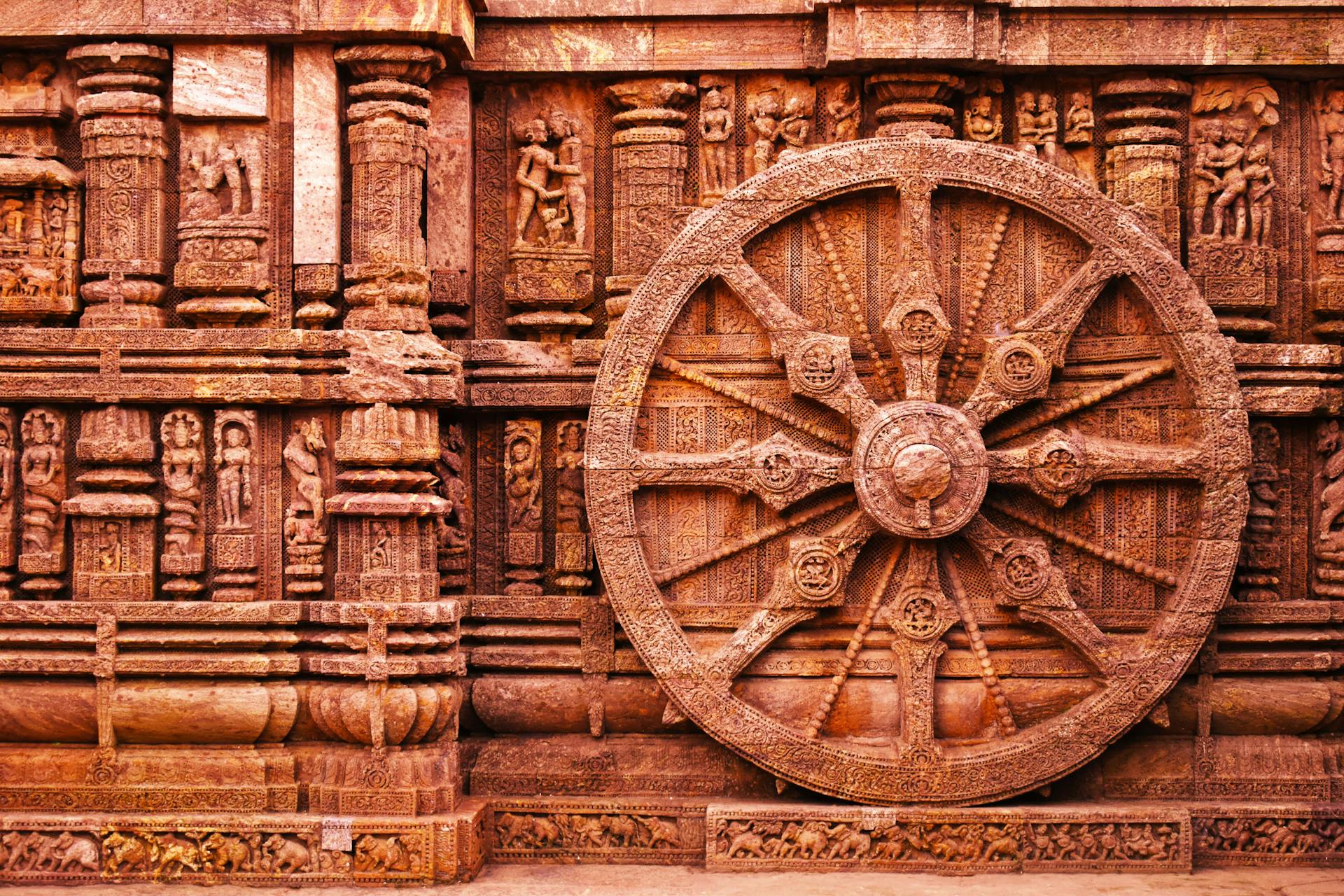
The biggest bucket wheel excavator is a behemoth of modern mining technology. It's a game-changer that's capable of moving massive amounts of earth at an incredible rate.
Standing at an impressive 225 meters tall, this massive machine is a sight to behold. Its massive bucket wheel is designed to dig deep into the earth, uncovering valuable resources like coal and iron ore.
