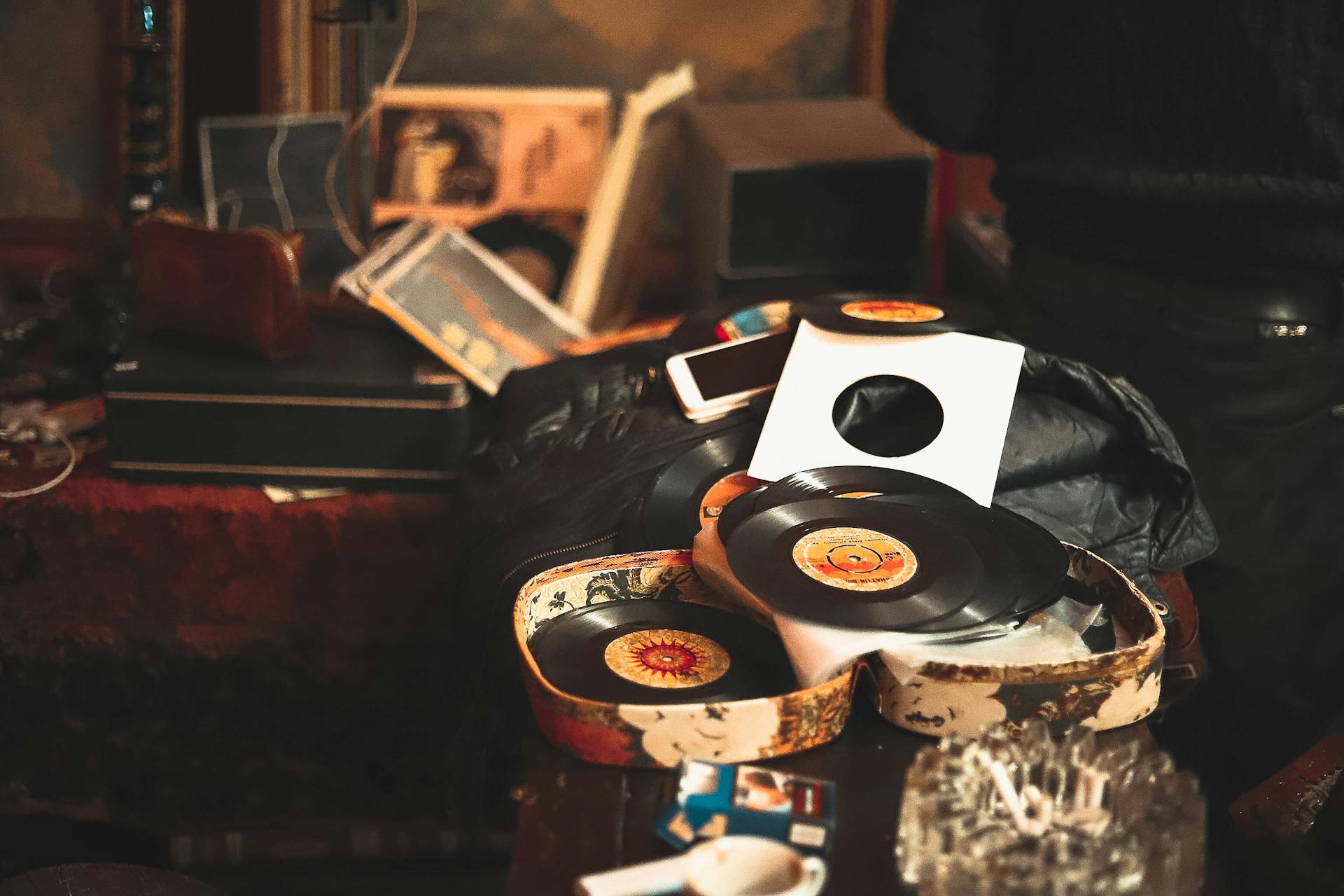
Batch records are an important part of the documentation process in the pharmaceutical manufacturing industry. They are true documentation of what happened during a specific batch manufacturing process. Maintaining complete and accurate BMRs is crucial for drug administration compliance organizations to ensure that everything that needed to happen during production happened, and what didn't happen was not supposed to happen.
