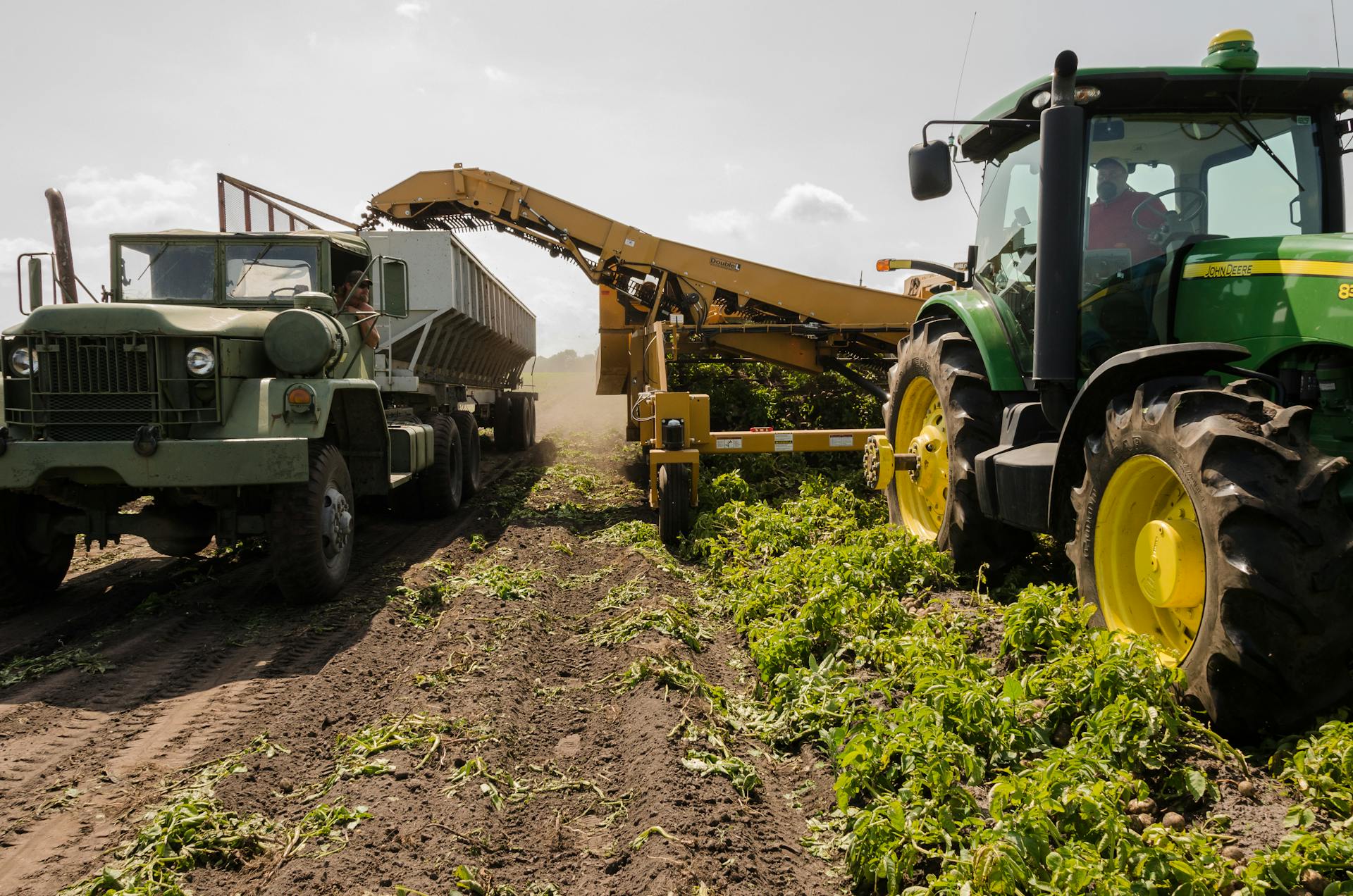
The bucket wheel excavator is a massive machine that's been making waves in the mining industry for decades. Its technology has revolutionized the way we extract materials from the earth.
