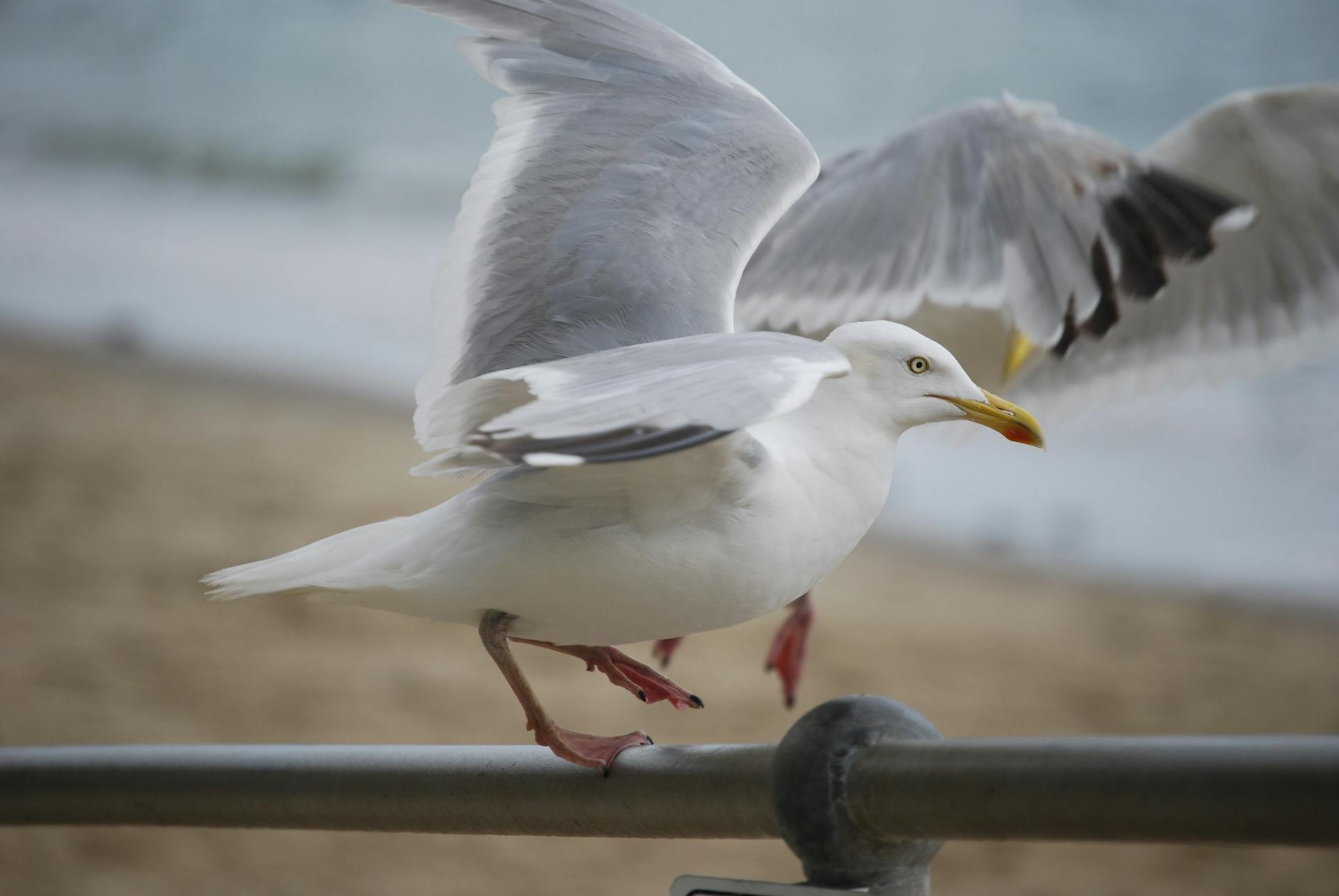
A free piston engine linear generator is a type of engine that can be used in hybrid electric vehicles.
This technology has the potential to improve fuel efficiency and reduce emissions in vehicles.
A free piston engine linear generator is essentially a linear electric generator that uses a free piston engine to generate electricity.
The free piston engine is a type of engine that uses a piston without a traditional crankshaft, allowing for a more efficient conversion of energy into electricity.
In a hybrid electric vehicle, the free piston engine linear generator can be used to charge the vehicle's battery, reducing the need for a traditional gasoline engine.
The free piston engine linear generator can also be used to generate electricity while the vehicle is stationary, such as at a stoplight or in traffic.
You might enjoy: Direct Current Electric Generator
Research and Development
Toyota's R&D team has been working on improving the free piston linear generator, a technology that generates electricity directly from the motion of a piston. This innovative approach is different from traditional internal combustion engines (ICEs).
Expand your knowledge: Free Piston Linear Alternator
The team's prototype FPEG was presented to the SAE in 2014. They have since developed a new control method that enhances the stability and flexibility of the piston motion control.
A traditional ICE propels a drive shaft, whereas a free piston engine linear generator (FPEG) converts kinetic energy to electrical energy using magnets attached to the piston moving within a linear coil. This process generates electricity directly.
The Toyota researchers encountered technical challenges when trying to achieve continuous operation over a long period. The piston motion control is a significant factor in improving the robustness and efficiency of the FPEG.
The team developed a target position feedback control method, which worked well at low power but struggled to maintain the piston swing motion at higher output powers. To address this issue, they created the "resonant pendulum" control method.
Linear Generator
The linear generator is a crucial component of the FPEG prototype, playing multiple roles in its operation. It can operate as a motor, generator, or motor for the four-stroke engine during start-up and non-power stroke.