Not having proper systems in place or not following current good manufacturing practice (cGMP) regulations when creating batch records can have serious consequences. It's important to understand exactly what should be included in these records and how they should be maintained. In this comprehensive guide, we will delve into the ins and outs of understanding batch records. So, if you're not happy with your batch manufacturing processes or want to ensure your BMRs are up-to-date, keep reading! And if your download didn't start, click on this link for access to the full guide.
For more insights, see: Discrete vs Process Manufacturing
The Significance of Batch Records: A Comprehensive Guide
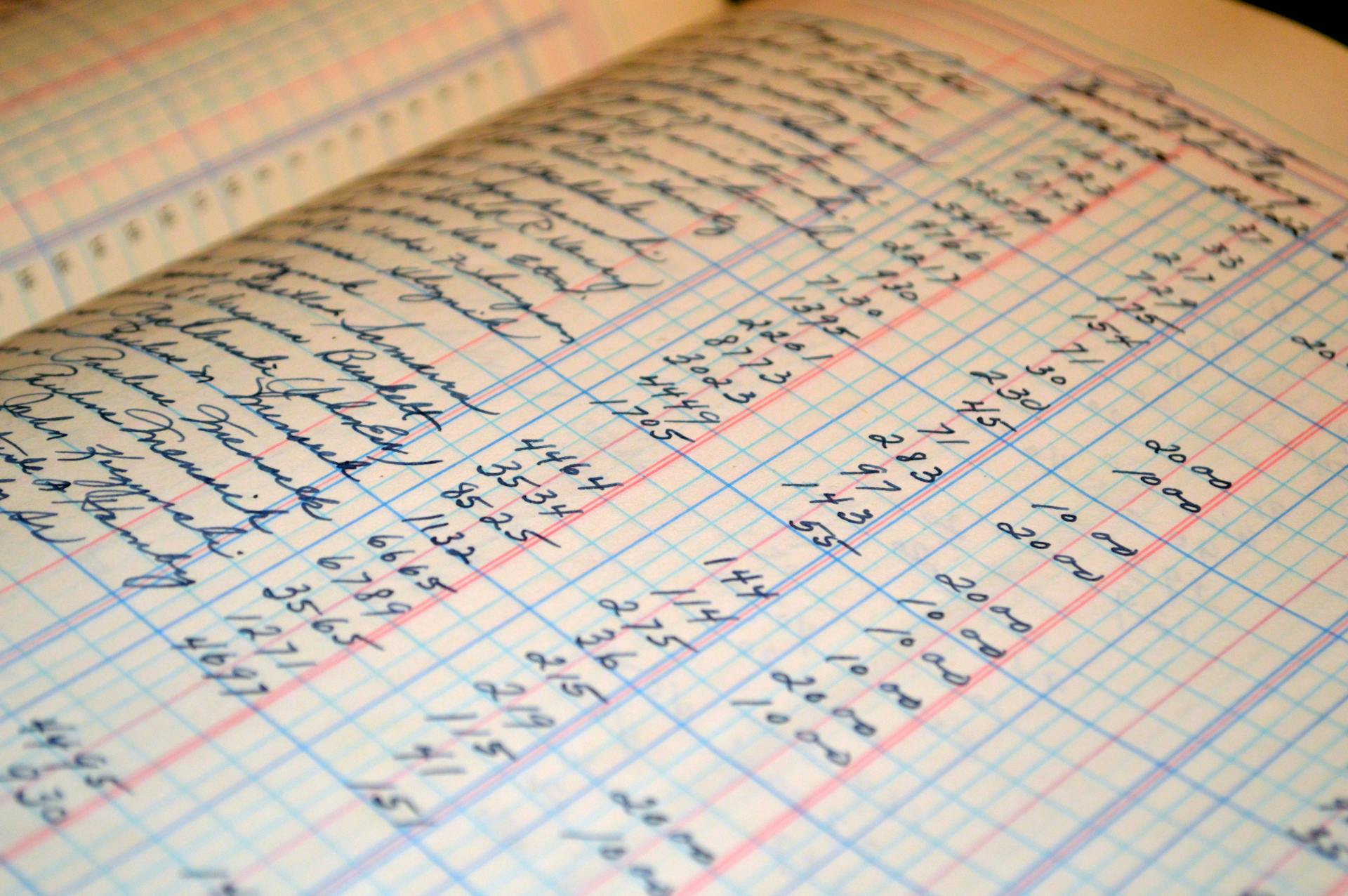
Batch records are essential documents in pharmaceutical manufacturing that provide critical information about each specific quantity of a drug produced. These records include details about the uniform character, active ingredient strength, and other specifications for each batch. A single manufacturing order can produce 100000 pills or more, and it is important to keep track of all necessary information throughout the entire production process.
