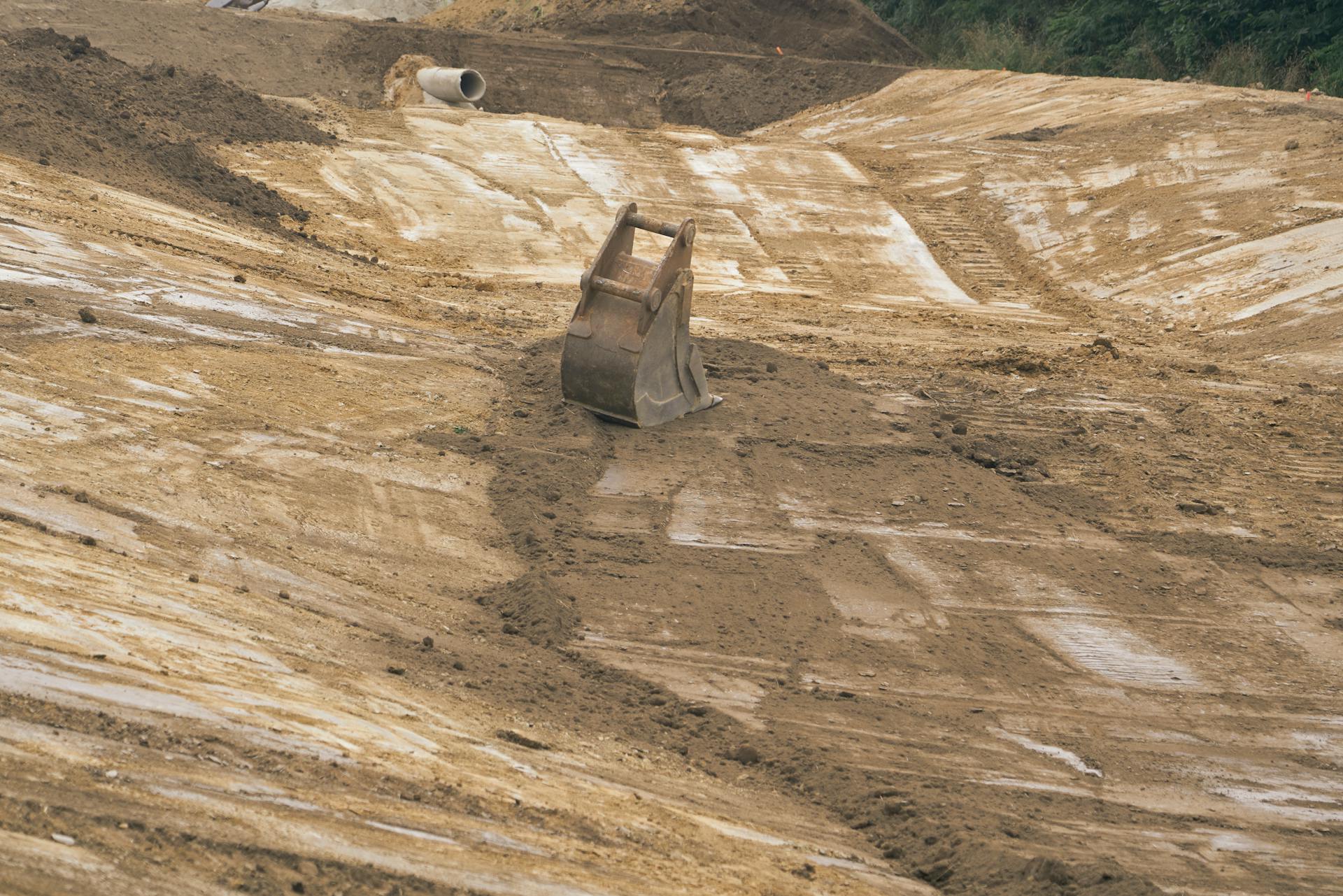
Hydraulic pump systems in excavators are complex, but understanding the basics can help you troubleshoot issues and make informed decisions when purchasing or maintaining your equipment.