The biggest bucket wheel excavator can dig up to 250,000 cubic meters of earth per day, making it one of the most efficient mining machines on the planet.
Discover more: Largest Earth Moving Equipment
Design and Engineering
The Bagger 293's design and engineering are truly impressive.
The excavator's massive dimensions are a result of precision engineering, with a bucket wheel over 21 meters in diameter.
Chief engineer Klaus Dieter Bartsch and mechanical engineer Manfred Kuhn led the project, which began planning in the 1980s and took five years to complete.
The construction process required the use of high-grade steel, rubber, and plastics, all fabricated at specialist manufacturing plants and then transported to the site for assembly.
The estimated cost of the project was around $100 million.
Even with its immense size, the excavator is remarkably efficient, with only five operators working in shifts around the clock to keep it running.
Size
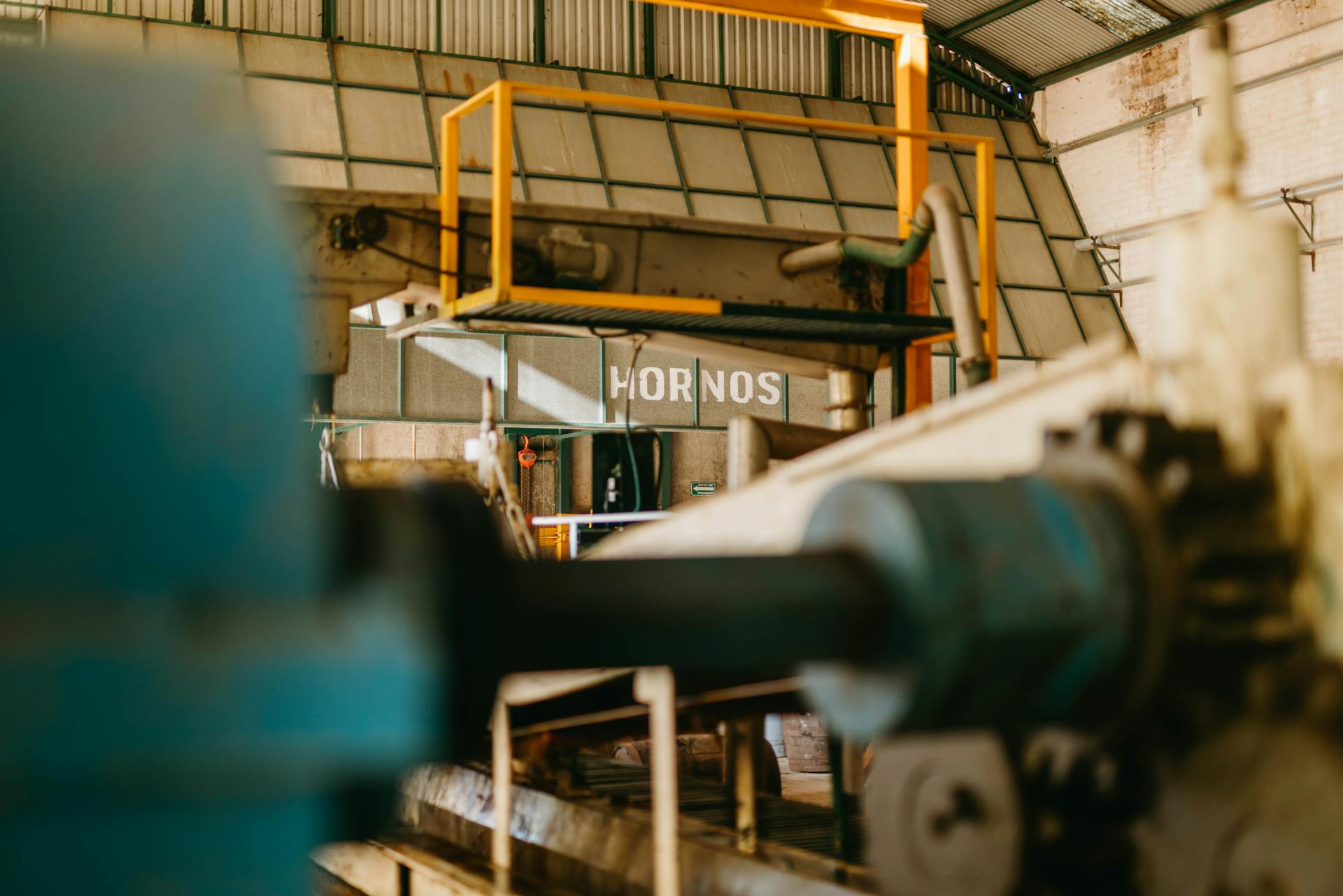
The size of Bucket Wheel Excavators (BWEs) is truly impressive. Compact BWEs designed by ThyssenKrupp can have boom lengths as small as six metres (20ft) and weigh 50 tons.