Batch records are crucial for ensuring product quality and safety. They provide a complete record of every step taken during the manufacturing process, from raw material selection to final packaging. In case of any issues or concerns regarding a particular batch, these records can be used to trace back the source of the problem and address it quickly. The pharmaceutical industry relies heavily on batch records to maintain high standards of quality control, making them an indispensable tool for producing safe and effective medications.
For more insights, see: Purchase Order Process
What should be included in a batch manufacturing record?
A Batch Manufacturing Record (BMR) is a document that contains step-by-step documentation of the entire manufacturing process involved in producing a product batch, including the expected batch yields and labeling requirements. The BMR documents everything from the start to end dates of the manufacturing process, as well as the batch lot and control numbers.
The MFR includes instructions for each step, including dual sign-offs by the person performing them. Safety information, potential hazards, and personal protective equipment (PPE) required are also documented. Quality control tests and status checks including deviations are recorded along with cleaning information for processing lines.
The time completed health and safety information, PPE required, bill number, complete change log, audit trail, and finished product documentation proving that finished product meets established specifications are also part of the BMR.
Related reading: Ppe Manufacturing
The Essential Components of a Master Formula Record
A Master Formula Record (MFR) outlines all the components required to make a product batch. It includes information on the manufacturing process, step-by-step guidelines, and safety information such as proper handling, heating/cooling, and storage temperatures. The materials you'll need are also included in the MFR, as well as personal protective equipment (PPE) required for the manufacturing process.
The manufacturing process is outlined in detail with clear and straightforward instructions that must be followed in the proper order. This includes maintenance cleaning and sanitizing instructions that must be performed prior to starting the manufacturing process. The MFR outlines detailed information such as estimated costs and labor hours required to complete each step of the production.
The materials list includes size, weight, and quantity of each item needed for the batch record. The MFR provides step-by-step instructions for each component so that every team member knows what to do at any given time during production. This document can take up to 15 minutes to review before beginning work on a new product batch but it's an essential part of ensuring quality control throughout the entire manufacturing process.
A different take: Production Management
Discovering the Basics of an Electronic Batch Record
