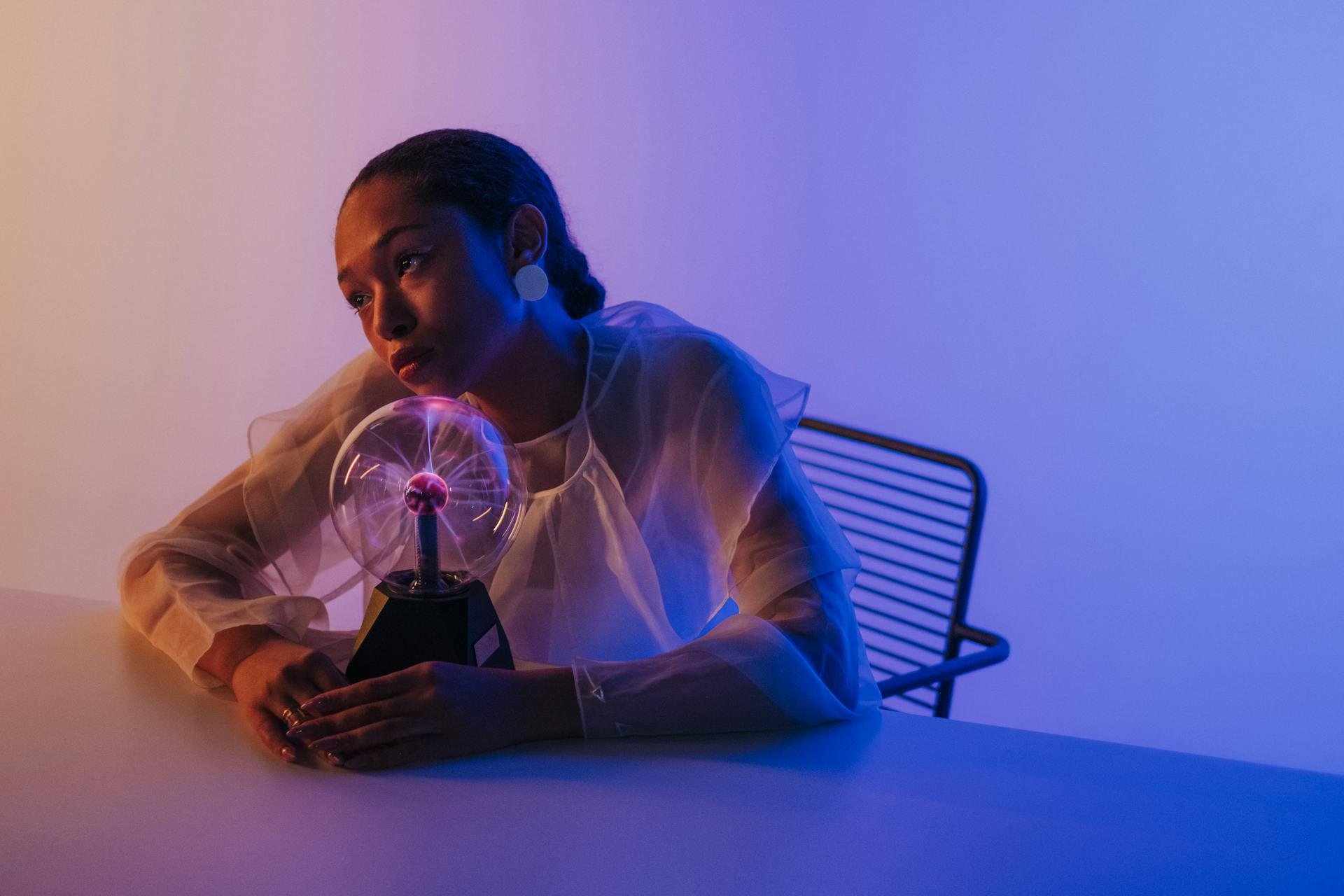
Permanent magnet synchronous generators are a type of generator that uses a permanent magnet as the rotor, which eliminates the need for an excitation winding.
These generators are highly efficient, with an efficiency of up to 98% due to the absence of electrical losses in the rotor.
Their design allows for a compact and lightweight construction, making them ideal for applications where space and weight are limited.
The permanent magnet synchronous generator's design is based on the principles of electromagnetic induction, where a magnetic field is generated in the stator and interacts with the rotor's magnetic field to produce electricity.
For your interest: Asynchronous Vs. Synchronous Generator
Synchronous Generator Working Principle
A synchronous generator works on the principle of a magnetic field produced by a permanent magnet attached to the rotor. This field is essential for converting mechanical energy into electrical energy.
