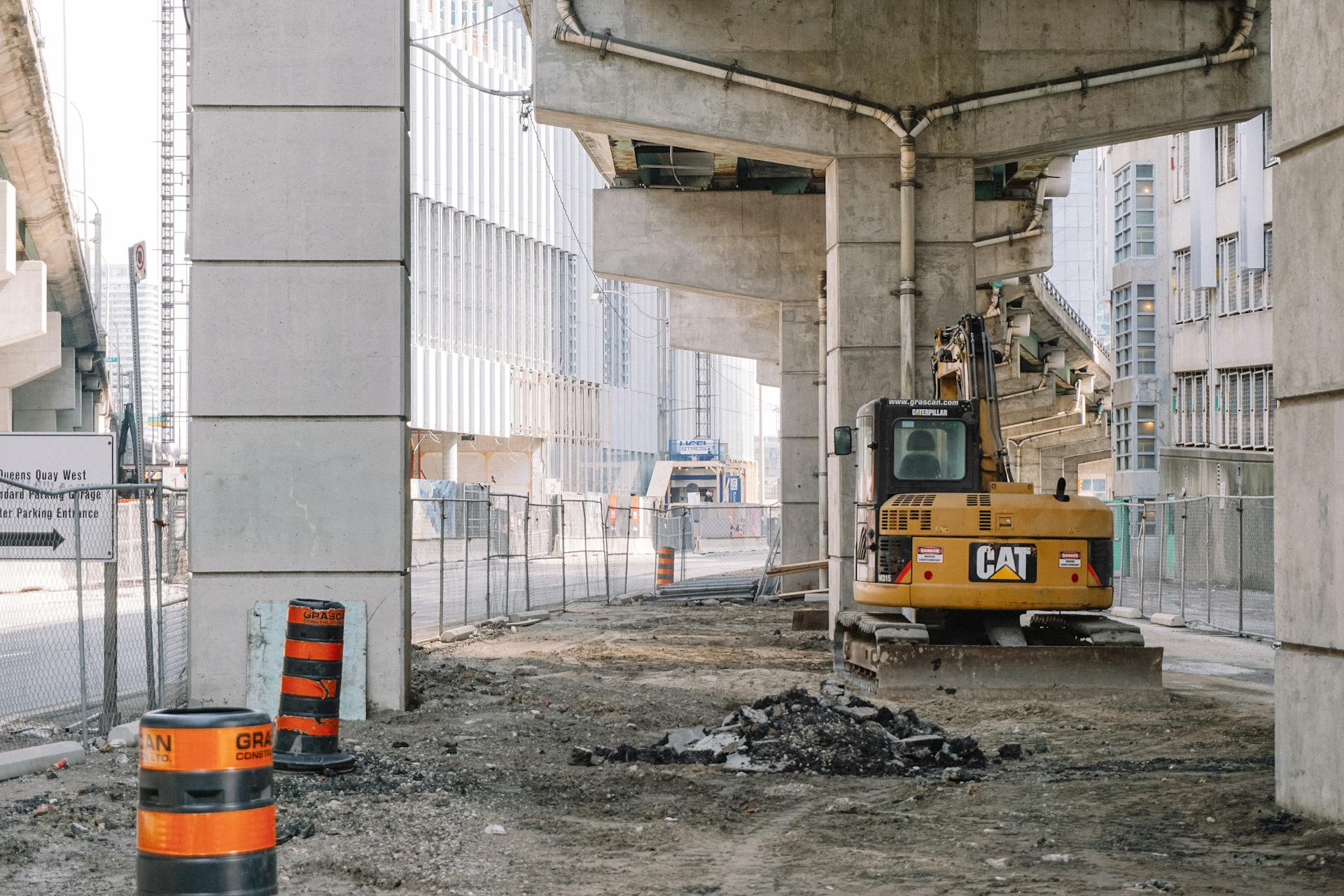
Choosing the right hydraulic fluid for your excavator is crucial for its performance and longevity. The fluid's viscosity index is a key factor, with a higher index indicating better performance in extreme temperatures.
Excavators that operate in cold temperatures require hydraulic fluids with a lower viscosity index, such as those with a -30°C pour point. This ensures the fluid remains fluid and doesn't thicken, which can cause damage to the excavator's hydraulic system.
Regular maintenance of the hydraulic fluid is essential to prevent damage and extend the life of the excavator. This includes checking the fluid's level, color, and consistency on a regular basis.