Their larger models reach boom lengths of 80m (260ft), which is a significant increase in size. This allows them to move 12,500m (440,000cuft) of earth per hour.
The largest BWE ever constructed is TAKRAF's Bagger 293, which stands at an incredible 93 meters tall and 225 meters long. This massive machine weighs 14,200 tonnes.
The scale of BWEs varies significantly depending on the intended application, and their size can have a huge impact on their efficiency. BWEs used in the United States tend to be smaller than those constructed in Germany.
A unique perspective: Knuckle Boom Log Loader
Structure
A bucket wheel excavator's structure is quite complex, but let's break it down. The superstructure is the main frame that holds everything together.
The bucket wheel itself is a large, round wheel with scoops that can rotate. It's fixed to a boom and can pick up material with its cutting wheel.
Material is transferred back along the boom, and in newer designs, it's discharged through a stationary chute. Early cell-type bucket wheels used a chute leading from each bucket.
The discharge boom receives material from the cutting boom and carries it away from the machine, often to an external conveyor system. This boom is a crucial part of the structure.
A counterweight boom balances the cutting boom and is cantilevered from the superstructure. In larger BWEs, all three booms are supported by cables running across towers at the top of the superstructure.
The movement systems, which allow the machine to travel, are located beneath the superstructure. Older models used rails, but newer BWEs often have crawlers for increased flexibility.
The superstructure can rotate about a vertical axis, known as slewing, at speeds of around 30 m/min. This is made possible by large gears.
Suggestion: Boom Truck vs Crane
Automation
Automation is a crucial aspect of BWE design and engineering, and it involves integrating many sensors and electrical components.
These components include GPS, data acquisition systems, and online monitoring capabilities, which work together to take away some of the work from operators.
By automating certain tasks, project managers and operators can track crucial data regarding the BWEs and other machinery in mining operations via the Internet.
This enables them to make informed decisions and optimize mining speeds.
Engineering the Bagger
The Bagger 293 is an engineering marvel, with a bucket wheel over 21 meters in diameter. It can scoop up 15 cubic meters of material in each of its 18 buckets.
Its sheer size is just the beginning of its impressive credentials. The Bagger 293 consumes a remarkable 19 megawatts of power, a combination of diesel and electricity.
Planning for the Bagger 293 began in the 1980s, and the construction process took a staggering five years to complete, with an estimated cost of around $100 million.
Its massive scale required the use of high-grade steel, rubber, and plastics, all fabricated at specialist manufacturing plants and then transported to the mining facility's site for assembly.
Moving the Bagger 293 to new positions on the site is a Herculean task, taking around three weeks to complete.
Suggestion: Bagger 1473
Applications and Uses
Bucket wheel excavators have a wide range of applications, but their primary use is in lignite mining, where they excel at removing soft rock overburden without blasting.
Their ability to continuously deliver large volumes of materials to processors makes them a crucial tool in this industry, especially considering the continuous demand for lignite.
In lignite mining, BWEs have undergone significant development, with the addition of automated systems, greater manoeuvrability, and components designed specifically for this application, resulting in increased reliability and efficiency.
Applications
Bucket wheel excavators and bucket chain excavators have largely replaced rope shovels and draglines in most applications. They're still used for very large-scale operations, where they can be used for the transfer of loose materials or the excavation of soft to semi-hard overburden.
One of the key areas where BWEs are used is in lignite mining, where they're used for soft rock overburden removal in the absence of blasting. They're useful in this capacity for their ability to continuously deliver large volumes of materials to processors.