If this caught your attention, see: Homopolar Motor Generator
A linear electric machine is used in the FPEG prototype, offering several functions. It can operate as a motor during start-up and drive the piston up to the required compression ratio for ignition, as well as operate as a generator to produce electricity during stable operation.
The current availability of commercial linear motors in the 10 s kWe size is limited, with most designed for smaller-scale process engineering and manufacturing applications rather than specifically for electricity generation. A Moog Model 50204D linear motor was adopted due to its high power density and ability to provide sufficient force during the starting process.
The motor drive used is the Parker model Compax3H, which requires configuration using C3 Manager Software via a RS232 connection to a master control computer.
Take a look at this: Ac Generator Motor
Prototype Details
The FPEG prototype specifications vary between different examples, but some key details are consistent. The cylinder bore is typically around 50-60 mm, with a maximum stroke of 40-60 mm. The moving mass is around 1.5-7 kg, depending on the design.
The maximum intake and exhaust valve lift is usually around 4-5 mm. The intake and exhaust valve diameters are also consistent, ranging from 15-20 mm.
A key feature of the FPEG is its ability to operate at high speeds, with operational speeds ranging from 5-15 Hz. This is made possible by the use of a compact and efficient design.
Here are the detailed specifications of the FPEG prototype:
The FPEG prototype also features a comprehensive control system, including a CompactRIO system by National Instruments and a bespoke injection control algorithm developed in LabVIEW. This allows for precise control over the engine's operation and enables real-time measurement of in-cylinder pressure.
System Components
A free piston engine linear generator is made up of several key components that work together to produce electricity.
The engine block is a crucial component, as it houses the moving parts of the engine, including the piston and connecting rod.
The linear generator is essentially a motor that converts the back-and-forth motion of the piston into electrical energy.
The power take-off (PTO) is responsible for extracting the electrical energy from the generator and sending it to a load, such as a battery or the electrical grid.
The control system is used to regulate the engine speed and optimize the power output of the generator.
The control system is also responsible for monitoring the engine's performance and detecting any potential issues.
The engine's efficiency is improved by using a high-stroke, low-frequency design, which allows for more energy to be extracted from the engine's motion.
The free piston design eliminates the need for a traditional crankshaft and camshaft, reducing the engine's overall weight and size.
A unique perspective: Generators Create Electrical Energy.
Base Operational Case
In a base operational case, the free piston engine linear generator is designed to operate at a constant speed of 1000 RPM. This speed is crucial for efficient energy conversion.
The engine's stroke frequency is directly related to the speed, and at 1000 RPM, the stroke frequency is 100 Hz. This frequency is essential for optimal generator performance.
The base operational case assumes a constant load of 10 kW, which is a typical value for residential applications. This load is sufficient to power a small household.
The engine's displacement volume is 1.5 liters, and at 1000 RPM, the engine's power output is approximately 15 kW. This power output is higher than the assumed load, allowing for some reserve capacity.
The generator's efficiency is around 90%, which means that 90% of the engine's power output is converted into electrical energy. This efficiency is a significant factor in the overall performance of the free piston engine linear generator.
For your interest: Seebeck Generator Efficiency
Timing and Control
Advancing the spark ignition timing from −16.0 to 2.0 ms aTDC significantly impacted the dynamic performance of a FPEG.
The mean value or cycle is presented, but unfortunately, noisy data at around −4.0 ms aTDC was not able to be processed in full.
As spark timing was advanced, the timing and magnitude of peak pressure were also advanced and increased, respectively.
Spark Ignition Timing
Spark ignition timing is a crucial parameter in engine performance, and it's been extensively studied in the context of FPEG engines. The spark ignition timing was varied from −16.0 to 2.0 ms aTDC.
Advanced spark timing generally increased the indicated power, indicated efficiency, and iMEP, with maximum values achieved at around −13.0 ms aTDC. This corresponded to 0.7 kWe at 26% indicated efficiency.
However, later ignition times resulted in lower efficiencies due to the exhaust opening time being fixed. This meant that the engine had less time to scavenge the burned gases before the valve was opened.
Interestingly, no knocking combustion events were observed, even with more advanced spark timings. This suggests that the engine's design and operation allowed for efficient combustion under a wide range of spark timing settings.
The spark ignition timing sweep also showed a linear trend in engine performance parameters, indicating the potential for optimizing performance through manipulation of the timing of combustion.
Exhaust Valve Timing
A sweep of exhaust valve opening times was carried out, with the open duration fixed to 0.038 seconds. This revealed that outside a certain operating window, combustion was irregular and couldn't be sustained.
The results showed that delaying the exhaust valve opening control parameter generally resulted in higher in-cylinder pressures. However, this did not affect the timing of peak pressures.
The changes to exhaust valve time yielded only minor differences to the observed performance parameters, such as power and efficiency. The prototype proved highly sensitive to the scavenging process.
Frequently Asked Questions
Are free-piston engines still used?
Yes, free-piston engines are still used in modern applications, including hydraulic engines for off-highway vehicles and free-piston engine generators for hybrid electric vehicles. They continue to be developed for various uses due to their potential efficiency and performance benefits.
How does a linear generator work?
A linear generator converts linear motion into electric energy by using magnets driven through a stator. This process harnesses chemical energy from fuel to produce electricity.
Sources
- https://www.wikiwand.com/en/articles/Free-piston_linear_generator
- https://www.sciencepublishinggroup.com/article/10060800
- https://newatlas.com/dlr-free-piston-linear-generator-range-extender/27736/
- https://chargedevs.com/newswire/toyota-rd-team-improves-free-piston-linear-generators/
- https://www.ncbi.nlm.nih.gov/pmc/articles/PMC7587148/
Featured Images: pexels.com