This behemoth of a machine is capable of moving a staggering 1,000 cubic meters of material in a single hour, making it an essential tool for large-scale mining operations.
The bucket wheel excavator's sheer size is a testament to its impressive capabilities, with some machines reaching heights of over 60 meters and weighing in excess of 10,000 tons.
Its massive size also allows it to dig deep into the earth, with some machines capable of excavating up to 40 meters below the surface.
A different take: Excavating Machine
History and Development
Bucket-wheel excavators have been in use for over a century, with the first ones being manufactured in the 1920s.
Their size has grown drastically since the end of World War II, with some German mining firms ordering extremely large BWEs in the 1950s. The German BWEs had a wheel of over 16 m (52 ft) in diameter and weighed 5,500 short tons (5,000 t).
In the decades since, BWEs have continued to grow, with some reaching sizes as large as 96 m (315 ft) tall and 225 m (738 ft) long.
For another approach, see: German Bucket Wheel Excavator
History
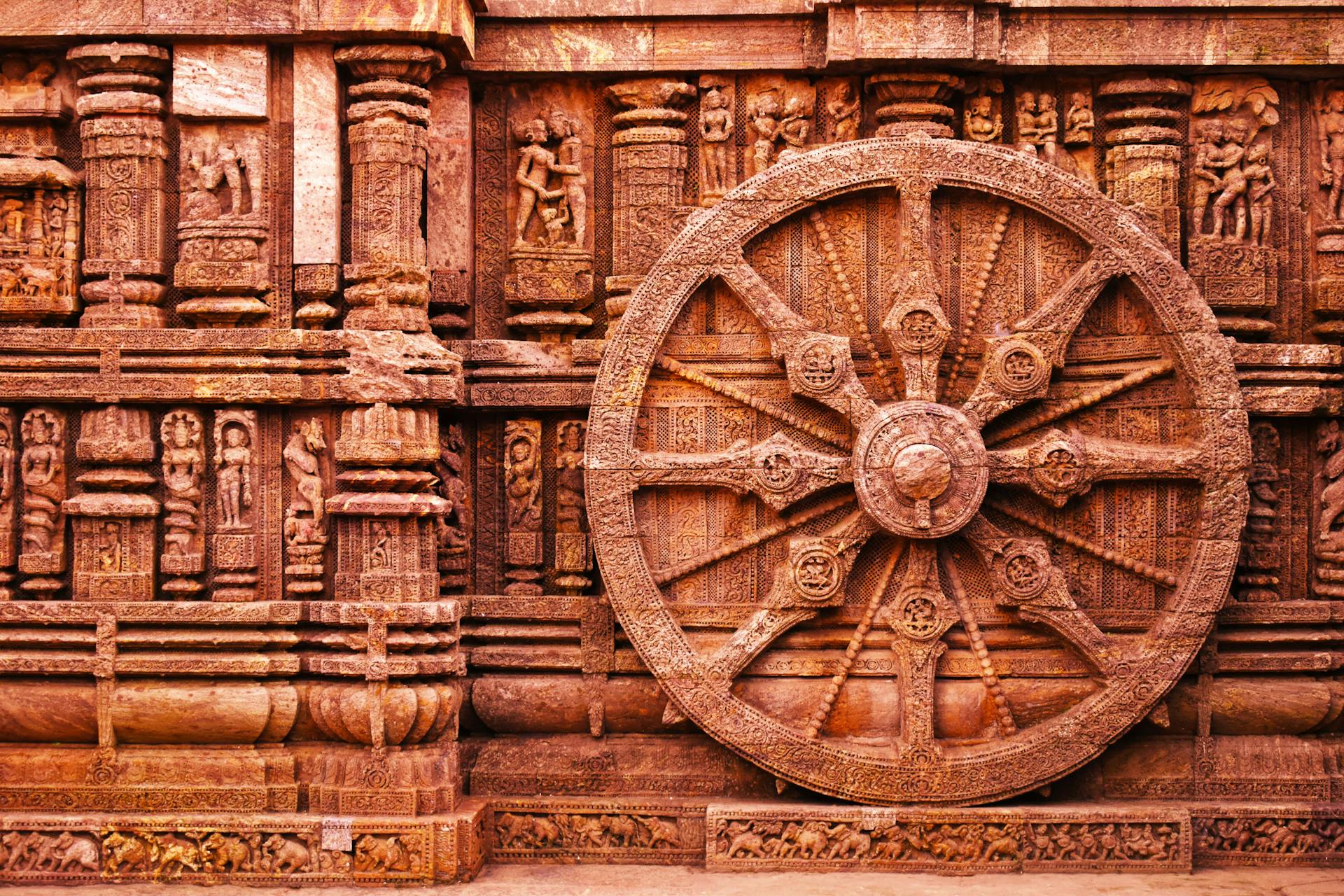
Bucket-wheel excavators have been around for over a century, with the first ones being manufactured in the 1920s. They've come a long way since then.
