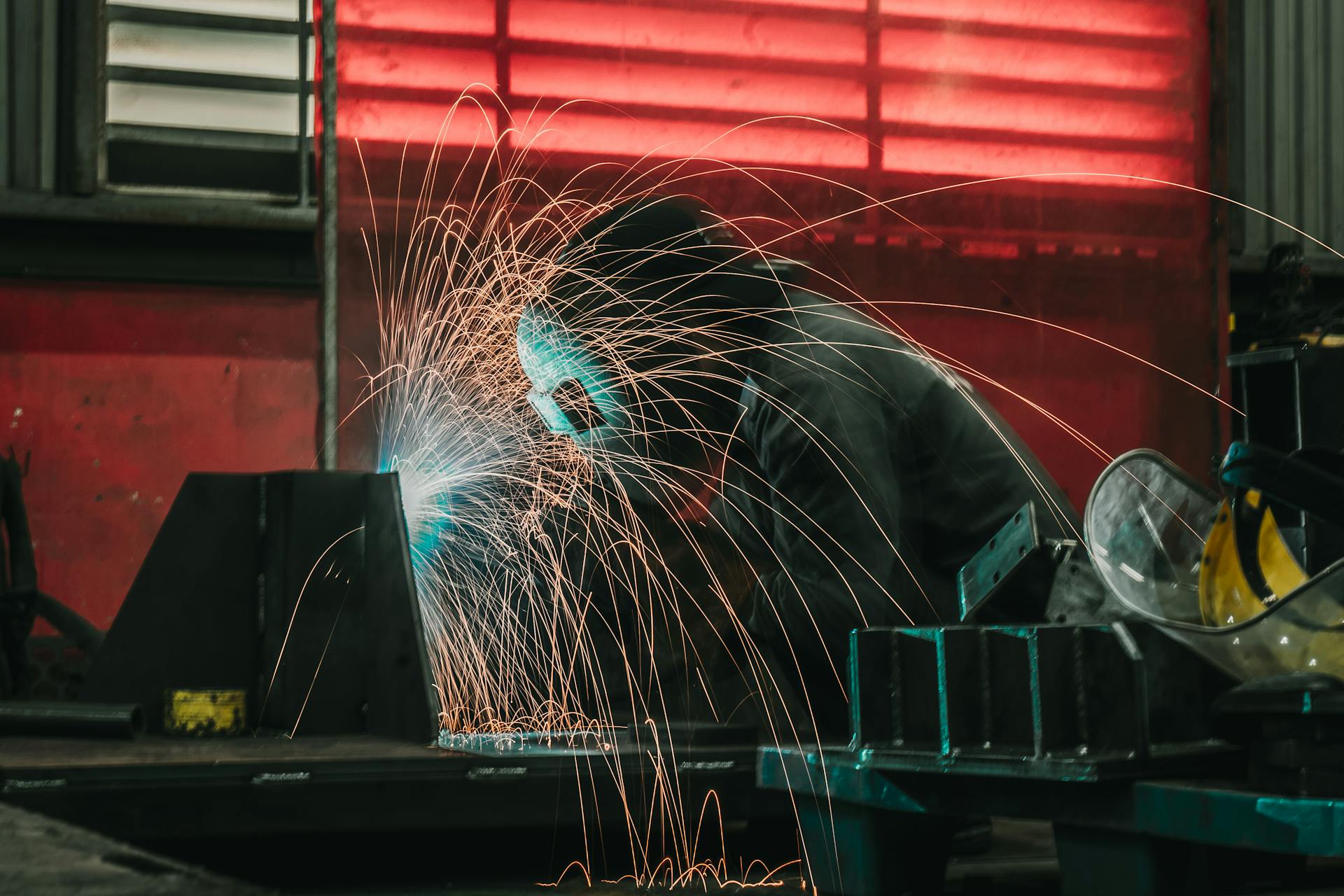
Are you looking to improve your company's welding project? If so, it's important to understand the different types of welding available. Welding is an important step in many manufacturing projects and can be found in items we use every day, from phones to laptops.