A hydraulic pump is the heart of an excavator's system, converting mechanical energy into hydraulic energy. It's typically driven by the engine's crankshaft, which powers the pump's pistons.
The pump's performance is crucial to an excavator's overall efficiency and productivity. A high-quality pump can make a significant difference in the machine's performance.
In an excavator, the hydraulic pump system is responsible for powering the machine's various functions, including the boom, stick, and bucket.
See what others are reading: Excavating Machine
Pump Components and Functionality
A hydraulic pump in an excavator is a crucial component that converts mechanical energy into hydraulic energy. It's essentially a device that pumps fluid through the system to generate power.
The pump's driving force comes from a prime mover, such as an electric motor or internal combustion engine, which drives the impeller, gear, or vane to create a flow of fluid within the pump's housing.
Broaden your view: Excavator Hydraulic Fluid
A hydraulic pump operates on positive displacement, where a confined fluid is subjected to pressure using a reciprocating or rotary action. This creates a vacuum at the pump's inlet, allowing atmospheric pressure to force fluid into the pump.
The different types of pumps, including gear, vane, and piston pumps, utilize various mechanisms to create fluid flow and pressure. For example, a gear pump uses two meshing gears that rotate in opposite directions, creating chambers that expand and contract, generating fluid flow and pressure.
Here's a breakdown of the main types of hydraulic pumps used in excavators:
The performance of a hydraulic pump is determined by the size and shape of the pump's internal chambers, the speed at which the pump operates, and the power supplied to the pump.
Types of Pumps and Systems
Excavators utilize a variety of hydraulic pump types, each with its own unique characteristics and applications.
Gear pumps are one of the most widely used hydraulic pump types in excavators, known for their simplicity, reliability, and cost-effectiveness. They use the meshing of two gears to draw in and pressurize the hydraulic fluid.
Consider reading: Types of Tower Cranes
Piston pumps, particularly axial piston pumps, are popular in larger and more powerful excavators, using a series of reciprocating pistons to create the hydraulic pressure.
Vane pumps are another common type of hydraulic pump found in excavators, using a rotor with sliding vanes to draw in and pressurize the hydraulic fluid. They are known for their compact design, high volumetric efficiency, and relatively low noise levels.
Screw pumps, also known as rotary positive displacement pumps, are less common in excavators but are sometimes used in specialized applications. They use a pair of intermeshing helical screws to create the hydraulic pressure.
Here are the main hydraulic pump types used in excavators:
How Systems Work
Hydraulic systems are a type of mechanical design used in equipment manufacturing to provide lift, reach, tilt, and other functions the equipment needs. They operate based on the principle of fluid pressure flowing through a closed-loop circuit.
The machine contains a reservoir of hydraulic oil that gets pumped through a valve and into the cylinder of the hydraulic component it powers. The pressure of the fluid being pumped toward the cylinder forces the component to move.
Hydraulic systems work by using a transfer of force from one point to another through the movement of fluid. This is why they're capable of lifting heavier loads at greater force.
A hydraulic pump operates on positive displacement, where a confined fluid is subjected to pressure using a reciprocating or rotary action. The pump's driving force is supplied by a prime mover, such as an electric motor, internal combustion engine, human labor, or compressed air.
There are different types of pumps, including gear, vane, and piston pumps. Each type utilizes a different mechanism to create fluid flow and pressure.
Here are the key differences between gear, vane, and piston pumps:
- Gear pump: Two meshing gears rotate in opposite directions, creating chambers that expand and contract, generating fluid flow and pressure.
- Vane pump: Vanes are pushed outwards by centrifugal force and pushed back into the rotor as they move past the pump inlet and outlet, generating fluid flow and pressure.
- Piston pump: A piston is moved back and forth within a cylinder, creating chambers of varying size that draw in and compress fluid, generating fluid flow and pressure.
A hydraulic pump's performance is determined by the size and shape of the pump's internal chambers, the speed at which the pump operates, and the power supplied to the pump.