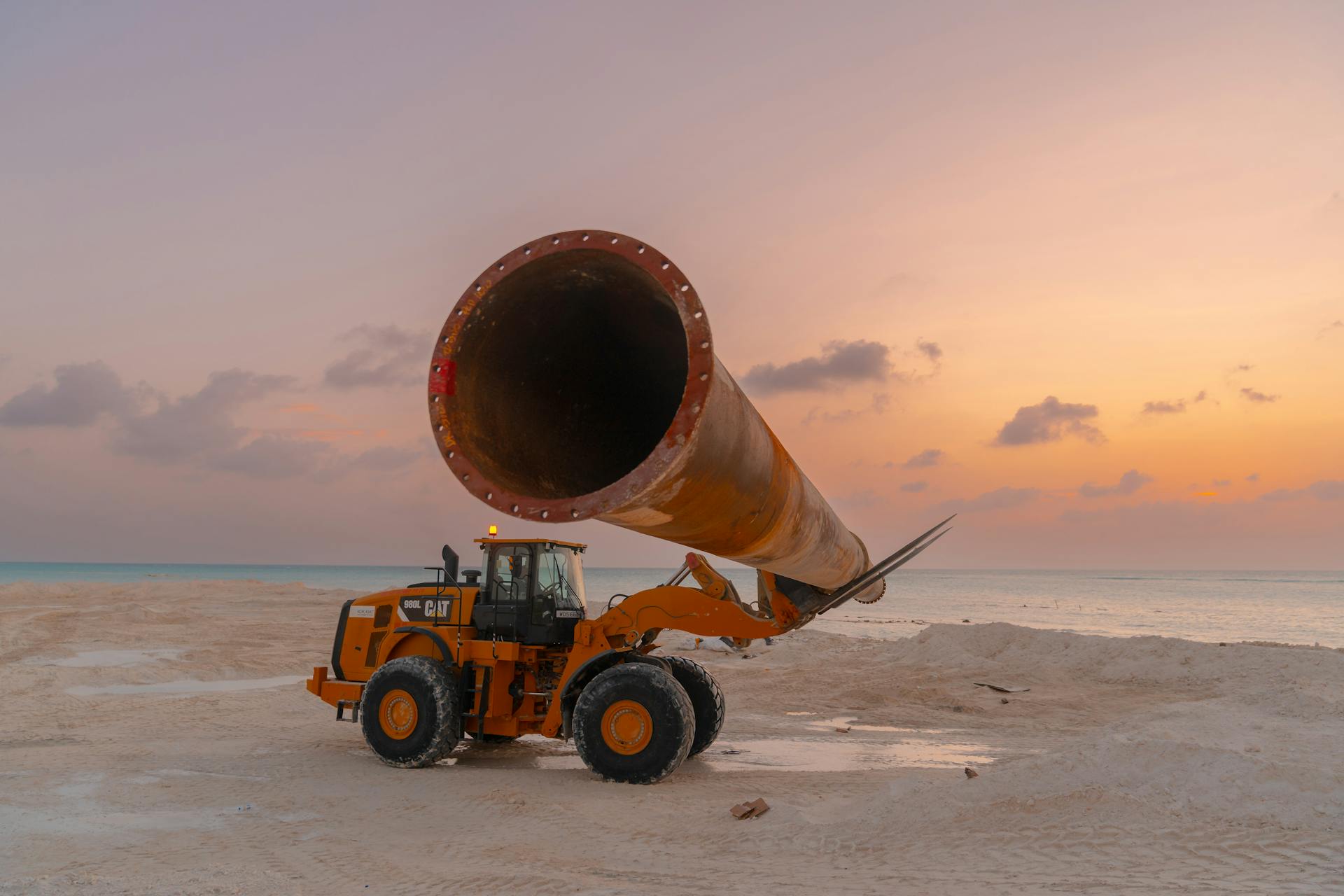
The great demand for lignite has led to significant development of BWEs, with automated systems and greater manoeuvrability increasing their reliability and efficiency. This is especially important given the continuous demand for lignite.
Bucket wheel technology is used extensively in bulk materials handling, where bucket wheel reclaimers pick up material positioned by a stacker for transport to a processing plant.