The permanent magnet synchronous generator (PMSG) has two types of windings: armature and field winding. The armature winding is wound on the stator, while the field winding is wound on the rotor.
The stator of the generator has 6 coils of copper windings, which are fixed in their respective places. This is where the magic happens, converting mechanical energy into electrical energy.
The rotor, which has a permanent magnet, is connected to the bearing and rotates on the shaft. There are two rotors in this generator, one behind the stator and the other at the exterior side.
Both rotors are connected to each other through long studs, which move through a hole in the stator. These studs have blades that connect the rotors and help rotate them for the production of electrical energy.
This clever design allows the PMSG to efficiently convert mechanical energy into electrical energy, making it a vital component in many applications.
Worth a look: How Is a Shunt Wound Dc Generator Connected
Modeling and Parameters
The PMSG wind turbine has a maximum power characteristic, where the turbine output power is related to the rotor speed for varying wind speeds, with a maximum obtainable power output of 1.0 pu at 1.0 pu rotational speed.
The mechanical power extracted by the PMSG wind turbine from the wind is expressed as Pw = 0.5 * ρ * R^2 * Vw^3 * Cp, where Pw is the wind power, ρ is the air density, R is the radius, Vw is the wind speed, and Cp is the power coefficient.
The wind generator's power coefficient Cp is related to the ratio of the tip speed (λ) and angle of the pitch (β), as expressed in Eq. 2.
The PMSG differential equations can be obtained by substituting Eqs 7 and 8 into Eqs 5 and 6, and the PMSG active and reactive powers are given as P = 3/2 * (Vsd * Isd + Vsq * Isq) and Q = 3/2 * (Vsd * Isq - Vsq * Isd).
The wind generator electrical torque with number of pole pairs is given as Te = 3/2 * p * (ψsd * Isq - ψsq * Isd), where p is the number of pole pairs, ψsd and ψsq are the flux linkages, and Isd and Isq are the currents in the stator d and q reference frames.
Table 1 shows the parameters of the PMSG wind turbine used for this study.
Description
Synchronous generators are the majority source of commercial electrical energy, converting mechanical power from steam turbines, gas turbines, and hydro turbines into electrical power.
The rotating assembly in the center of the generator, called the rotor, contains the magnet, while the stator is the stationary armature connected to a load.
A set of three conductors make up the armature winding in standard utility equipment, constituting three phases of a power circuit.
The phases are wound such that they are 120° apart spatially on the stator, providing a uniform force or torque on the rotor.
The Permanent Magnet Synchronous Machine block implements a three-phase or a five-phase permanent magnet synchronous machine.
The stator windings are connected in wye to an internal neutral point.
A three-phase machine can have a sinusoidal or trapezoidal back EMF waveform, and the rotor can be round or salient-pole for the sinusoidal machine.
Related reading: Three Phase Ac Generator
Three-Phase Model System
The three-phase model system is a fundamental component of many electrical systems, including synchronous generators and permanent magnet synchronous machines. This system consists of three-phase windings, which are connected in a specific way to create a rotating magnetic field.
The three-phase model system can be expressed in different reference frames, including the rotor reference frame (qd frame) and the phase reference frame (abc frame). In the rotor reference frame, the equations are expressed in terms of the q-axis and d-axis inductances (Lq and Ld), which represent the relation between the phase inductance and the rotor position due to the saliency of the rotor.
The dq inductances are given by Ld = max(Lab)2 and Lq = min(Lab)2 for a salient round rotor. This means that the q-axis inductance is greater than the d-axis inductance, resulting in a rotating magnetic field.
The three-phase model system can also be expressed in terms of the phase-to-phase inductance (Lab), which is given by Lab = Ld + Lq + (Lq - Ld)cos(2θe + π/3). The electrical angle (θe) represents the position of the rotor.
Here's a summary of the key parameters of the three-phase model system:
- Lq and Ld: q-axis and d-axis inductances
- Lab: phase-to-phase inductance
- θe: electrical angle
- ωm: angular velocity of the rotor
These parameters are essential for understanding the behavior of the three-phase model system and for designing and optimizing electrical systems that use this type of model.
Flux Linkage Constant 0.1194
The flux linkage constant 0.1194 is a default value that represents the constant flux λ (Wb) per pole pairs induced in the stator windings by the magnets.
This value is used when the Specify parameter is set to Flux linkage established by magnets (V.s).
The constant flux linkage is a fundamental parameter in modeling and parameters, and understanding its value is crucial for accurate simulations.