Types of Pumps
Let's talk about the different types of pumps. There are several types of hydraulic pumps, each with its own unique characteristics and applications.
A hydraulic pump's main function is to create pressure, which is essential for heavy machinery like excavators. Gear pumps, for example, use the meshing of two gears to draw in and pressurize the hydraulic fluid, making them well-suited for a range of excavator applications.
Piston pumps, particularly axial piston pumps, are popular in larger and more powerful excavators. They use a series of reciprocating pistons to create the hydraulic pressure, allowing for higher flow rates and pressures compared to gear pumps.
Vane pumps are another common type of hydraulic pump found in excavators. They use a rotor with sliding vanes to draw in and pressurize the hydraulic fluid, and are known for their compact design and high volumetric efficiency.
Screw pumps, also known as rotary positive displacement pumps, use a pair of intermeshing helical screws to create the hydraulic pressure. They're less common in excavators but are sometimes used in specialized applications where high flow rates are required.
Here's a quick rundown of the main types of hydraulic pumps:
The selection of the appropriate hydraulic pump type depends on factors such as the machine's size, power requirements, operating conditions, and specific application needs.
Two-Stage Pump
A two-stage pump is a type of hydraulic pump that uses two stages to achieve high pressure levels.
It works by drawing fluid from a reservoir into a high volume, large-gear unit, which elevates the gear housing's pressure level.
Once the first-stage pressure meets a certain threshold, a combiner check valve opens and feeds into the second-stage, small-gear unit, joining flows at relatively low pressure.
The load sensing pin triggers the unloading valve to open and the check valve to close, directing the flow exclusively to the discharge port.
A small amount of fluid may feedback to the load sensing pin to measure the pressure at the outlet and signal lower flow rate in the first unit, allowing the cycle to repeat.
This process allows the two-stage pump to alternate between units, making it a versatile and efficient option for hydraulic systems.
Common Applications
Hydraulic pumps are used in a variety of industries, including the automotive industry, where they're combined with jacks and engine hoists for lifting vehicles and heavy loads.
In mechanical workshops, hydraulic pumps power tools for tasks like cutting, drilling, and pressing. They're also used in wood workshops for powering hydraulic jacks in splitters.
Heavy-duty hydraulic pumps are used in process and manufacturing for driving and tapping applications, as well as turning heavy valves and tightening or expanding objects. This requires a lot of power, which hydraulic pumps can provide.
Hydraulic pumps are also used in heavy machinery like excavators, cranes, loaders, and tractors. They're also used in production facilities for powering conveyors, mixers, and forklifts.
Here are some of the key applications of hydraulic pumps:
- Automotive industry: lifting vehicles and heavy loads
- Mechanical workshops: powering tools for cutting, drilling, and pressing
- Wood workshops: powering hydraulic jacks in splitters
- Process and manufacturing: driving and tapping applications, turning heavy valves, tightening and expanding objects
- Heavy machinery: excavators, cranes, loaders, and tractors
- Production facilities: conveyors, mixers, and forklifts
Frequently Asked Questions
How does the hydraulic system work on an excavator?
An excavator's hydraulic system uses a double-acting system, where oil is pumped on both sides of the piston to move it in two directions. This allows for smooth and efficient movement of the excavator's arms and attachments.
How does a hydraulic pump work step by step?
Here's a concise FAQ answer: "A hydraulic pump works by creating a partial vacuum at the inlet, drawing in fluid, and then forcing it out as the gear teeth mesh, resulting in a smooth and efficient flow. This process allows for high volumetric efficiencies, reaching up to 93% under optimal conditions
Sources
- https://www.gregorypoole.com/complete-guide-to-construction-equipment-hydraulic-systems/
- https://www.panagonsystems.com/hydraulic-pumps-and-motors-in-action/
- https://tameson.com/pages/hydraulic-pump
- https://www.panagonsystems.com/how-does-a-2-stage-hydraulic-pump-work/
- https://www.kpdiesel.com/unleashing-the-power-a-comprehensive-guide-to-excavator-hydraulic-pumps/
Featured Images: pexels.com