The overall concept of BWEs hasn't changed much, but their size has grown drastically since World War II. The largest BWEs now reach incredible heights of 96 m (315 ft) and lengths of 225 m (738 ft).
In the 1950s, German mining firms built the world's first extremely large BWEs, with wheels over 16 m (52 ft) in diameter and weighing 5,500 short tons (5,000 t). They were over 180 m (600 ft) long and could cut a swath of over 180 m (600 ft) at one time.
BWEs built since the 1990s have reached sizes as large as 14,200 t (31,300,000 lb) and can operate in extreme conditions, including temperatures as low as −45 °C (−49 °F).
Worth a look: World's Largest Crawler Crane
Engineering the Bagger
The Bagger 293's massive dimensions are a testament to its impressive credentials. With a bucket wheel over 21 meters in diameter, it can scoop up 15 cubic meters of material in each of its 18 buckets.
Chief engineer Klaus Dieter Bartsch led the project alongside mechanical engineer Manfred Kuhn, and their team's relentless pursuit of efficiency resulted in a machine that's remarkably efficient, with only five operators working in shifts around the clock to keep it running.
Planning for the Bagger 293 began in the 1980s, and the construction process took a staggering five years to complete, with an estimated cost of around $100 million.
The Bagger 293 consumes a remarkable 19 megawatts of power, powered by a combination of diesel and electricity, and can shift a mind-boggling 240,000 tons of Earth daily.
You might enjoy: Bagger 288 Precio
Design and Components
A bucket wheel excavator's design is a marvel of engineering, with several key components working together in harmony. The bucket wheel, a large round wheel with scoops, is the heart of the machine, capable of rotating to pick up material.
The bucket wheel is fixed to a boom, which is cantilevered from the superstructure. In larger machines, the booms are supported by cables running across towers at the top of the superstructure. The discharge boom receives material from the cutting boom and carries it away from the machine.
The counterweight boom balances the cutting boom, ensuring the machine remains stable. The movement systems, which include rails or crawlers, allow the machine to travel along a path and change direction.