Electronic batch records are the digital versions of batch records which are stored electronically, short irrespective of the medium in which they were generated. Electronic batch records are becoming increasingly popular, especially in life sciences companies that produce large amounts of product records. These electronic batch records have enabled companies to manage their production process more efficiently and effectively by reducing the amount of paperwork required and simplifying data entry. In essence, electronic batch records allow a company to streamline its production process while minimizing human error and maximizing quality control.
Readers also liked: Production Planning
All you need to know about Batch Manufacturing Record BMR
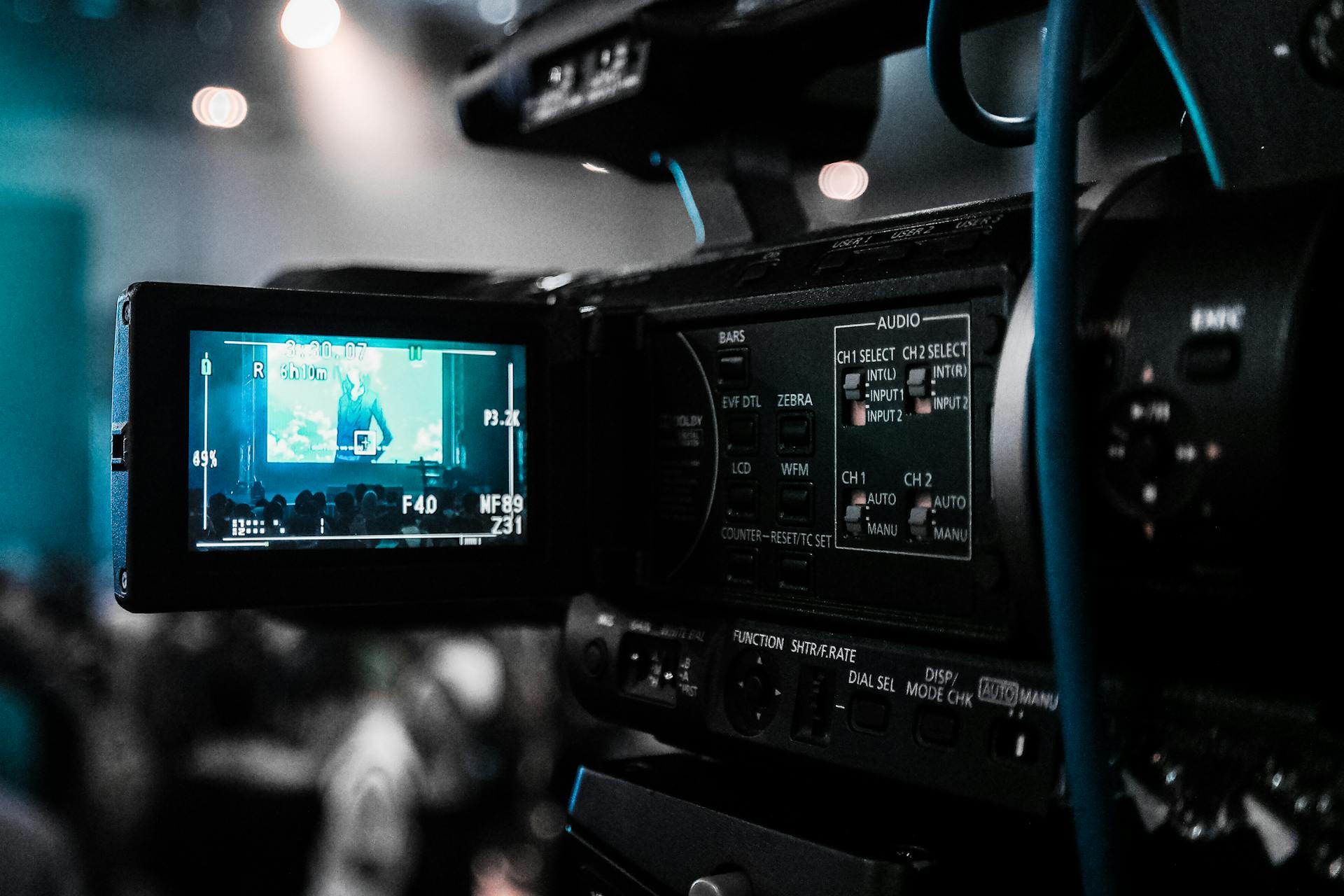
A batch manufacturing record (BMR) is a written record of the entire manufacturing process of a specific quantity of chemical, food, drug or other consumable products. It provides detailed instructions on how to produce the product batch with uniform character and within specific limits produced under a single manufacturing order. Process manufacturers use BMRs to ensure health safety while meeting FDA requirements and regulations apply.
The purpose of BMRs is to make sure that consumable products such as body including pharmaceuticals, packaged foods, nutritional supplements, personal care products meet quality standards set by FDA regulators. Safety procedures must be followed correctly during production of these items. Quality control testing should be performed on ingredients and handled properly by employees with proper clearance and dual sign-offs.
BMRs are an essential part of the process for chemical and process manufacturers. A BMR chemical or a master formula record (MFR) enables them to maintain consistency in their production processes. If you're considering producing consumable products, you should familiarize yourself with the best practices around creating BMRs so that you can ensure your product meets all regulatory requirements while maintaining safety for both consumers and employees who handle the product during production.
Project management for manufacturing: the five stages of planning
Project management is an essential process for any manufacturing organization. An efficient way to plan and manage the production process is by breaking it down into five stages of planning. The first stage is project initiation, where you define the scope of the project and its objectives.
The second stage is project planning, where you identify all the resources required to complete the project efficiently. This includes materials, equipment, and personnel needed to accomplish the task. Once you have identified all the resources needed, you can allocate them in an efficient manner to ensure that you are utilizing your resources efficiently.
The third stage is project execution, where you put your plan into action. This involves coordinating all the resources that you have allocated in a way that helps you achieve your objectives quickly and effectively. By following these five stages of planning, you can ensure that your manufacturing project is completed on time and within budget. Learn more about business tips like this by checking out our top 10 articles on our website! This article was a quick 6 mins read filled with useful business tips for manufacturers looking to improve their project management skills in just 5 mins read!
Recommended read: Project Management for Manufacturing
The Makers of Batch Manufacturing Records: Unveiled!