Heap Leaching
Heap leaching is an extension of the uses of Bucket Wheel Excavators (BWEs). They are used in heap leaching processes, where stacks of crushed ore are constructed and a solvent is passed through to extract valuable materials.
The construction and removal of the heaps are an obvious application of stacking and reclaiming technology. BWEs play a crucial role in this process, making it efficient and cost-effective.
BWEs are used mainly in the area of lignite (brown coal) mining for the production of electricity, mostly in Germany and East/Southeastern Europe. This is due to the high demand for electricity in these regions.
Unex, Czech Republic, is one of the few companies that can manufacture BWEs, as they still have the original casting forms. However, the demand for new machines has decreased due to the decline in strip mining.
Here are some notable BWEs used in heap leaching:
- Bagger 288
- Bagger 293
- Bagger 1473
Operation
The biggest bucket wheel excavator is a marvel of engineering, and its operation is a testament to human ingenuity. It's used for continuous overburden removal in surface mining applications.
The excavator uses its cutting wheels to strip away a section of earth, dictated by the size of the machine. This working block can include area both above and below the level of the machine, known as the bench level.
Through hoisting, the working block can be reached and removed by the excavator. By slewing, the excavator can reach through a horizontal range, allowing it to access and remove overburden efficiently.
The overburden is then delivered to the discharge boom, which transfers the cut earth to another machine for transfer to a spreader. This spreader can be a fixed belt conveyor system or a mobile conveyor with crawlers.