Welding requires varying levels of precision depending on the project at hand. Knowing which type of welding to use can make or break the success of your manufacturing process. In this article, we'll provide a comprehensive list of welding types explained, ensuring you're equipped with the knowledge necessary for happy manufacturing.
Joining metals together through welding is a complex process that involves many different techniques. It's essential to choose the correct method for each project, as using an incorrect technique may lead to faulty joints that could weaken over time. By understanding the types of welding available and their appropriate applications, you can ensure a successful outcome for your manufacturing projects.
Discover more: Types of Tower Cranes
Discover the Various Ways to Join Metals!
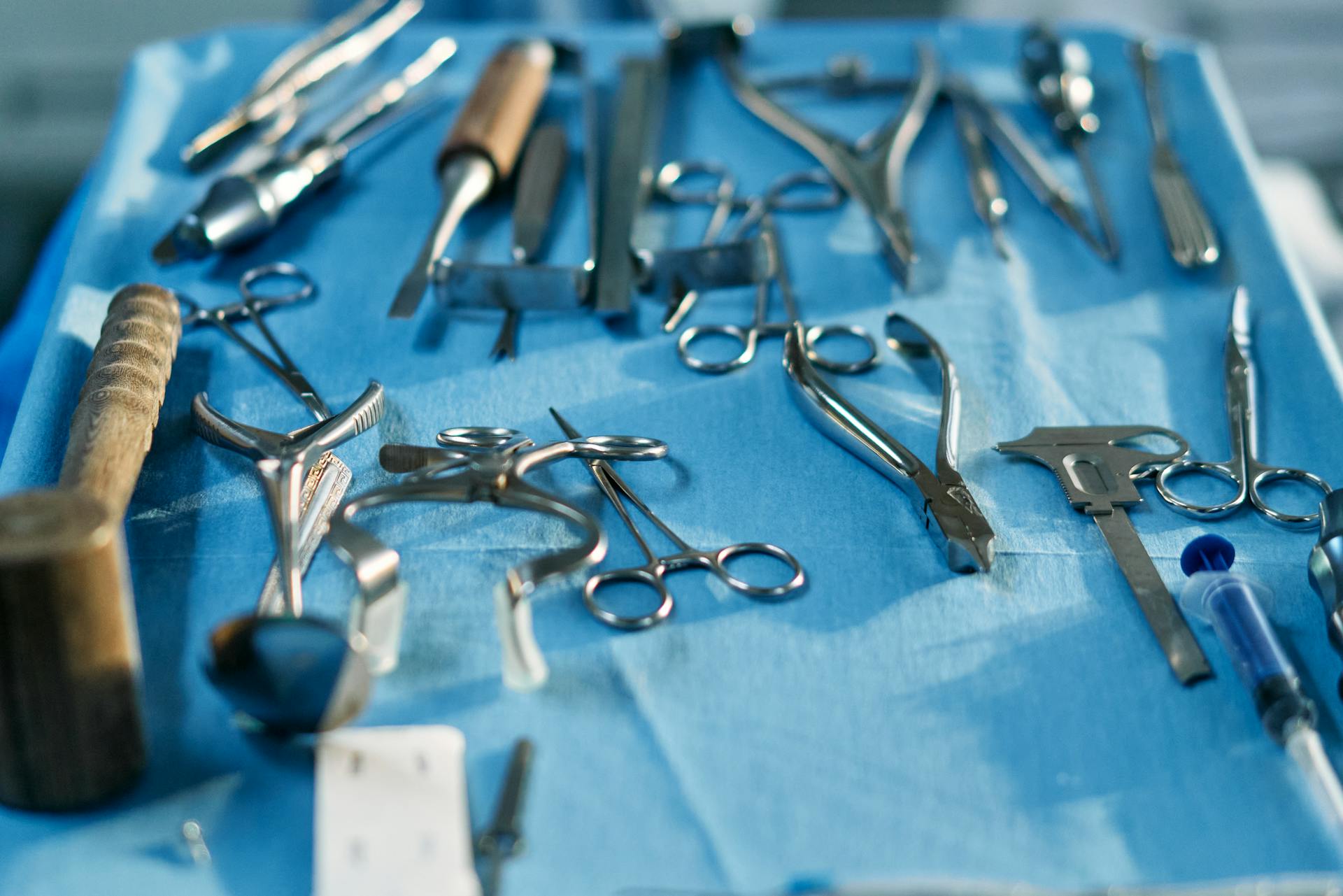
If you're in the metalworking industry, there are various ways to join metals. The most common type of welding includes arc welding, resistance welding, and oxyfuel welding. These methods use heat to melt the metal and fuse it together.