The makers of batch manufacturing records play a crucial role in the production process. In larger companies, there are often separate teams and departments involved in creating and maintaining these records to ensure they comply with cgmp regulations. A designated individual, typically the person responsible for quality control operations, oversees the creation of these records and ensures that they are accurate and up-to-date.
In smaller companies, the personnel involved in creating batch records may be limited, with one or two individuals handling all aspects of the process. Regardless of the size of the company, batch records serve as a critical tool in documenting the manufacturing process from start to finish. These records provide detailed information on each step involved in producing a product, including raw materials used, equipment used, and any deviations from standard procedures. By ensuring that batch records are accurate and complete, manufacturers can maintain product consistency and safety for their customers.
Choosing the Right Electronic Batch Records Solution
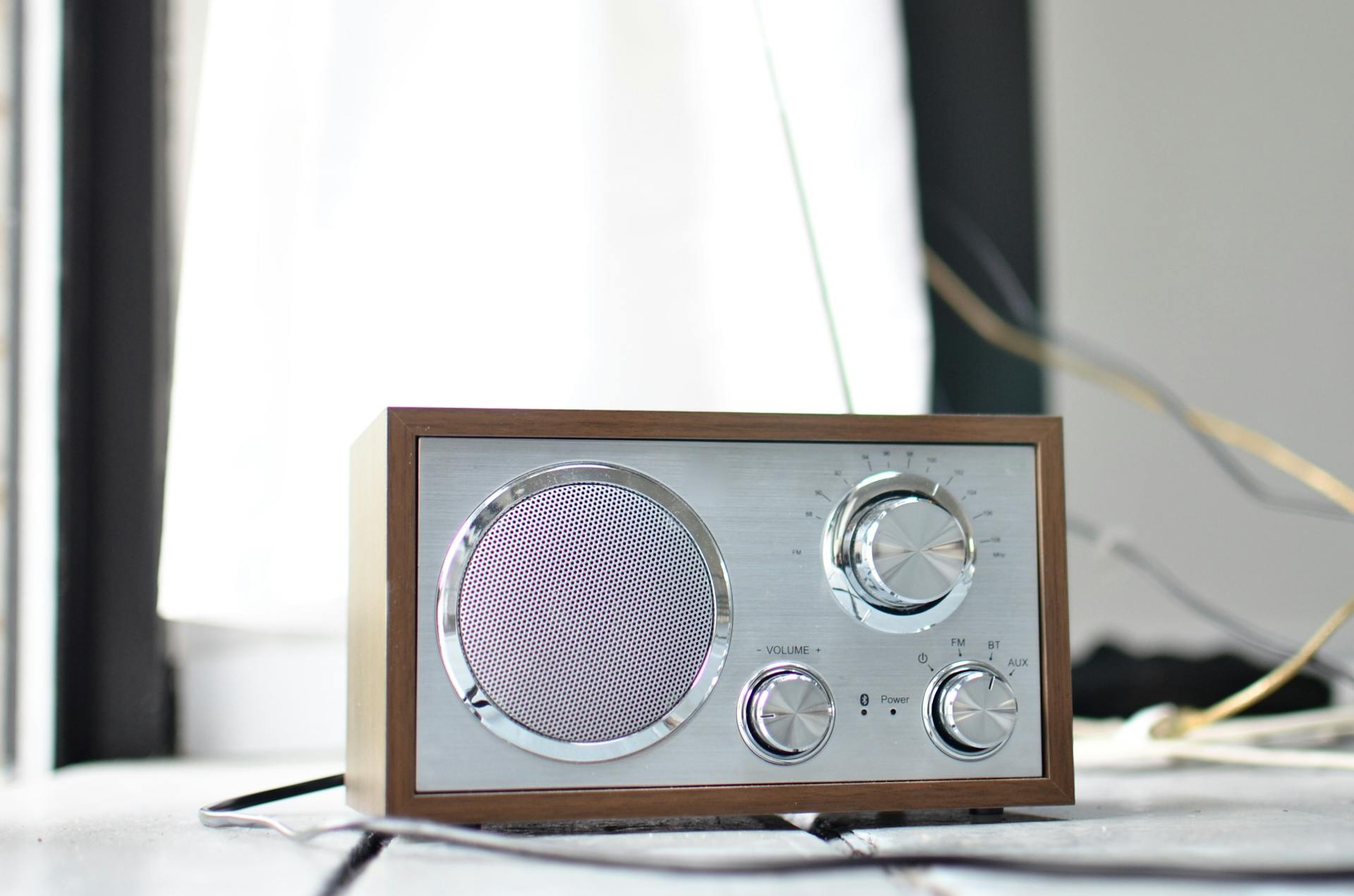
As mentioned earlier, manual management of batch records can come with inherent challenges. These include issues related to data integrity, human error, and security. Storage problems are also a concern when dealing with huge amounts of documentation for each manufactured product. Fortunately, there are efficient electronic batch records solutions that address many of these concerns.