Choosing the Right Fluid
Choosing the right hydraulic fluid for your excavator is crucial for its normal operation and reliability. Using the wrong fluid can lead to hydraulic issues, increased heat, wear, oxidation, and sludge buildup.
To choose the right fluid, consider the minimum permissible and optimum viscosity values for your hydraulic components. For example, a radial piston component requires a minimum viscosity of 18 cSt and an optimum viscosity of 30 cSt.
The type of hydraulic oil you choose also matters. Biodegradable hydraulic oils, made from natural and non-toxic components like soybean, rapeseed, and sunflower seeds, offer excellent high viscosity index, lubrication, oxidation resistance, and anti-wear properties.
Here's a quick reference table to help you choose the right fluid for your excavator's components:
Types of Hydraulic Fluid
Choosing the right type of hydraulic fluid is crucial for the normal operation and reliability of excavators. Excavator hydraulic fluid types vary, each with distinct characteristics and advantages.
Synthetic oil is a great option for machinery operating under extreme temperatures or high pressures. It has a longer lifespan and superior lubrication performance.
Fire-resistant fluids are designed to prevent fires in extreme conditions. They typically consist of a combination of water, ethylene glycol, and polyol esters.
Biodegradable hydraulic oil is an environmentally friendly alternative to mineral oil. It's usually made from natural, non-toxic components like soybean, rapeseed, and sunflower seeds.
Curious to learn more? Check out: Excavator Hydraulic Oil
Synthetic vs. Conventional
When choosing between synthetic and conventional fluids, it's essential to consider their unique characteristics. Synthetic fluids offer superior performance in extreme temperatures, with a viscosity index of 150 or higher, compared to conventional fluids which typically have a viscosity index of 100 or lower.
Synthetic fluids are designed to provide better lubrication and wear protection in high-temperature applications. They also have a higher flash point, making them safer to use in environments where sparks are a concern.
Conventional fluids, on the other hand, are generally less expensive and more readily available. However, they may not provide the same level of performance as synthetic fluids in extreme temperatures.
Synthetic fluids can withstand temperatures up to 300°F, while conventional fluids typically break down and lose their lubricating properties at temperatures above 250°F.
Fluid Maintenance and Checks
Fluid maintenance is crucial for the longevity and performance of your mini excavator. Regular checks can help prevent damage from low levels affecting functions.
The ideal time to check fluid levels is after the machine has cooled down, allowing for an accurate reading. This usually takes 15-20 minutes after shutting off the engine.
You'll want to use the sight gauge or dipstick to check the fluid level, ensuring it falls within the minimum and maximum fill lines. If it's below the minimum point, it's time to top it up.
Before topping off, inspect the existing hydraulic oil for any signs of contamination, such as discoloration or particles. If you find any, it's best to drain and flush the system instead of risking further damage.
To check the fluid level, open the reservoir cap and pull out the dipstick. Wipe it clean with a rag and check the fluid level between the 'Full' and 'Low' marks. If it's low, add the recommended fluid through the reservoir opening slowly.
It's essential to maintain optimal fluid levels indicated on the dipstick. Frequent top-ups may indicate hydraulic leaks that must be addressed to prevent fluid loss and equipment damage over time.
Here's a quick checklist for refilling and maintaining fluid levels:
- Only use the recommended fluid type for your excavator model.
- Clean the area around the reservoir opening before unscrewing to prevent contamination.
- Slowly add fluid through a clean funnel or directly using a cleaned bottle to avoid overflow or aeration.
- Allow 10 minutes for settling, and check the level as specified when the fluid is warm.
- Top up if needed, and tightly close the reservoir cap after refilling to prevent fluid loss or dirt infiltration.
Regular fluid checks can help prevent damage, catch minor issues before they escalate, and indicate leaks and maintenance needs. It's recommended to inspect fluid levels weekly and perform related maintenance monthly or as specified in the manual.
Understanding Fluid Performance
Hydraulic fluid plays a crucial role in the performance of your excavator, and understanding its properties is key to optimal operation.
Anti-wear additives in hydraulic oil form a protective film on metal surfaces, reducing wear and friction. This is especially important for hydraulic components like cylinders, which can experience high levels of wear and tear.
The viscosity of hydraulic oil is closely related to temperature changes, increasing with decreasing temperature and vice versa. Choosing the right viscosity is crucial for lubricating internal components and maintaining effective thickness at low temperatures.