In this case, the default value of 0.1194 is a positive scalar that indicates the strength of the magnetic field induced in the stator windings.
This value can be adjusted to suit specific design requirements, but it's essential to note that changing this parameter may affect the overall performance of the system.
Machine Components
A Permanent magnet synchronous generator (PMSG) is made up of several key machine components. The rotor is typically made of a permanent magnet, which provides a constant magnetic field.
The stator is the stationary part of the PMSG, consisting of a set of windings and a core that carries the magnetic field generated by the rotor.
Synchronous Generators
Synchronous Generators are used to provide the power for the excitation of high rating synchronous generators, which is a crucial function in maintaining system voltage during short circuits.
They're also used in power generation systems where wind turbines are involved, which is a great way to harness renewable energy.
In these systems, synchronous generators play a vital role in maintaining the required voltage for the system during short circuits.
Here are some key applications of Permanent Synchronous Generators:
- Powering high rating synchronous generators for excitation
- Maintaining system voltage during short circuits
- Power generation in wind turbine systems
Rotor Type - Round
The Round rotor type is a great option for many applications. It's the default choice for a reason.
In a Round rotor type machine, the stator and rotor are designed to work together seamlessly. This is especially true when the Back EMF waveform is set to Sinusoidal, which is the default option.
To enable the Round rotor type, you'll need to set the Number of phases to 3 and the Back EMF waveform to Sinusoidal. This will give you the best results for your machine.
Readers also liked: Gen Set Generator
One of the key benefits of the Round rotor type is its ability to handle a wide range of speeds. This is thanks in part to the Hall effect signal, which provides a logical indication of the back EMF positioning. This signal is very useful for directly controlling the power switches.
Here's a quick rundown of the key parameters for the Round rotor type:
- Number of phases: 3
- Back EMF waveform: Sinusoidal
- Stator phase inductance Ls: Not applicable (this parameter is only available for the Trapezoidal model)
- Rotor type: Round
By choosing the Round rotor type, you'll be able to take advantage of its many benefits and get the most out of your machine. It's a great choice for anyone looking for a reliable and efficient solution.
Stator Resistance
The stator resistance is a crucial component in any machine, and it's measured in Ohms. It's a positive scalar value that can be adjusted.
In the default setting, the stator phase resistance is 0.0485 Ohms. This value is specific to the machine's design and can affect its overall performance.
To enable stator resistance, you need to set the number of phases to 3, the back EMF waveform to sinusoidal, and the rotor type to salient-pole.
Armature Inductance (H)
Armature inductance is a critical machine component that affects the performance of electric machines. The default armature inductance of the sinusoidal model is 0.000395.
To enable armature inductance, you need to set the Number of phases to 3, Back EMF waveform to Sinusoidal, and Rotor type to Round. This configuration is specific to the sinusoidal model with a round rotor.
The armature inductance of the sinusoidal model is equal to Ld, which is also equal to Lq. This means that the inductance values are identical in this specific configuration.
Brushless DC Motor with Six-Step Inverter
A brushless DC motor fed by a six-step inverter is a great option for applications that require high efficiency and reliability. This type of motor is rated 1kW and operates at 3000 rpm.
The six-step inverter switch-on mode is specifically designed for trapezoidal PMSM motors. This mode provides precise speed regulation.
In this setup, the motor's speed can be adjusted with great accuracy. The six-step inverter ensures a smooth and efficient operation of the motor.
The use of a six-step inverter with a brushless DC motor offers many benefits, including improved efficiency and reduced maintenance.
Here's an interesting read: Seebeck Generator Efficiency
Frequently Asked Questions
What is the working principle of a permanent magnet generator?
The working principle of a permanent magnet generator is based on Faraday's Law of Electromagnetic Induction, which induces an electromotive force (EMF) in a coil when magnetic flux changes. This fundamental principle enables the generation of electricity in a simple and efficient way.
Sources
- https://en.wikipedia.org/wiki/Permanent_magnet_synchronous_generator
- https://medium.com/@zahidmehmood-40074/permanent-magnet-synchronous-generator-the-engineering-knowledge-28b746bc53db
- https://www.mathworks.com/help/sps/powersys/ref/permanentmagnetsynchronousmachine.html
- https://testbook.com/question-answer/in-case-of-permanent-magnet-synchronous-generator--638023edee9ebeab7da27a9d
- https://www.frontiersin.org/journals/energy-research/articles/10.3389/fenrg.2021.655051/full
Featured Images: pexels.com