Solid-state welding joins metals without melting them. This type of welding is ideal for metals that would otherwise be damaged or distorted by high temperatures. Solid-state welding includes diffusion welding, friction welding, and ultrasonic welding.
Finally, there's explosive welding – a process that joins two dissimilar materials by using explosives to create a collision between them. This method is useful for combining materials with different properties or thicknesses. Regardless of the method chosen, each has its advantages and disadvantages depending on the job at hand.
A Q&A with Katana’s CPO and Head of Product Engineering on roadmap-based development
If you're into manufacturing, then chances are that you have heard of Katana. As a leading software company in the industry, they're known for doing things differently. Recently, we had the opportunity to sit down with Katana's CPO and Head of Product Engineering to discuss their approach to roadmap-based development.
When asked about how the engineering department at Katana approaches product development, they emphasized the importance of having a clear roadmap. They explained that it's crucial to have a plan in place that outlines what needs to be accomplished and when. This helps keep everyone on track and ensures that everyone is working towards the same goals.
In terms of business tips, they also shared some great advice on prioritizing features. They advised businesses to focus on building features that will provide the most value to their customers first. This not only helps with customer retention but also ensures that resources are being used effectively. Overall, this Q&A was a great insight into how Katana operates and provides valuable business tips for those looking to improve their product development processes.
Concluding Our Journey: Unveiling the Final Remarks
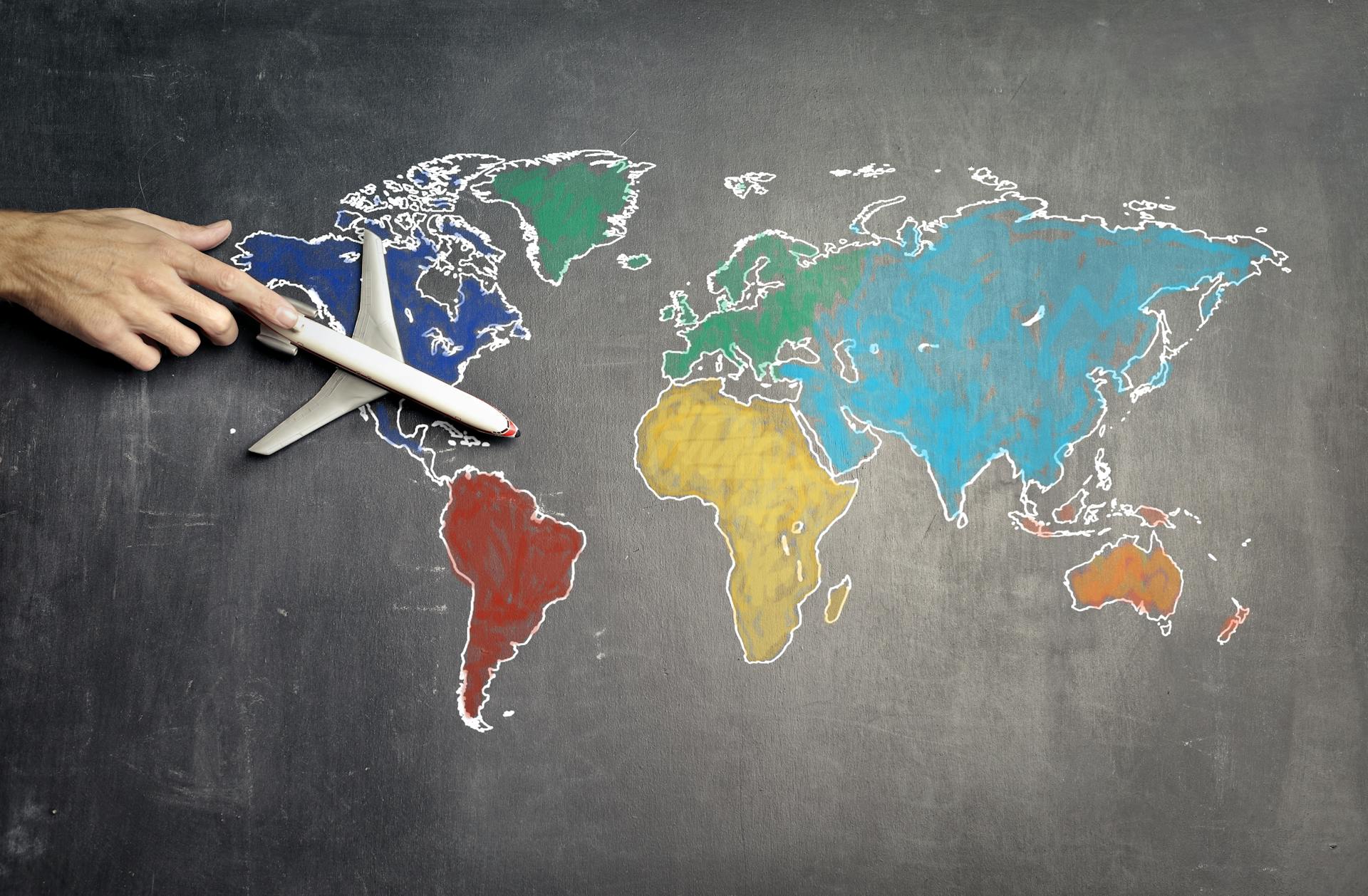