Recommended read: Knuckle Boom Log Loader
Structure
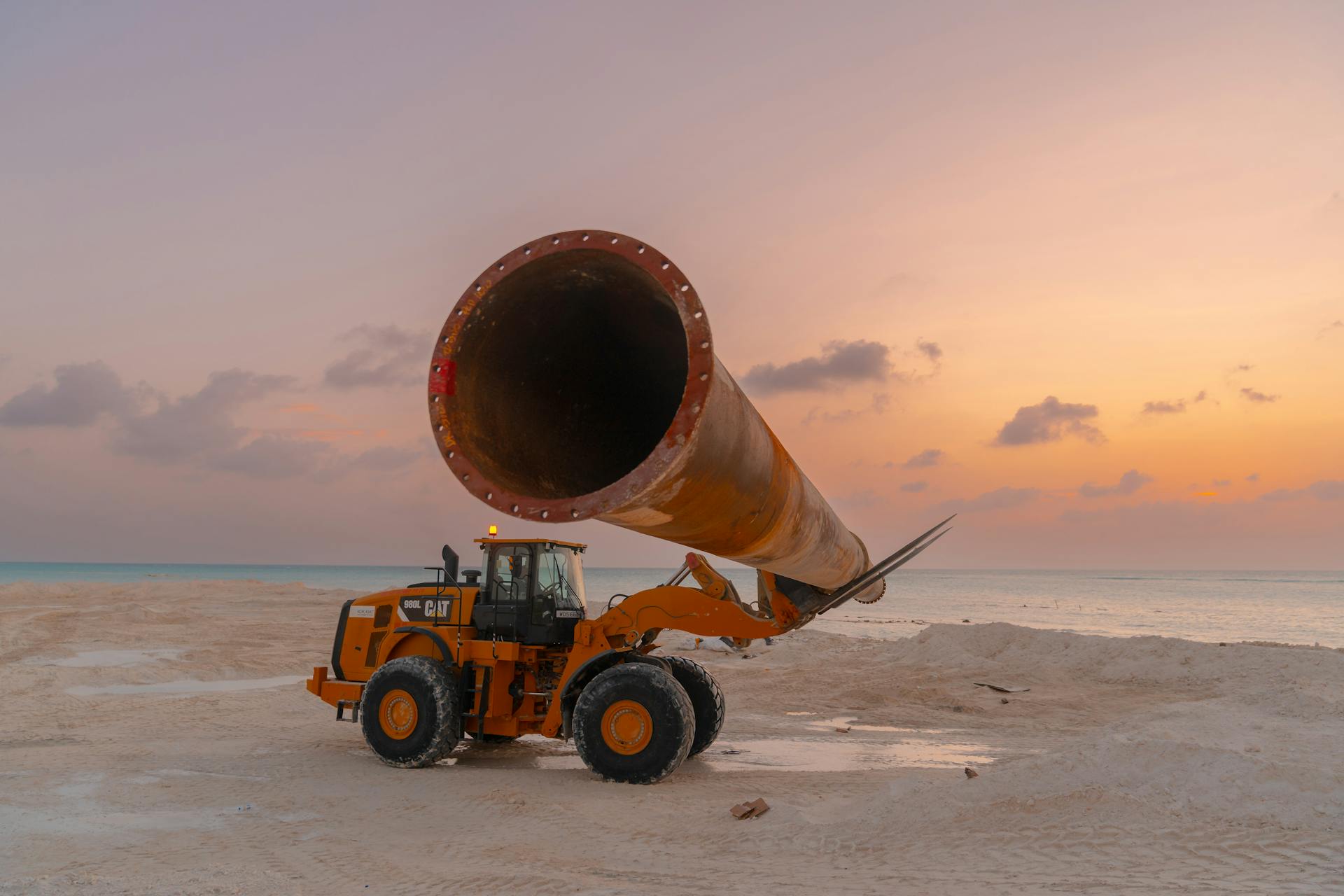
A bucket wheel excavator's (BWE) structure is a marvel of engineering. It's made up of a superstructure to which several more components are fixed, including the bucket wheel.
The bucket wheel is a large, round wheel with a configuration of scoops that's fixed to a boom and can rotate. Material picked up by the cutting wheel is transferred back along the boom.
The discharge boom receives material through the superstructure from the cutting boom and carries it away from the machine, frequently to an external conveyor system. This is crucial for the excavator's operation.
A counterweight boom balances the cutting boom and is cantilevered either on the lower part of the superstructure or the upper part. This balance is essential for the excavator's stability.
Beneath the superstructure lie the movement systems, which on older models are rails for the machine to travel along. However, newer BWEs are frequently equipped with crawlers, granting them increased flexibility of motion.
The superstructure of a BWE is capable of rotating about a vertical axis, known as slewing. This allows it to complete its duties efficiently.