Mobile conveyors permanently attached to the excavator take the burden of directing the material off of the operator, making the process safer and more efficient. The overburden can also be transferred directly to a cross-pit Spreader, which reaches across the pit and scatters overburden at the dumping ground.
Intriguing read: Excavating Machine
History and Objective
Bucket-wheel excavators have been around for over a century, with some of the first being manufactured in the 1920s. They've come a long way since then.
The first extremely large BWEs were built in the 1950s for mining lignite near Cologne, Germany. These massive machines had a wheel of over 16 meters in diameter and weighed 5,500 short tons.
The size of BWEs has grown drastically since World War II, with some machines now reaching sizes as large as 96 meters tall and 225 meters long. The bucket-wheel itself can be over 21 meters in diameter with as many as 20 buckets.
Readers also liked: Long Reach Trackhoe
History
Bucket-wheel excavators have been used in mining for over a century, with some of the first being manufactured in the 1920s.
Their size has grown drastically since the end of World War II, with the first extremely large BWEs being built in the 1950s for mining lignite near Cologne, Germany.
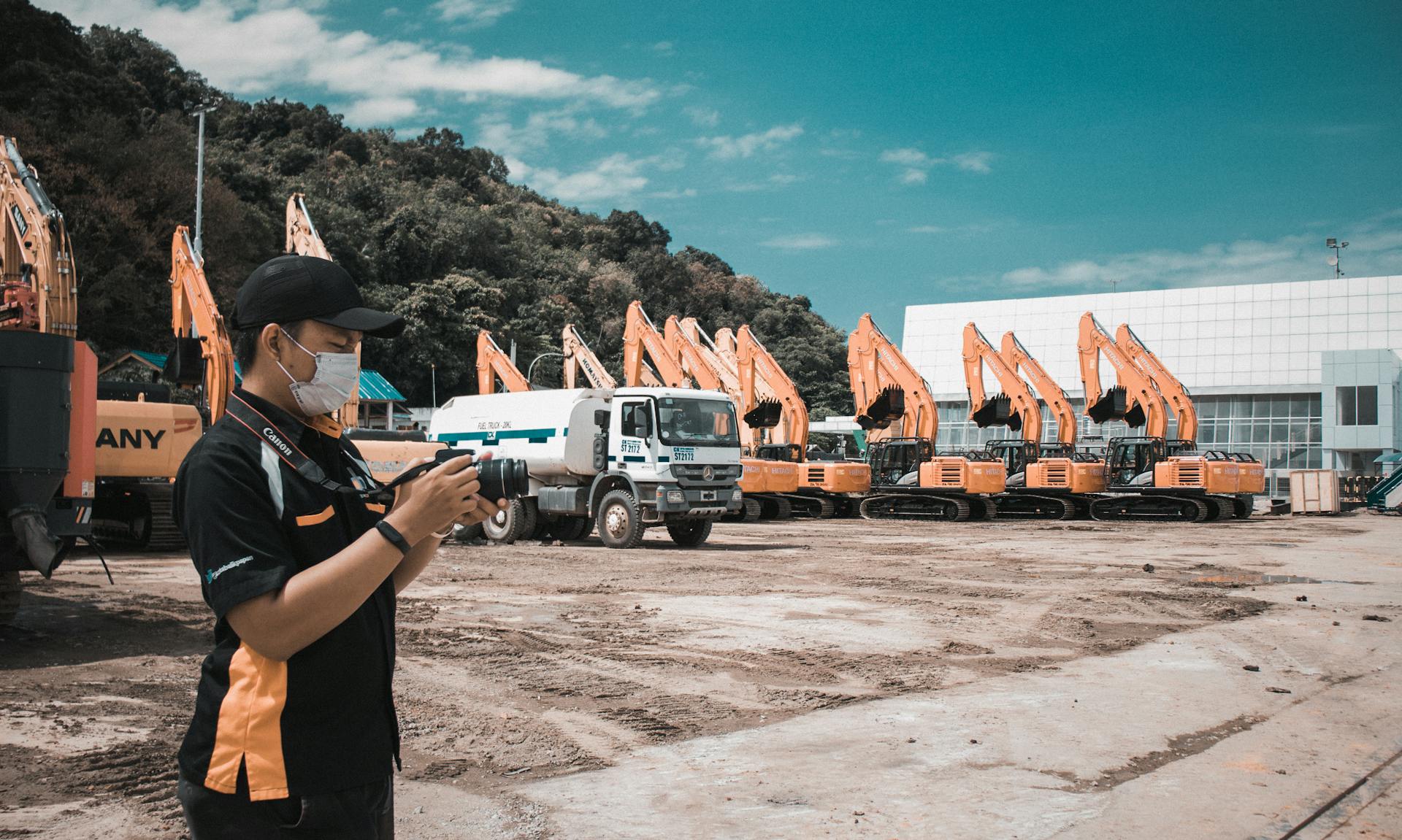
These early German BWEs had a wheel of over 16 m (52 ft) in diameter, weighed 5,500 short tons (5,000 t), and were over 180 m (600 ft) long.
They were capable of cutting a swath of over 180 m (600 ft) at one time, and had eighteen crawler units for movement.
BWEs built since the 1990s, such as the Bagger 293, have reached sizes as large as 96 m (315 ft) tall and 225 m (738 ft) long.
Some of these modern BWEs are as heavy as 14,200 t (31,300,000 lb), with bucket-wheels over 21 m (70 ft) in diameter and as many as 20 buckets, each holding over 15 m (20 cu yd) of material.
