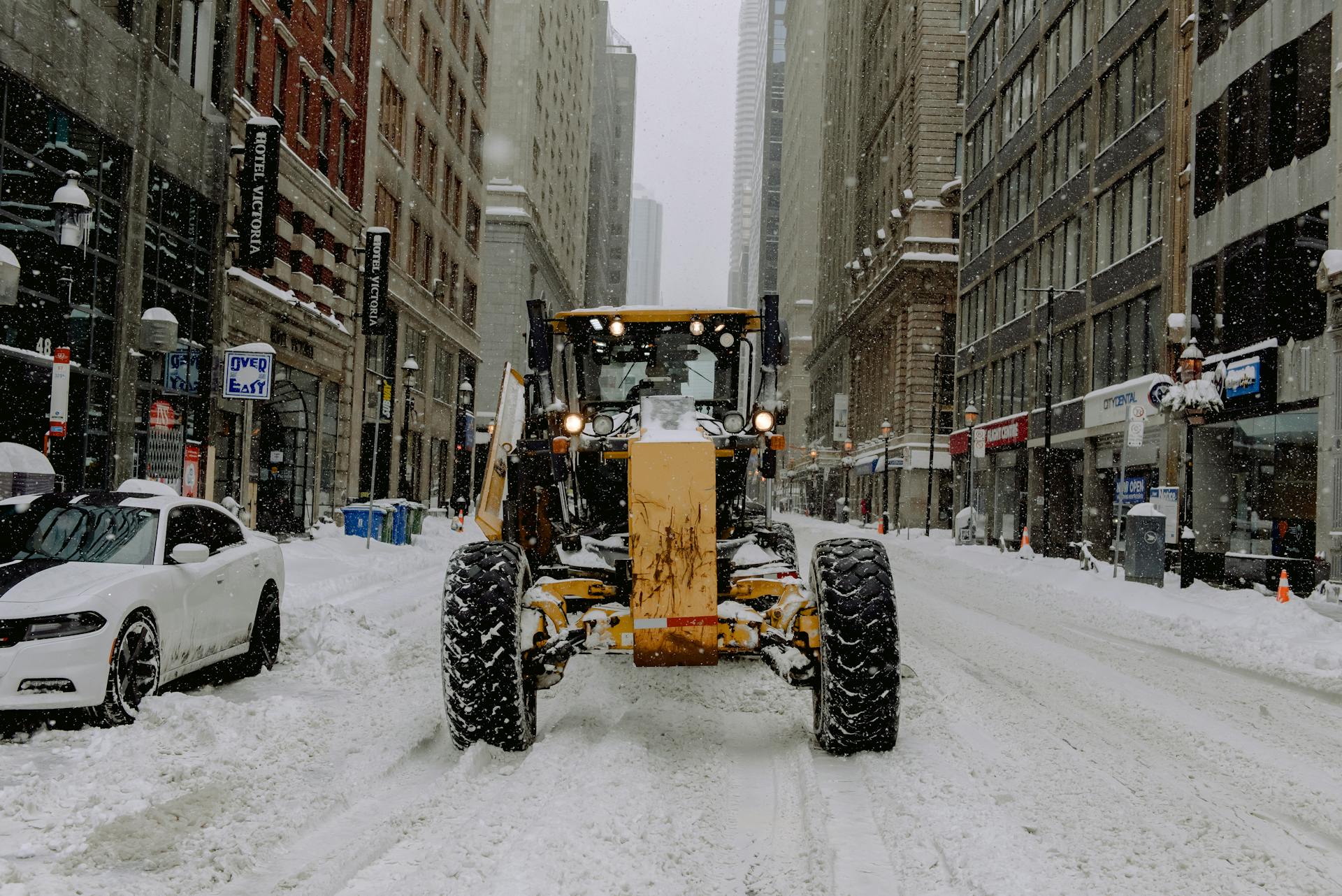
To maximize motor grader blade efficiency, it's essential to maintain the right blade angle. A blade angle between 10 and 15 degrees is ideal for most applications.
Using the correct blade angle can significantly improve performance and reduce wear on the blade.
Proper blade maintenance, including regular cleaning and lubrication, can extend the life of the blade by up to 50%.
Choosing the Right Blade
The shape of the blade is a crucial factor in choosing the right motor grader blade. Consider a flat or curved edge, with serrated edges available in both configurations.
The width of the blade is also important, as it will affect the blade's performance in different applications. Cat offers two types of grader edges, so it's essential to choose the one that best fits your needs.
There are three edge thicknesses to choose from for the 16M and 24M motor graders. This means you can select the thickness that provides the right balance of durability and performance for your specific application.
Cat's Cat GraderBits system expands the range of edge shape options, giving you more flexibility when choosing a blade. This system offers a variety of shapes and thicknesses to fit every application.
Here are the three edge types mentioned in the article:
Reducing Costs and Maintenance
Proper management of the machine and materials interface can significantly lower machine operating costs and reduce cab vibration, improving operator comfort.