Consider reading: Boom Truck vs Crane
PPT
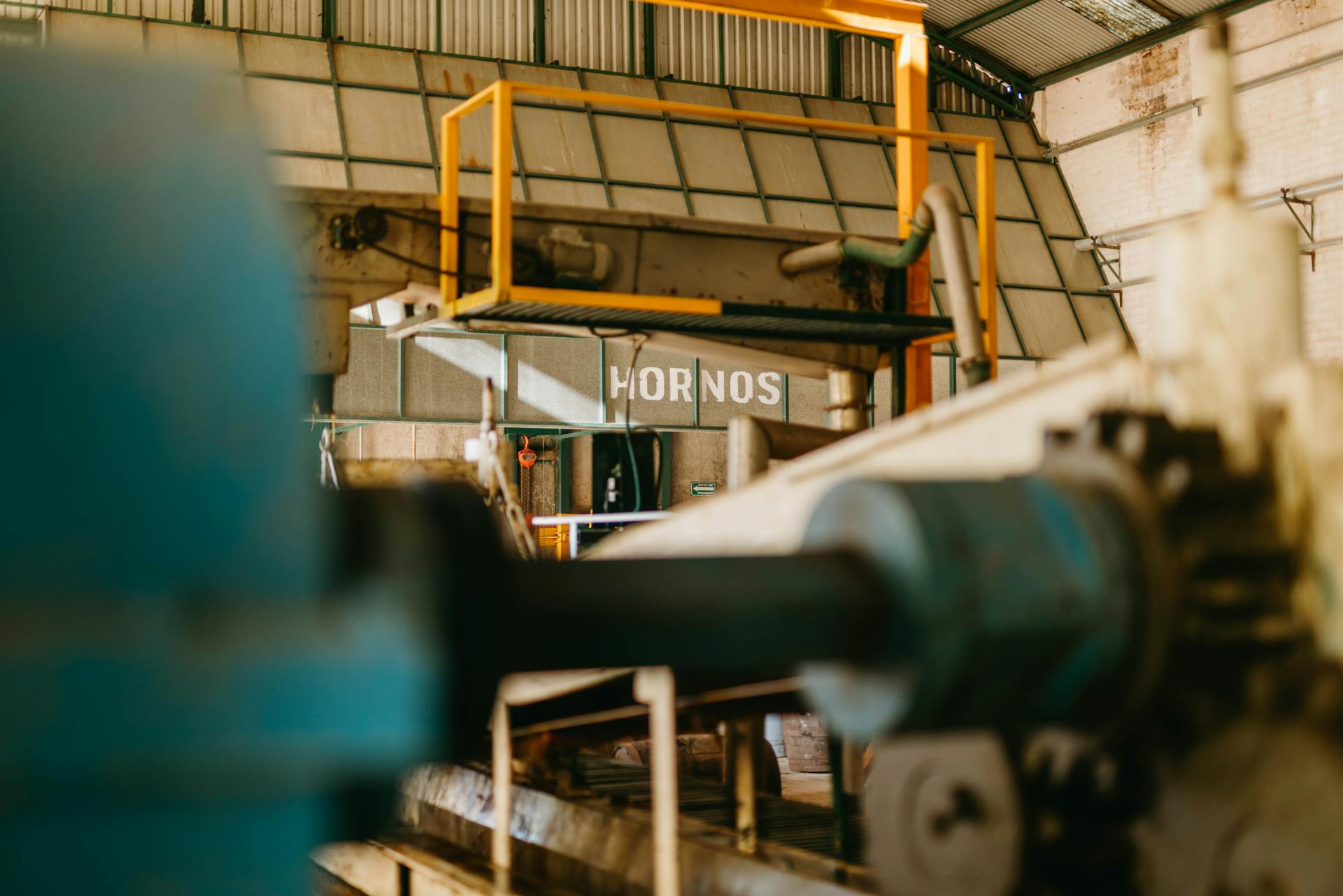
The bucket wheel excavator's (BWE) design and components are quite impressive.
The largest bucket wheel excavators can be over 90 meters tall and 240 meters long, with a 21-meter diameter wheel.
These massive machines are commonly used in strip mining and lignite mining to continuously remove overburden and deliver large volumes of material.
The largest BWE ever constructed is TAKRAF's Bagger 293, which weighs 14,200 tonnes.
BWEs used in the United States tend to be smaller than those constructed in Germany.