The right electronic batch records solution should provide access assured data integrity, decreased human error-related problems, and state-of-the-art security. This makes it easier to comply with regulatory requirements while reducing the risk of costly mistakes. Linking batch records to inspection records, documented acceptance criteria, work instructions, standard operating protocols, device master records and nonconformance equipment products can help ensure consistency and accuracy throughout the manufacturing process.
Ultimately, finding a suitable solution will depend on your specific needs and budget. Look for a provider with experience in your industry who can offer customizable software that fits your unique requirements. With the right electronic batch records system in place, you can streamline your manufacturing processes while ensuring compliance and minimizing risks associated with manual record-keeping.
On a similar theme: Batch Manufacturing
Unveiling the Contents of Your Batch Manufacturing Record
Batch records are a compilation of all documents related to a batch, from raw material procurement to final product packaging. These records should be properly formatted and maintained for future reference. The contents of a batch record may vary depending on the type of product being manufactured, but generally include information about equipment used, processing steps taken, and quality control measures performed. A thorough understanding of the contents of your batch manufacturing record can help ensure consistency in production and aid in identifying any potential issues or deviations during the manufacturing process.
1. Definitions
The batch record is a document that details the ingredients, processes, and procedures used in the manufacturing of each batch of a product. This section defines the requirements for creating and maintaining accurate and complete batch records. It is essential that production understands the importance of following these guidelines to ensure consistency and quality in every batch produced.
A complete batch record includes information such as lot numbers for raw materials, equipment used, processing instructions, testing results, packaging specifications, and any deviations or corrective actions taken during production. This section aims to provide clarity on what should be documented in each batch record to ensure compliance with regulatory requirements and industry standards. By following these guidelines, companies can improve their ability to detect and resolve issues quickly while maintaining consistent product quality.
Exploring the Contents of an Electronic Batch Record
A typical electronic batch record contains essential information that pharmaceutical organizations and medical device manufacturers need to ensure quality and compliance. The actual batch record details include control numbers, quantity released, laboratory control results, acceptance records, and complete labeling control records. These data help personnel supervising the manufacturing process to monitor the production and ensure that all products meet the required standards.
The exception summary section in an electronic batch record is a critical component that allows manufacturers to track any issues that arise during production. This section contains information about deviations from standard operating procedures (SOPs) and how they were resolved. Manufacturers can use this information to identify areas where improvements are necessary or to inform future decisions about production processes.
Having a one-size-fits-all approach when creating electronic batch records is not practical as each product has its unique device identifier (UDI) or universal product code (UPC). Therefore, it's essential for manufacturers to tailor their electronic batch records to match their specific products' requirements. By doing this, they can efficiently manage their production processes and ensure that all products meet regulatory standards.
Frequently Asked Questions
What are batch records?
Batch records are documents that record the production and testing of a batch of a product. These records ensure quality control by documenting each step of the manufacturing process, from raw materials to finished products.
What is the importance of batch records?
Batch records are important documentation that tracks the production, testing and distribution of a batch of products. They serve as a legal record and an audit trail to ensure quality control and regulatory compliance in the manufacturing process.
Do medical device manufacturers and pharmaceutical companies need batch records?
Yes, medical device manufacturers and pharmaceutical companies are required to maintain accurate batch records to ensure product quality, safety, and traceability throughout the manufacturing process. These records must include details such as raw material sourcing, production dates, testing results, and any deviations from standard procedures.
How do electronic batch records systems improve data integrity?
Electronic batch records systems improve data integrity by automating data capture, reducing manual errors, providing real-time visibility into production processes, and ensuring compliance with regulatory requirements.
What is the difference between paper forms and electronic batch record?
Paper forms require manual data entry and can be prone to errors, while electronic batch records automate the process and provide real-time data for improved accuracy and efficiency.
Featured Images: pexels.com