Hydraulic oil with good thermal stability is essential for withstanding high-temperature environments without premature degradation or the formation of deposits. This will help maintain the stability of the oil and prevent compromises to the hydraulic system.
Viscosity and Density
Viscosity and Density are two crucial properties of hydraulic oil that affect its performance. Viscosity refers to the oil's flow resistance or thickness, which increases with decreasing temperature and vice versa.
Choosing the correct viscosity is vital for lubricating internal components and maintaining effective thickness at low temperatures. This is because the viscosity of hydraulic oil directly impacts its ability to flow and perform under different conditions.
The density of hydraulic oil, typically ranging from 800 kg/m³ to 1000 kg/m³, affects the mass and volume of the liquid in the hydraulic system. This, in turn, influences the working pressure and flow rate of the system.
Higher density oils can suspend and remove contaminants, enhancing contamination control in the hydraulic system. For example, common mineral oil hydraulic oils usually have densities ranging from 850 kg/m³ to 900 kg/m³.
To choose the right hydraulic oil viscosity or grade, consider the following factors:
- Starting viscosity at minimum ambient temperature
- Maximum expected operating temperature, influenced by maximum ambient temperature
- Permissible and optimum viscosity range for the system's components
Here's a quick reference guide to typical minimum viscosity values for different types of hydraulic components:
Anti-Wear Performance and Thermal Stability
Hydraulic oil contains additives that enhance its performance, such as phosphates, sulfides, and zinc compounds, which can form a protective film on metal surfaces, reducing direct metal-to-metal contact and minimizing wear and friction.
These additives are crucial in preventing premature wear and tear on hydraulic systems, which can lead to costly repairs and downtime.
Phosphates, sulfides, and zinc compounds are common anti-wear additives found in hydraulic oil, and they play a vital role in maintaining the overall performance and longevity of hydraulic systems.
Hydraulic systems often operate at elevated temperatures, and hydraulic oil needs to withstand these high-temperature environments without premature degradation, oxidation, or the formation of deposits.
If hydraulic oil is not thermally stable, it can compromise the stability of the system, leading to reduced performance and potentially catastrophic failures.
Good thermal stability in hydraulic oil is essential for maintaining the health and performance of hydraulic systems, especially in high-temperature applications.
Troubleshooting and Best Practices
Catching issues early allows simple troubleshooting, which is crucial for extending the life of your excavator's hydraulic system. This means regularly checking the fluid level and looking for signs of leaks or contamination.
Inspect your pump, pipes, and valves for leaks or issues causing overheating, as this can lead to costly damage. If you notice a burnt smell, it's likely due to overheating from leaks or restricted flow.
To prevent costly repairs, it's essential to address issues promptly, such as draining and flushing the system if you notice cloudy or contaminated fluid. Regularly replacing filters and fluid can also help prevent problems.
Identifying Deterioration and Common Issues
Identifying deterioration in hydraulic fluid is crucial to prevent expensive damage.
Cloudy or contaminated fluid is a clear indicator of deterioration, which can be resolved by draining the system, flushing clean, and replacing filters and fluid.
Low fluid level is another common issue, easily fixed by topping up with the recommended fluid and finding and fixing leaks causing loss.
Overheated fluid can be caused by leaks or issues with the pump, pipes, and valves, and should be addressed immediately.