Bagger 293 GIF
The Bagger 293 GIF is a fascinating visual representation of the massive mining machine's operation. It's a 300-meter-long, 220-meter-wide, and 14-meter-high machine that can move 240,000 cubic meters of excavated material per day.
The Bagger 293 is a bucket-wheel excavator, a type of mining machine that uses a rotating wheel with buckets to excavate and transport soil and rock. It's a marvel of engineering that has been in operation since 1995.
The Bagger 293 is powered by two diesel engines, each producing 1,000 horsepower, which gives it the energy to move massive amounts of material.
A different take: Bagger 1473
Operation and Control
BWEs are used for continuous overburden removal in surface mining applications. They use their cutting wheels to strip away a section of earth dictated by the size of the excavator.
The overburden is then delivered to the discharge boom, which transfers the cut earth to another machine for transfer to a spreader. This may be a fixed belt conveyor system or a mobile conveyor with crawlers similar to those found on the BWE.
Mobile conveyors permanently attached to the excavator take the burden of directing the material off of the operator. The overburden can also be transferred directly to a cross-pit Spreader, which reaches across the pit and scatters overburden at the dumping ground.
Automation of the BWEs requires integrating many sensors and electrical components such as GPS, data acquisition systems, and online monitoring capabilities. Sensors can detect how much material is being scooped onto the conveyor belt, and the automation system can then vary the speed on the conveyor belts in order to feed a continuous amount of material.
See what others are reading: Automation in Construction
Operation
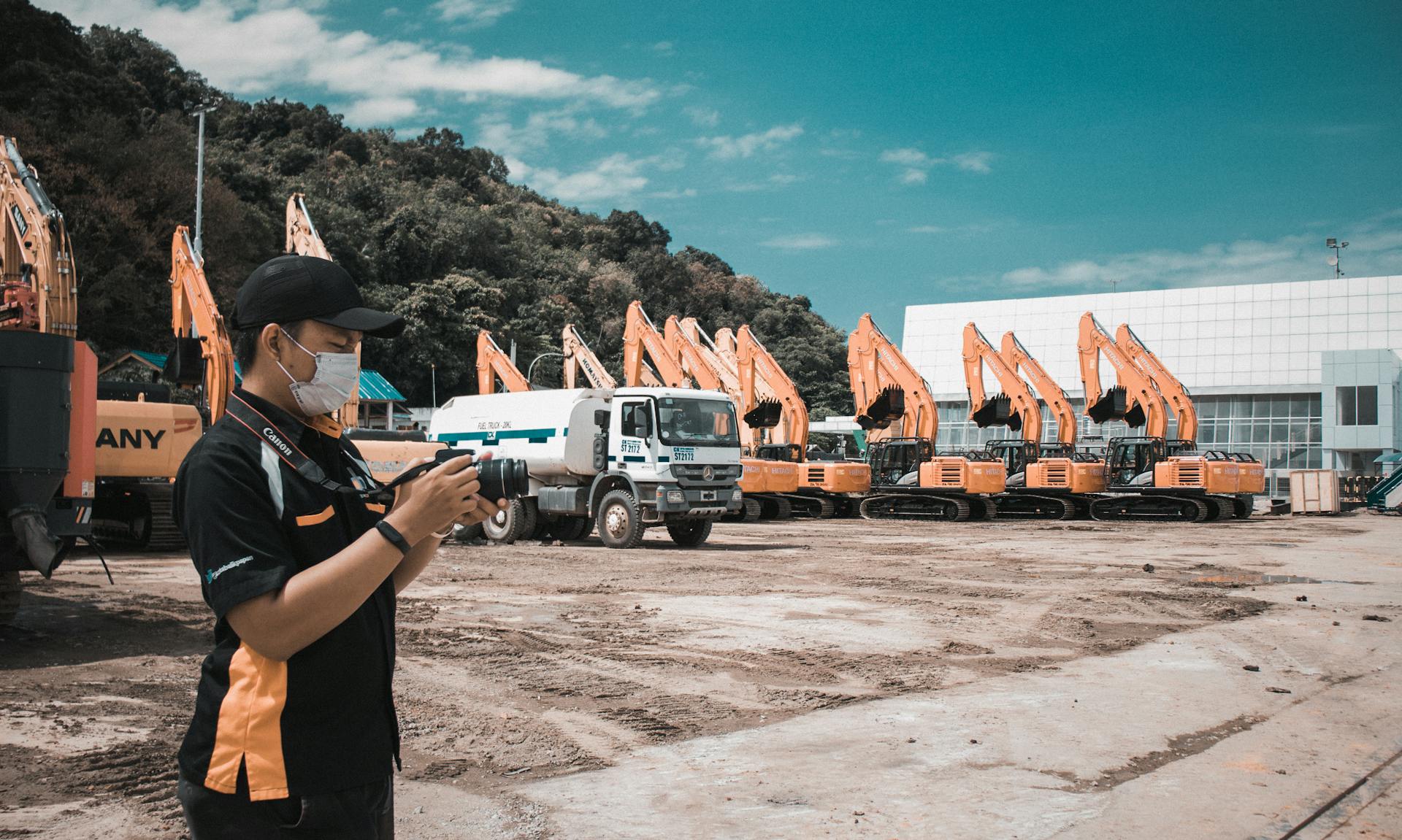
In surface mining applications, BWEs are used for continuous overburden removal. They work by cutting away a section of earth, known as the working block, dictated by the size of the excavator.
The working block can include area both above and below the level of the machine, thanks to the ability to hoist. This allows for efficient removal of overburden.
Through slewing, the excavator can reach through a horizontal range, giving it the flexibility to access different areas of the pit. The overburden is then delivered to the discharge boom, which transfers the cut earth to another machine.
This machine is usually a fixed belt conveyor system or a mobile conveyor with crawlers, similar to those found on the BWE. Mobile conveyors permanently attached to the excavator take the burden of directing the material off of the operator.