In conclusion, welding is a strong joining process that has been around for centuries. Welding involves heating two metal parts to their melting points and fusing them together to form one solid piece. There are many types of welding processes that can be used depending on the material being welded and the application it will be used for.
Some welding methods require costly specialized equipment, while others only require simple tools. One of the faster methods related to welding is MIG welding, where a wire electrode is fed through a gun to melt and fuse metals together. No matter what type of welding process you use, it's important to have the proper tools on hand to ensure a successful weld. You can download a PDF with 26 essential welding tools or sign up for our newsletter with your email address to stay updated on new techniques and tool releases.
In conclusion, we hope this article has provided you with insight into the basics of different types of welding processes. Remember that safety should always come first when working with any type of power tool or welding equipment. Always wear proper protective gear and follow all safety guidelines provided by your equipment manufacturer or employer. With these tips in mind, you'll be well on your way to becoming a skilled welder!
Additional reading: 5 Types
1. 14 thoughts on “12 Types of Welding Processes & Their Uses [Full Guide] PDF”
After reading the article on "12 Types of Welding Processes & Their Uses [Full Guide] PDF", it's clear that welding is a complex and important process in many industries. The article breaks down each type of welding and explains its uses in a clear and concise manner. Many readers have commented positively, such as Sisay Gutamarch 3 2023 atreply, who found the guide helpful.
One comment from Sarah Jones July 26 2022 atreply praises the author for explaining well, which is a testament to the quality of information presented. Even those with some prior knowledge, like Emmanuel Belmonte Sarmiento March 10 2022 atreply, found value in the guide. Overall, this is a great piece for anyone looking to learn more about types of welding and their applications.