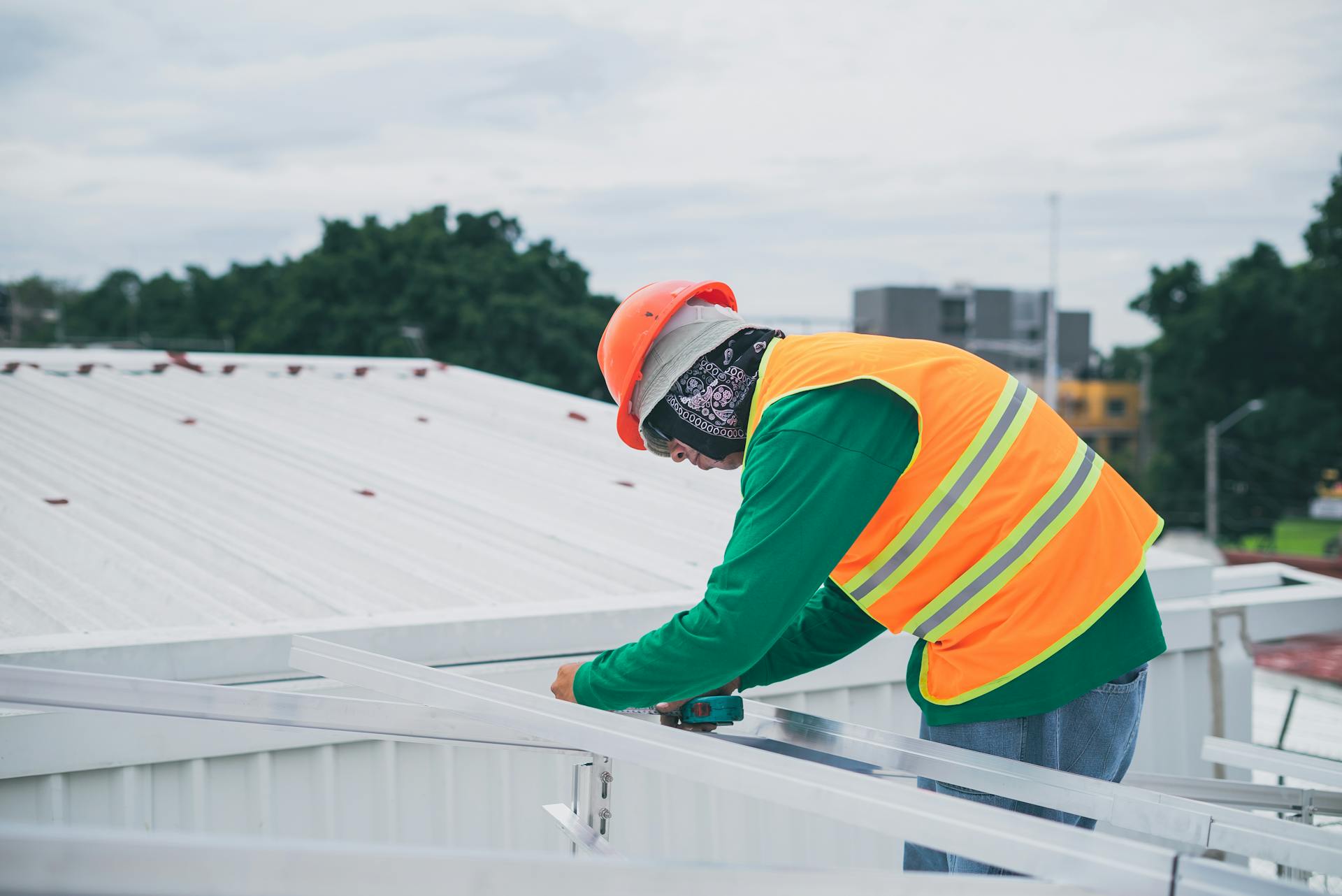
Water in the fluid requires draining, flushing, and replacing the fluid and filters, along with finding and rectifying the source of water ingress.
A burnt smell usually indicates overheating from leaks or restricted flow, and should be inspected for damage before flushing the system.
Noisy pump/motors may be a sign of fluid breakdown or air in the lines, so it's essential to check the fluid and reservoir cap, and replace filters and bleed lines if needed.
Sluggish cylinder action can be caused by fluid breakdown, low levels, leaks, or a dirty filter, and should be addressed by replacing filters or flushing the system if sluggishness persists after refilling.
Catching issues early allows for simple troubleshooting, whereas neglecting problems can lead to damage to expensive components, requiring repairs or part replacement.
Mistakes to Avoid and OEM Recommendations
Avoiding mistakes is crucial when it comes to maintaining your equipment. Overfilling hydraulic fluid can cause foaming and system damage.
