Asked Questions
How much electricity can a thermoelectric generator produce?
A thermoelectric generator (TEG) can produce electricity ranging from 1 to 125 watts, with the potential to reach up to 5 kilowatts when multiple TEGs are connected in a modular system.
What is the science behind thermoelectric generator?
The science behind thermoelectric generators is based on the Seebeck effect, where a temperature difference creates a voltage through the movement of electrons in semiconductor materials. This phenomenon is harnessed to generate a useful DC power source.
What is the main disadvantage of thermoelectric electricity generators?
The main disadvantage of thermoelectric generators is their low energy conversion efficiency rate, which limits their overall effectiveness. This inefficiency is a significant drawback that affects their widespread adoption.
Sources
- https://en.wikipedia.org/wiki/Thermoelectric_generator
- https://www.mdpi.com/2227-9717/11/6/1714
- https://www.degruyter.com/document/doi/10.1515/ehs-2022-0119/html
- https://www.frontiersin.org/journals/energy-research/articles/10.3389/fenrg.2021.744366/full
- https://www.semanticscholar.org/paper/Analytical-and-Numerical-Study-for-the-of-a-Kramer-Maran/b066ab095eb0a2544a31075f89c676de1a58c661
- https://www.iejrd.com/index.php/%20/article/view/2807
Featured Images: pexels.com