Starting with the correct moldboard position is key. Make sure to position the moldboard 2” ahead of the edge for optimal results.
Excessive down pressure can lead to edge slivering, so keep your speed below 6mph/8kph.
Crowning occurs when the cutting edge conforms to the material being graded, but a narrow and thin edge can reduce the amount of "throw away" material.
Standardizing your hardware can simplify inventory and lower costs. For example, using moldboard bushings that reduce 3/4” holes to 5/8” can make a big difference.
By following these simple tips, you can reduce costs and maintenance, ensuring your motor grader blade operates efficiently and effectively.
Importance of Blade Maintenance
The blade of a motor grader is a critical component that requires regular maintenance to ensure optimal performance.
A worn-out blade can cause excessive shock, putting pressure on the rest of the motor grader, including the frame and drivetrain. This can result in damage or significant shortening of the life of these components.
Even with expert operators, the cutting edge of a motor grader's blade is designed to wear and will need to be replaced eventually. Regular inspections can help identify signs of excessive wear or bending.
More horsepower is needed to force a worn-out blade through each cut, resulting in higher fuel costs, more wear and tear on tyres, and lower overall productivity.
The blade is far from the most expensive or time-consuming part to replace, but neglecting its maintenance can lead to costly repairs down the line.
Operating and Maintenance Procedures
Operating a motor grader requires expertise and experience, as proper use of the blade significantly reduces wear and tear. An expert operator can keep the cutting edge even and sharp, making it a vital part of motor grader operation.
It's essential to position the moldboard correctly and use the right speed to avoid jerky movements. Working the motor grader in a slow and smooth way is the best way to avoid wear and tear of your grader.
To minimize stress on the blade and prevent damage, you should avoid any jerky motions and work at a speed between 10 kilometres to 16 kilometres per hour. This will make the motor grader more fuel competent and reduce the risk of damage.
Rotating Bit System
The Rotating Bit System is a game-changer for road reconditioning applications. It outperforms steel blades in high-production road reconditioning applications.
Individual cutting bits have tungsten carbide tips and form a serrated edge to penetrate and lift material to the surface immediately. This results in most road maintenance jobs being accomplished in a single pass.
Material is brought to the surface for reuse, reducing the expense of spreading new gravel. This is a significant cost savings for road maintenance crews.
If this caught your attention, see: Road Grader
The Rotating Scarifier Bits are self-sharpening for more uniform wear and long life. Cutting height is maintained as cutting tools may be rotated from position to position.
The rotating bit system allows for no cast angle restriction, giving operators more flexibility in their work. This can be especially helpful in tight spaces or complex road layouts.
Rotating Scarifier Bits can last as long as 5-10 sets of conventional grader blades, making them a cost-effective option in the long run. They are made for applications such as dirt and gravel reclamation, oil road reclamation, and snow and ice removal.
Here are some key features of the rotating bit system:
Follow Procedure
Following the correct procedure is crucial to operating a motor grader efficiently and safely. An expert operator can significantly reduce wear and tear on a grader's cutting edge.
To keep the blade sharp, position the moldboard correctly and use appropriate speed, avoiding jerky movements. An expert operator can minimize stress on the blade and prevent shock loads.
You should look for an experienced operator who follows proper procedures, such as keeping the mouldboard's position correct and using the right speed. This will help reduce wear and tear on the blade.
The edge of the motor grader is designed to wear out naturally, so it's essential to inspect the blade regularly and replace it if you notice signs of major wear and tear, such as bending or missing bolts.
It's also crucial to avoid keeping the moldboard pitched forward, as this will prematurely blunt the edge. Instead, keep the top of the blade just slightly forward of the cutting edge, pitching it forward only when necessary.
Blade Maintenance Tips
Keeping your motor grader blade sharp is crucial for its performance and longevity. The blade is the most expensive part to replace, so it's essential to maintain it properly.
A sharp blade can deliver a high level of performance over a sustained period of time, whereas a worn-out blade can lead to excessive shock, putting other components under stress and reducing their lifespan.
You'll need more horsepower to move a worn-out blade through each cut, resulting in higher fuel costs and increased operational costs. This can add up quickly, making regular blade maintenance a cost-effective decision.
To avoid these issues, it's essential to keep your blade sharp. Regular sharpening can help prevent excessive shock and reduce the wear and tear on other components.
Frequently Asked Questions
What can you do with a grader blade?
A grader blade is used to remove road irregularities and level out unsealed shoulders on rural roads. It's a key tool for road maintenance, helping to create a smoother and safer driving experience.
Sources
- https://equipmentblades.com/collections/new-motor-graders
- https://www.toromontcat.com/get/motor-graders.html
- https://www.khplant.co.za/blog/motor-grader-tips-keeping-blade-sharp/
- https://albahar-sem.com/blog/4-tips-to-get-more-from-your-motor-grader-blade/
- https://www.mahindraconstructionequipment.com/blog/tips-for-keeping-the-motor-grader-blade-sharp
Featured Images: pexels.com