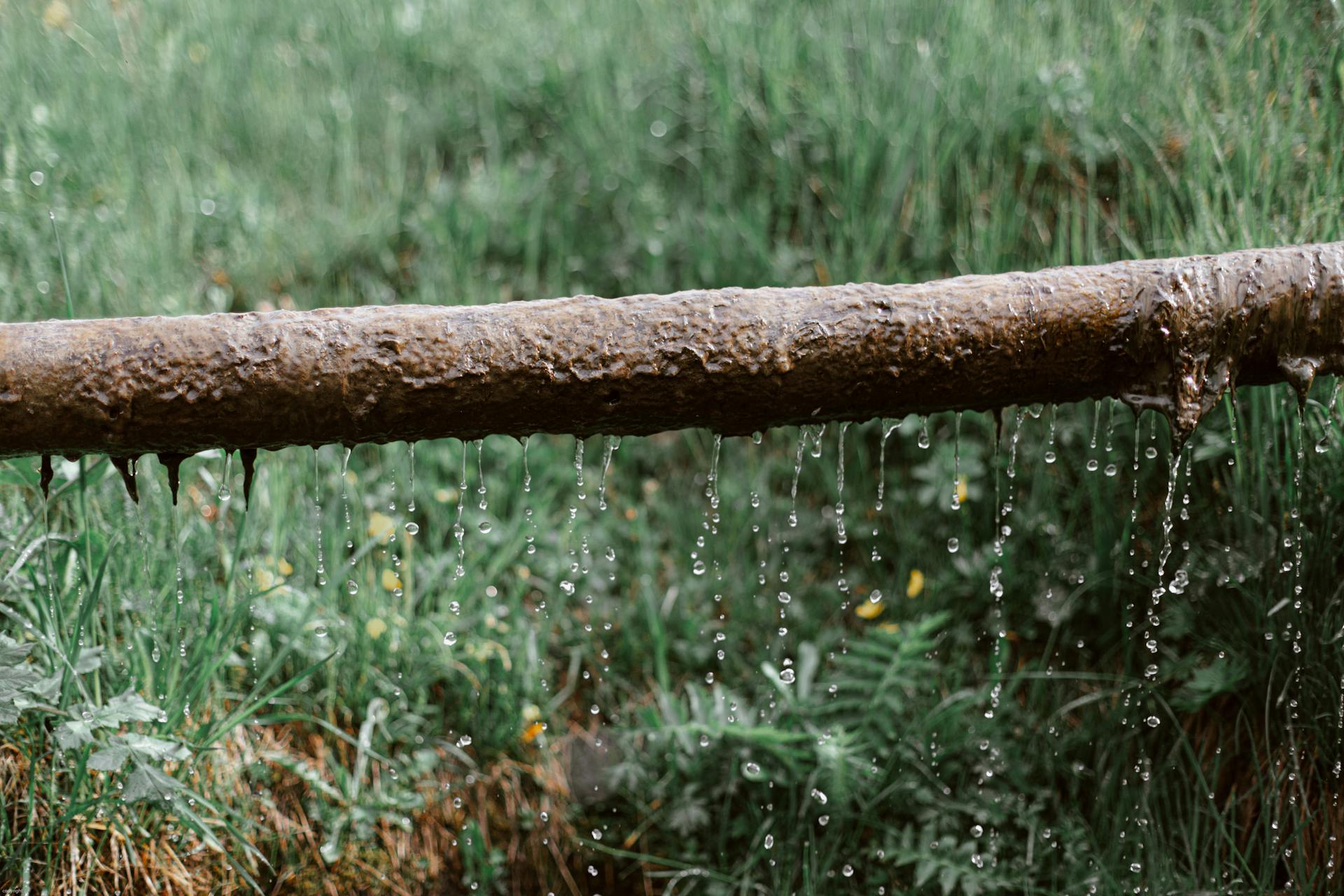
Using the wrong type of fluid is a common error, and it's essential to always use the manufacturer-recommended oil. This will ensure accurate readings and proper maintenance.
Checking hydraulic fluid on uneven ground can lead to false readings, so make sure to check it on a level surface. Dirt entering the system can cause significant problems, so neglecting to clean the area is a mistake to avoid.
Ignoring small leaks is also a mistake, as it can lead to system failure. Address any leaks promptly to prevent damage.
Here are some common mistakes to avoid when checking hydraulic fluid:
- Checking on uneven ground
- Overfilling
- Using the wrong type of fluid
- Neglecting to clean the area
- Ignoring small leaks
It's also a good idea to review the OEM's specifications, as they may have warranty-related reasons for following their recommendations. If you're unsure, it's best to consult with a technical specialist.
Frequently Asked Questions
Should I use 46 or 68 hydraulic oil?
Choose hydraulic oil #46 for low winter temperatures and #68 for warmer summer temperatures. Select the viscosity that matches your climate for optimal performance
Sources
- https://www.fridayparts.com/blog/excavator-hydraulic-fluid-101
- https://ahmcorp.com/blogs/news/how-to-add-hydraulic-fluid-to-excavator
- https://www.boleous.com/blog/how-to-check-hydraulic-fluid-on-mini-excavator/
- https://ahmcorp.com/blogs/news/how-to-check-hydraulic-oil-level-on-excavator
- https://www.machinerylubrication.com/Read/702/how-to-choose-right-hydraulic-fluid-oil
Featured Images: pexels.com