The overburden can also be transferred directly to a cross-pit Spreader, which reaches across the pit and scatters overburden at the dumping ground.
Automation
Automation has revolutionized the way mining operations are managed, allowing project managers and operators to track crucial data regarding BWEs and other machinery via the Internet. This enables real-time monitoring and control.
Sensors play a crucial role in automation, detecting how much material is being scooped onto the conveyor belt. This information is then used to vary the speed on the conveyor belts to feed a continuous amount of material.
Automation systems can take away some of the work from operators, allowing them to achieve higher mining speeds. By automating routine tasks, operators can focus on more critical aspects of the operation.
The integration of many sensors and electrical components, such as GPS and data acquisition systems, is necessary for effective automation. These systems provide the necessary data for the automation system to make informed decisions.
Online monitoring capabilities are also a key component of automation, enabling operators to track the performance of BWEs and other machinery remotely. This allows for quick identification and resolution of any issues that may arise.
Frequently Asked Questions
Are bucket wheel excavators still used?
Yes, bucket wheel excavators are still used, primarily in lignite mining for electricity production in Europe. Their use is mainly concentrated in Germany and Eastern/Southeastern Europe.
How much does a bucket wheel cost?
A bucket wheel excavator costs around $100 million.
Are there any bucket wheel excavators in the United States?
Yes, bucket wheel excavators are used in surface mining projects across the United States, including the massive 14,200-ton Bagger 293, the world's largest-ever wheel excavator. These massive machines are a common sight in US surface mining operations.
How much did Bagger 293 cost?
The Bagger 293 was constructed at a cost of around 100 million US dollars. This significant investment was made to build one of the world's largest excavators.
Sources
- https://en.wikipedia.org/wiki/Bucket-wheel_excavator
- https://interestingengineering.com/innovation/bagger-mining-bucket-wheel-excavator
- https://www.mci-austria.com/en/equipment/bucket-wheel-excavator/
- https://www.slideshare.net/slideshow/bucket-wheel-excavator-ppt/83661423
- https://www.homemadetools.net/forum/bagger-293-bucket-wheel-excavator-gif-56203
Featured Images: pexels.com