Food for thought while you look for the perfect welding technique
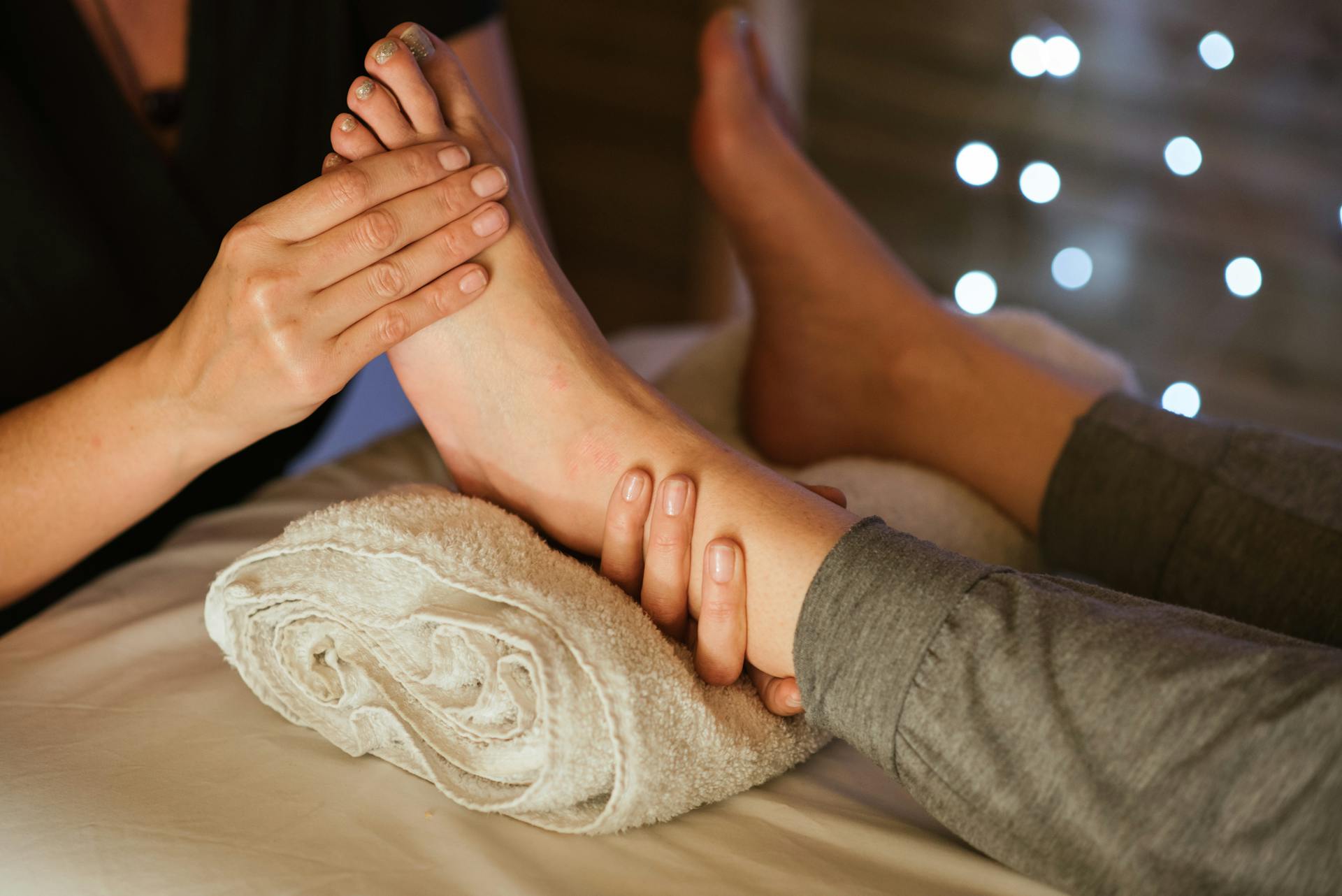
Finding the perfect type of welding for your project can be a daunting task. There are many types of welding available, each with their own unique characteristics and applications. Before starting any welding project, it is important to have a basic understanding of the different types of welding available.
Some projects require fusion welding, which uses heat to melt and fuse metals together. This includes processes like MIG, TIG, and stick welding. Other projects may require solid-state welding, which does not involve melting the metal. Instead, pressure or friction is used to bond the materials together.
When searching for the perfect type of welding for your project, consider factors like cost, strength, speed, and ease of use. It may take some trial and error before finding the best method for your specific needs. But with a little patience and perseverance, you can make any welding project good luck!