Objective
The Bagger 288 was built for a very specific job: removing overburden before coal mining at the Hambach surface mine in Germany. It can excavate an incredible amount of coal or overburden daily - 240,000 tons or 240,000 cubic meters.
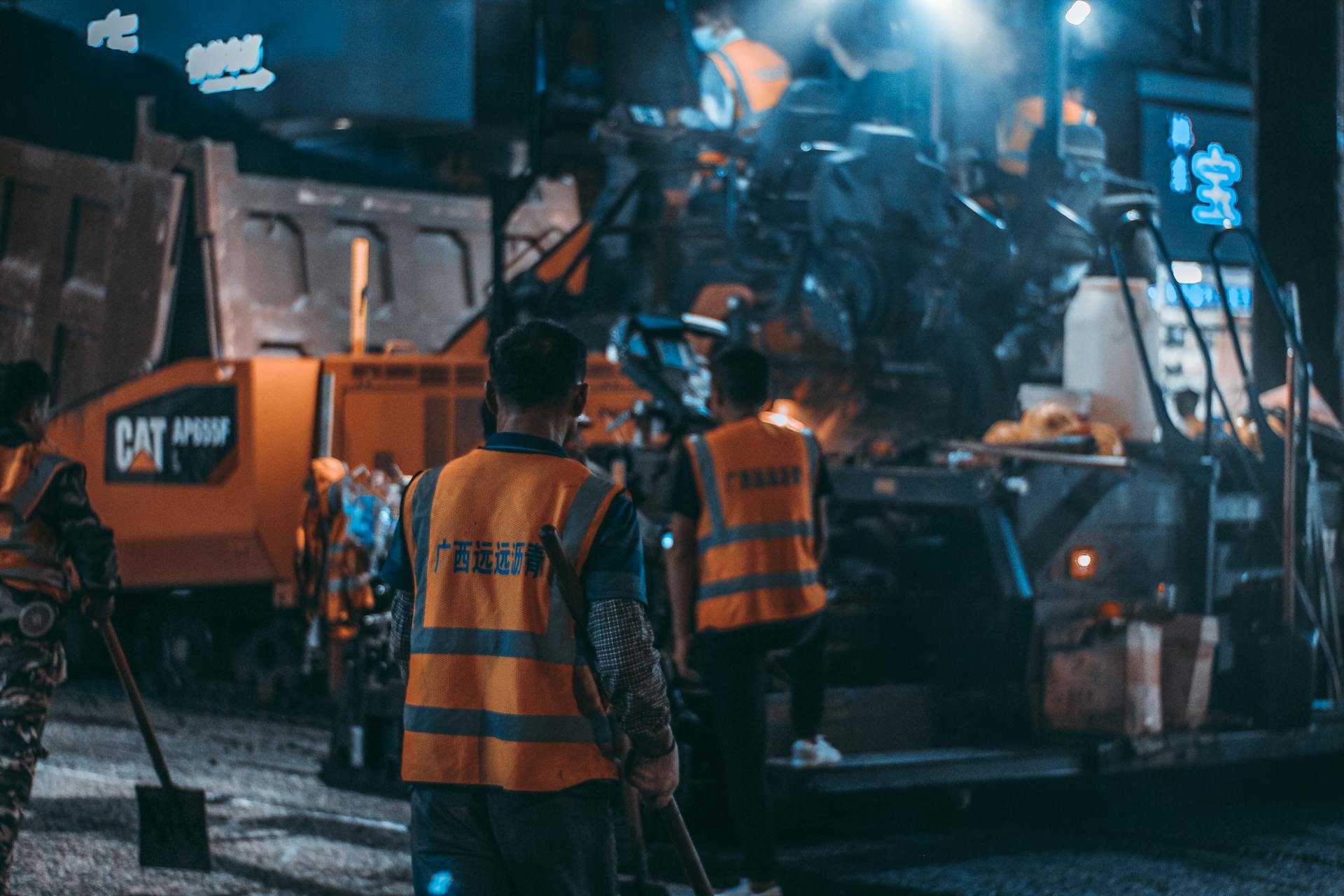
The excavator is massive, measuring 220 meters long and 96 meters high. That's slightly shorter than its siblings, the Bagger 287 and 293.
The Bagger 288 requires a lot of electricity to operate, using 16.56 megawatts externally supplied electricity. It can travel at a pace of 0.1 to 0.6 km/h, or 2 to 10 meters per minute.
The excavator's large surface area and caterpillar track assemblies allow it to travel over different terrain without leaving a significant track. The ground pressure of the Bagger 288 is very small, at 1.71 bar or 24.8 psi.
Recommended read: 1 Ton Excavator Attachments
Frequently Asked Questions
Is the Bagger 293 bigger than Bagger 288?
The Bagger 293 and Bagger 288 share the Guinness World Record for tallest terrestrial vehicle, but they have different weights. The Bagger 293 weighs 14,200 tonnes, while the weight of the Bagger 288 is not mentioned in the provided information.
Is Bagger 288 the biggest?
Bagger 288 was the heaviest land vehicle in the world when it was completed in 1978, weighing 13,500 tons. Its massive size and weight made it a record-breaker for over 40 years.
Sources
- https://www.wikiwand.com/en/articles/Bucket-wheel_excavator
- https://en.wikipedia.org/wiki/Bucket-wheel_excavator
- https://en.wikipedia.org/wiki/Bagger_288
- https://www.constructionjunkie.com/blog/2017/1/29/watch-a-310-foot-tall-100-million-bucket-wheel-excavator-rip-through-240k-tons-of-dirt-a-day
- https://interestingengineering.com/innovation/bagger-mining-bucket-wheel-excavator
Featured Images: pexels.com