Discover the Concept of Welding and its Meaning.
What is welding? Welding is a permanent joining process that brings metal pieces similar in nature together with the help of heat. The heating process raises the temperature high enough to melt the metal join, and additional metal known as filler material, also known as filler metal, is used to join the two pieces together.
The concept of welding involves a variety of techniques that are used according to the application and requirement. Some techniques involve melting points additional metal for the welding process, while others do not require any filler material. Understanding these different types of welding can be fundamental when choosing which method to use for your project. Ultimately, welding plays an essential role in many industries and applications, from construction to manufacturing and even art.
Is distributed manufacturing the future of production?
Distributed manufacturing promotes efficiency and flexibility in production. With this process, manufacturers can produce their products at different locations, reducing transportation and lead times. It also allows for faster response times to market changes and reduces the risk of supply chain disruptions.
Moreover, distributed manufacturing reduces costs by eliminating the need for large warehouses and inventory management. By moving production closer to customers, businesses can save money on transportation and storage costs. Plus, with a shorter supply chain, there is less risk of unexpected delays or quality issues.
In conclusion, distributed manufacturing is an efficient way to produce goods that will continue to shape the future of production. By reducing costs and promoting flexibility, it provides businesses with the tools they need to stay competitive in today's global economy. For more business tips on welding types and other topics related to manufacturing, check out our blog!
How Welding Benefits Industries and Creative Projects
Welding is a vital process in the metal industry and is widely used in various industrial sectors. The automobile industry, ships, aerospace, railway coaches, earthmover bodies are some of the industries that rely heavily on welding for their manufacturing processes. Welding plays a significant role in constructing automobile chassis since it provides a strong bond that can withstand heavy loads and extreme environmental conditions.
Welding is also used extensively in creative projects such as making window shutters, doors gates, and other fabrication work. With welding, artists and designers can create unique and intricate designs that would not be possible with traditional techniques. This allows them to create custom-made pieces of art or decorative items that are both aesthetically pleasing and durable.
In conclusion, welding benefits many industries by providing strong bonds between metals that can withstand heavy loads and harsh environments. It also allows for customization of designs in creative projects which results in unique pieces of artwork or decorative items. The importance of welding cannot be overstated as it has become an essential part of modern-day manufacturing processes across various industries.
Explore further: Types of Heavy Trucks
Selecting the Right Costing Method: Why It Matters
Costing methods are essential for any business to determine the cost of goods sold (COGS) and improve profit margins. However, there are many types of costing methods available in the market, and picking one that works best for your business can be a daunting task. Understanding the main differences between each costing method is crucial to make an informed decision.
By choosing a suitable costing method, businesses can gain valuable insights into their expenses and profits. The right approach will help them understand which products or services are generating more revenue and where they need to cut costs. This information can then be used to make informed business decisions that improve their bottom line. So, if you're looking for business tips on how to improve your profitability, learning about different costing methods is an excellent place to start!
Frequently Asked Questions
What are the four basic Weld types?
The four basic types of welding are MIG, TIG, Stick, and Flux-cored. Each type of welding uses a different method to join two pieces of metal together.
What is the strongest type of Weld?
The strongest type of weld is a fusion weld, which creates a bond between two pieces of metal by melting them together. This type of weld results in a strong, permanent joint that can withstand high levels of stress and pressure.
What type of welding makes the most money?
Pipe welding is the highest paying type of welding due to the high demand and specialized skill required. Experienced pipe welders can earn upwards of six figures annually.
Which is the best welding?
The best welding method depends on the specific project and materials being used. Some popular methods include MIG, TIG, and stick welding, each with their own strengths and weaknesses. It's important to consult with a professional welder to determine the best method for your needs.
What is the best welding for beginners?
MIG welding is generally considered the best type of welding for beginners due to its ease of use, versatility, and affordability. It uses a continuously fed wire as the electrode and is suitable for welding thin materials such as automotive parts, household appliances, and light structural work.
Featured Images: pexels.com